UNITED STATES
SECURITIES AND EXCHANGE COMMISSION
Washington, D.C. 20549
FORM 6-K
Report
of Foreign Private Issuer Pursuant to Rule 13a-16
or 15d-16 of the Securities Exchange Act of 1934
For the month of October 2023 |
|
Commission File Number 001-40569 |
Standard Lithium Ltd. |
(Translation of registrant’s name into English) |
|
Suite 1625, 1075 West Georgia Street
Vancouver, British Columbia, Canada V6E 3C9 |
(Address of principal executive offices) |
Indicate by check mark whether the registrant files or will file annual
reports under cover of Form 20-F or Form 40-F:
Form 20-F ¨
Form 40-F x
Indicate by check mark if the registrant is submitting the Form 6-K
in paper as permitted by Regulation S-T Rule 101(b)(1): ¨
Indicate by check mark if the registrant is submitting the Form 6-K
in paper as permitted by Regulation S-T Rule 101(b)(7): ¨
DOCUMENTS INCLUDED AS PART OF THIS REPORT
SIGNATURES
Pursuant to the requirements of the Securities
Exchange Act of 1934, the registrant has duly caused this report to be signed on its behalf by the undersigned, thereunto duly authorized.
|
Standard Lithium Ltd. |
|
(Registrant) |
|
|
Date: |
October 18, 2023 |
|
By: |
/s/ Robert Mintak |
|
|
|
|
Name: |
Robert Mintak |
|
|
|
|
Title: |
CEO and Director |
Exhibit 99.1
October 18, 2023
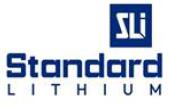
STANDARD LITHIUM FILES DEFINITIVE FEASIBILITY
STUDY FOR ITS FIRST COMMERCIAL LITHIUM EXTRACTION PLANT – PHASE 1A
October 18,
2023 – El Dorado, AR, USA – Standard Lithium Ltd. (“Standard Lithium” or the “Company”)
(TSXV:SLI) (NYSE American:SLI) (FRA:S5L), a leading near-commercial lithium company, today announced that the Definitive Feasibility Study
(the “Report”) for its first commercial lithium project (“Phase
1A”) proposed to be located at the LANXESS South Plant has been filed.
With expected first production in 2026, Phase
1A is anticipated to be the first US-based lithium production project built in six decades, and the first commercial direct lithium extraction
facility in North America with potential to double current United States lithium production from current levels.
Phase 1A will process lithium-rich brine currently
flowing through existing infrastructure and represents production of only five percent of the total Measured and Indicated Resource of
2.8 Mt lithium carbonate equivalent (“LCE”)1. The Definitive Feasibility Study demonstrates strong economics,
assuming initial annual production of 5,700 tonnes, and an average annual production of 5,400 tonnes of battery-quality lithium carbonate
over a 25-year operating life based on Proven and Probable Reserves of 208 Kt LCE at an average concentration of 217 mg/L. Phase 1A represents
a modest 60-times scale up from the operational Demonstration Plant, which over a three-and-a-half-year period of effective and efficient
lithium extraction, has used the same brine that will feed the proposed commercial plant. The Company expects to make a final investment
decision for Phase 1A in the first half of 2024.
Standard Lithium
intends to scale and replicate the development model for the Phase 1A project across its portfolio of projects in the Smackover Formation,
including the South West Arkansas Project and highly prospective East Texas landholdings. The lithium concentrations of the Company’s
projects tend to improve from east to west across the Smackover Formation. Most recently, East Texas drilling results delivered
the new, highest grade lithium brine concentrations in North America that the Company is aware of, at 663 mg/L. Higher lithium concentrations
paired with economies of scale through the advancement of multiple projects is expected to afford the Company a competitive advantage
as it expands its footprint through the Smackover Formation.
1 Total Measured and Indicated Resource of 2.8 Mt LCE at
average concentration of 148 mg/L for the combined LANXESS South, Central and West Brine Units; Phase 1A represents production of approximately
135,000 tonnes LCE or 5% of the total Measured and Indicated Resources.
Standard Lithium's filing of the Definitive Feasibility
Study highlights its commitment to commercialize direct lithium extraction technology, starting with Phase 1A. This approach aims to unlock
the resource potential of the Smackover Formation and address critical mineral needs in the U.S. sustainably and responsibly.
The Report is available
for review under the Company’s profile on SEDAR+ at www.sedar.com and on the Company’s website at www.standardlithium.com/projects/arkansas-smackover.
For highlights of this Report, please refer to the Company’s press release dated 6 September 2023.
About Standard Lithium Ltd.
Standard Lithium is a leading near-commercial
lithium development company focused on the sustainable development of a portfolio of lithium-brine bearing properties in the United States. The
Company prioritizes brine projects characterized by high-grade resources, robust infrastructure, skilled labor, and streamlined permitting.
The Company aims to achieve sustainable, commercial-scale lithium production via the application of a scalable and fully-integrated Direct
Lithium Extraction (“DLE”) and purification process. The Company’s signature projects, the Phase 1A Project and the
South West Arkansas Project, are located on the Smackover Formation in southern Arkansas near the Louisiana state line, a region with
a long-standing and established brine processing industry. The Company has also identified a number of highly prospective lithium brine
project areas in the Smackover Formation in East Texas and began an extensive brine leasing program in the key project areas. In
addition, the Company has an interest in certain mineral leases located in the Mojave Desert in San Bernardino County, California.
Standard Lithium
trades on both the TSX Venture Exchange and the NYSE American under the symbol “SLI”; and on the Frankfurt Stock Exchange
under the symbol “S5L”. Please visit the Company’s website at www.standardlithium.com.
Qualified Person
Steve Ross, P.Geol., a qualified person as defined
by National Instrument 43-101, and Vice President Resource Development for the Company, has reviewed and approved the relevant scientific
and technical information in this news release.
Investor and Media Inquiries
Allysa Howell
Vice President, Corporate Communications
+1 720 484 1147
a.howell@standardlithium.com
Twitter: @standardlithium
LinkedIn: https://www.linkedin.com/company/standard-lithium/
Neither
the TSX Venture Exchange nor its Regulation Services Provider (as that term is defined in policies of the TSX Venture Exchange) accepts
responsibility for the adequacy or accuracy of this release. This news release may contain certain “Forward-Looking Statements”
within the meaning of the United States Private Securities Litigation Reform Act of 1995 and applicable Canadian securities laws. When
used in this news release, the words “anticipate”, “believe”, “estimate”, “expect”, “target,
“plan”, “forecast”, “may”, “schedule” and other similar words or expressions identify
forward-looking statements or information. These forward-looking statements or information may relate to intended development timelines,
future prices of commodities, accuracy of mineral or resource exploration activity, reserves or resources, regulatory or government requirements
or approvals, the reliability of third party information, continued access to mineral properties or infrastructure, fluctuations in the
market for lithium and its derivatives, changes in exploration costs and government regulation in Canada and the United States, and other
factors or information. Such statements represent the Company’s current views with respect to future events and are necessarily
based upon a number of assumptions and estimates that, while considered reasonable by the Company, are inherently subject to significant
business, economic, competitive, political and social risks, contingencies and uncertainties. Many factors, both known and unknown, could
cause results, performance or achievements to be materially different from the results, performance or achievements that are or may be
expressed or implied by such forward-looking statements. The Company does not intend, and does not assume any obligation, to update these
forward-looking statements or information to reflect changes in assumptions or changes in circumstances or any other events affecting
such statements and information other than as required by applicable laws, rules and regulations.
Exhibit 99.2
|
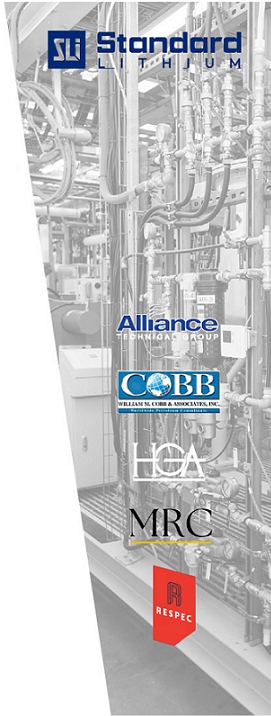
|
|
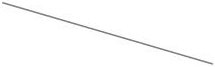 |
|
NI
43-101 |
Technical
Report for |
the
Definitive Feasibility Study |
for
commercial lithium |
extraction
plant at |
lanxess
south plant |
|
REPORT
RSI-3353 |
|
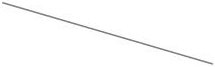 |
|
Prepared
by |
Randal M. Brush, PE (William
M. Cobb & Associates, Inc.) |
Charles Daniel Campbell, PE (Alliance
Technical Group) |
Frank Gay, PE (Hunt, Guillot &
Associates, LLC) |
Susan B. Patton, PE (RESPEC
Company, LLC) |
Mike Rockandel, RM-SME (Mike
Rockandel Consulting, LLC) |
Robert E. Williams, Jr., PG, CPG (William M. Cobb & Associates, Inc.) |
|
Prepared
For |
Standard Lithium Ltd. |
1625 – 1075 West Georgia
St |
Vancouver, British Columbia
V6E 3C9 |
Canada |
|
Effective
DAte August 18, 2023 |
|
Report
Date October 18, 2023 |
|
Project Number M0226.22001.003 |
|
|
|
|
|
|
|
|
Cautionary Note Regarding Forward-Looking
Information
These forward-looking statements relate
to, among other things, resource estimates, grades and recoveries, development plans, mining methods and metrics including recovery process
and, mining and production expectations including expected cash flows, capital cost estimates and expected life of mine, operating costs,
the expected payback period, receipt of government approvals and licenses, time frame for construction, financial forecasts including
net present value and internal rate of return estimates, tax and royalty rates, and other expected costs.
Forward-looking information is necessarily
based upon a number of estimates and assumptions that, while considered reasonable, are inherently subject to significant political,
business, economic and competitive uncertainties and contingencies. There may be factors that cause results, assumptions, performance,
achievements, prospects or opportunities in future periods not to be as anticipated, estimated or intended.
There can be no assurances that forward-looking
information and statements will prove to be accurate, as many factors and future events, both known and unknown could cause actual results,
performance or achievements to vary or differ materially from the results, performance or achievements that are or may be expressed or
implied by such forward-looking statements contained herein or incorporated by reference. Accordingly, all such factors should be considered
carefully when making decisions with respect to the Project, and prospective investors should not place undue reliance on forward-looking
information. Forward-looking information in this technical report is as of the effective date, August 18, 2023. Standard Lithium
Ltd. assumes no obligation to update or revise forward-looking information to reflect changes in assumptions, changes in circumstances
or any other events affecting such forward-looking information, except as required by applicable law.
i |
 |
RSI-3353 |
Certificate
of Author
I, Randal M. “Randy” Brush,
PE, as a co-author of the Technical Report titled Technical Report for the Definitive Feasibility Study for Commercial Lithium Extraction
Plant at LANXESS South Plant (the Technical Report), effective date August 18, 2023, do hereby certify that:
| / | I
am currently employed as President of William M. Cobb & Associates, Inc. with
an office at 12770 Coit Road, Suite 907, Dallas, Texas, 75251. |
| / | I
hold a Master of Science degree in petroleum engineering from Stanford University and a Bachelor
of Science in chemical engineering from Rice University. |
| / | I
am a member in good standing of the Society of Petroleum Engineers, a constituent organization
within the AIME, the American Institute of Mining, Metallurgical and Petroleum Engineers
(Member # 0515460). I am also a member of the Society of Petroleum Evaluation Engineers. |
| / | I
am a professional engineer, registered in Texas, and have been practicing in this capacity
since 1999. |
| / | As
a professional engineer, I have over 42 years of experience in evaluating the injection
and production of water, brines, and other fluids into and out of porous formations like
the Smackover. This includes 10 years of evaluating this specific field. These tasks have
included the following: |
| » | Using
engineering analysis, mathematical modeling, and appropriate data collection and analysis
techniques to evaluate the injection of gases, water, and steam into underground geologic
formations, and the recovery of oil, gas, and water from those formations. |
| » | Specializing
in reservoir evaluation, management, and simulation studies to define hydrocarbon (crude
oil, condensate, and natural gas) and non-hydrocarbon (e.g., bromine, lithium, CO2,
and helium) reserves and inventories, providing ultimate recovery estimates by predicting
reservoir performance under alternate development plans and various reservoir drive mechanisms,
and evaluating the performance of gas and CO2 storage reservoirs in response to
internal and external operational factors. |
| / | As
a result of my experience and qualifications, I am a Qualified Person as defined in
National Instrument 43-101. |
| / | I
am independent of Standard Lithium applying all the tests in Section 1.5 of NI 43101. |
| / | I
am co-responsible for Chapters 7–12 and 14–16 of this Technical Report. |
| / | I
have had prior involvement with the Property that is the subject of the Technical Report.
The nature of my involvement included 10 years of evaluating the field’s bromine recovery
performance for LANXESS. |
| / | Under
my supervision, representatives from William M. Cobb & Associates, Inc. were
Robert E. Williams, Jr., geologist, and Tor Meling, reservoir engineer. |
| / | My
most recent personal inspection of the Property was on May 17 to 19, 2022. |
| / | I
have read National Instrument 43-101, Form 43-101F1, and the Technical Report for which
I am responsible, and the document has been prepared in compliance with National Instrument 43-101. |
| / | As
of the date of this certificate, to the best of my knowledge, information, and belief, this
Technical Report contains all of the scientific and technical information that is required
to be disclosed to clearly understand the Technical Report. |
| / | I
consent to the filing of this Technical Report with any stock exchange, provided that the
Technical Report complies with the framework of that regulatory exchange, and other regulatory
authority or publication by them for regulatory purposes, including electronic publication
in the public company files on their websites accessible by the public. |
Signed in Dallas, Texas, October 18,
2023. |
|
|
|
S/S Randal M. Brush |
|
|
|
Randal M. Brush, PE |
|
William M. Cobb & Associates, Inc. |
|
ii |
 |
RSI-3353 |
Certificate
of Author
I, Robert E. Williams, Jr., PG,
CPG, as a co-author of the Technical Report titled Technical Report for the Definitive Feasibility Study for Commercial Lithium Extraction
Plant at LANXESS South Plant (the Technical Report), effective date August 18, 2023, do hereby certify that:
| / | I
am currently employed as a Senior Geologist of William M. Cobb & Associates 12770
Coit Road Suite 907, Dallas Texas, 75251. |
| / | I
am a graduate of Oklahoma State University and earned a degree Bachelor of Science in Geology
in 1991. |
| / | I
am a member in good standing of American Institute of Professional Geologists (AIPG) Certification
#12158, awarded January 9, 2023. |
| / | I
am a professional geologist registered with Texas Board of Professional Geoscientists #3964,
awarded August 31, 2003. |
| / | As
a Senior Geologist with over three decades of experience in the petroleum and mineral industry, I
have worked extensively across various regions in North and South America. Notably, I
have dedicated more than 10 years to the Smackover Formation, conducting projects spanning
from Alabama to Texas. Throughout my career, my role has involved a diverse range of responsibilities,
prominently focused on the detailed mapping of geologic subsurface attributes. This mapping
process has played a fundamental role in evaluating reservoir volumetrics and accurate reserve
estimates. |
| / | As
a result of my experience and qualifications, I am a Qualified Person as defined in
National Instrument 43-101. |
| / | I
am independent of Standard Lithium applying all the tests in Section 1.5 of NI 43-101. |
| / | I
am co-responsible for Chapters 7–12 and 14–16 of this Technical Report. |
| / | Under
my supervision, representatives from William M. Cobb & Associates, Inc. was
Donald L. Bailey, geologist. |
| / | My
most recent personal inspection of the Property was on May 17 to 19, 2022. |
| / | I
have read National Instrument 43-101, Form 43-101F1 and the Technical Report for which
I am responsible, and the document has been prepared in compliance with NI 43-101. |
| / | As
of the date of this certificate, to the best of my knowledge, information, and belief, this
Technical Report contains all of the scientific and technical information that is required
to be disclosed to clearly understand the Technical Report. |
| / | I
consent to the filing of this Technical Report with any stock exchange, provided that the
Technical Report complies with the framework of that regulatory exchange, and other regulatory
authority or publication by them for regulatory purposes, including electronic publication
in the public company files on their websites accessible by the public. |
Signed in Dallas, Texas, October 18,
2023. |
|
|
|
S/S Robert E. Williams, Jr. |
|
|
|
Robert E. Williams, Jr., PG, CPG |
|
William M. Cobb & Associates, Inc. |
|
iii |
 |
RSI-3353 |
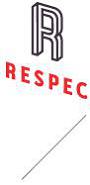
Certificate
of Author
I, Charles Daniel Campbell, P.E., as
a co-author of the Technical Report titled Technical Report for the Definitive Feasibility Study for Commercial Lithium Extraction
Plant at LANXESS South Plant (the Technical Report), effective date August 18, 2023, do hereby certify that:
| / | I
am currently retained as a Consulting Engineer by Alliance Technical Group with an office
at 219 Brown Lane, Bryant, Arkansas, 72022. |
| / | I
hold a Bachelor of Science degree in petroleum engineering from Louisiana Tech University. |
| / | I
am a registered professional engineer in AR, KS, LA, MS, MO, OK, SC, and TX, and have been
practicing in this capacity since 1983. |
| / | As
a professional engineer, I have over 35 years of experience in environmental engineering
as a consultant, manager, and state regulator. I have performed environmental planning, cost
analysis, design, and contract management for numerous industrial facilities. I have regulatory
compliance experience including NPDES, wastewater treatment, evaluation of groundwater data,
erosion/sediment control, Air (Title V and Minor Source), hazardous waste, solid waste, underground
injection, and site remediation. Specific tasks include: |
| » | I
directed environmental compliance activities programs for petroleum production and specialty
chemical processing companies with multiple production, transportation, and distribution
facilities in the U.S. |
| » | I
was responsible for the preparation of NPDES, Title V, and RCRA permit applications |
| » | I
have evaluated groundwater hydrology of monitoring well networks and prepared reports for
regulatory agencies, conducted transient tests on recovery wells, and developed well rehabilitation
projects |
| / | As
a result of my experience and qualifications, I am a Qualified Person as defined in
National Instrument 43-101. |
| / | I
am independent of Standard Lithium applying all the tests in Section 1.5 of National
Instrument 43-101. |
| / | I
am responsible for Chapter 20 of this Technical Report. |
| / | I
have had prior involvement with the Property that is the subject of the Technical Report.
The nature of my involvement included consulting as an environmental professional retained
by Standard Lithium as a regulatory resource for the subject Property. Related to the subject
Property, I have been directly employed as an environmental professional by Great Lakes
Chemical Corporation (GLCC), predecessor to LANXESS Corporation, and as a consulting environmental
engineer to GLCC, Chemtura Corporation, and LANXESS Corporation. |
| / | Under
my supervision, representatives from GBMc & Associates, Inc. (now Alliance)
have provided environmental regulatory support to LANXESS Corporation and its predecessors. |
| / | My
most recent personal inspection of the Property was on November 8, 2022. |
| / | I
have read National Instrument 43-101, Form 43-101F1, and the Technical Report for which
I am responsible, and the document has been prepared in compliance with National Instrument 43-101. |
| / | As
of the date of this certificate, to the best of my knowledge, information, and belief, this
Technical Report contains all of the scientific and technical information that is required
to be disclosed to clearly understand the Technical Report. |
| / | I
consent to the filing of this Technical Report with any stock exchange, provided that the
Technical Report complies with the framework of that regulatory exchange, and other regulatory
authority or publication by them for regulatory purposes, including electronic publication
in the public company files on their websites accessible by the public. |
Signed in Bryant, Arkansas, October 18,
2023. |
|
|
|
S/S Charles Daniel Campbell |
|
|
|
Charles Daniel Campbell, PE |
|
Alliance (formerly GBMc & Associates) |
|
iv |
 |
RSI-3353 |
Certificate
of Author
I, Frank Gay, PE, as a co-author of
the Technical Report titled Technical Report for the Definitive Feasibility Study for Commercial Lithium Extraction Plant at LANXESS
South Plant (the Technical Report), effective date August 18, 2023, do hereby certify that:
| / | I
am the Vice President, Owner’s Representative Services of Hunt, Guillot &
Associates, LLC, with an office at 8401 New Trails Drive, Suite 175, The Woodlands,
TX 77381. |
| / | I
hold a Bachelor of Science degree in chemical engineering from the Massachusetts Institute
of Technology and a Master of Science degree in chemical engineering practice also from the
Massachusetts Institute of Technology. |
| / | I
am a professional engineer, registered in North Carolina, have been practicing in this capacity
since 1985, and am in good standing. |
| / | As
a professional engineer, I have more than 35 years of experience in project and engineering
management, cost and scheduling control, process design, stress analysis, petrochemical industry,
and design and execution. These tasks have included the following: |
| » | I
participated in licensor selection, pre-front-end engineering design (pre-FEED), FEED, and
Project Management Consulting (PMC) during the engineering, procurement, and construction
(EPC) phase. I set up and led the project from early configuration studies through FEED,
followed by the PMC role during detailed design, procurement, and construction. The project
consisted of the design and installation of four major inside battery limits (ISBL) units,
including a naphtha hydrocracker, diesel hydrotreater, a hydrogen production unit, a sulfur
recovery unit, and associated utilities and off-sites for a major refinery expansion
on the west coast of Saudi Arabia. My responsibilities included overall management of cost
schedule and quality for the FEED and capital cost estimate for the project. |
| » | I
developed Pre-FEED (design basis scoping paper [DBSP]) package for a new-technology polyols
facility located in Saudi Arabia. The work was performed entirely in Saudi Arabia using approximately
30% Saudi engineers and other project management professionals. I was responsible for the
execution of the project. |
| / | As
a result of my experience and qualifications, I am a Qualified Person as defined in
National Instrument 43-101. |
| / | I
am independent of Standard Lithium applying all the tests in Section 1.5 of National
Instrument 43-101. |
| / | I
am responsible for Chapter 22 of this Technical Report. |
| / | I
have not had prior involvement with the Property that is the subject of the Technical Report. |
| / | I
have never visited the Property. |
| / | I
have read National Instrument 43-101, Form 43-101F1, and the Technical Report for which
I am responsible, and the document has been prepared in compliance with National Instrument 43-101. |
| / | As
of the date of this certificate, to the best of my knowledge, information, and belief, this
Technical Report contains all of the scientific and technical information that is required
to be disclosed to clearly understand the Technical Report. |
| / | I
consent to the filing of this Technical Report with any stock exchange, provided that the
Technical Report complies with the framework of that regulatory exchange, and other regulatory
authority or publication by them for regulatory purposes, including electronic publication
in the public company files on their websites accessible by the public. |
Signed in Ruston, Louisiana, October 18,
2023. |
|
|
|
S/S Frank Gay |
|
|
|
Frank Gay, PE |
|
Hunt, Guillot & Associates, LLC |
|
v |
 |
RSI-3353 |
Certificate
of Author
I, Susan B. Patton, PE, Principal Consultant,
as a co-author of the Technical Report Technical Report for the Definitive Feasibility Study for Commercial Lithium Extraction Plant
at LANXESS South Plant (the Technical Report), effective date August 18, 2023, do hereby certify that:
| / | I
am currently employed as a Principal Consultant of RESPEC, 1601 Riverfront Drive, Suite 204,
Grand Junction, Colorado, 81501. |
| / | I
hold a Bachelor of Science degree in mining engineering from the New Mexico Institute of
Mining and Technology, a Master of Science degree in Mineral Engineering from the University
of Alabama, and an interdisciplinary Doctorate in Mineral and Environmental Engineering from
the University of Alabama. |
| / | I
am a registered member in good standing of the Society for Mining, Metallurgy and Exploration
(Member #248220). |
| / | I
am a professional engineer, registered in Alabama, Colorado, New Mexico, Montana, West Virginia,
Pennsylvania, South Dakota, Utah, and Kentucky. |
| / | I
am a mining engineer and have been practicing in this capacity since 1983. |
| / | As
a Principal Consultant, I have been involved with mineral brines since 2007. These tasks
have included resource and reserve estimation for dilute mineral brines for the production
of potash, magnesium chloride, and lithium |
| / | As
a result of my experience and qualifications, I am a Qualified Person as defined in
National Instrument 43-101. |
| / | I
am independent of Standard Lithium applying all the tests in Section 1.5 of NI 43-101. |
| / | I
am responsible for Chapters 1–6 and 23–27 of this Technical Report. |
| / | I
have had no prior involvement with the Property that is the subject of the Technical Report. |
| / | My
most recent personal inspection of the Property was on June 27, 2023. |
| / | I
have read National Instrument 43-101, Form 43-101F1 and the Technical Report for which
I am responsible, and the document has been prepared in compliance with National Instrument
43-101. |
| / | As
of the date of this certificate, to the best of my knowledge, information, and belief, this
Technical Report contains all of the scientific and technical information that is required
to be disclosed to clearly understand the Technical Report. |
| / | I
consent to the filing of this Technical Report with any stock exchange, provided that the
Technical Report complies with the framework of that regulatory exchange, and other regulatory
authority or publication by them for regulatory purposes, including electronic publication
in the public company files on their websites accessible by the public. |
Signed in Grand Junction, Colorado,
October 18, 2023. |
|
|
|
S/S Susan B. Patton |
|
|
|
Susan B. Patton, PE |
|
RESPEC Consulting, Inc. |
|
vi |
 |
RSI-3353 |
Certificate
of Author
I, Mike Rockandel, President, as an
author of the Technical Report titled Technical Report for the Definitive Feasibility Study for Commercial Lithium Extraction Plant
at LANXESS South Plant (the Technical Report), effective date August 18, 2023, do hereby certify that:
| / | I
am currently employed as President of Mike Rockandel Consulting, LLC with an office at 11414
N. Mountain Breeze, Tucson, Arizona, 85737. |
| / | I
hold a Bachelor of Science degree in metallurgical engineering from the University of British
Columbia. |
| / | I
am a member in good standing of the Society for Mining, Metallurgy and Exploration (Member #
4122579). |
| / | As
a process and engineering consultant, I have been involved with lithium since 2018.
I have more than 45 years of varied process experience at all levels of project development
from laboratory development through commissioning, startup, and operations supervision. I
am skilled in process modeling with tools such as Metsim and HSC Chemistry. My career has
been broad based covering projects in the hydro and pyrometallurgical, industrial minerals,
chemical, and environmental industries. Throughout much of my career, I have worked
as a lead process engineer responsible for the preparation of process flow diagrams, mass
balances, process design specification, equipment sizing and specification, utility, and
operating cost evaluation, bid evaluation, commissioning, start-up, and process optimization.
These tasks have included the following: |
| » | I
assisted Lithium Nevada in the development of their clay-based lithium project. My duties
have included flowsheet development, simulation, and optimization of the process, preparation
of specifications, and assistance with equipment selection. |
| » | I
am the lead process engineer for the American Pacific Borate and Lithium pre-feasibility
study (in-situ) colemanite leach process producing 90,000 t/y of boric acid. This project
is now advancing to the FEED stage. This project includes a Mannheim potassium sulphate production
facility. |
| / | As
a result of my experience and qualifications, I am a Qualified Person as defined in
National Instrument 43-101. |
| / | I
am independent of Standard Lithium applying all the tests in Section 1.5 of NI 43-101. |
| / | I
am responsible for Chapters 13, 17, and 21 of this Technical Report. |
| / | I
have had no prior involvement with the Property that is the subject of the Technical Report. |
| / | My
most recent personal inspection of the Property was on October 10–12, 2022. |
| / | I
have read National Instrument 43-101, Form 43-101F1 and the Technical Report for which
I am responsible, and the document has been prepared in compliance with National Instrument
43-101. |
| / | As
of the date of this certificate, to the best of my knowledge, information, and belief, this
Technical Report contains all of the scientific and technical information that is required
to be disclosed to clearly understand the Technical Report. |
| / | I
consent to the filing of this Technical Report with any stock exchange, provided that the
Technical Report complies with the framework of that regulatory exchange, and other regulatory
authority or publication by them for regulatory purposes, including electronic publication
in the public company files on their websites accessible by the public. |
Signed in Tucson, Arizona, October 18,
2023. |
|
|
|
S/S Mike Rockandel |
|
|
|
Mike Rockandel, President |
|
Mike Rockandel Consulting, LLC |
|
vii |
 |
RSI-3353 |
TABLE
OF CONTENTS
1.0 |
Executive Summary |
1 |
|
|
|
|
|
1.1 |
Property Description |
2 |
|
1.2 |
Geology and Mineralization |
4 |
|
1.3 |
Status of Exploration |
4 |
|
1.4 |
Mineral Resource Estimate |
4 |
|
1.5 |
Mineral Reserve Estimate |
6 |
|
1.6 |
Mining Methods |
6 |
|
1.7 |
Recovery Method |
7 |
|
1.8 |
Project Infrastructure |
8 |
|
1.9 |
Marketing |
9 |
|
1.10 |
Environmental Permitting |
9 |
|
1.11 |
Capital and Operating Expenses |
10 |
|
1.12 |
Economic Analysis |
12 |
|
1.13 |
Qualified Person’s Conclusions |
13 |
|
1.14 |
Qualified Person’s Recommendations |
14 |
|
|
|
|
2.0 |
Introduction |
15 |
|
|
|
|
|
2.1 |
Terms of Reference and Purpose of Report |
15 |
|
2.2 |
Qualified Persons |
17 |
|
2.3 |
Personal Inspection of Property by Qualified
Persons |
17 |
|
2.4 |
Sources of Information |
17 |
|
2.5 |
Currency, Abbreviations, and Units of Measures |
19 |
|
|
|
|
3.0 |
Reliance on Other Experts |
22 |
|
|
|
|
|
3.1 |
Mineral Tenure |
22 |
|
3.2 |
Market Pricing |
22 |
|
|
|
|
4.0 |
Property Description and Location |
23 |
|
|
|
|
|
4.1 |
Property Description and Location |
23 |
|
4.2 |
Surface and Mineral Rights |
25 |
|
|
4.2.1 |
Mineral Rights |
25 |
|
|
4.2.2 |
Surface Rights |
25 |
|
4.3 |
Payments to Lessors |
27 |
|
4.4 |
Overview of the Standard Lithium – LANXESS Agreements |
28 |
|
|
4.4.1 |
Amended and Restated Memorandum
of Understanding |
28 |
|
|
4.4.2 |
Site Access, Reservation and License Agreement |
29 |
|
4.5 |
Environmental Liabilities and Permitting |
31 |
|
4.6 |
Significant Encumbrances or Risks to Perform
Work on Property |
32 |
|
|
|
|
5.0 |
Accessibility, Climate, Local Resources,Infrastructure, and Physiography |
33 |
|
|
|
|
|
5.1 |
Accessibility |
33 |
viii |
 |
RSI-3353 |
|
|
5.1.1 |
Airport Access |
33 |
|
|
5.1.2 |
Rail Access |
33 |
|
|
5.1.3 |
Road Access |
33 |
|
5.2 |
Climate |
35 |
|
5.3 |
Local |
35 |
|
|
5.3.1 |
Local Labor |
35 |
|
|
5.3.2 |
Transport |
35 |
|
|
5.3.3 |
Water |
36 |
|
|
5.3.4 |
Power |
36 |
|
|
5.3.5 |
Natural Gas |
36 |
|
|
5.3.6 |
Supporting Services |
36 |
|
5.4 |
Physiography |
36 |
|
5.5 |
Summary |
36 |
|
|
|
|
6.0 |
History |
37 |
|
|
|
|
6.1 |
History of the LANXESS Property |
37 |
|
6.2 |
Historical Mineral Resource Estimates |
40 |
|
6.3 |
Production from the Property |
42 |
|
|
|
|
7.0 |
Geological Setting and Mineralization |
43 |
|
|
|
|
8.0 |
Deposit Type |
50 |
|
|
|
|
9.0 |
Exploration |
53 |
|
|
|
|
|
9.1 |
Geologic Data Sampling Methods, Quality,
and Extent |
53 |
|
9.2 |
Lithium Concentration Data Sampling Methods,
Quality, and Extent |
53 |
|
9.3 |
Exploration Results and Interpretation |
55 |
|
|
|
|
10.0 |
Drilling |
59 |
|
|
|
|
11.0 |
Sample Preparation, Analyses, and Security |
63 |
|
|
|
|
|
11.1 |
Sampling Procedures |
63 |
|
|
11.1.1 |
Methodology |
63 |
|
|
11.1.2 |
Analytical Protocol |
64 |
|
|
|
|
12.0 |
Data Verification |
65 |
|
|
|
|
|
12.1 |
Verification of Lithium Concentration Data |
65 |
|
12.2 |
Verification of Well Logs and Core Data |
70 |
|
12.3 |
Verification of Production and Injection
Data |
70 |
|
12.4 |
Qualified Person’s Opinion |
71 |
|
|
|
|
13.0 |
Mineral Processing and Metallurgical Testing |
72 |
|
|
|
|
|
13.1 |
Introduction |
72 |
|
13.1 |
Process Overview |
73 |
|
13.2 |
Historical Testing |
74 |
|
13.3 |
Demonstration Plant Testing |
74 |
|
|
13.1.1 |
Demonstration Plant |
75 |
ix |
 |
RSI-3353 |
|
|
13.1.2 |
Tail Brine Measurement Skid |
79 |
|
|
13.1.3 |
Brine Pre-Treatment Testing |
79 |
|
13.2 |
Brine Pre-treatment at LANXESS |
80 |
|
13.3 |
Brine pH Control |
80 |
|
13.4 |
Brine Filtration |
81 |
|
13.5 |
Key Findings from Brine Pre-Treatment Test
Work |
82 |
|
|
13.5.1 |
DLE Testing at the Demonstration Plant |
82 |
|
|
|
13.5.1.1 |
LiSTR DLE Testing |
82 |
|
|
|
13.5.1.2 |
Key Findings from LiSTR DLE Test Work |
82 |
|
|
|
13.5.1.3 |
LSS DLE Testing |
83 |
|
|
|
13.5.1.4 |
Key Findings from LSS DLE Test Work |
84 |
|
13.6 |
Demonstration Plant LiCl Solution Purification and Concentration |
84 |
|
13.7 |
LiCl Solution Concentration by Reverse Osmosis |
85 |
|
|
13.7.1 |
Brackish Water Reverse Osmosis (BWRO) |
85 |
|
|
13.7.2 |
Osmotically Assisted Reverse Osmosis (OARO) |
85 |
|
13.8 |
Calcium and Magnesium Removal Processes |
86 |
|
|
13.8.1 |
Soda Lime Softening Testing |
86 |
|
|
13.8.2 |
Calcium and Magnesium Ion Exchange |
89 |
|
13.9 |
Boron Removal Ion Exchange |
89 |
|
13.10 |
Key Findings from LiCl Purification and
Concentration Test Work |
89 |
|
13.11 |
Additional LiCl Purification and Concentration
Testing |
90 |
|
13.12 |
Lithium Carbonate Crystallization |
90 |
|
|
13.12.1 |
First Production of Lithium Carbonate |
91 |
|
|
13.12.2 |
Second Production of Lithium Carbonate |
93 |
|
|
13.12.3 |
Third Production of Lithium Carbonate |
95 |
|
|
13.12.4 |
Key Findings from Lithium Carbonate Crystallization
Test Work |
97 |
|
13.13 |
Process Testing QA/QC |
97 |
|
13.14 |
Process Technical Risks and Mitigation
Measures |
98 |
|
13.15 |
Conclusions and Recommendations |
98 |
|
|
|
|
14.0 |
Mineral Resources Estimates |
99 |
|
|
|
|
|
14.1 Geologic Model Description |
100 |
|
14.2 Simulation Model Description |
103 |
|
14.3 Lithium Resource Estimate |
109 |
|
14.4 Qualified Person Discussion |
111 |
|
|
|
|
15.0 |
Mineral Reserve Estimates |
113 |
|
|
|
|
|
15.1 |
Introduction |
113 |
|
15.2 |
Lithium Reserve Estimate |
113 |
|
15.3 |
Discussion of Results |
116 |
|
|
|
|
16.0 |
Mining Methods |
117 |
|
|
|
|
|
16.1 |
Production Plan |
120 |
x |
 |
RSI-3353 |
17.0 |
Recovery Methods |
123 |
|
|
|
|
|
17.1 |
Overview |
123 |
|
17.2 |
Brine Supply and Reinjection (LANXESS) |
124 |
|
|
17.2.1 |
Brine Supply |
124 |
|
|
17.2.2 |
Brine reinjection |
125 |
|
17.3 |
Brine Pre-Treatment |
125 |
|
17.4 |
Direct Lithium Extraction |
126 |
|
|
17.4.1 |
Lithium Selective Sorption |
126 |
|
|
17.4.2 |
Lithium-Depleted Brine Processing |
126 |
|
17.5 |
Purification and Concentration |
127 |
|
|
17.5.1 |
Brackish Water Reverse Osmosis |
127 |
|
|
17.5.2 |
Chemical Softening |
127 |
|
|
17.5.3 |
Ion Exchange |
127 |
|
|
|
17.5.3.1 |
Calcium and Magnesium Removal |
127 |
|
|
|
17.5.3.2 |
Ion Exchange Boron Removal |
128 |
|
|
17.5.4 |
Osmotically-Assisted Reverse Osmosis (OARO) |
128 |
|
17.6 |
Lithium Carbonate Conversion |
128 |
|
|
17.6.1 |
Lithium Carbonate Crystallization |
128 |
|
|
17.6.2 |
Drying, Milling, and Packaging |
129 |
|
17.7 |
Energy. Water, and Process Materials |
129 |
|
|
17.7.1 |
Energy Requirements |
129 |
|
|
17.7.2 |
Water Supply |
130 |
|
|
17.7.3 |
Reagents |
130 |
|
|
|
|
18.0 |
Project Infrastructure |
131 |
|
|
|
|
|
18.1 |
Infrastructure Description |
131 |
|
|
18.1.1 |
Geotechnical |
132 |
|
18.2 |
Brine Supply and Return |
132 |
|
18.3 |
Processing Plant |
133 |
|
|
18.3.1 |
Brine Pre-Treatment |
134 |
|
|
18.3.2 |
Lithium Selective Sorption (LSS) |
135 |
|
|
18.3.3 |
Softening |
135 |
|
|
18.3.4 |
Ion Exchange |
135 |
|
|
18.3.5 |
Lithium Chloride Concentration |
135 |
|
|
18.3.6 |
Lithium Carbonate Production |
135 |
|
|
18.3.7 |
Drying, Milling, and Packaging |
136 |
|
|
18.3.8 |
Effluent Brine |
136 |
|
|
18.3.9 |
Process Control& Instrumentation Systems |
136 |
|
18.4 |
Non-Process Buildings |
137 |
|
18.5 |
Support Services |
138 |
|
|
18.5.1 |
Transportation |
138 |
xi |
 |
RSI-3353 |
|
|
18.5.2 |
Reagents |
138 |
|
|
18.5.3 |
Utilities |
138 |
|
|
|
18.5.3.1 |
Natural Gas |
138 |
|
|
|
18.5.3.2 |
Electrical Power |
138 |
|
|
|
18.5.3.3 |
Water Supply |
139 |
|
|
|
18.5.3.4 |
Steam& Condensate |
139 |
|
|
|
18.5.3.5 |
Compressed Air |
139 |
|
|
|
18.5.3.6 |
Sewage Treatment |
139 |
|
|
18.5.4 |
Fire Protection |
139 |
|
|
18.5.5 |
Stormwater Management |
139 |
|
|
18.5.6 |
UIC Disposal Wells |
140 |
|
|
18.5.7 |
Security |
140 |
|
|
18.5.8 |
Telecommunications |
140 |
|
|
|
18.5.8.1 |
Main Internet Service |
140 |
|
|
|
18.5.8.2 |
Cloud Based PBX phone system |
140 |
|
|
|
18.5.8.3 |
Plant Wireless System |
140 |
|
|
|
18.5.8.4 |
VHF/UHF Radio System |
141 |
|
|
|
18.5.8.5 |
Business lan/WAN |
141 |
|
|
|
18.5.8.6 |
Process Control Plan |
141 |
|
18.6 |
LANXESS Constructed Improvements |
142 |
|
|
|
|
19.0 |
Market Studies and Contracts |
143 |
|
|
|
|
|
19.1 |
The Lithium Market |
143 |
|
19.2 |
Lithium Supply and Demand |
145 |
|
19.3 |
Lithium Carbonate Price |
146 |
|
19.4 |
LANXESS Memorandum of Understanding and
Offtake Option |
148 |
|
|
|
|
20.0 |
Environmental Studies, Permitting, and Social or Community Impact |
149 |
|
|
|
|
|
20.1 |
Environmental Regulatory Setting |
149 |
|
20.2 |
Permits and Authorities |
149 |
|
|
20.2.1 |
Federal |
150 |
|
|
20.2.2 |
State of Arkansas |
150 |
|
20.3 |
Construction and/or Operation Permits |
151 |
|
|
20.3.1 |
CWA SECTION 404 – Nationwide Permit 39 |
151 |
|
|
20.3.2 |
Minor Source Air Permit |
152 |
|
|
20.3.3 |
Public Water Supply |
152 |
|
|
20.3.4 |
NPDES Construction Stormwater Discharge |
152 |
|
|
20.3.5 |
NPDES Non-Brine Process Water Discharge |
153 |
|
|
20.3.6 |
State Construction Permit for Wastewater
Treatment |
153 |
|
|
20.3.7 |
NPDES Stormwater Discharges from Categorical
Industry |
153 |
|
|
20.3.8 |
State No-Discharge Permit |
154 |
|
|
20.3.9 |
Underground Injection Control Permit |
154 |
xii |
 |
RSI-3353 |
|
|
20.3.10 |
Resource Conservation and Recovery Act Subtitle C Treatment, Storage, and Disposal Permit |
154 |
|
20.4 |
Permit Modifications |
155 |
|
20.5 |
Environmental Liabilities |
155 |
|
20.6 |
Environmental Baseline Studies |
156 |
|
|
20.6.1 |
Subsurface – Groundwater |
156 |
|
|
20.6.2 |
Subsurface – Soil |
157 |
|
|
20.6.3 |
Surface – Stormwater |
158 |
|
|
20.6.4 |
Surface – Sediment |
158 |
|
|
20.6.5 |
Surface – Vegetation |
158 |
|
20.7 |
Wildlife |
159 |
|
20.8 |
Cultural Resources |
160 |
|
20.9 |
Environmental Impact |
161 |
|
20.10 |
Social Impact |
162 |
|
20.11 |
Waste Management/Disposal |
162 |
|
20.12 |
Environmental Management and Closure Plan |
163 |
|
|
|
|
21.0 |
Capital and Operating Costs |
164 |
|
|
|
|
21.1 |
Capital Costs |
164 |
|
|
21.1.1 |
Estimate Methodology |
165 |
|
|
21.1.2 |
Scope of Estimate |
166 |
|
|
|
21.1.2.1 |
Direct Costs |
166 |
|
|
|
21.1.2.2 |
Indirect Costs |
167 |
|
|
21.1.3 |
Schedule |
167 |
|
|
21.1.4 |
Contracting Approach |
168 |
|
|
21.1.5 |
Allowances |
168 |
|
|
21.1.6 |
Contingency |
168 |
|
|
21.1.7 |
Exclusions |
169 |
|
|
21.1.8 |
Estimate Confidence |
169 |
|
21.2 |
Operating Cost Estimate |
169 |
|
|
21.2.1 |
Electric Power and Infrastructure |
170 |
|
|
21.2.2 |
Reagents and Consumables |
171 |
|
|
21.2.3 |
Maintenance Materials and External Services |
171 |
|
|
21.2.4 |
Workforce |
172 |
|
|
21.2.5 |
Insurance |
173 |
|
|
21.2.6 |
Miscellaneous costs |
173 |
|
|
21.2.7 |
Sustaining Capital |
173 |
|
|
21.2.8 |
Exclusions |
174 |
|
21.3 QP Opinion |
174 |
|
|
|
22.0 |
Economic Analysis |
175 |
|
|
|
|
22.1 |
Inputs and Assumptions |
175 |
|
|
22.1.1 |
CAPEX |
176 |
xiii |
 |
RSI-3353 |
|
|
22.1.2 |
OPEX |
176 |
|
|
22.1.3 |
Sustaining Capital |
176 |
|
|
22.1.4 |
Cash Flow |
176 |
|
|
22.1.5 |
Construction |
176 |
|
|
22.1.6 |
Operating Life |
176 |
|
|
22.1.7 |
Commodity Pricing |
177 |
|
|
22.1.8 |
Discounted Cash Flow (DCF) |
177 |
|
|
22.1.9 |
Pre-Construction Expenses |
177 |
|
22.2 |
Taxes& Royalties |
177 |
|
|
22.2.1 |
Fees and Royalties |
177 |
|
|
22.2.2 |
Depreciation |
177 |
|
|
22.2.3 |
Corporate Taxes |
177 |
|
|
22.2.4 |
45X MPTC Tax Credit |
177 |
|
22.3 |
CAPEX Spending Schedule |
177 |
|
22.4 |
Production Revenues |
178 |
|
22.5 |
Cash-Flow Projection |
178 |
|
22.6 |
Economic Evaluation Results |
178 |
|
22.7 |
Sensitivity Analysis |
179 |
|
22.8 |
Conclusions and Sensitivity Analysis |
182 |
|
|
|
23.0 |
Adjacent Properties |
183 |
|
|
|
23.1 |
LANXESS Corporation |
183 |
|
23.2 |
Albemarle Corporation |
183 |
|
23.3 |
Saltwerx (Subsidiary to Galvanic, LLC) |
184 |
|
23.4 |
Tetra Technologies |
184 |
|
23.5 |
South West Arkansas Project |
184 |
|
|
|
|
24.0 |
Other Relevant Data and Information |
186 |
|
|
|
25.0 |
Interpretations and Conclusions |
187 |
|
|
|
|
25.1 |
Geology, Resources and Reserve Estimate |
187 |
|
25.2 |
Process Information and Design |
188 |
|
25.3 |
Infrastructure |
189 |
|
25.4 |
Environmental Studies |
189 |
|
25.5 |
Environmental Regulatory Permitting |
189 |
|
25.6 |
Social and Community Impact |
190 |
|
25.7 |
Capital and Operating Costs |
191 |
|
25.8 |
Economic Analysis |
191 |
|
25.9 |
Project Risks |
192 |
|
|
|
|
26.0 |
Recommendations |
194 |
|
|
|
27.0 |
References |
195 |
xiv |
 |
RSI-3353 |
LIST OF
TABLES
Table |
|
|
|
Table
1-1. Description of LANXESS Unitized and Non-Unitized Land Holdings for Brine Production |
4 |
|
|
Table
1-2. LANXESS Project Mineral Resource Estimation by Unit |
5 |
|
|
Table
1-3. LANXESS Project Phase 1A Mineral Reserves Estimation |
6 |
|
|
Table
1-4. Project Permits |
9 |
|
|
Table
1-5. Phase 1A Capital Cost Summary |
10 |
|
|
Table
1-6. Phase 1A Operating Cost Summary |
11 |
|
|
Table
1-7. Phase 1A Financial Results Summary |
12 |
|
|
Table
2-1. Glossary of Terms |
16 |
|
|
Table
2-2. Qualified Persons and Responsibilities |
17 |
|
|
Table
2-3. Contributor Sub-Consultants |
18 |
|
|
Table
2-4. Abbreviations and Acronyms |
19 |
|
|
Table
2-5. Units of Measure |
21 |
|
|
Table
2-6. Minerals |
21 |
|
|
Table
4-1. Description of LANXESS Unitized Land Holdings for Brine Production |
23 |
|
|
Table
4-2. Expected Permits for the Project |
31 |
|
|
Table
6-1. Summary of Historical Brine Analyses (Worley 2019) |
38 |
|
|
Table
6-2. 2018 Inferred Mineral Resource (Eccles et al. 2018) |
40 |
|
|
Table
6-3. Indicated Mineral Resource (Dworzanowski et al. 2019) |
41 |
|
|
Table
9-1. Average of Supply Well Lithium Concentration Data |
56 |
|
|
Table
10-1. Well Data |
59 |
|
|
Table
12-1. Sample Concentration Comparison |
69 |
|
|
Table
13-1. Demonstration Plant LiCl Analysis |
78 |
|
|
Table
13-2. LSS Process Parameters |
84 |
|
|
Table
13-3. OARO Examples |
86 |
|
|
Table
13-4 - LiCl Product Used for Lithium Carbonate Conversion – Trial 1 |
91 |
|
|
Table
13-5 –Lithium Carbonate Product – Trial 1 |
92 |
|
|
Table
13-6 - LiCl Product Used for Lithium Carbonate Conversion – Trial 2 |
93 |
|
|
Table
13-7 - Lithium Carbonate Product – Trial 2 |
94 |
|
|
Table
13-8. LiCl Product Used for Lithium Carbonate Conversion – Trial 3 |
96 |
|
|
Table
13-9. Lithium Carbonate Product – Trial 3 |
97 |
|
|
Table
14-1. Estimated Unit Properties Resulting from Finite Difference Modeling |
109 |
|
|
Table
14-2. Statement of Resources In-Place by Unit effective date, August 18, 2023 |
110 |
|
|
Table
15-1. Phase 1A Proven and Probable Reserves |
115 |
xv |
 |
RSI-3353 |
Table
15-2. Phase 1A Modifying Factors |
115 |
|
|
Table
16-1. Planned South Unit Production by Year for First 25 Years of Production |
122 |
|
|
Table
17-1. Reagent Consumption |
130 |
|
|
Table
20-1. Permits for Project |
151 |
|
|
Table
20-2. Permits for LANXESS South Plant to be Modified |
155 |
|
|
Table
21-1. Project Capital Cost Estimate Summary |
164 |
|
|
Table
21-2. Project Operating Cost Summary |
170 |
|
|
Table
21-3. Reagent Cost Estimate |
171 |
|
|
Table
21-4. Consumable Costs |
171 |
|
|
Table
21-5. Workforce Positions |
172 |
|
|
Table
21-6. Workforce Costs |
173 |
|
|
Table
22-1. Project Economic Model Key Input Parameters |
175 |
|
|
Table
22-2. Project Discounted Cashflow Model |
178 |
|
|
Table
22-3. Project Economic Evaluation |
178 |
|
|
Table
22-4. Sensitivity Analysis to CAPEX Variation |
179 |
|
|
Table
22-5. Sensitivity Analysis to OPEX Variation |
179 |
|
|
Table
22-6. Sensitivity Analysis to Product Price Variation |
179 |
|
|
Table
22-7. Sensitivity Analysis to Production Volume Variation |
180 |
|
|
Table
25-1. Project Economic Analysis Conclusions |
192 |
xvi |
 |
RSI-3353 |
LIST OF
FIGURES
FIGURE |
Page |
|
|
Figure
1-1. Overall Location Map |
3 |
|
|
Figure
1-2. LANXESS Project Phase 1A Production Plan |
7 |
|
|
Figure
1-3. Proposed Project Location |
8 |
|
|
Figure
1-4. Project Schedule |
11 |
|
|
Figure
4-1. Overall Property Location Map |
24 |
|
|
Figure
4-2. Property Location showing LANXESS Plant Locations within Units |
26 |
|
|
Figure
4-3. Land Reserved for Project Facility Construction |
27 |
|
|
Figure
5-1. LANXESS Project Access Routes |
34 |
|
|
Figure
5-2. Average Temperature and Total Precipitation at El Dorado, Arkansas, for 2022 (Weather.gov, 2023) |
35 |
|
|
Figure
6-1. Smackover Formation Lithium Brine Values Derived within, and Adjacent to, the LANXESS Property (Blondes, et al. 2018) |
39 |
|
|
Figure
7-1. Facies Map of the Smackover Formation, Northern Gulf Coast Basin (Budd et al. 1981) |
43 |
|
|
Figure
7-2. Smackover Production Oil and Gas Wells Drilling Information as of May 2023 (Enverus,2023) |
44 |
|
|
Figure
7-3. Structural Framework, Northern Gulf Coast (Budd D.A. et al. 1981). |
45 |
|
|
Figure
7-4. LANXESS Project Area Map |
46 |
|
|
Figure
7-5. Smackover Structure Map |
47 |
|
|
Figure
7-6. Smackover Stratigraphic Column (after Eccles et al. 2018) |
48 |
|
|
Figure
7-7. North-South Cross Section with Geologic Model Oolite 1-6 Zones |
49 |
|
|
Figure
9-1. Well Data Source |
54 |
|
|
Figure
9-2. Standard Lithium Sample Locations |
57 |
|
|
Figure
9-3. Estimated Initial Lithium Concentration |
58 |
|
|
Figure
12-1. Recent Average Well Lithium Concentrations |
66 |
|
|
Figure
12-2. Historical and Recent Well Lithium Concentrations |
67 |
|
|
Figure
12-3. Duplicate Sample Comparison |
70 |
|
|
Figure
13-1. Project Process Block Flow Diagram |
74 |
|
|
Figure
13-2. Standard Lithium Demonstration Plant |
76 |
|
|
Figure
13-3. Tail Brine Measurement Skid at the LANXESS Bromine Tower |
79 |
|
|
Figure
13-4. Sludge Dissolution for Tail Brine pH Adjustment |
81 |
|
|
Figure
13-5. Sludge Dissolution for Brine pH Control |
81 |
|
|
Figure
13-6. Osmotically Assisted Reverse Osmosis System at the Demonstration Plant |
86 |
|
|
Figure
13-7. Calcium Removal with Soda Ash |
87 |
|
|
Figure
13-8. Magnesium Removal with Soda Ash |
88 |
|
|
Figure
13-9. Calcium and Magnesium Ion Exchange System at the Demonstration Plant |
89 |
xvii |
 |
RSI-3353 |
Figure
13-10. Photo of 2nd Stage Lithium Carbonate Crystals |
93 |
|
|
Figure
13-11. Photo of 1st Stage Lithium Carbonate Crystals |
95 |
|
|
Figure
13-12. Photo of 2nd Stage Lithium Carbonate Crystals |
95 |
|
|
Figure
14-1. LANXESS Property Smackover Type Well |
102 |
|
|
Figure
14-2. Porosity Log Net Pay Example |
102 |
|
|
Figure
14-3. Total Gross Pay Map Zones 1-6 |
103 |
|
|
Figure
14-4. Simulation Model Grid Layout |
105 |
|
|
Figure
14-5. Simulation Model Match of Unit Produced Lithium Concentration Data |
106 |
|
|
Figure
14-6. Simulation Model Match of South Unit Well Produced Lithium Concentration Data |
108 |
|
|
Figure
16-1. Typical Brine Source Well Diagram |
117 |
|
|
Figure
16-2. Typical Disposal Well Diagram |
118 |
|
|
Figure
16-3. South Unit Well and Flow Line Configuration |
119 |
|
|
Figure
16-4. South Unit Production - Concentration Estimates |
120 |
|
|
Figure
16-5. Project Production Plan |
121 |
|
|
Figure
17-1. Project Process Block Flow Diagram |
124 |
|
|
Figure
17-2. Standard Lithium and LANXESS Process Block Flow Diagram |
124 |
|
|
Figure
18-1. Proposed Project Facility Location |
131 |
|
|
Figure
18-2. Project Site Overview |
132 |
|
|
Figure
18-3. Brine Supply and Return Pipelines |
133 |
|
|
Figure
18-4. Project Facility Layout |
134 |
|
|
Figure
18-5. Project Brine Pipeline Network |
142 |
|
|
Figure
19-1. Global Lithium-Ion Battery Cell Demand, GWh, Base (after McKinsey & Company 2023). |
143 |
|
|
Figure
19-2. Forecasted Lithium Demand (Albemarle, 2023) |
144 |
|
|
Figure
19-3. Lithium Supply and Demand Forecast (McKinsey & Company, 2023) |
145 |
|
|
Figure
19-4. Global Weighted Average Lithium Carbonate Price From 2016 to Q1 2023 (source, https://tradingeconomics.com/commodity/lithium) |
147 |
|
|
Figure
19-5. Battery Quality Lithium Price Carbonate Scenarios 2023-2030 |
148 |
|
|
Figure
21-1. Project Capital Estimate Component Breakdown |
165 |
|
|
Figure
21-2. Project Schedule |
168 |
|
|
Figure
22-1. Pre-Tax IRR Sensitivity |
180 |
|
|
Figure
22-2. Post-Tax IRR Sensitivity |
180 |
|
|
Figure
22-3. Pre-Tax NPV Sensitivity |
181 |
|
|
Figure
22-4. Post-Tax NPV Sensitivity |
181 |
|
|
Figure
23-1. Location of Active and Potential Brine Producers in Southern Arkansas |
185 |
xviii |
 |
RSI-3353 |
Standard Lithium Ltd. (Standard Lithium
or Company) is a lithium development company with a portfolio of lithium production projects proposed for development in the United States
of America (USA). The LANXESS Project refers to a suite of contemplated staged expansion projects relating to the LANXESS South, Central,
and West Brine Production Units. This Commercial Lithium Extraction Plant Project at LANXESS South Plant (Phase 1A or Project) is the
first stage of development of the LANXESS Project.
It is proposed that the Project will
receive lithium-rich brine currently being produced from the Smackover Formation by LANXESS for their existing South Plant, and following
bromine processing by LANXESS, extract the lithium from the residual brine using Direct Lithium Extraction technology, convert it to
battery quality lithium carbonate, and then return the lithium-depleted brine to the existing South Plant brine disposal network for
reinjection into the Smackover Formation.
Standard Lithium is a jointly listed
company on the TSX Venture Exchange (stock symbol TSXV:SLI), New York Stock Exchange (stock symbol: NYSE American:SLI), and Frankfurt
Stock Exchange (stock symbol: Frankfurt Exchange:S5L), with their head office in Vancouver, BC.
RESPEC Company, LLC (RESPEC) was commissioned
by Standard Lithium to provide an independent Qualified Person’s (QP) review and National Instrument (NI) 43-101 Technical Report
(TR) on the commercial viability of lithium extraction on a mass scale from brine that is already produced for an existing bromine production
facility operated by LANXESS Corporation (LANXESS) located near the town of El Dorado in Union County, Arkansas, USA.
LANXESS has the exclusive brine extraction
rights for a contiguous block of 60,477 hectares (ha) [149,442 acres (ac)], contained within three brine production units, referred to
as the South, Central and West Brine Units of which 15,458 ha [38,198 ac] make up the South Unit, the Property associated with the Project.
The purpose of this report is to summarize
the results of the feasibility of the Project at the LANXESS South Plant including establishment of the associated brine Mineral Reserves
and update the broader Mineral Resources for the overall LANXESS Project. The Definitive Feasibility Study (DFS) encompassed the geologic
modeling, resource and reserve estimation, extraction planning and design, methodology and equipment, hydrogeology modeling, surface
infrastructure requirements, labor, lithium processing Demonstration Plant test work results, lithium brine field operations, environmental
and permitting, marketing, project economics, project development schedule, and risks in developing the Project.
Standard Lithium’s objective is
to become a leading American producer of high-quality lithium products from the Smackover region to supply domestic lithium markets and
address long-term supply deficits. With the completion of the DFS the Project has demonstrated feasibility and established that lithium
can be profitably extracted from Smackover brine.
1 |
 |
RSI-3353 |
The LANXESS property is located south
of the City of El Dorado in Union County, AR, USA, as presented in Figure 1-1. The southern and western edges of the Property border
the state of Louisiana (LA) and Columbia County, respectively. The Property encompasses Townships 16-19 South, and Ranges 14-18, West
of the 5th Meridian (W5M). The Property center is at Universal Transverse Mercator (UTM) 520600 Easting, 3670000 Northing,
Zone 15N, NAD83.
LANXESS has the rights to extract brine
from the South, Central, and West brine production units through the unitization by the Arkansas Oil and Gas Commission (AOGC). Definitive
commercial agreements between LANXESS and Standard Lithium, once in effect, will grant Standard Lithium the associated rights required
for lithium extraction. The production units, which are shown on the property overview in Figure 1-1, consist of 60,477 ha [149,442 ac]
that cover over 608 square kilometers (km2). Table 1-1 provides a description of the LANXESS Unitized land holdings. Each
of the three Units (South, Central, and West) has their own brine supply wells, pipeline network, and bromine processing (extraction)
infrastructure. The South Unit, which where referenced includes the South Unit Expansion, is the focus of the Project.
Standard Lithium and LANXESS signed
a binding Revised and Restated Memorandum of Understanding (MOU) which forms the basis on which the parties agree to cooperate in a phased
process towards developing commercial opportunities related to the production, marketing, and sale of battery-quality lithium products
for South, Central and West Brine units (Standard Lithium Ltd., 2022). Specifically, the MOU sets out the process for the establishment
of definitive commercial agreements between the parties, which once in place, will grant Standard Lithium rights required for development
of the Project which is associated with the South Brine Unit and govern the broader relationship throughout the life of the Project.
The MOU also provides LANXESS an option to acquire an ownership interest in the Project. A separate access, license and reservation agreement
between the parties provides Standard Lithium the exclusive rights to 39 ha of surface lands for development of the Project and potential
future stages of the LANXESS Project as well as access to the property for development purposes.
2 |
 |
RSI-3353 |
Figure 1-1. Overall Location
Map
3 |
 |
RSI-3353 |
Table 1-1.
Description of LANXESS Unitized and Non-Unitized Land Holdings for Brine Production
|
|
AOGC Order
Reference |
|
Date | | |
Acres | | |
Hectares | |
South Plant Brine Unit |
|
BU 1-1995 |
|
March 28,
1995 | | |
| 30,877 | | |
| 12,495 | |
South Expansion Brine Unit |
|
086-1-2016-11 |
|
November 28,
2016 | | |
| 7,321 | | |
| 2,963 | |
Central Plant Brine Unit |
|
BU 2-1995 |
|
August 22,
1995 | | |
| 42,974 | | |
| 17,391 | |
Central Expansion Brine Unit |
|
095-2022-12 |
|
January 5,
2023 | | |
| 6,560 | | |
| 2,655 | |
West Plant Brine Unit |
|
BU 3-1995 |
|
November 28,
1995 | | |
| 60,354 | | |
| 24,424 | |
West Expansion Brine Unit-H |
|
048-2-2015-04 |
|
May 14,
2015 | | |
| 1,356 | | |
| 549 | |
Notes:
[1] The expansion brine units listed
in the table are to differentiate the AOGC orders and dates from the original area brine units. Unless specifically stated in the TR,
any reference to an area brine unit includes the associated expansion brine unit.
1.2 | Geology
and Mineralization |
The focus of this resource assessment
is the lithium bearing Smackover Formation in southern Arkansas. The Smackover Formation, Upper Jurassic in age, is commonly subdivided
into two intervals: Upper and Lower.
The Upper Smackover interval is the
development target for the Project and has been subdivided into the Reynolds Member oolite, an oolitic limestone, and the Middle Smackover.
The Lower Smackover interval, also known as the Brown Dense, is composed of dark, dense limestone with argillaceous bands. The structure
of the Smackover in the Property generally dips from north-northeast to south-southwest and varies in depth from approximately 1,920
meters [6,300 feet] subsea to approximately 2,621 meters [8,600 feet] subsea.
The Smackover Formation’s productive
characteristics have been extensively characterized by the drilling of over 1,000 wells in approximately 600 former and producing oil
and gas fields, with approximately 150 of those fields in Arkansas.
No new exploration drilling has occurred
for this TR as all production wells proposed for the Project are already constructed and producing. The lithium concentration data used
in this TR resulted from brine samples collected by Standard Lithium from 2017 through May 2022 and analyzed by Western Environmental
Testing Laboratory (WetLab). The concentration data for each well was used to develop a map of the initial distribution of lithium throughout
the Property which formed the basis for the computer simulation model-based estimates. In addition, the brine samples collected at the
inlet of each of the processing facilities were used to quantify the inlet lithium concentrations at the three bromine processing facilities
for comparison to the simulation model’s initial predicted values.
1.4 | Mineral
Resource Estimate |
A geologic multi-zone model of the Property
was constructed using Petra® that serves the basis of the brine body simulation model. The geologic mapping covered the Property
and the surrounding area. The volume of porous rock as described in the geologic model and the estimated lithium concentrations present
in the brines stored within the formation on the Property serve as the basis for the Mineral Resource estimate.
4 |
 |
RSI-3353 |
The geologic multi-zone model was input
into a Merlin finite-difference reservoir simulation model to estimate the resources present in each of the three Units. The Merlin finite-difference
reservoir simulation model was used to model brine content, brine movement, bromine recovery, and lithium recovery. Simulation was required
to estimate the resources because the ongoing production and injection of brine for bromine recovery project, while not altering the
overall lithium content of the Property, results in geographical changes in lithium concentration over time.
Mineral Resources are subdivided in
order of increasing geological confidence into Inferred, Indicated, and Measured categories. The total in-situ Measured and Indicated
Brine Resource for the LANXESS Project are estimated at 2.8 Mt of Lithium Carbonate Equivalent (LCE) or 529,000 tonnes of elemental lithium
at an average lithium concentration of 148 mg/L across all three units.
Table 1-2.
LANXESS Project Mineral Resource Estimation by Unit
Category | |
Units | |
South | | |
West | | |
Central | | |
Central
Expansion | | |
Total | |
Lithium Concentration | |
mg/L | |
| 204 | | |
| 122 | | |
| 164 | | |
| 78 | | |
| 148 | |
Measured Resource | |
thousand tonnes | |
| 148 | | |
| 192 | | |
| 173 | | |
| - | | |
| 513 | |
Indicated Resource | |
thousand tonnes | |
| - | | |
| - | | |
| - | | |
| 16 | | |
| 16 | |
Measured LCE Resource | |
thousand tonnes | |
| 788 | | |
| 1,022 | | |
| 921 | | |
| - | | |
| 2,731 | |
Indicated LCE Resource | |
thousand tonnes | |
| - | | |
| - | | |
| - | | |
| 85 | | |
| 85 | |
Notes:
[1] Volumes are
in-place.
[2] Cutoff of 9%
porosity.
[3] The effective
date is August 18, 2023.
[4] Mineral Resources
are inclusive of Mineral Reserves.
[5] The Qualified
Persons for the Mineral Resource Estimates is Randal M. Brush, PE and Robert E. Williams, Jr., PG, CPG.
[6] The Mineral
Resource estimate follows 2014 CIM Definition Standards and the 2019 CIM MRMR Best Practice Guidelines.
[7] These Mineral
Resources are not Mineral Reserves as they have not demonstrated economic viability.
[8] Calculated brine
volumes only include Measured and Indicated Mineral Resource volumes that when blended from the well field result in feed above the cut-off
grade of 100 mg/L.
[9] Lithium Carbonate
Equivalent (LCE) is calculated using mass of LCE = 5.323 multiplied by mass of lithium metal.
[10] Results are presented
in-situ. The number of tonnes was rounded to the nearest thousand. Any discrepancies in the totals are due to rounding effects.
[11] The Qualified
Person is not aware of any known environmental, permitting, legal, title-related, taxation, socio-political or market issues, or any
other relevant issue that could materially affect the potential development of Mineral Resources other than those discussed in the Mineral
Resource Estimates.
5 |
 |
RSI-3353 |
1.5 | Mineral
Reserve Estimate |
Reserves were calculated from the simulated
Smackover Formation brine production rates as applied to the South Unit. Proven and Probable Reserves were estimated from the Measured
and Indicated Resources based on the forecast operating capacity of the South Plant brine supply and disposal network projected for a
25 and 40-year period.
Proven and Probable Lithium Brine Reserves
are estimated to be recovered by the Project over a 25-year forecast period, with the anticipated Project start-up in 2026. Probable
Lithium Brine Reserves are estimated to be recovered from year 26-40.
Table 1-3.
LANXESS Project Phase 1A Mineral Reserves Estimation
Category | |
Units | |
Proven | | |
Probable | | |
Proven
+ Probable | |
Brine Reserves | |
million m³ | |
| 124 | | |
| 84 | | |
| 209 | |
Average Lithium Concentration | |
mg/L | |
| 227 | | |
| 201 | | |
| 217 | |
Lithium Metal | |
thousand tonnes | |
| 28.2 | | |
| 17.0 | | |
| 45.2 | |
LCE Reserves | |
thousand tonnes | |
| 129 | | |
| 79 | | |
| 208 | |
Notes:
[1] The effective date is August18,
2023.
[2] Any discrepancies in the totals
are due to rounding effects.
[3] The Qualified Person for the Mineral
Reserve estimate is Randal M. Brush, PE.
[4] Converted Reserves are exclusive
to the South Brine Unit.
[5] The average lithium concentration
is weighted per well simulated extraction rates.
[6] The Proven
case assumes a 25-year operating life at 4.96 million m3/year of brine production at a cut-off of 100 mg/L.
[7] Proven plus
Probable reserves assume a 40-year operating life at 5.21 million m3/year of brine production at a cut-off of 100 mg/L.
[8] The Reserves
reference point for the Brine Pumped, Average Lithium Concentration, and Lithium Metal is the brine inlet to the processing plant.
[9] The Reserves
reference point for the LCE is the product output of the processing plant.
[10] Lithium Carbonate
production values consider plant processing efficiency factors.
[11] The Mineral
Reserve estimate follows 2014 CIM Definition Standards and the 2019 CIM MRMR Best Practice Guidelines.
[12] Lithium Carbonate
Equivalent (“LCE”) is calculated using mass of LCE = 5.323 multiplied by mass of lithium metal.
[13] The Qualified Person is not aware
of any known environmental, permitting, legal, title-related, taxation, socio-political or marketing issues, or any other relevant issue,
that could materially affect the potential development of Mineral Resources other than those discussed in the Mineral Resource Estimates.
Recovery of the lithium will use the
existing LANXESS South Unit brine production facilities to supply the Feed Brine from the LANXESS South Plant to the Project. Once the
lithium is extracted from the brine, the processed brine will be reinjected into existing LANXESS South Unit brine disposal wells.
The Project contemplates production
of battery-quality lithium carbonate averaging 5,400 tonnes per annum (tpa) over a 25-year operating life, producing 135,000 tonnes LCE
from the LANXESS South Brine Unit.
6 |
 |
RSI-3353 |
The Project has the potential to operate
over a 40-year life based on the Proven and Probable Reserves of 208,000 tonnes LCE. The TR makes very conservative assumptions that
production of brine will occur from the existing wellfield, and that no additional wells are drilled in the future to supplement or add
to the current brine flow, or to add additional brine from higher lithium content zones available in the production unit(s). See Figure
1-2 for the annual production plan.
Figure 1-2. LANXESS Project Phase
1A Production Plan
The Standard Lithium plant utilizes
the Lithium Selective Sorption (LSS) process to directly extract lithium ions from bromine depleted pretreated Smackover brine delivered
from the LANXESS South plant. LSS is a Koch Technology Solutions, LLC (KTS) proprietary technology. Under the joint development agreement
with KTS, Standard Lithium has Smackover regional exclusivity for the LSS process for a period of time. Eluate from the LSS process (raw
lithium chloride solution) is concentrated and purified and subsequently converted into battery-quality lithium carbonate.
Standard Lithium proposes to process
up to 680 m3/hr [3,000 US gpm] of brine containing on average 227mg/L lithium over the 25-year life of the Project. The brine
is filtered, pH and temperature adjusted, followed by lithium extraction using the LSS process. The LSS product eluate is concentrated
by conventional reverse osmosis, chemically softened for calcium and magnesium removal, and then passed through ion exchange columns
to remove the residual calcium, magnesium, and boron. The treated brine is further concentrated by Osmotically Assisted Reverse Osmosis
(OARO) prior to conventional two-stage lithium carbonate crystallization to produce up to 5,730 tonnes per year of lithium carbonate.
The effluent brine is returned to the LANXESS facility for reinjection into the Smackover Formation through existing injection wells.
Standard Lithium has operated a Demonstration
Plant, exclusively processing Smackover brine from LANXESS South Unit, since May 2020. This has provided a valuable source of knowledge
in regard to the behavior of the brine, direct testing of various process elements, and providing a test bed for operator training. In
addition, the Demonstration Plant has facilitated an ability to produce lithium chloride samples along with brine samples from various
stages of the process to support additional bench scale metallurgical testing, mini-pilot plant testing and vendor testing in support
of equipment design and process guarantees. The testing undertaken during the DFS phase produced battery-quality lithium carbonate from
LANXESS South Unit brines processed through the Demonstration Plant, confirming the viability of the process.
7 |
 |
RSI-3353 |
Based on the performance at the Demonstration
Plant, process modelling, and various performance and design criteria from potential equipment vendors, the processing facility is expected
to recover 93.1% of the lithium contained in the brine delivered by LANXESS into battery-quality lithium carbonate.
1.8 | Project
Infrastructure |
The proposed Project Facility is strategically
located on undeveloped lands adjacent to the existing LANXESS South Plant to allow interconnection with key elements of existing LANXESS
South Plant infrastructure, specifically the brine handling system. Supporting services including power, natural gas, and water is readily
available and in close proximity to the Project Site.
Figure 1-3. Proposed Project
Location
Brine will be delivered to and from
the Project Facility via two new fiberglass pipelines connecting the facility and the existing South Plant Tail Brine system. The processing
plant includes facilities required for brine pre-treatment, direct lithium extraction, effluent brine handling, chemical softening, ion
exchange, lithium chloride concentration, lithium carbonate production and product drying, milling, and packaging. The Project Facility
also includes an administration building, hourly workers building, warehouse, maintenance shop, onsite laboratory, and guardhouse in
support of the approximately 90 people anticipated to be required for its operation.
Natural gas will be delivered by Energy
Transfer from their existing supply pipeline located north of the South Plant via a short dedicated interconnecting pipeline constructed
and operated by the Project. A dedicated and independent power supply will be provided for the Project Facility by Entergy from their
115kV El Dorado Upland Substation which is located immediately to the east of the Project Facility. Two new Underground Injection Control
Class I non-hazardous injection wells for disposal of any excess barren brine are also proposed to be constructed by the Project.
8 |
 |
RSI-3353 |
The demand for lithium
is expected to continue to outpace supply for the foreseeable future even with the new supplies coming online due predominantly to the
energy transition for lithium battery materials. For purposes of estimating project future cash flows a conservative price of $30,000/tonne
was selected for use in economic evaluations over the lifetime of the project.
1.10 | Environmental
Permitting |
The Project is not subject to review
under the National Environmental Policy Act (NEPA). Construction and operational emissions to air, surface waters, and subsurface waters
are regulated by the federal and state agencies to protect the environment while allowing responsible development of the lithium resources.
Table 1-4 lists the permits required by the Project Company. In addition, the existing LANXESS brine reinjection permit will be modified
to include the Project Facility. The permit modification request will be initiated by LANXESS and supported by the Project.
Standard Lithium has initiated early
consultation with permitting agencies for the construction and operation of the Project. A Baseline Environmental Site Assessment has
been conducted as well as investigations of jurisdictional waters of the U. S., wildlife studies, and cultural resources of the Project.
Table 1-4.
Project Permits
Agency |
|
Permitted
Activity |
USACE |
|
Placement of fill in waters
of the U.S. |
ADEE-DEQ |
|
Air Permit for Commercial Facility |
ADH |
|
Fresh Water Supply for Potable
Water |
ADEE-DEQ |
|
Construction Storm Water NPDES
Permit for Facility Construction Site |
ADEE-DEQ |
|
Surface Discharge of Non-Brine
Process Wastewater, Non-contact Cooling Water, Treated Sanitary Wastewater |
ADEE-DEQ |
|
Construction of Treatment System
Associated with a NPDES Permit |
ADEE-DEQ |
|
Stormwater Discharges from
a Categorical Industry |
ADEE-DEQ |
|
Construct/Operate Surface Facility
for New Class I Nonhazardous Injection Wells |
ADEE-DEQ |
|
Construct/Operate New Class I
Nonhazardous Injection Wells |
ADEE-AOGC |
|
Construct Drilling Pit for
Class 1 Nonhazardous Injection Wells |
ADEE-DEQ |
|
Transfer Barren Brine to LANXESS
No-Discharge Permitted Facility |
9 |
 |
RSI-3353 |
1.11 | Capital
and Operating Expenses |
The total capital cost (CAPEX), including
contingency, to construct the Project is estimated at $365 million. Direct project costs represent $259 million and indirect Project
Costs represent $56 million of the total cost. A contingency of $50 million is included, which equates to approximately 15% of direct
and indirect costs.
The capital cost estimate is considered
to have an accuracy range of -15% to +20%. All costs are expressed in 2023 US Dollars. No allowances are included for cost escalation.
The total estimated capital cost for
the Project by area is summarized in Table 1-5.
Table 1-5.
Phase 1A Capital Cost Summary
Area |
|
Capital
Cost ($M) |
Brine
Delivery (Tie-ins) |
|
9.0 |
Brine
Pretreatment |
|
43.3 |
Direct
Lithium Extraction |
|
38.1 |
Concentration
and Purification |
|
53.3 |
Carbonation |
|
53.4 |
Drying,
Milling and Packaging |
|
18.9 |
Effluent
Brine Disposal |
|
24.3 |
Reagent
Systems |
|
8.8 |
Utilities |
|
51.1 |
Other
(First Fills, Membranes, Commercial Fees) |
|
14.7 |
Contingency
|
|
49.9 |
Total
Capital Cost |
|
364.9 |
Notes:
[1] Direct costs
were estimated using either vendor-supplied quotes, and/or engineer estimated pricing (based on recent experience) for all major equipment.
[2] Indirect costs
include all contractor costs (including engineering); indirect labor costs and Owner’s Engineer costs.
[3] Any discrepancies
in the totals are due to rounding effects.
Standard Lithium has undertaken efforts
to effectively de-risk the construction process for the Project and ensure on-time delivery. This includes a Term Sheet with the nominated
EPC contractor, Optimized Process Designs LLC, which sets out construction performance and schedule guarantees to ensure on-time construction,
as well as guarantees related to the production of battery-quality lithium carbonate at the facility’s design capacity. This Term
Sheet is subject to agreement between the parties on pricing and definitive documentation.
The
capital cost estimate is based on construction and commissioning of the facility in accordance with the Project contracting strategy
and Project schedule as outlined in Figure 1-4. The Company expects to make a Final Investment Decision in the first half of 2024 which
would result in first production of lithium carbonate in 2026.
10 |
 |
RSI-3353 |
Figure 1-4. Project Schedule
The operating cost for the life of the
Project is estimated to be $6,810/t of lithium carbonate. Labor, reagents, consumables, and energy account for over 70% of the operating
costs. All-in operating cost, including sustaining capital expenditures is $7,390/t. A summary of the operating costs is included in
Table 1-6.
Table 1-6.
Phase 1A Operating Cost Summary
Category |
|
Average
Annual Cost ($/t) [1] |
|
Electrical
Power and Infrastructure |
|
950 |
|
Reagents
and Consumables |
|
2,880 |
|
Maintenance
and External Services [2] |
|
610 |
|
Workforce
[3] |
|
1,930 |
|
Insurance |
|
340 |
|
Miscellaneous
Costs [4] |
|
100 |
|
Total
Operating Cost |
|
6,810 |
|
Sustaining
Capital Expenditures [5][6] |
|
580 |
|
All-in
Operating Cost |
|
7,390 |
|
Notes:
[1] Operating costs
are calculated based on average annual production of 5,400 tonnes of lithium carbonate.
[2] Includes contract
maintenance, solids waste disposal, and external lab services.
[3] Approximately
89 full time equivalent positions.
[4] Includes general
and administrative expenses.
11 |
 |
RSI-3353 |
[5] Does not include future brine lease-fees-in-lieu-of-royalties
which are still to be determined and subject to regulatory approval (lease-fees-in-lieu-of-royalties have been determined for bromine
and certain other minerals in the State of Arkansas but have not yet been determined for lithium extraction).
[6] Does not include brine fees which
may be due to LANXESS as a result of finalization of the commercial arrangements between LANXESS and Company.
The financial results are derived from
inputs based on the annual production schedule summarized in Table 1-7. Sensitivity analysis on the unlevered economic results over a
25-year operating life are summarized in Table 1-7.
Table 1-7.
Phase 1A Financial Results Summary
Category | |
Units | |
Value | |
Initial
Annual Production of Li2CO3 | |
| tpa[1] | |
| 5,730 | [2] |
Average
Annual Production of Li2CO3 | |
| tpa | |
| 5,400 | |
Plant Operating Life | |
| years | |
| 25 | [3] |
Total Capital Expenditures | |
| $millions | |
| 365 | [4,
5] |
Average Annual Operating Cost | |
| $/t | |
| 6,810 | |
Average Annual All-in Operating cost | |
| $/t | |
| 7,390 | [6,
7] |
Selling Price | |
| $/t | |
| 30,000 | [8] |
Discount Rate | |
| % | |
| 8 | |
Net Present Value (NPV) Pre-Tax | |
| $millions | |
| 772 | |
NPV After-Tax | |
| $millions | |
| 550 | [9] |
Internal Rate of Return (IRR) Pre-Tax | |
| % | |
| 29.5 | |
IRR After -Tax | |
| % | |
| 24.0 | |
Notes:
[1] Tonnes (1,000 kg) per annum.
[2] Initial annual production figure
represents Year 2 production, following a ramp-up period in Year 1.
[3] Plant design and financial modelling
based on 25-year economic life. Proven and Probable Reserves support a 40-year operating life.
[4] Capital expenditures include 15%
contingency.
[5] No inflation or escalation has been
carried out for the economic modelling.
[6] Includes operating expenditures
and sustaining capital.
[7] Brine lease-fees-in-lieu-of-royalties
(to be approved by AOGC) have not been defined and are not currently included in the economic modelling.
[8] Selling price of battery-quality
lithium carbonate based on a flatline price of $30,000/t over total project lifetime.
[9] Assumes a U.S. Federal tax rate
of 21% and State of Arkansas Tax rate of 5.1%, as well as variable property taxes.
12 |
 |
RSI-3353 |
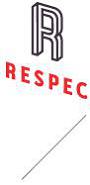
Sensitivity analysis on the unlevered
economic results over a 25-year operating life are summarized in Table 1-8.
Table 1-8. Sensitivity
Analysis Summary
Category | |
After-tax NPV
($millions) | | |
After-Tax IRR (%) | |
| |
| | |
| |
Li2CO3
Price | |
| |
-20% | |
| 337 | | |
| 18.4 | |
0% | |
| 550 | | |
| 24.0 | |
+20% | |
| 762 | | |
| 29.3 | |
Production | |
| | | |
| | |
-5% | |
| 502 | | |
| 22.8 | |
0 | |
| 550 | | |
| 24.0 | |
+5% | |
| 597 | | |
| 25.3 | |
Capital Costs | |
| | | |
| | |
+20% | |
| 491 | | |
| 20.4 | |
0% | |
| 550 | | |
| 24.0 | |
-20% | |
| 608 | | |
| 29.2 | |
Operating Costs | |
| | | |
| | |
+20% | |
| 507 | | |
| 22.9 | |
0% | |
| 550 | | |
| 24.0 | |
-20% | |
| 592 | | |
| 25.2 | |
1.13 | Qualified
Person’s Conclusions |
The Project has been independently evaluated,
leading to the following conclusions and interpretations regarding the suitability of the proposed site and the viability of the Project.
It is determined that a clear path is established to reach a positive Final Investment Decision subject to concluding remaining commercial
agreements and obtaining the required financing.
| / | The
Proven and Probable Reserves confirm the viability of the Project over its 25 year economic
life at an average annual production rate of 5,400 tonne per annum of lithium carbonate. |
| / | The
Proven and Probable Reserves support an operating life of up to 40 years. |
| / | The
development and testing completed at the Demonstration Plant provides a robust basis for
the commercial design which is based on Direct Lithium Extraction technology. |
| / | Work
to date completed at the Demonstration Plant illustrates that lithium can be economically
extracted from the lithium rich brine produced from the Smackover Formation. |
| / | The
Project Site secured is considered well suited for development and is situated near all required
utilities. |
| / | Environmental
studies have concluded the site is suitable for development with limited adverse environmental
and social impacts, generally limited to the boundaries of the Project Site. |
| / | There
is a clear pathway for the Project to obtain the state permits required for development. |
13 |
 |
RSI-3353 |
| / | The
economic analysis yielded positive results in a timeline for development and first production
that is considered realistic based on timely funding and is typical of projects of similar
magnitude within industry. |
| / | Overall,
the result of this Feasibility Study demonstrates that lithium can be economically extracted
from the lithium rich brine within the Smackover Formation. |
1.14 | Qualified
Person’s Recommendations |
The Qualified Persons involved in the
Report make the following recommendations:
| / | Obtain
and review any new log and core data collected in the West, Central, and South Brine Units
which may become available in the future. |
| / | Continue
to monitor the LANXESS South Unit brine production performance. |
| / | Continue
test work at the Demonstration Plant. |
| / | Continue
to advance key permits and authorizations required for construction and operation of the
Project. |
| / | Address
the responsibility for pre-existing environmental conditions in commercial agreements. |
| / | Continue
the process of establishing project-specific lithium royalties (lease-fees-in-lieu-of-royalties)
with the AOGC. |
| / | Evaluate
and pursue additional federal and state incentive programs which may be available to improve
overall Project economics. |
| / | Given
the sensitivity of the Project economics to the product price, consider offtake pricing mechanisms,
to mitigate the commercial risk associated with short-term lithium price fluctuations. |
| / | Finalize
definitive commercial agreements with LANXESS and other parties which are required to support
a positive Final Investment Decision. |
14 |
 |
RSI-3353 |
2.1 | Terms
of Reference and Purpose of Report |
This Technical Report (TR) was prepared
by RESPEC Company, LLC (RESPEC) at the request of Standard Lithium Ltd. (Standard Lithium, or the Company), a Canada Business Corporations
Act company, for a Definitive Feasibility Study (DFS) of the Commercial Lithium Extraction Plant Project (Phase 1A of the LANXESS
Project, or the Project) and an update of the Mineral Resource, located in Arkansas, USA. Standard Lithium, trading under the symbol
SLI on the TSX Venture Exchange, the New York Stock Exchange, and the Frankfurt Exchange, is headquartered at 1625-1075 West Georgia
Street, Vancouver, British Columbia.
Phase 1A, Standard Lithium’s first
commercial lithium extraction plant, is proposed to be located at the LANXESS South Plant, approximately 13 kilometers [8 miles] southwest
of the City of El Dorado in Union County, Arkansas. LANXESS Corporation, a US subsidiary of LANXESS AG, a specialty chemicals company,
has exclusive brine extraction rights for 60,477 hectares [149,442 acres] which is contained within three brine production units, referred
to as the South, Central, and West Brine Units. The development process for the Project, including development of definitive commercial
agreements, equity participation and phasing are governed by a Memorandum of Understanding (MOU) between Standard Lithium and LANXESS.
This TR considers lithium brine at the
Project that is present in the brines throughout the LANXESS South, Central, and West Brine Units. The Mineral Resources and Mineral
Reserve estimates presented in this report have been prepared in accordance with the Canadian Institute of Mining, Metallurgy and Petroleum
(CIM) CIM Estimation of Mineral Resources and Mineral Reserves Best Practice Guidelines (CIM, 2019) and CIM Definition Standards
for Mineral Resources and Mineral Reserves (CIM, 2014), as referred to in National Instrument (NI) 43-101 and Form 43-101F,
Standards of Disclosure for Mineral Projects and in force as of the effective date of this report. This is consistent with CIM Best
Practice Guidelines for Resource and Reserve Estimation for Lithium Brines (CIM, 2012), in which it is stated that the CIM considers
brine projects to be mineral projects, as defined in NI 43-101.
In this TR, the terms “Mineral
Resource,” “Inferred Mineral Resource,” “Indicated Mineral Resource,” “Measured Mineral Resource,”
“Proven Mineral Reserve,” and “Probable Mineral Reserves” have the meanings ascribed to those terms by the CIM
Definition Standards on Mineral Resources and Mineral Reserves adopted by CIM Council, as amended. Investors are cautioned that Mineral
Resources cannot be classified as Mineral Reserves until further work is completed to upgrade the material’s classification. Resources
also cannot be reclassified until other economic and technical feasibility factors based upon such work have been resolved and can be
demonstrated that the Resources may be legally and economically extracted and produced. As a result, investors should not assume that
all or any part of the mineralized material reported in any of these categories referred to in the Resource Estimate and this TR will
be converted into Mineral Reserves.
Throughout this TR, geological, technical,
and lithium industry-specific terminology is commonly used. Table 2-1 provides a list of definitions for the most common terms and phrases.
15 |
 |
RSI-3353 |
Table 2-1.
Glossary of Terms
Term |
|
Definition |
Assay |
|
A test performed to determine
a mineral sample’s chemical content. |
Brine Expansion Unit |
|
Each separate composite area
of land so designated by order of the AOGC as an expansion area adjacent to an existing brine production unit to produce brine or
the reinjection of effluent. |
Brine Production Unit |
|
Each separate composite area
of land so designated by order of the Arkansas Oil and Gas Commission (AOGC) to produce brine and the reinjection of effluent. |
Bypass Brine |
|
The output brine that has bypassed
the LANXESS bromine facility. |
Company |
|
Standard Lithium Ltd. (Standard
Lithium) and its subsidiaries. |
Eluate |
|
A liquid solution resulting
from desorbing an absorbed material using a solvent. |
Feed Brine |
|
The input brine to the Project. |
Final Investment Decision |
|
A milestone activity to determine
the Project will proceed with acquiring funding. |
LANXESS Project |
|
Suite of contemplated
staged expansion projects relating to the LANXESS South, Central, and West Brine Production Units for lithium extraction. |
Project |
|
Commercial Lithium Extraction
Plant Project at the LANXESS South Plant which is Phase 1A of the LANXESS Project. |
Project Company |
|
Standard Lithium Ltd. El Dorado
South LLC, a wholly owned subsidiary of Standard Lithium. |
Project Facility |
|
The buildings and areas associated
to the Commercial Lithium Extraction Plant Project under future Standard Lithium Ltd. control. |
Project Site |
|
Location at which the Commercial
Lithium Extraction Plant Project is to occur. |
Property |
|
LANXESS South, Central and
West Units. |
Raffinate |
|
The liquid which comes out
of an extraction process involving two liquids. |
Tail Brine |
|
The output brine from the LANXESS
bromine facility. |
16 |
 |
RSI-3353 |
Table 2-2 presents the Qualified Persons
(QPs) for the Technical Report and their responsibilities.
Table 2-2.
Qualified Persons and Responsibilities
Qualified
Person |
|
Company |
|
Chapter(s) |
Susan B. Patton, PE |
|
RESPEC Company, LLC |
|
Chapters 1–6, 19, 23–27 |
Randal M. Brush, PE |
|
William M. Cobb &
Associates, Inc. |
|
Chapters 7–12, 14–16 |
Robert E. Williams, Jr., CPG |
|
William M. Cobb &
Associates, Inc. |
|
Chapters 7–12, 14–16 |
Mike Rockandel, RM-SME |
|
Mike Rockandel Consulting,
LLC |
|
Chapters 13, 17, 18, 21 |
Charles Daniel Campbell, PE |
|
Alliance (formerly GBMc &
Associates) |
|
Chapter 20 |
Frank Gay, PE |
|
Hunt, Guillot & Associates,
LLC |
|
Chapter 22 |
Notes:
CPG, Certified Professional Geologist
PE, Professional Engineer
PG, Professional Geologist
RM-SME, Registered Member Society for
Mining, Metallurgy and Exploration
2.3 | Personal
Inspection of Property by Qualified Persons |
The following QPs personally inspected
the Standard Lithium Project Site:
| / | Randal
Brush, PE, and Robert E. Williams, Jr., PG, visited the Standard Lithium Project Site May 17
through 19, 2022, and participated in sampling 10 different operating brine supply wells
at the LANXESS bromine Property. LANXESS personnel captured the samples, which were observed,
recorded, labeled, and shipped to the laboratory for assay. Standard Lithium personnel were
present and obtained additional samples. The sample results make up part of the lithium concentration
data used in the analyses. |
| / | Charles Daniel Campbell, PE, visited the Standard Lithium Project Site on November 8, 2022, where he
performed a reconnaissance of the proposed site to examine surface topography including surface
water run-on from the adjacent property and runoff pathways. He confirmed locations for permanent
groundwater monitoring wells to be installed and the general conditions of the undeveloped
site. |
| / | Mike
Rockandel, RM-SME, visited the Standard Lithium Project Site October 10 through 12,
2022, where he viewed the process tie-points, visited the Demonstration Plant for 1 day,
and visited the laboratory to understand the analytical requirements. Mike held numerous
discussions with plant personnel on operating issues and reviewed historical data. |
| / | Susan
Patton visited the Standard Lithium Demonstration Plant site on June 27, 2023. She viewed
the Tail Brine input from LANXESS, toured the operating Demonstration Plant, laboratory,
and the proposed location of the commercial plant. |
2.4 | Sources
of Information |
This TR is based, in part, on internal
company technical reports, maps, company letters, memoranda, public disclosure, and public information, as listed in the NI 43-101
Technical Report Preliminary Economic Assessment of LANXESS Smackover Project (Worley, 2019). Information brought forward from previous
reports has been reviewed and verified as accurate by the QPs.
17 |
 |
RSI-3353 |
The sub-consultants presented in Table
2-3 were contracted to complete specific technical studies/analyses for input into the DFS Report.
Table 2-3.
Contributor Sub-Consultants
Sub-Consultants |
|
Area
Contribution |
Alliance
(formerly GBMc & Associates) |
|
Permitting
and Site Conditions |
Hunt, Guillot &
Associates |
|
FEED |
M3 Engineering |
|
FEED |
Optimized
Process Design |
|
FEED |
RHI-Group |
|
FEED Cost
Estimating |
Terra Dynamics |
|
UIC Permitting |
FEED
= front-end engineering design
UIC
= Underground Injection Control |
|
|
18 |
 |
RSI-3353 |
2.5 | Currency,
Abbreviations, and Units of Measures |
Unless otherwise stated, metric units
and the United States dollar (USD) are used in this TR. Abbreviations, units of measure, and minerals referenced herein are defined in
Tables 2-4, 2-5, and 2-6, respectively.
Table 2-4.
Abbreviations and Acronyms
Term |
|
Definition |
|
Term |
|
Definition |
AACE |
|
Association for the Advancement of Cost Engineering |
|
ML |
|
Mother Liquor |
ADEE-AOGC |
|
Arkansas Oil and Gas Commission |
|
MOU |
|
Memorandum of Understanding |
ADEE-DEQ |
|
Arkansas Department of Energy & Environment Division of Environmental Quality |
|
MRMR |
|
Mineral Resource Mineral Reserve |
ADH |
|
Arkansas Department of Health |
|
NAAQS |
|
National Ambient Air Quality Standards |
AHPP |
|
Arkansas Historic Preservation Program |
|
NEPA |
|
National Environmental Policy Act |
AIME |
|
The American Institute of Mining, Metallurgy and Petroleum Engineers |
|
NFPA |
|
National Fire Protection Association |
AIPG |
|
American Institute of Professional Geologists |
|
NI |
|
National Instrument |
API |
|
American Petroleum Institute |
|
NPDES |
|
National Pollutant Discharge Elimination System |
ASL |
|
Above Sea Level |
|
NPV |
|
Net Present Value |
BBLS |
|
Barrels |
|
NYSE |
|
New York Stock Exchange |
BOE |
|
Basis of Estimate |
|
OARO |
|
Osmotically Assisted Reverse Osmosis |
BSW |
|
Brine Supply Well |
|
OAT |
|
One Factor at a Time |
BV |
|
Bed Volumes |
|
OLI |
|
Systems In. Process Software |
BWRO |
|
Brackish Water Reverse Osmosis |
|
OPD |
|
Optimized Process Designs, LLC |
CAA |
|
Clean Air Act |
|
OPEX |
|
Operating Cost |
CAPEX |
|
Capital Cost |
|
ORP |
|
Oxidation-Reduction Potential |
CCR |
|
Central Control Room |
|
PAH |
|
Polycyclic Aromatic Hydrocarbon |
CCTV |
|
Closed Circuit Television |
|
PCS |
|
Process Control System |
CERCLA |
|
Comprehensive Environmental
Response, Compensation, and Liability Act |
|
PDC |
|
Power Distribution Center |
CIM |
|
Canadian Institute of Mining,
Metallurgy and Petroleum |
|
PE |
|
Professional Engineer |
CIP |
|
Clean In-Place |
|
PEA |
|
Preliminary Economic Assessment |
CIT |
|
Corporate Income Tax |
|
PG |
|
Professional Geologist |
CPG |
|
Certified Professional Geologist |
|
PMC |
|
Project Management Consulting |
CWA |
|
Clean Water Act |
|
PSI |
|
Pounds per Square Inch |
DBSP |
|
Design Basis Scoping Paper |
|
PSIG |
|
Pounds per Square Inch Guage |
DCF |
|
Discounted Cashflow |
|
PTZ |
|
Pan-Tilt-Zoom |
DFS |
|
Definitive Feasibility Study |
|
PVC |
|
Polyvinyl Chloride |
DLE |
|
Direct Lithium Extraction |
|
QA/QC |
|
Quality Assurance Quality Control |
DTB |
|
Draft Tube Baffled |
|
QP |
|
Qualified Person |
DXC |
|
Dangxiongcuo |
|
RCRA |
|
The Resource Conservation and Recovery Act |
EA |
|
Environmental Assessment |
|
RESPEC |
|
RESPEC Company, LLC |
19 |
 |
RSI-3353 |
EDC |
|
Dichloroethane |
|
RIO |
|
Remote Input/Output |
EPA |
|
Environmental Protection Agency |
|
RM-SME |
|
Registered Member of the Society of Mining, Metallurgy and Exploration |
EPC |
|
Engineering, Procurement and Construction |
|
RO |
|
Reverse Osmosis |
ESA |
|
Environmental Site Assessment |
|
SARA |
|
Superfund Amendment and Reauthorization Act |
EV |
|
Electric vehicle |
|
SARL |
|
Site Access, License and Reservation Agreement |
FEED |
|
Front End Engineering Design |
|
SBS |
|
Sodium Bisulfite |
FID |
|
Final Investment Decision |
|
SCFM |
|
Standard Cubic Feet per Minute |
GHG |
|
Greenhouse Gas |
|
SDWA |
|
Safe Drinking Water Act |
GLCC |
|
Great Lakes Chemical Corporation |
|
SLL |
|
Standard Lithium Limited |
GLO |
|
General Land Office |
|
SP |
|
Spontaneous Potential |
GPM |
|
Gallons per Minute |
|
SVOC |
|
Semi Volatile Organic compounds |
GR |
|
Gamma Ray |
|
SWPPP |
|
Stormwater Pollution Prevention Plan |
GWH |
|
Gigawatt Hour |
|
SWRO |
|
Sea Water Reverse Osmosis |
HMI |
|
Human Machine Interface |
|
TDS |
|
Total Dissolved Solids |
HWY |
|
Highway |
|
TM |
|
Trademark |
IPaC |
|
Information for Planning and Consulting |
|
TR |
|
Technical Report |
IRR |
|
Internal Rate of Return |
|
TSXV |
|
Toronto Venture Exchange |
ISBL |
|
Inside Battery Limits |
|
UF |
|
Ultrafiltration |
IT |
|
Internet Technology |
|
UIC |
|
Underground Injection Control |
JV |
|
Joint Venture |
|
USACE |
|
U.S. Army Corps of Engineers |
KES |
|
Koch Engineered Systems |
|
USD |
|
United States Dollar |
KTS |
|
Koch Technology Solutions |
|
USFWS |
|
United States Fish and Wildlife Service |
LAS |
|
Log ASCII Standard |
|
USGS |
|
United States Geological Survey |
LCE |
|
Lithium Carbonate Equivalent |
|
UST |
|
Underground Storage Tanks |
LiSTR |
|
Lithium Stirred Tank Reactors |
|
UTM |
|
Universal transverse Mercator |
LLC |
|
Limited Liability Company |
|
UV |
|
Ultraviolet |
LSS |
|
Lithium Selective Sorption |
|
VOC |
|
Volatile Organic Compounds |
MCC |
|
Motor Control Center |
|
WCA |
|
William M. Cobb & Associates |
MIRE |
|
Maiden Inferred Resource Estimate |
|
XRD |
|
X-Ray Diffraction |
20 |
 |
RSI-3353 |
Table 2-5.
Units of Measure
Term |
|
Definition |
°C |
|
degrees Celsius |
g/L |
|
grams per liter |
L |
|
liter |
m |
|
meters |
mg |
|
milligram |
mg/L |
|
milligrams per liter |
mg/L |
|
milligrams per liter |
US BBLS |
|
United States barrels |
US$ |
|
United States dollar |
wt% |
|
percentage by weight |
μm |
|
microns |
Table 2-6.
Minerals
Term |
|
Chemical
Formula |
Boron |
|
B |
Bromine |
|
Br2 |
Calcium |
|
Ca |
Calcium Chloride |
|
CaCl2 |
Chlorine |
|
Cl2 |
Hydrogen Sulfide |
|
H2S |
Lithium |
|
Li |
Lithium Carbonate |
|
Li2CO3 |
Magnesium |
|
Mg |
Potassium |
|
K |
Rubidium |
|
Rb |
Silica |
|
Si |
Sodium |
|
Na |
21 |
 |
RSI-3353 |
3.0 | Reliance
on Other Experts |
The QP has reviewed the mineral tenure
of LANXESS using the publicly available information on Units approved by the AOGC: South Plant Brine Unit, BU 1-1995, March 28,
1995; South Expansion Brine Unit 086-1-2016-11 November 28, 2016; Central Plant Brine Unit BU 2-1995 August 22, 1995; Central
Expansion Brine Unit 095-2022-12 January 5, 2023; West Plant Brine Unit BU 3-1995 November 28, 1995 and the West Expansion
Brine Unit-H 048-2-2015-04 May 14, 2015. The Authors have not independently verified the legal status or ownership of the mineral
title, and underlying property agreements of LANXESS. The QP reviewed the terms of the amended and restated MOU with LANXESS dated February 23,
2022 concerning the rights of Standard Lithium to access the LANXESS brines and the conditions of the access in the Site Access Reservation
and License Agreement dated November 15, 2022. The QP has relied on Standard Lithium for minerals rights definition in section 4.0.
Standard Lithium obtained a third-party
marketing study (The Lithium Market A summary of the market for lithium chemicals with a battery quality carbonate price forecast to
2036, Global Lithium LLC, June 5, 2023) to establish the lithium carbonate price. The Authors have reviewed against publicly available
pricing forecasts and deemed it applicable for reporting purposes and have thus relied on the information contained in the market study
to establish the product pricing for use in the economic analysis (section 22).
22 |
 |
RSI-3353 |
4.0 | Property
Description and Location |
4.1 | Property
Description and Location |
The Property, which includes the LANXESS
South, Central and West Brine Units, is located south of the City of El Dorado in Union County, Arkansas, USA, as presented in Figure
4-1. The southern and western edges of the Property border the state of Louisiana and Columbia County, respectively. The Property
encompasses Townships 16-19 South, and Ranges 14-18, West of the 5th Meridian. The Property center is at UTM 520600 Easting,
3670000 Northing, Zone 15N, North American Datum of 1983.
LANXESS has the rights to extract brine
from the South, Central, and West brine production units through the unitization by the Arkansas Oil and Gas Commission (AOGC). Standard
Lithium’s Memorandum of Understanding in place with LANXESS sets out the process for the establishment of definitive commercial
agreements between the parties, which once in place, will grant Standard Lithium certain rights related to the extraction of lithium.
(See Section 4.4 below).
Figure 4-2 provides an overview of the
Property, including the location of the bromine processing facilities in the South, Central, and West Units. The land package, which
is shown in Figure 4-2, consists of 60,477 hectares (149,442 acres) that cover more than 608 square kilometers (km2). Table
4-1 provides a description of the LANXESS Unitized land holdings.
Each Unit (South, Central, and West)
has its own brine supply wells, pipeline network, and bromine-processing (separation) infrastructure. The facilities and their locations,
which are wholly owned and operated by LANXESS, are as follows:
| / | South
Unit (South Plant): 324 Southfield Cutoff, El Dorado, Arkansas 71730 |
| / | Central
Unit (Central Plant): 2226 Haynesville Highway (HWY 15S), El Dorado, Arkansas 71731 |
| / | West
Unit (West Plant): 5821 Shuler Road, Magnolia, Arkansas 71731 |
Table 4-1.
Description of LANXESS Unitized Land Holdings for Brine Production
Unit | |
AOGC Order Reference | |
Date | | |
Hectares | | |
Acres | |
South Plant Brine Unit | |
BU 1-1995 | |
March 28,
1995 | | |
| 12,495 | | |
| 30,877 | |
South Expansion Brine Unit | |
086-1-2016-11 | |
November 28,
2016 | | |
| 2,963 | | |
| 7,321 | |
Central Brine Unit | |
BU 2-1995 | |
August 22,
1995 | | |
| 17,391 | | |
| 42,974 | |
Central Expansion Brine Unit | |
095-2022-12 | |
January 5,
2023 | | |
| 2,655 | | |
| 6,560 | |
West Brine Unit | |
BU 3-1995 | |
November 28,
1995 | | |
| 24,424 | | |
| 60,354 | |
West Expansion Brine Unit-H | |
048-2-2015-04 | |
May 14,
2015 | | |
| 549 | | |
| 1,356 | |
23 |
 |
RSI-3353 |
Figure 4-1. Overall Property
Location Map
24 |
 |
RSI-3353 |
| 4.2 | Surface
and Mineral Rights |
Per Arkansas Code Title
15, Natural Resources and Economic Development § 15-56-301 minerals “include oil, gas, asphalt, coal, iron, zinc, lead, cinnabar,
bauxite, and salt water whose naturally dissolved components or solutes are used as a source of raw materials for bromine and other products
derived there from in bromine production.” The mineral interest owner has the inherent right to develop the minerals and the right
to lease the minerals to others for development. The development, production and royalties are regulated by the Arkansas Brine Conservation
Act § 15-76-301(Arkansas, 2023).
Payments made to the Lessor
for brine production are governed by statute in Arkansas. For brine used to produce bromine, the statutory rate is currently $66.93 per
net mineral acre per year. For substances extracted from brine other than the bromine, the Arkansas Oil and Gas Commission is responsible
for determining ‘fair and equitable’ compensation. The Arkansas Oil and Gas Commission has not yet determined what constitutes
‘fair and equitable’ compensation for brine used to produce lithium.
In many instances the surface
estate has been severed from the mineral estate. The owner of the mineral estate, as the dominant estate, has the right to make reasonable
use of the surface in order to extract minerals. In most cases brine leases include the right to use the surface to produce brine.
The proposed site (Project
Site) for the Project is located approximately 13 km [8 miles] south of El Dorado, Arkansas in Union County, immediately east of the
existing South Plant bromine extraction facility owned and operated by LANXESS. The location of the proposed Project Site is shown in
Figure 4-2.
25 |
 |
RSI-3353 |
Figure 4-2. Property Location showing
LANXESS Plant Locations within Units
The Project Facility is
proposed to be constructed on leased property which is owned by LANXESS Corporation, immediately to the East of the existing South Plant
bromine extraction facility. The Project Company has entered into commercial agreements with LANXESS which reserves up to 39 hectares
(96 acres) for the development of the Project and future phases of development at the site, which phases are subject to the completion
of future feasibility studies. Refer to Section 4.4 for an overview of the Standard Lithium – LANXESS Agreements including
the Site Access, Reservation and License Agreement.
Certain agreements with
LANXESS contemplate future additional production of lithium chemicals across LANXESS’s facilities; the Project as described herein
does not include any expansions or additional lithium plants.
Figure 4-3 outlines the
land reserved for development by Standard Lithium, a portion of which is proposed to be leased for construction of the Project Facility.
26 |
 |
RSI-3353 |
Figure 4-3. Land
Reserved for Project Facility Construction
Road access to the Project
Facility is contemplated to be via Southfield Cutoff. The nearest major intersection is 1 km southeast of the facility at the junction
of Highway 63 and Southfield Cutoff. Refer to Section 5 for a description of accessibility, climate, local resources, infrastructure,
and physiography.
The AOGC, in accordance
with Arkansas law to avoid waste and maximize recovery of Mineral Resources, establishes drilling units that ensure all mineral owners
potentially impacted by a producing well receive proper payment.
The AOGC must approve the
lease payment rate for any ‘additional substance’ profitably extracted from brine produced by an operator of a brine unit.
The extraction of lithium from Tail Brine produced in South Arkansas is an additional substance triggering the fee analysis. Standard
Lithium and LANXESS have a joint application before the AOGC which sets out a proposed royalty structure (also at times referred to as
‘Lease-fees-in-lieu-of-royalties’) as fair and equitable compensation to mineral owners for the commercial extraction of
lithium from the South Brine Unit.
On October 10, 2018,
the AOGC granted an Order approving the deployment of the Demonstration Plant to test the commercial viability of the extraction of lithium
from brine processed at the South Unit processing plant operated LANXESS and Arkansas Lithium Corporation (a wholly owned subsidiary
of Standard Lithium). The Order took effect November 19, 2018 (AOGC, 2018a). The Demonstration Plant started operation in May of
2020. By Order No. 58-2023-08 the AOGC granted an additional extension to operate the Demonstration Plant through December 5,
2023 and Standard Lithium has an application before the AOGC for a further extension of operations. Standard Lithium asserts the successful
testing and production of lithium products at the Demonstration Plant illustrates, subject to execution of lithium purchase agreement
with a suitable Offtake counterparty, that lithium can be profitably extracted from brine.
27 |
 |
RSI-3353 |
| 4.4 | Overview
of the Standard Lithium – LANXESS Agreements |
| 4.4.1 | Amended
and Restated Memorandum of Understanding |
Standard Lithium entered into an Amended
and Restated Memorandum of Understanding (“MOU”) on February 23, 2022, (Standard, 2022) with LANXESS. The MOU replaces
the LANXESS MOU and LANXESS Joint Venture (JV) Term Sheet, which previously set out the basis on which the parties had agreed to cooperate
in a phased process towards developing commercial opportunities related to the production, marketing, and sale of battery-quality lithium
products.
Specifically, the MOU sets
out the process for the establishment of definitive commercial agreements between the parties, which once in place, will grant Standard
Lithium the rights required for development of the Project and govern the relationship throughout the life of the Project. Under the
MOU, LANXESS is obliged to support development of the Project.
The Project is currently
wholly owned by Standard Lithium’s wholly owned subsidiary project company (“Project Company”). With completion of
this DFS, pursuant to the MOU, LANXESS will be given the option to acquire an equity interest in the Project Company of up to 49% and
not less than 30%, at a price equal to a ratable share of Standard Lithium’s aggregate investment in the Project Company.
If LANXESS acquires an
equity interest in the Project Company, the parties will share the costs of financing construction of the Project, on a ratable basis.
The Project Company is expected to directly acquire the required debt financing for the Project and this process remains independent
of the LANXESS equity election process.
If LANXESS does not acquire
an equity interest in the Project Company, Standard Lithium will continue to own 100% and may elicit bids from other interested parties
to acquire an interest of up to 50% in the Project Company.
Note that Standard Lithium
retains 100% ownership of its South West Arkansas Project, including certain other sites in Arkansas, its Project Sites in East Texas,
and all of the proprietary extraction technologies, relevant intellectual property and know-how owned or licensed by Standard Lithium.
Under the MOU, LANXESS
has the right to acquire some, or all of the lithium carbonate offtake produced at the Project.
The MOU also sets out the
definitive commercial agreements between the parties which are currently contemplated to be completed prior to, or concurrent with, the
Final Investment Decision for the Project, which include:
| / | Brine
Agreement which will set out the terms and conditions for the supply and return of brine
for the Project. |
28 |
 |
RSI-3353 |
| / | Lithium
Purchase (Offtake) Agreement which sets out the terms and conditions for the purchase of
Lithium Carbonate by LANXESS from the Project, if any. |
| / | Ground
Lease Agreement for the lands required to construct the Project adjacent to the South Plant,
including additional right of ways and easements on the broader LANXESS property. |
| / | Site
Services Agreement which sets out the services to be provided by LANXESS to support the Project. |
Select
key terms and conditions required to be included in these definitive commercial agreements are further set out in the MOU and the Site
Access, Reservation and License Agreement as outlined below.
| 4.4.2 | Site
Access, Reservation and License Agreement |
The Site Access, Reservation
and License Agreement (“SARL”), executed in November 2022 between LANXESS, Standard Lithium and the Project Company,
provides for access to the LANXESS properties during the term of the SARL for the purposes of developing the Project, reserves up to
96 acres for the development of the Project and any future phases of development and sets out key terms and conditions to be included
in the definitive commercial agreements between the parties.
A principal purpose of
the SARL is to facilitate access by the Project Company to complete surveying, sampling and other intrusive investigations on the LANXESS
properties to support Project development. The permitted activities include:
| / | ground
surveying and location of existing facilities; |
| / | conducting
geotechnical field investigations, including drilling and test-pitting; |
| / | installation
of groundwater monitoring wells; |
| / | establishing
baseline environmental conditions, including sampling of surface water, soils, vegetation
and ground water; and, |
| / | location
of underground utilities. |
Under the SARL, the Project
Company has the exclusive right to develop the Project on undeveloped land owned by LANXESS that is immediately east of the existing
South Plant bromine extraction facility (refer to Figure 4-3), subject to execution of the definitive Ground Lease Agreement which is
contemplated to become effective upon a successful FID.
The Project Company is
expected to lease approximately 20 hectares (50 acres) of the reserved lands pursuant to the Ground Lease Agreement, leaving the balance
available for future phases of development. The reservation of the real property for future development is anticipated to be addressed
through a separate option agreement, which will supersede the SARL, and a separate future ground lease agreement.
In order to allow the Project
to proceed with confidence, the SARL also establishes key terms to be incorporated into the definitive commercial agreements between
LANXESS and the Project Company, with highlights as summarized below.
29 |
 |
RSI-3353 |
Term
of Agreements
| / | Definitive
commercial agreements, including the Brine Agreement, Ground Lease Agreement and Site Services
Agreement, will each have an initial term of 25 years, which aligns with the Project economic
life. |
| / | The
Project Company will have the right to extend the term of the commercial agreements up to
40 years, with notice, in 5 year increments. |
Brine
Agreement
| / | LANXESS
commits to supply the Project with a guaranteed minimum quantity of brine over the 25 year
operating life of the Project in accordance with the development plan established for the
South Brine Unit. |
| / | Establishment
of the brine supply and discharge infrastructure to be constructed by the Project Company
and that infrastructure to be constructed by LANXESS as currently set out in the SARL, as
well as a commitment to construct such infrastructure by an agreed upon milestone schedule. |
| / | Conditions
for brine supply and disposal including, quality parameters for both Feed Brine and the lithium-depleted
effluent brine as well as minimum and maximum flow conditions and metering requirements.
Metering will be the responsibility of the Project Company. |
| / | Responsibility
of each party to maintain permits necessary to perform their respective obligations under
the brine agreement, including supply and disposal of brine. |
Ground Lease
| / | Right
to lease the real property required for the Project including a right to purchase the leased
real property if LANXESS desires to sell, with the right to lease additional real property
for future development of the Project pursuant to a separate option agreement ; |
| / | Permitted
use of the leased property includes construction and operation of the commercial lithium
extraction plant as well as research and development work; |
| / | Grant
of permanent and temporary access rights, rights-of-way, licenses, easements required for
construction, operation and maintenance of the Project and any future phases of development
including rights required for infrastructure, utilities, site services, laydown, parking,
pipelines and powerlines; |
| / | Decommissioning
obligations by the Project Company; and, |
| / | Responsibility
of each party for any current and future environmental liabilities. |
Site
Services Agreement
| / | Provision
of power and utilities for the Project infrastructure located outside the primary leased
property within the LANXESS facility; and, |
| / | Provision
of chlorinated water for the Project. |
30 |
 |
RSI-3353 |
| 4.5 | Environmental
Liabilities and Permitting |
Potential environmental liabilities associated
with construction of the Project Facility include discovery of improperly abandoned oil/gas wells, permanent closure/abandonment of existing
LANXESS ground water monitoring wells within the construction area, and potential off-site transport of sediments because of improper
or inadequate erosion control measures.
LANXESS is responsible
for environmental liabilities incurred by Standard Lithium arising from pre-existing environmental conditions (to the extent not exacerbated
by Standard Lithium) during the investigative activities covered under the SARL. It is currently contemplated, subject to finalization
of the Ground Lease Agreement, that environmental liabilities which arise from pre-existing environmental conditions (to the extent not
exacerbated by Standard Lithium), will remain the responsibility of LANXESS as lessor.
Based on the permitting
evaluations completed to date, the Project is not subject to review under the National Environmental Policy Act (NEPA). Construction
and operational emissions to air, surface waters, and subsurface waters are regulated by the federal and state agencies to protect the
environment while allowing responsible development of the lithium resources.
Standard Lithium has initiated
early consultation with permitting agencies for the construction and operation of the Project. A Baseline Environmental Site Assessment
has been conducted as well as investigations of jurisdictional waters of the U. S., cultural resource assessment, and wildlife studies
for the Project. New permits expected to be required for the Project are summarized in Table 4-2.
Table
4-2. Expected Permits for the Project
Agency |
|
Permitted
Activity |
ADEE-DEQ |
|
Air Permit for
Commercial Facility |
ADH |
|
Fresh Water Supply
for Potable Water |
ADEE-DEQ |
|
Construction
Storm Water NPDES Permit for Facility Construction Site |
ADEE-DEQ |
|
Surface Discharge
of Non-Brine Process Wastewater, Non-contact Cooling Water, Treated Sanitary Wastewater |
ADEE-DEQ |
|
Construction
of Treatment System Associated with a NPDES Permit |
ADEE-DEQ |
|
Stormwater Discharges
from a Categorical Industry |
ADEE-DEQ |
|
Construct/Operate
Surface Facility for New Class I Nonhazardous Injection Wells |
ADEE-DEQ |
|
Construct/Operate
Class I Nonhazardous Injection Wells |
ADEE-AOGC |
|
Construct Drilling
Pit for Class 1 Nonhazardous Injection Wells |
ADEE-DEQ |
|
Transfer Barren
Brine to LANXESS No-Discharge Permitted Facility |
USACE |
|
Placement of
fill in waters of the U.S. |
31 |
 |
RSI-3353 |
| 4.6 | Significant
Encumbrances or Risks to Perform Work on Property |
As with any development project, there
exists potential risks and uncertainties. There are no known significant encumbrances on the property. Standard Lithium will attempt
to reduce risk/uncertainty through effective project management, utilization of technical experts, community engagement, and development
of contingency plans. These risks to perform work on the property include but are not limited to the following:
| / | Obtaining
all the necessary licenses and permits on acceptable terms, in a timely manner. |
| / | Completing
remaining commercial agreements with LANXESS on acceptable terms, in a timely manner. |
| / | Operational
variances within the LANXESS plant that adversely impact the quality of the Tail Brine beyond
those brine conditions that have already been tested in the Demonstration Plant. |
| / | Changes
in laws and their implementation, impacting activities on the properties. |
| / | Activities
on adjacent properties having an impact on the Project. |
32 |
 |
RSI-3353 |
| 5.0 | Accessibility,
Climate, Local Resources, Infrastructure, and Physiography |
The Property consists of
the LANXESS South, Central and West Units and is situated in Union County in southern Arkansas. Union County is the largest county in
the State of Arkansas (2,730 km2) and borders the State of Louisiana. The LANXESS Central Unit is located directly adjacent
to and southwest of the City of El Dorado, Arkansas, as shown in Figure 5-1. El Dorado is the County Seat of Union County and has
a population of slightly more than 18,000. It is considered the population, cultural, and business center of the regional area. LANXESS’
South and West Units are located approximately 13 km [8 miles] and 35 km [22 miles] south and west of El Dorado, respectively. The LANXESS
Property can be readily accessed via plane, rail, and an extensive road network.
National airports are regionally
located in Little Rock, Arkansas (approximately 2.5 hours north of the Property by car) and Shreveport, Louisiana (1.5 hours southwest
of the Property by car).
Products are shipped to
and from the El Dorado predominantly by truck and rail; rail lines dissect the Central and South Units with direct access to both the
LANXESS South and Central Plants. Railroad companies and rail lines within Union County include Camden & Southern, Union Pacific,
Louisiana & North West, and El Dorado & Wesson railroads/railways.
The following primary U.S.
Highways are in the region:
| / | South
Unit (South Plant): U.S. Highway 7 and Highway 167 |
| / | Central
Unit (Central Plant): U.S. Highway 15, Highway 82, and Highway 335 |
| / | West
Unit (West Plant): U.S. Highway 82, Highway 57, Highway 160, and Highway 172 |
The secondary, major, Township,
and well-pad access roads provide an integrated network that allows year-round access to almost every part of the Property and El Dorado
has an extensive all-season secondary road network (see Figure 5-1).
33 |
 |
RSI-3353 |
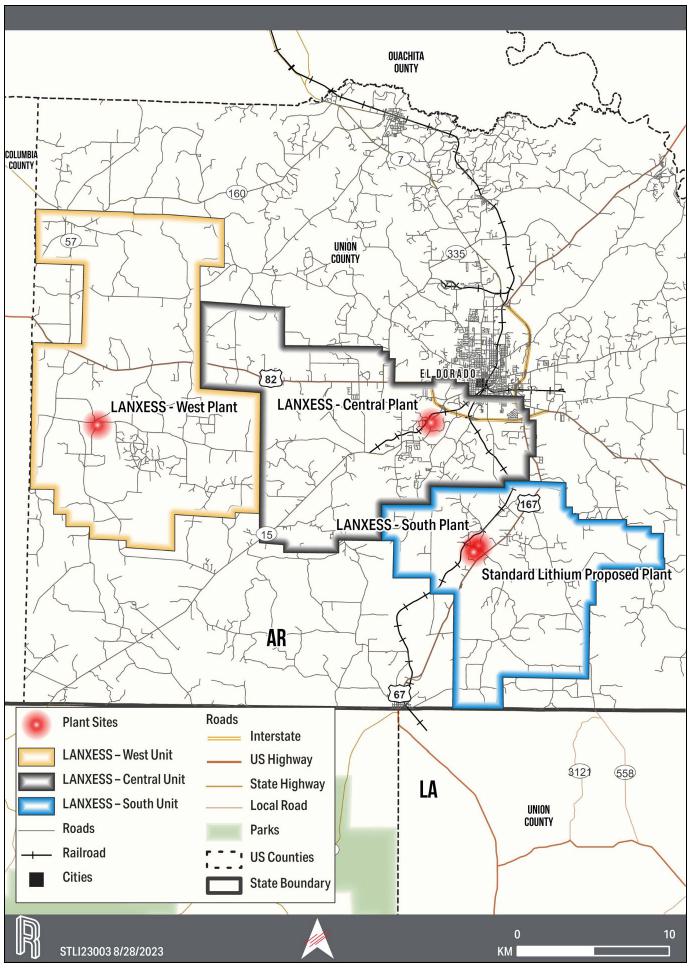
Figure 5-1. LANXESS
Project Access Routes
34 |
 |
RSI-3353 |
The Project area’s climate is generally
humid. The average annual temperature and total precipitation at El Dorado for 2022 (recorded at El Dorado Goodwin Field in Arkansas)
is 17.61°C and 128.0 centimeters, respectively (Figure 5-2). Annual rainfall is evenly distributed throughout the year. The wettest
month of the year is August, with a total rainfall of 19.1 centimeters (Weather.gov, 2023).
The warmest month of the year is July,
with an average maximum temperature of 34.9°C , while the coldest month of the year is January with an average minimum temperature
of -0.4°C.
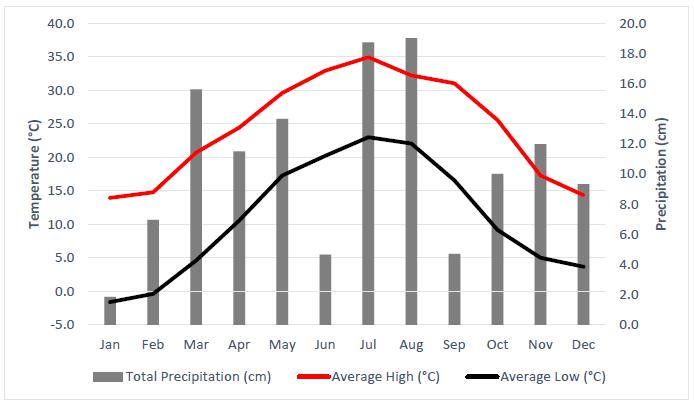
Figure 5-2. Average
Temperature and Total Precipitation at El Dorado, Arkansas, for 2022 (Weather.gov, 2023)
| 5.3 | Local
Resources and Infrastructure |
The greater than 60 years
of brine production in the area has built a robust infrastructure and resource center to support the production from the Property.
In the El Dorado area, the largest manufacturers
include Delek US – El Dorado Refinery, LANXESS, Pro Ampac, LSB Industries, and Milbank Manufacturing Co. Production of elemental
bromine in Arkansas has a long history in the area including LANXESS and Albemarle. The work force supporting these industries has significant
knowledge in brine technology, chemical engineering, and production.
There are multiple trucking
and logistics companies operating in the area.
35 |
 |
RSI-3353 |
The South Plant is fed by wells from the
Sparta Aquifer and the intent of the new Project Facility is to have water supplied from the Sparta Aquifer as well.
The local electric power
is provided by Entergy Arkansas, with its nearest generating facility , a 1,800-megawatt combined cycle gas plant, located approximately
12 km northeast of El Dorado.
Energy Transfer for
the gas transportation services currently supply the South Plant and the intent of the new Project Facility is to have gas tied in to
the same metering station.
The area has a significant
number of businesses that service all aspects of the brine, oil, and gas industries.
Union County covers a total area of 2,730
km2, of which 98.5 percent (2,690 km2) consists of land and 1.5 percent (41 km2) of water. The West
Gulf Coastal Plain covers the southeastern and south-central portions of the state along the border of Louisiana. El Dorado, which lies
within the West Gulf Coastal Plain, has an elevation of 102 meters (m) above sea level (asl).
The area surrounding the
Property is characterized by pine forests and farmlands. The Felsenthal National Wildlife Refuge, the world’s largest green tree
reservoir, is located approximately 45 km east of the City of El Dorado. The Property does not infringe on the Wildlife Refuge.
Southern Arkansas, Union County, the City
of El Dorado, and the Property all have well developed infrastructure and an experienced workforce available for the brine exploration,
production, and processing in the region. The Property can be accessed year-round.
36 |
 |
RSI-3353 |
Despite there having been
many years of bromine production, the exploration and Mineral Resource estimates for lithium have only been occurring since 2018.
| 6.1 | History
of the LANXESS property |
LANXESS Corporation, a
subsidiary of LANXESS AG, a specialty chemical company, has exclusive brine extraction rights over the Property. LANXESS was founded
on September 22, 2004, via the spin-off of the chemicals division and parts of the polymers business from Bayer Aktiengesellschaft,
which was founded in 1863.
The core business of LANXESS
is the manufacturing of chemical intermediates, additives, specialty chemicals, and plastics. LANXESS has a specialty in bromine extraction
from the Smackover Formation where the bromine is either sold as a product or used as a raw material within the other plants.
The following is an abbreviated
history of the Property:
| / | Great
Lakes Chemical Corporation was founded in Michigan in 1936 to extract bromine from underground
saltwater brine deposits. |
| / | Great
Lakes Chemical Corporation was acquired by McClanahan Oil in 1948 and the name changed to
Great Lakes Oil and Chemical Company. |
| / | The
company ended hydrocarbon production in 1957 and focused on the production of bromine-based
chemicals in Arkansas. Around this time, the company assumed its original name of Great Lakes
Chemical Corporation (GLCC). |
| / | The
acquisition of the bromine operations of Northwest Industries operations near El Dorado,
AR is noted as the early stages of the Property bromine assets. |
| / | In
2005, Great Lakes Chemical Corporation merged with Crompton to become Chemtura. Great Lakes
Chemical Corporation remained in existence as a wholly owned subsidiary of Chemtura to own
and operate all the brine production facilities in Union County. |
| / | In
2016, LANXESS acquired Chemtura. |
| / | In
2020, GLCC merged into its corporate parent LANXESS Corporation. As a result of this internal
merger LANXESS is the owner and operator operations of the El Dorado facilities listed above. |
| / | All
infrastructure on the Property is owned by LANXESS. Three bromine plants, West, Central and
South Units, are in operation and produce bromine in the El Dorado region. |
The South Plant was the
first bromine plant and was originally developed by Michigan/Chemical/Murphy Oil in 1957. The West Plant is the smallest of the three
LANXESS El Dorado plants. The Central Plant was expanded in the 1970’s to produce flame retardants and oil field completion fluids.
LANXESS has conducted exploration
on the property as an ongoing part of their operations and production planning. That exploration, while focused on bromine, also included
brine analyses with lithium analytical results. LANXESS has also collected pre- and post-bromine processing brine samples. The historical
brine samples by LANXESS that were analyzed for lithium as presented by Worley (Worley, 2019) are shown in Table 6-1. The average value
of this lithium data is higher than that of the datasets presented by Moldovanyi and Walter (Moldovanyi, 1992) and the USGS National
Produced Waters Geochemical Database (Blondes, 2016) of 141 to 150 mg/L Li.
37 |
 |
RSI-3353 |
Table
6-1. Summary of Historical Brine Analyses (Worley 2019)
Unit | |
Sample
Source Point | |
Number
of Analyses | | |
Minimum
Li (mg/L) | | |
Maximum
Li (mg/L) | | |
Average
Li (mg/L) | |
South | |
All wells | |
| 25 | | |
| 177.0 | | |
| 547.0 | | |
| 349.9 | |
| |
Post-bromine tail | |
| 3 | | |
| 206.0 | | |
| 356.0 | | |
| 274.7 | |
Central | |
All wells | |
| 15 | | |
| 72.0 | | |
| 262.0 | | |
| 157.7 | |
| |
Post-bromine tail | |
| 7 | | |
| 69.8 | | |
| 272.0 | | |
| 119.6 | |
West | |
All wells | |
| 100 | | |
| 32.0 | | |
| 588.0 | | |
| 239.3 | |
| |
Post-bromine feed | |
| 1 | | |
| 80.0 | | |
| 1,800.0 | | |
| 180.0 | |
| |
Post-bromine
tail | |
| 6 | | |
| 79.6 | | |
| 229.0 | | |
| 123.9 | |
| |
All
Analyses | |
| 157 | | |
| 32.0 | | |
| 588.0 | | |
| 239.7 | |
Moldovanyi and Walter conducted
a regional brine chemical study of brine samples from 87 producing wells from Smackover Formation reservoirs in southwest Arkansas, east
Texas, and northern Louisiana. Worley concluded the regional distribution of elevated Smackover Formation Li-brine exhibited the following:
| / | Boron
(B) and alkali metal Li, potassium (K), rubidium (Rb) concentrations in Smackover Formation
waters exhibit coherent geochemical relations across the southwest Arkansas shelf. |
| / | In
general, the concentration of B, Li, K, and Rb is greater and more heterogeneous in hydrogen
sulfide (H2S)-rich brine than in H2S-free brine. |
| / | Regional
concentration gradients in H2S, B, Li, K, and Rb suggest fluids enriched in these
elements may have migrated into the Smackover Formation reservoirs from large-scale circulation
of deep-seated waters along segments of the South Arkansas and Louisiana State Line graben
fault system (Moldovanyi and Walter, 1992). |
Nineteen brine
analyses within the boundaries of the Property are reported in the Moldovanyi and Walter (1992) dataset. Li-brine values reported range
from 47 mg/L Li to 191 mg/L Li, with an average of 144 mg/L Li.
38 |
 |
RSI-3353 |
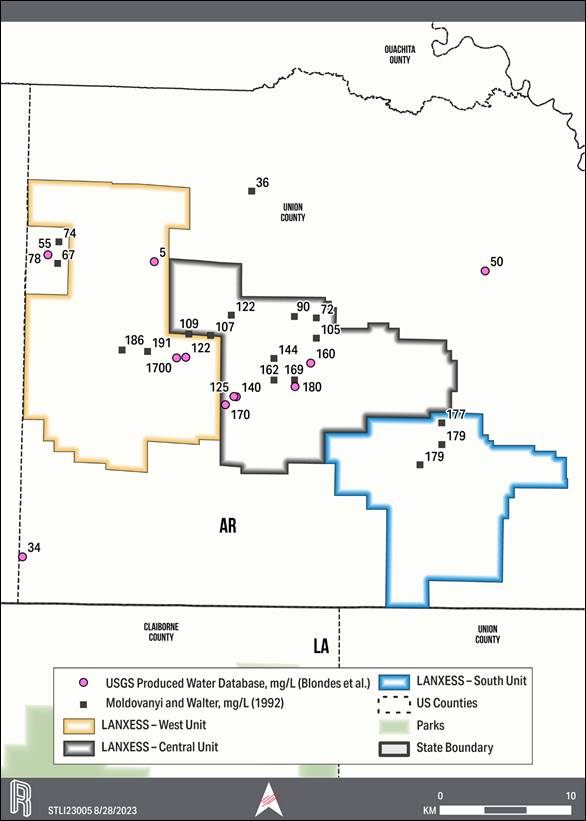
Figure 6-1. Smackover
Formation Lithium Brine Values Derived within, and Adjacent to, the LANXESS Property (Blondes, et al. 2018)
39 |
 |
RSI-3353 |
The USGS National Produced
Waters Geochemical Database contains an additional seven brine analyses not included in the dataset published by Moldovanyi and Walter
(1992). Of the seven analyses, five sample locations report between 122 mg/L and 180 mg/L Li. These data are unreferenced in the USGS
database. Two outlier analytical results yield 5 mg/L and 1,700 mg/L Li, representing the lowest and highest Li-brine values in
the Southern Arkansas historical Li-brine data, respectively. These outlier values are viewed with some skepticism.
Standard Lithium conducted
a sampling program to verify the lithium content of the Smackover Formation brine underlying the Property. Historical datasets show the
Smackover Formation at the Property has average values of 141 to 150 mg/L Li.
| 6.2 | Historical
Mineral resource estimates |
Historical Mineral Resource
estimates have been completed by APEX Geoscience, Ltd. (2018) and Worley (2019). APEX (2018) reported a maiden Inferred resource
of 580,000 tonnes of elemental Li (Table 6-2). The total LCE for the main resource is 3,086,000. Mineral Resources are not Mineral Reserves
and do not have demonstrated economic viability. There is no guarantee that all or any part of the Mineral Resource will be converted
into a Mineral Reserve.
Table
6-2. 2018 Inferred Mineral Resource (Eccles et al. 2018).
Reporting
Parameter | |
South
Unit | | |
Central
Unit | | |
West
Unit | | |
Total
Resource | |
Aquifer
volume (km3) | |
| 5,828 | | |
| 8,289 | | |
| 16,310 | | |
| 30,427 | |
Brine
Volume (km3) | |
| 0.689 | | |
| 0.995 | | |
| 1.835 | | |
| 3.515 | |
Average lithium concentration (mg/L) | |
| 164.9 | | |
| 164.9 | | |
| 164.9 | | |
| 164.9 | |
Average Porosity (%) | |
| 11.8 | | |
| 12.0 | | |
| 11.2 | | |
| 11.6 | |
Total
elemental Li resource (tonnes) | |
| 114,000 | | |
| 164,000 | | |
| 303,000 | | |
| 580,000 | |
Total
LCE (tonnes) | |
| 605,000 | | |
| 873,000 | | |
| 1,610,000 | | |
| 3,086,000 | |
Notes:
[1] Mineral Resources are
not Mineral Reserves and do not have demonstrated economic viability. There is no guarantee that all or any part of the Mineral Resource
will be converted into a Mineral Reserve. The estimate of Mineral Resources may be materially affected by geology, environment, permitting,
legal, title, taxation, socio-political, marketing or other relevant issues.
[2] The weights are reported
in metric tonnes (1,000 kg or 2,204.6 lbs)
[3] Numbers may not add
up due to rounding of the resource values percentages (rounded to the nearest 1,000 unit).
[4] In a ‘confined’
aquifer (as reported herein), porosity is a proxy for specific yield; especially given the number of effective porosity measurements
evaluated in this report and their positive correlation with Log ASCII Standard (LAS) log total porosity.
[5] The ‘Total’
volume and weights are estimated at volume-weighted average porosities of the block-model (i.e. calculated by using the porosity of the
brine units and their respective unit areas). It is assumed that all pore space is occupied by brine.
[6] The LANXESS estimation
was completed and reported using a cutoff of 50 mg/L Li.
[7] In order to describe
the resource in terms of industry standard, a conversion factor of 5.323 is used to convert elemental Li to Li2CO3, or Lithium Carbonate
Equivalent (LCE).
40 |
 |
RSI-3353 |
Worley (2019) reclassified
the inferred Mineral Resource through the demonstration of potential economics in a PEA (Table 6-3) based on additional sampling and
test work by Standard Lithium including:
| / | Smackover
Formation brine sampling program and an assessment of the lithium concentration in the Smackover
Formation brine over time |
| / | Disclosure
of Li extraction technological information based on Standard Lithium’s bench-scale
and mini-pilot-plant laboratory processing test work |
| / | An
update on the Demonstration Plant with some discussion as to the scalability of the technology
toward potential commercial production |
Table
6-3. Indicated Mineral Resource (Dworzanowski et al. 2019).
Reporting
Parameter | |
South
Unit | | |
Central
Unit | | |
West
Unit | | |
Total
Resource | |
Aquifer
volume (km3) | |
| 5,828 | | |
| 8,289 | | |
| 16,310 | | |
| 30,427 | |
Brine
Volume (km3) | |
| 0.689 | | |
| 0.995 | | |
| 1.835 | | |
| 3.515 | |
Average lithium concentration (mg/L) | |
| 168 | | |
| 168 | | |
| 168 | | |
| 168 | |
Average Porosity (%) | |
| 11.8 | | |
| 12.0 | | |
| 11.2 | | |
| 11.6 | |
Total
elemental Li resource (tonnes) | |
| 116,000 | | |
| 167,000 | | |
| 308,000 | | |
| 590,000 | |
Total
LCE (tonnes) | |
| 615,000 | | |
| 889,000 | | |
| 1,639,000 | | |
| 3,140,000 | |
Notes:
[1] Mineral Resources are
not Mineral Reserves and do not have demonstrated economic viability. There is no guarantee that all or any part of the Mineral Resource
will be converted into a Mineral Reserve. The estimate of Mineral Resources may be materially affected by geology, environment, permitting,
legal, title, taxation, socio-political, marketing or other relevant issues.
[2] The weights are reported
in tonnes (1,000 kg).
[3] Numbers may not add
up due to rounding of the resource values percentages (rounded to the nearest 1,000 unit).
[4] In a ‘confined’
aquifer (as reported herein), porosity is a proxy for specific yield; especially given the number of effective porosity measurements
evaluated in this report and their positive correlation with Log ASCII Standard (LAS) log total porosity.
[5] The ‘Total’
volume and weights are estimated at volume-weighted average porosities of the block-model (i.e. calculated by using the porosity of the
brine units and their respective unit areas). It is assumed that all pore space is occupied by brine.
[6] The LANXESS estimation
was completed and reported using a cutoff of 100 mg/L Li.
[7] To describe the resource
in terms of industry standard, a conversion factor of 5.323 is used to convert elemental Li to lithium carbonate, or Lithium Carbonate
Equivalent (LCE).
The resource variation
is attributed to the increase in the average lithium concentration used to calculate the resource estimate from 165 mg/L Li to 168 mg/L
Li. The increase in the average concentration is from the analytical results of 90 brine analyses versus 45 analyses in (Eccles et al,
2018). The doubling of analytical data increased the confidence level of the information used to calculate the Indicated LANXESS Li-Brine
Resource Estimate.
41 |
 |
RSI-3353 |
| 6.3 | Production
from the Property |
No lithium has been commercially
produced from the Property. A small quantity of lithium has been extracted from the LANXESS South Plant Tail Brine in the Demonstration
Plant for testing and development purposes.
42 |
 |
RSI-3353 |
| 7.0 | Geological
Setting and Mineralization |
QP Brush has reviewed in
detail the prior geological setting and mineralization evaluations of the Project, including the “Amended Geological Introduction
and Maiden Inferred Resource Estimate For Standard Lithium’s LANXESS Smackover Lithium-Brine Property In Arkansas, United States”,
effective date 19 November 2018 (MIRE)(Eccles, D.R. et al. 2018), and the “Preliminary Economic Assessment of LANXESS Smackover
Project”, dated 1 August 2019 (PEA) (Dworzanowski, et al. 2019), and will note where their descriptions, of the geological
setting and mineralization are adopted by this report. In particular, the extensive descriptions of the geologic setting and Property
history are accurate and are adopted here without repetition.
The Smackover Formation
is Upper Jurassic in age and was named after the Smackover Field, Union County, Arkansas, which first produced oil in 1922 (Schneider1924).
The Smackover Formation extends from the panhandle of Florida through Alabama, Mississippi, Louisiana, and Arkansas to Texas, Figure
7-1 (Budd et al. 1981). The Smackover Formation’s productive characteristics have been extensively characterized by the drilling
of over 1,000 wells in approximately 600 former and producing oil and gas fields, with approximately 150 of those fields in Arkansas,
Figure 7-2.
Figure 7-1. Facies
Map of the Smackover Formation, Northern Gulf Coast Basin (Budd et al. 1981)
43 |
 |
RSI-3353 |
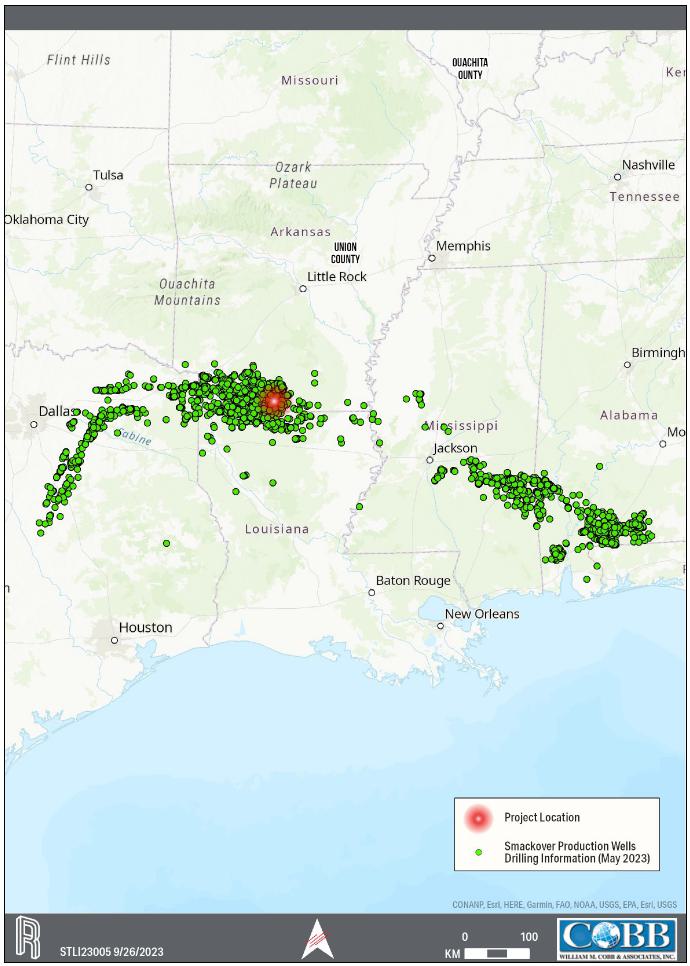
Figure 7-2. Smackover
Production Oil and Gas Wells Drilling Information as of May 2023 (Enverus,2023)
44 |
 |
RSI-3353 |
The portion of the Smackover
generally known to contain significant bromine and lithium is found between the Jurassic Gulf Coast basin-bounding faults to the north-northwest
of the Property and the “State Line” fault system to the south-southeast near the Arkansas-Louisiana border, Figure 7-3 (Budd
et al. 1981). Although some minor faulting within the Property has been inferred in public literature, no faulting effects have been
observed in the subsurface fluid movements associated with the Property operations.
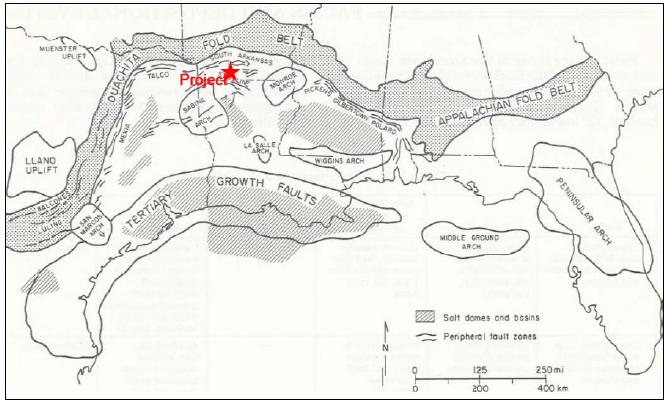
Figure 7-3. Structural
Framework, Northern Gulf Coast (Budd D.A. et al. 1981).
The focus of this resource
and reserves assessment is the LANXESS Project Area’s Smackover Formation in southern Arkansas. The LANXESS Property (Figure 7-4)
is approximately 41 kilometers (km) east to west and 31.4 km north to south. The lithium bearing Smackover reservoir is continuous across
the Property and extends beyond the property discussed in this TR. The lithium concentration within the Smackover Formation brines varies
throughout the Property and generally increases from north-northeast to south-southwest.
The structure of the Smackover
in the Property area generally dips from north-northeast to south-southwest, with a small structural high in southern portions of the
West and Central Units (Figure 7-5) and varies in depth from approximately 1,920 meters subsea to approximately 2,621 meters subsea.
Unlike the production of oil and gas, the reservoir structure is not by itself an important factor in brine production, because the similar
densities of injected and produced brines minimizes the influence of gravity on fluid flow in the reservoir.
45 |
 |
RSI-3353 |
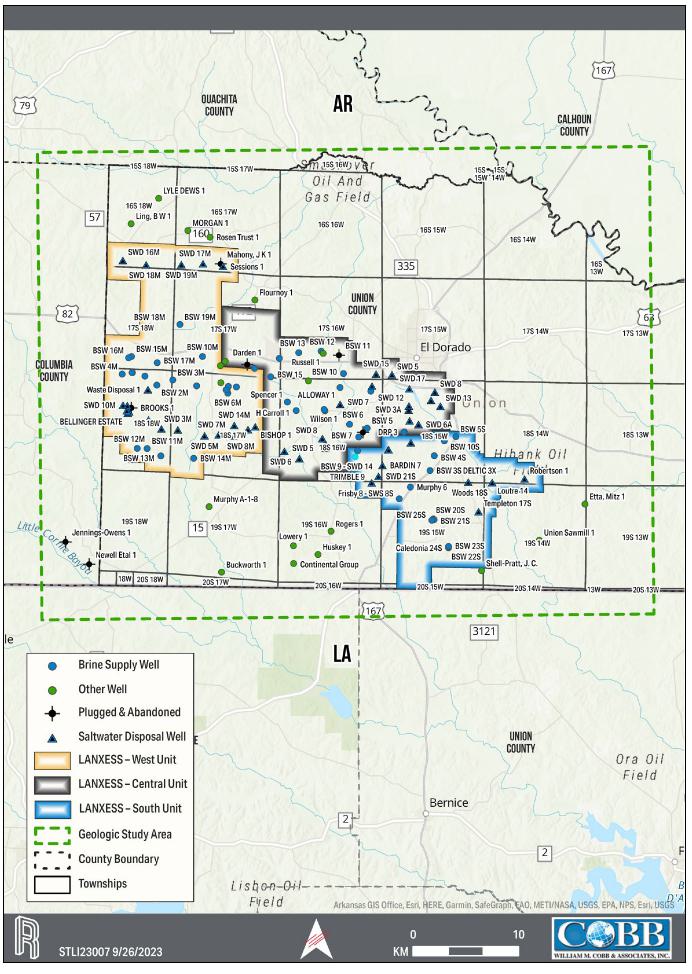
Figure 7-4. LANXESS
Project Area Map
46 |
 |
RSI-3353 |
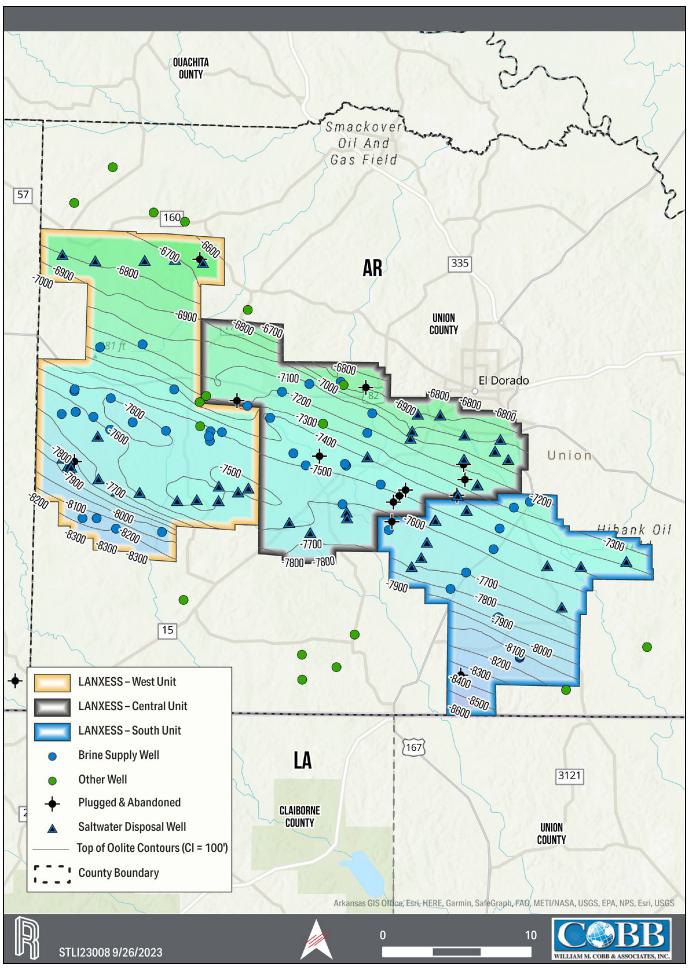
Figure 7-5. Smackover
Structure Map
47 |
 |
RSI-3353 |
As shown in Figure 7-6 of the MIRE (Eccles
et al. 2018), the Smackover Formation in southern Arkansas is commonly subdivided into two intervals, Upper and Lower. The Upper Smackover
Interval, which is the development target for this project, has been subdivided in southern Arkansas into the Reynolds Member Oolite,
a predominantly oolitic limestone, and the Middle Smackover. The Lower Smackover Interval, also known as the Brown Dense, is composed
of dark, dense limestone with argillaceous bands (Imlay 1940). The entire Smackover Formation has been dolomitized to varying degrees.
Figure 7-6. Smackover
Stratigraphic Column (after Eccles et al. 2018)
The lithium brine-bearing
Upper Smackover Interval is overlain by the Buckner Formation, which in Arkansas is dominated by red shale in the upper part and anhydrite
in the lower part above the Smackover carbonates, and, as a result of its low permeability, acts as a geologic seal which traps oil and
gas. The dense, low-permeability carbonate of the Lower Smackover interval is underlain by the clastic section of the Norphlet Formation.
The Norphlet Formation is comprised of red and gray clays with varying amounts of intercalated sands and occasional gravels. The relationship
between the Smackover Formation, the Buckner Formation, and the Norphlet Formation as shown in a north-south cross-section, Figure 7-7.
48 |
 |
RSI-3353 |
Figure 7-7. North-South
Cross Section with Geologic Model Oolite 1-6 Zones
Also shown on Figure 7-7, and as described
in more detail in Section 14, Cobb & Associates has subdivided the Upper Smackover Interval into six zones based on geologic
characteristics and lateral correlations. These six zones are referred to as oolite zones. Zones two and four are low-permeability zones
and were key correlation intervals used to define the six zones. The available well data was evaluated to determine the reservoir’s
structure, porosity, gross zone thickness, net pay thickness (that portion of the gross zone thickness expected to be productive because
it exceeded a minimum porosity value) and net pay thickness to gross zone thickness ratio (equal to the fraction of the oolite zone at
a given location that was estimated to be productive) for each oolite zone at each well location. Some wells did not drill deeply enough
to penetrate all oolite zones, so only penetrated oolite zones with data were used in the mapping effort at those locations.
49 |
 |
RSI-3353 |
The Property
lithium deposit is in the form of a lithium-bearing brine contained within the porosity of the Smackover Formation within the LANXESS
unitized boundaries. The volume of in-place lithium is proportional to the product of the brine-saturated pore volume in the Property
and the lithium concentration, both of which are known with reasonable accuracy, based on extensive drilling, logging, coring, and sampling
data obtained throughout the Property. A refinement of this TR in comparison to the MIRE (Eccles et al. 2018) and PEA (Dworzanowski et
al. 2019) reports is the inclusion of the varying lithium concentration in the Property, which changes both in location and with time.
The balance of information in this section has been brought forward from the previously issued PEA (Dworzanowski
et al. 2019).
Lithium
is a silver-grey alkali metal that commonly occurs with other alkali metals (sodium, potassium, rubidium, cesium). Lithium’s atomic
number is 3 and it has an atomic weight of 6.94, making it the lightest metal and the least dense of all elements that are not gases
at 20°C (the density of lithium in solid form at 20°C is 534 kg/m3). Lithium has excellent electrical conductivity
(i.e. a low electrical resistivity of 9.5 mΩ∙cm), making it an ideal component for battery manufacturing, where lithium ions
move from the negative electrode to the positive electrode during discharge and back when charging. Lithium imparts high mechanical strength
and thermal shock resistance in ceramics and glass.
The
average crustal abundance of lithium is approximate 17-20 parts per million (ppm), with higher abundances in igneous (28-30 ppm) and
sedimentary (53-60 ppm) rocks (Evans 2014; Kunasz 2006). Note: 1 mg/L Li is equivalent to 1 ppm (at a fluid density of 1 g/cm3) and 0.0001%.
Lithium does not occur in elemental form in nature because of its reactivity. There are over 100 minerals that contain lithium, but only
a few of these are currently economic to extract.
Lithium
can be described, priced and quoted as lithium content (Li), lithium oxide (Li2O; 0.464 Li content; conversion is Li x 2.153),
lithium carbonate (Li2CO3; 0.188 Li content) and lithium carbonate equivalent (LCE; conversion is Li x 5.323).
Resource estimates and production quantities of lithium are most commonly expressed as LCE.
Lithium
is extracted from two main categories of deposits: mineral and brine. With respect to mineral deposits, lithium is currently only extracted
commercially from pegmatite deposits. Pegmatite lithium deposits are found globally and account for half of the lithium produced today
(Benson et al. 2017). Spodumene is the most abundant Li-bearing mineral found in economic deposits.
Brine
deposits include unconfined (i.e. continental) and confined (i.e. geothermal and subsurface aquifer) brine deposits. Continental brine
occurs in endorheic basins, where inflowing surface and groundwater is moderately enriched in lithium. All producing lithium brine operations
are unconfined, or partially confined, continental deposits. Several first-order characteristics of this type of brine deposit are: (1) arid
climate; (2) closed basin containing a playa or salar; (3) tectonically driven subsidence; (4) associated igneous or geothermal
activity; (5) suitable lithium source-rocks; (6) one or more adequate aquifers; and (7) sufficient time to concentrate
a brine (Bradley et al. 2006).
50 |
 |
RSI-3353 |
Economic
continental brine deposits typically occur in areas where high solar evaporation results in beneficiating the Li-brine to higher levels
of lithium. Geothermal and/or volcanic associations are the favoured mechanisms for introducing lithium into continental basins, because
lithium-rich brines often exist in areas of volcanic activity (e.g. Imperial Valley, California; Reykjanes Field, Iceland; Taupo
Volcanic Zone, New Zealand). Typical grades are 0.04-0.15 mg/L Li.
Selected
continental brine deposit examples include: Salar de Uyuni in Bolivia (Bradley et al. 2017); Salar de Atacama in Chile (Garrett 2004);
Salar de Hombre Muerto in Argentina (Tahil 2007); Salar del Rincon and the Salar del Olaroz in Argentina (Pavlovic and Fowler 2004; Houston
and Gunn 2011); and the Zhabuye Salt Lake in the Tibetan Plateau, the DXC Salt Lake and the Qaidam Basin in China (Shengsong 1986; Zheng
et al. 2007). The only active lithium mine in North America is in Silver Peak, Nevada, where lithium brine extraction started in 1966.
The lithium occurs in an infilled playa sequence that covers an area of 72 km2 within a closed drainage basin of 1,342 km2 (Munk et al.
2011). Average lithium content at the initiation of production was 360 ppm in 1966, declining to 230 ppm in 2008 (Garrett 2004). The
mine currently produces 3,500 tonnes of LCE per year, with the capability to produce 6,000 tonnes of LCE per year.
Deep
aquifer Li-brine is frequently pumped as a waste product of hydrocarbon production from confined aquifers at depths of up to 4,000 m.
Lithium enrichment of deep saline brine is known to occur worldwide in sedimentary basins of various age, including: the Cambrian Siberian
Platform, Russia (Shouakar-Stash et al. 2007); Devonian Michigan Basin (Wilson and Long 1993); Mississippian–Pennsylvanian reservoirs
of the Illinois Basin (Stueber et al. 1993); Pennsylvanian Paradox Basin, Utah (Garrett 2004); Triassic strata of the Paris Basin, France
(Fontes and Matray 1993); and Jurassic Smackover strata from the Gulf Coast, Arkansas and Texas (Moldovanyi and Walter 1992).
If
the aquifer contains elevated concentrations of lithium, deep, confined aquifers associated with mature (or dwindling or dormant) oil
and gas fields can be converted to brine producing aquifers. A perfect example of this is bromine production from the Smackover Formation
in southern Arkansas. At the LANXESS Property, LANXESS’s predecessors ceased hydrocarbon production in favour of bromine production
in 1957 and this production has continued for over 50-years. Accordingly, these deep-seated aquifer brine deposits present enormous opportunity.
51 |
 |
RSI-3353 |
The
source of lithium in hypersaline brine aquifers, including the Smackover Formation, remains subject to debate. Theories relevant to the
Smackover Formation include, but are not limited to, the following:
| / | Smackover
Li-brine could be a result of the continental drainage of lithium-enriched solutions into
the sea, where the lithium stems from Triassic age volcanic rocks in the Gulf coast (Collins
1976). Continental water from springs or other hydrothermal fluids along fault systems could
have leached lithium from Triassic aged volcanic rocks. These lithium-enriched fluids then
drained into the Smackover Sea and the water was then concentrated by evaporation. |
| / | In
the Smackover brine, radiogenic Strontium -87/Strontium -86 are significantly higher than
Late Jurassic seawater, suggesting significant strontium contribution from detrital sources,
such as the Bossier Formation, which overlies and/or interfingers with the upper Smackover
Formation, or suggesting they were acquired during brine migration (Stueber et al. 1984). |
| / | Lithium
was mobilized from the Alleghenian-sourced volcaniclastics (including plutonic rocks) and
then concentrated in the underlying Norphlet Formation. These fluids could have originated
in the Louann Salt and migrated upward through faults or from shallower circulation through
the alluvial and wadi facies of the Norphlet (from Chuchla, unpublished, via Daitch 2018). |
| / | The
association between B, Li, K, and Rb, coupled with a general lack of clastic sediments in
the upper Smackover Formation in southwest Arkansas, suggest that the Smackover Formation
brines are mixing with deeper-seated waters that may have been geochemically modified by
siliciclastic diagenesis at higher temperature (Walter et al. 1990) |
| / | Regional
trends between H2S) and B, Li, K and Rb support the association of a higher temperature,
deeper-seated fluid end member; these fluids may have migrated into upper Smackover reservoirs
via major fault systems, the South Arkansas fault system and the Louisiana State Line graben,
and their associated fractures (Moldovanyi and Walter 1992). |
With
respect to resource modelling of confined aquifer Li-brine deposits, important criteria include defining the boundaries of the subsurface
aquifer; brine chemistry; and understanding of the hydrology of the brine. The reader is referred to the CIM Best Practice Guidelines
for Resource and Reserve Estimation for Lithium Brine (2012). While the guidelines define issues specific to unconfined continental brine
deposits (i.e. salars), they do provide general direction for reporting on confined deep aquifer deposits.
52 |
 |
RSI-3353 |
The exploration program to quantify the
Property brine lithium accumulation has focused on quantifying two key parameters: the distribution of porosity in the Smackover Formation
(which determines the volume of brine) and the initial distribution of lithium concentration within the Smackover Formation. The initial
total quantity of lithium in the Property is fully described by the combination of the formation’s structure and pore volume, as
estimated through the geologic characterization of the porosity and thickness of the Smackover Formation, as described in Section 14,
with the mapped lithium concentration for the Smackover Formation, as estimated from the results of the Standard Lithium sampling program
described here.
| 9.1 | Geologic
Data Sampling Methods, Quality, and Extent |
The Smackover Formation
geologic data used in this analysis was obtained by LANXESS and its predecessors as they developed the Property for bromine recovery.
Three categories of geologic data were obtained for the Property: well logs that provided structural data, well logs that provided porosity
data, and cores that provided porosity and permeability data. Figure 9-1 identifies the locations where these data were collected. The
structural data was obtained from 89 wells with log data in the Smackover Formation, while the porosity data originated in two forms:
the porosity logs (density porosity, sonic porosity, and neutron porosity logs) obtained from 68 wells, and the core samples obtained
from 27 wells. The logs and cores were gathered using industry-standard procedures by contractors experienced in their respective specialties.
All available wireline
well log data from the 89 wells was used to establish correlations for structural control and to define gross interval thickness for
each Smackover zone. Available well log data included spontaneous potential (SP), gamma ray (GR), resistivity (EL, ISFL, DIL, etc.),
MicroLog, and various porosity curves when available (acoustic, neutron, and density). The number of wells with wireline log data available
for structural and thickness determination exceeded the number of wells with porosity data from cores and porosity logs and was used
to constrain net reservoir thickness and to relate porosity to the established zone correlations. The primary source of porosity data,
the density porosity logs, were calibrated using the core porosity values, supplemented with the sonic porosity and neutron porosity
well logs, eliminating any significant systematic error or bias in the resulting porosity value estimates. The resulting geologic model
formed the basis for the geologic description of the brine-containing reservoir and the reservoir simulation model.
| 9.2 | Lithium
Concentration Data Sampling Methods, Quality, and Extent |
The lithium concentration
data used in this TR resulted from brine samples collected by Standard Lithium from 2017 through May 2022 and analyzed by Western
Environmental Testing Laboratory (WetLab), 1084 Lamoille Highway, Elko, Nevada 89801. The well concentration data were used to develop
a map of the initial distribution of lithium throughout the Property area which formed the basis for the computer simulation model-based
estimates for Project lithium production. In addition, the brine samples collected at the inlet of each of the processing facilities
were used to quantify the inlet lithium concentrations at the three bromine processing facilities for comparison to the simulation model’s
initial predicted values.
53 |
 |
RSI-3353 |
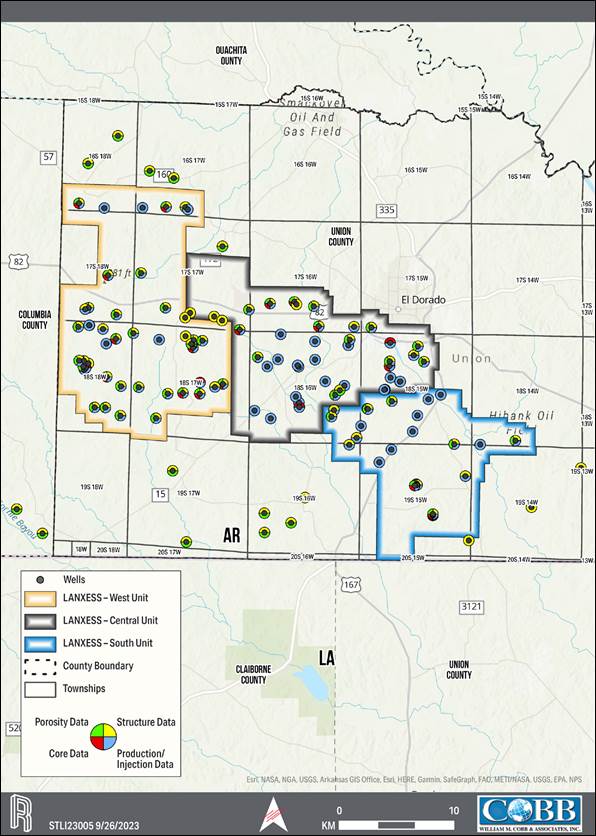
Figure 9-1. Well
Data Source
54 |
 |
RSI-3353 |
Standard Lithium’s
2017 (inlet brine samples only), 2018, and 2019 sampling programs on the Property and the resulting lithium concentration data are described
in detail in sections 9.1 and 9.3 of the MIRE (Eccles, et al. 2018), and in section 9 of the PEA (Dworzanowski
et al. 2019). The author has reviewed those reports and agrees that the sampling programs were appropriate, appear to have been executed
correctly, and have provided reasonable estimates of the brine sample lithium compositions. The WCA QPs Brush and Williams participated
in Standard Lithium’s May 2022 brine sampling program using the sampling procedures described in Section 11. These results
are incorporated with the 2017-2019 sampling data.
In total, there were six
well sampling events from June 2018 to May 2022, where 22 to 37 samples were collected in each event, with a total of 162 samples
analyzed. Table 9-1 lists the sample assay values averaged by well and Figure 9-2 is a map showing the locations of the sampled wells.
The three right-hand columns on Table 9-1 relate to removing the impact of injected brine on measured lithium concentration.
| 9.3 | Exploration
Results and Interpretation |
The extensive data collection
programs for both porosity (Figure 9-1) and lithium concentration (Table 9-1) address the two key factors determining the volume and
quality of the lithium resource for the Property, and the amount of lithium available for recovery in the South Unit by the Project.
In the QP’s Brush and Williams’ opinion the Property has an exceptional quantity, quality, and coverage of the key data,
thanks to the decades of data gathering associated with its development as a bromine recovery project and an extensive lithium sampling
program.
Correctable bias exists
in these recently measured lithium concentration values with respect to the initial (pre-bromine-development) concentration values because
the recent values are affected to varying degrees by the presence of re-injected brine that has a lithium concentration different from
the original lithium concentration at a specific well’s location. This effect was removed by accounting for the fraction of injected
brine present in the samples, thereby providing the data needed to initialize the simulation model with the initial, pre-development
lithium concentrations. This permitted the model to correctly evaluate the movement of lithium throughout the Property history.
The estimated original
lithium concentrations are presented in the right-hand column of Table 9-1. These estimated values were used to create a map of estimated
initial lithium concentrations throughout the Property, Figure 9-3. That map was then used as the initial lithium concentration data
for the computer simulation of the Property from the date of first production and injection of brine. As demonstrated by Table 9-1, the
large number of samples gathered over a broad area of the Property results in a high-quality data set suitable for estimating the initial
distribution of lithium concentration throughout the Property.
55 |
 |
RSI-3353 |
Table
9-1. Average of Supply Well Lithium Concentration Data
| |
| | |
Brine
Sampling | | |
Estimated
Initial Deposit | |
Well | |
Unit | | |
Number
of Samples | | |
Average Lithium Concentration (mg/L) | | |
Percent Standard Deviation
in Samples | | |
Estimated Fraction
of Injected
Brine in
Samples | | |
Estimated Average
Injected Brine
Lithium Concentration (mg/L) | | |
Estimated Original
Lithium Concentration (mg/L) | |
BSW 13 | |
| Central | | |
| 7 | | |
| 114 | | |
| 8.2 | % | |
| 0.27 | | |
| 135 | | |
| 106 | |
BSW 14 | |
| Central | | |
| 9 | | |
| 97 | | |
| 9.1 | % | |
| 0.09 | | |
| 135 | | |
| 93 | |
BSW 15 | |
| Central | | |
| 7 | | |
| 158 | | |
| 21.2 | % | |
| 0.24 | | |
| 135 | | |
| 165 | |
BSW Car1N | |
| Central | | |
| 7 | | |
| 195 | | |
| 10.2 | % | |
| 0.18 | | |
| 135 | | |
| 208 | |
BSW Spen N | |
| Central | | |
| 7 | | |
| 187 | | |
| 10.1 | % | |
| 0.38 | | |
| 135 | | |
| 219 | |
BSW
10S1 | |
| South | | |
| 3 | | |
| 192 | | |
| 0.6 | % | |
| 0.77 | | |
| 200 | | |
| 164 | |
BSW 20S | |
| South | | |
| 7 | | |
| 213 | | |
| 7.1 | % | |
| 0.55 | | |
| 200 | | |
| 230 | |
BSW 21S | |
| South | | |
| 6 | | |
| 238 | | |
| 6.9 | % | |
| 0.14 | | |
| 200 | | |
| 244 | |
BSW 22S | |
| South | | |
| 3 | | |
| 279 | | |
| 14.6 | % | |
| 0.05 | | |
| 200 | | |
| 283 | |
BSW 23S | |
| South | | |
| 4 | | |
| 256 | | |
| 9.4 | % | |
| 0.03 | | |
| 200 | | |
| 258 | |
BSW 24S | |
| South | | |
| 2 | | |
| 233 | | |
| 20.6 | % | |
| 0.46 | | |
| 200 | | |
| 261 | |
BSW 25S | |
| South | | |
| 2 | | |
| 250 | | |
| 2.0 | % | |
| 0.05 | | |
| 200 | | |
| 252 | |
BSW
4S1 | |
| South | | |
| 4 | | |
| 200 | | |
| 8.3 | % | |
| 0.46 | | |
| 200 | | |
| 200 | |
BSW
5S1 | |
| South | | |
| 3 | | |
| 176 | | |
| 3.5 | % | |
| 0.48 | | |
| 200 | | |
| 154 | |
BSW 10M | |
| West | | |
| 9 | | |
| 114 | | |
| 9.2 | % | |
| 0.18 | | |
| 165 | | |
| 102 | |
BSW 12M | |
| West | | |
| 7 | | |
| 256 | | |
| 6.7 | % | |
| 0.15 | | |
| 165 | | |
| 272 | |
BSW 13M | |
| West | | |
| 8 | | |
| 304 | | |
| 9.3 | % | |
| 0.16 | | |
| 165 | | |
| 331 | |
BSW 14M | |
| West | | |
| 7 | | |
| 255 | | |
| 11.4 | % | |
| 0.25 | | |
| 165 | | |
| 285 | |
BSW 15M | |
| West | | |
| 5 | | |
| 147 | | |
| 22.2 | % | |
| 0.10 | | |
| 165 | | |
| 145 | |
BSW 16M | |
| West | | |
| 5 | | |
| 171 | | |
| 9.7 | % | |
| 0.14 | | |
| 165 | | |
| 172 | |
BSW 17M | |
| West | | |
| 6 | | |
| 159 | | |
| 14.6 | % | |
| 0.14 | | |
| 165 | | |
| 158 | |
BSW 18M | |
| West | | |
| 6 | | |
| 82 | | |
| 5.2 | % | |
| 0.13 | | |
| 165 | | |
| 70 | |
BSW 19M | |
| West | | |
| 6 | | |
| 58 | | |
| 10.8 | % | |
| 0.15 | | |
| 165 | | |
| 38 | |
BSW 1M | |
| West | | |
| 8 | | |
| 183 | | |
| 7.2 | % | |
| 0.44 | | |
| 165 | | |
| 196 | |
BSW 5M | |
| West | | |
| 5 | | |
| 183 | | |
| 7.3 | % | |
| 0.37 | | |
| 165 | | |
| 194 | |
BSW 6M | |
| West | | |
| 3 | | |
| 194 | | |
| 3.0 | % | |
| 0.30 | | |
| 165 | | |
| 207 | |
BSW 7M | |
| West | | |
| 6 | | |
| 184 | | |
| 4.1 | % | |
| 0.54 | | |
| 165 | | |
| 206 | |
BSW A8M | |
| West | | |
| 5 | | |
| 205 | | |
| 11.2 | % | |
| 0.14 | | |
| 165 | | |
| 211 | |
BSW JK2 | |
| West | | |
| 5 | | |
| 185 | | |
| 4.5 | % | |
| 0.59 | | |
| 165 | | |
| 215 | |
Average | |
| | | |
| 5.6 | | |
| | | |
| 9.2 | % | |
| | | |
| | | |
| | |
Notes:
[1] Well no longer in service.
56 |
 |
RSI-3353 |
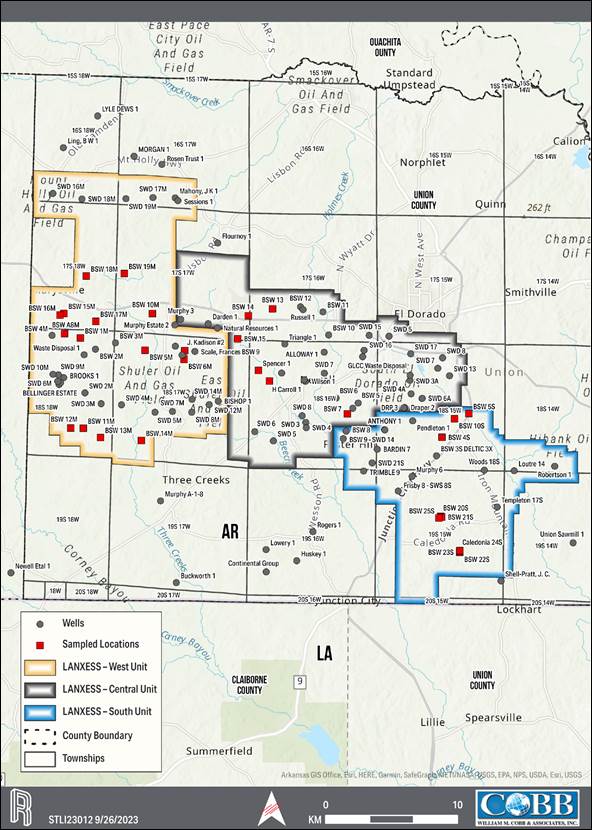
Figure 9-2. Standard
Lithium Sample Locations
57 |
 |
RSI-3353 |
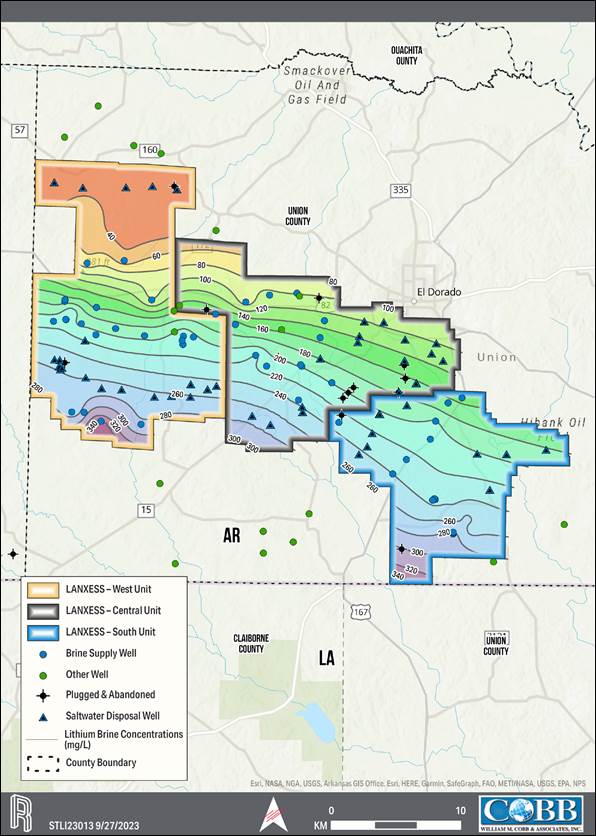
Figure 9-3. Estimated
Initial Lithium Concentration
58 |
 |
RSI-3353 |
The geologic model as described
in Section 14 is based on the well logs and core data obtained from 85 wells drilled in the Geologic Study Area (Figure 7-1) that
penetrated at least the top of the Smackover Formation. No new exploration wells were drilled as part of this estimate. These wells were
drilled either by LANXESS and its predecessor companies to assess and access the bromine-bearing brine, or by other operators exploring
the area for hydrocarbons. There are 89 wells with logs of various types providing structural control, with 68 wells providing log porosity
data and 27 wells providing core porosity data. The majority of the wells have associated injection and withdrawal data. Table 10-1 summarizes
the locations and data provided by all wells in the geologic study area.
Table
10-1. Well Data
API Number | |
Well
Name | |
Year
Drilled | |
Latitude | | |
Longitude | | |
Structure Data | |
Porosity Data | |
Core Data | |
Production
or Injection
Data |
0313904787 | |
Alloway 1 | |
1966 | |
| 33.1864500 | | |
| -92.7435200 | | |
| |
| |
| |
YES |
0313910088 | |
Anthony 1 | |
1947 | |
| 33.1333295 | | |
| -92.6945771 | | |
| |
| |
| |
YES |
0313983123 | |
Arkansas Chemicals 6 | |
1968 | |
| 33.1723900 | | |
| -92.7782200 | | |
| |
| |
| |
YES |
0313910415 | |
Bardin 7 | |
1972 | |
| 33.1198800 | | |
| -92.7005500 | | |
| |
| |
| |
YES |
0313911278 | |
Bellinger Estate | |
1980 | |
| 33.1647342 | | |
| -92.9595850 | | |
| |
| |
| |
YES |
0313912191 | |
Bishop 1 | |
1961 | |
| 33.1531830 | | |
| -92.8298900 | | |
YES | |
YES | |
YES | |
YES |
0313911279 | |
Brooks 1 | |
1980 | |
| 33.1693362 | | |
| -92.9558853 | | |
YES | |
| |
| |
|
0313910820 | |
BSW 10 | |
1977 | |
| 33.1983093 | | |
| -92.7399135 | | |
YES | |
YES | |
YES | |
YES |
0313912920 | |
BSW 10M | |
1993 | |
| 33.2131270 | | |
| -92.8835200 | | |
YES | |
YES | |
| |
YES |
0313910475 | |
BSW 10S | |
1973 | |
| 33.1406949 | | |
| -92.6374519 | | |
| |
| |
| |
YES |
0313911063 | |
BSW 11 | |
1978 | |
| 33.2141222 | | |
| -92.7444945 | | |
YES | |
YES | |
| |
YES |
0313911522 | |
BSW 11M | |
1994 | |
| 33.1346777 | | |
| -92.9398784 | | |
YES | |
YES | |
| |
YES |
0313912745 | |
BSW 12 | |
1987 | |
| 33.2176181 | | |
| -92.7627527 | | |
YES | |
YES | |
YES | |
YES |
0313912946 | |
BSW 12M | |
1995 | |
| 33.1348063 | | |
| -92.9500576 | | |
YES | |
YES | |
| |
YES |
0313912779 | |
BSW 13 | |
1988 | |
| 33.2163149 | | |
| -92.7854856 | | |
YES | |
YES | |
YES | |
YES |
0313912948 | |
BSW 13M | |
1995 | |
| 33.1283211 | | |
| -92.9258458 | | |
YES | |
YES | |
| |
YES |
0313912924 | |
BSW 14 | |
1994 | |
| 33.2115435 | | |
| -92.8053158 | | |
YES | |
YES | |
| |
YES |
0313912949 | |
BSW 14M | |
1995 | |
| 33.1262500 | | |
| -92.8925400 | | |
YES | |
YES | |
| |
YES |
0313912985 | |
BSW 15 | |
1998 | |
| 33.1957500 | | |
| -92.8139800 | | |
YES | |
YES | |
YES | |
YES |
0313912970 | |
BSW 15M | |
1996 | |
| 33.2132500 | | |
| -92.9556600 | | |
YES | |
YES | |
YES | |
YES |
0313912971 | |
BSW 16M | |
1996 | |
| 33.2121000 | | |
| -92.9558800 | | |
YES | |
| |
| |
YES |
0313912965 | |
BSW 17M | |
1996 | |
| 33.2078053 | | |
| -92.9295332 | | |
YES | |
YES | |
| |
YES |
0313912983 | |
BSW 18M | |
1998 | |
| 33.2388500 | | |
| -92.9373000 | | |
YES | |
YES | |
YES | |
YES |
0313913041 | |
BSW 19M | |
2005 | |
| 33.2405837 | | |
| -92.9064449 | | |
YES | |
YES | |
| |
YES |
0313910558 | |
BSW 1M | |
1975 | |
| 33.1964325 | | |
| -92.9421636 | | |
YES | |
| |
| |
YES |
0313910552 | |
BSW 20S | |
1974 | |
| 33.0738200 | | |
| -92.6490700 | | |
YES | |
| |
| |
YES |
0313912968 | |
BSW 21S | |
1996 | |
| 33.0732500 | | |
| -92.6482900 | | |
YES | |
| |
| |
YES |
0313913549 | |
BSW 22S | |
1996 | |
| 33.0491314 | | |
| -92.6336003 | | |
YES | |
YES | |
YES | |
YES |
0313913558 | |
BSW 23S | |
2018 | |
| 33.0498160 | | |
| -92.6335556 | | |
YES | |
YES | |
YES | |
YES |
0313913560 | |
BSW 25S | |
2018 | |
| 33.0727400 | | |
| -92.6505300 | | |
YES | |
YES | |
YES | |
YES |
59 |
 |
RSI-3353 |
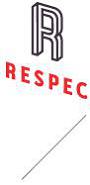
API
Number | |
Well
Name | |
Year
Drilled | |
| Latitude | | |
| Longitude | | |
Structure Data | |
Porosity Data | |
Core Data | |
Production
or Injection
Data |
0313910577 | |
BSW 2M | |
1974 | |
| 33.1887170 | | |
| -92.9300000 | | |
YES | |
YES | |
YES | |
YES |
0313910616 | |
BSW 3M | |
1975 | |
| 33.1931071 | | |
| -92.9136646 | | |
YES | |
YES | |
| |
YES |
0313910117 | |
BSW 3S DELTIC 3X | |
1969 | |
| 33.1153266 | | |
| -92.6522708 | | |
| |
| |
| |
YES |
0313910714 | |
BSW 4M | |
1976 | |
| 33.1981672 | | |
| -92.9652242 | | |
YES | |
YES | |
| |
YES |
0313910248 | |
BSW 4S | |
1970 | |
| 33.1279821 | | |
| -92.6477757 | | |
| |
| |
| |
YES |
0313910099 | |
BSW 5 | |
1969 | |
| 33.1516340 | | |
| -92.7159650 | | |
| |
| |
| |
YES |
0313971205 | |
BSW 5M | |
1977 | |
| 33.1880308 | | |
| -92.8895329 | | |
| |
| |
| |
YES |
0313910411 | |
BSW 5S | |
1972 | |
| 33.1441965 | | |
| -92.6258082 | | |
| |
| |
| |
YES |
0313970114 | |
BSW 6 | |
1970 | |
| 33.1550500 | | |
| -92.7339700 | | |
| |
| |
| |
YES |
0313911211 | |
BSW 6M | |
1979 | |
| 33.1818300 | | |
| -92.8577400 | | |
YES | |
YES | |
YES | |
YES |
0313910177 | |
BSW 7 | |
1970 | |
| 33.1442544 | | |
| -92.7247228 | | |
YES | |
YES | |
| |
YES |
0313972061 | |
BSW 7M | |
1977 | |
| 33.1846430 | | |
| -92.8583700 | | |
| |
| |
| |
YES |
0313910184 | |
BSW 8 | |
1970 | |
| 33.1323599 | | |
| -92.7258727 | | |
YES | |
| |
| |
YES |
0313911179 | |
BSW 8M | |
1979 | |
| 33.1993803 | | |
| -92.9548591 | | |
| |
| |
| |
YES |
0313910498 | |
BSW 9 – SWD 14 | |
1979 | |
| 33.1272655 | | |
| -92.7281765 | | |
YES | |
YES | |
| |
YES |
0313913034 | |
BSW A8M | |
2004 | |
| 33.1994360 | | |
| -92.9551300 | | |
| |
| |
| |
YES |
0313903426 | |
BSW_WIL2N | |
1963 | |
| 33.1676505 | | |
| -92.7598252 | | |
| |
| |
| |
YES |
0313912880 | |
Buckworth 1 | |
1991 | |
| 33.0287550 | | |
| -92.8643200 | | |
YES | |
YES | |
| |
|
0313913562 | |
Caledonia 24S | |
2018 | |
| 33.0502432 | | |
| -92.6335473 | | |
YES | |
YES | |
YES | |
YES |
0313911374 | |
Continental Group | |
1981 | |
| 33.0361020 | | |
| -92.7911300 | | |
YES | |
YES | |
| |
|
0313912660 | |
Darden 1 | |
2004 | |
| 33.2062028 | | |
| -92.8380019 | | |
YES | |
| |
| |
|
0313910089 | |
Draper 2 | |
1969 | |
| 33.1484896 | | |
| -92.6781299 | | |
| |
| |
| |
YES |
0313913539 | |
DRP 3 | |
2017 | |
| 33.1483300 | | |
| -92.6786250 | | |
| |
| |
| |
YES |
0313911523 | |
Etta, Mitz 1 | |
1981 | |
| 33.0860520 | | |
| -92.4948500 | | |
YES | |
YES | |
| |
|
0313911269 | |
Flournoy 1 | |
1980 | |
| 33.2615000 | | |
| -92.8300600 | | |
YES | |
YES | |
| |
|
0313910473 | |
Frisby 8 – SWS 8S | |
1973 | |
| 33.0912255 | | |
| -92.6835493 | | |
| |
| |
| |
YES |
0313912624 | |
GLCC Waste Disposal | |
1973 | |
| 33.1833202 | | |
| -92.7122686 | | |
| |
| |
| |
YES |
0313910076 | |
H Carroll 1 | |
1969 | |
| 33.1668170 | | |
| -92.7882400 | | |
| |
| |
| |
YES |
0313913017 | |
Huskey 1 | |
2002 | |
| 33.0436970 | | |
| -92.7662900 | | |
YES | |
YES | |
| |
|
0313912864 | |
J. Kadison #2 | |
1991 | |
| 33.1876481 | | |
| -92.8572285 | | |
YES | |
YES | |
YES | |
YES |
0302710233 | |
Jennings -Owens 1 | |
1974 | |
| 33.0547476 | | |
| -93.0229414 | | |
YES | |
YES | |
| |
|
0313911491 | |
Jerry Estate 1 | |
1981 | |
| 33.1967050 | | |
| -92.5013200 | | |
YES | |
YES | |
| |
|
0313904794 | |
Kadison, Joy 1 | |
1966 | |
| 33.1907270 | | |
| -92.8647700 | | |
YES | |
| |
| |
|
0313910555 | |
King, B W 1 | |
1974 | |
| 33.3268740 | | |
| -92.9559800 | | |
YES | |
YES | |
| |
|
0313913545 | |
LANXESS 1 | |
2017 | |
| 33.0385880 | | |
| -92.6762690 | | |
YES | |
YES | |
YES | |
|
0313910541 | |
Loutre 14 | |
1974 | |
| 33.1048891 | | |
| -92.5890446 | | |
| |
| |
| |
YES |
0313913014 | |
Lowery 1 | |
2002 | |
| 33.0513214 | | |
| -92.7912450 | | |
YES | |
YES | |
| |
|
0313910831 | |
LYLE DEWS 1 | |
1976 | |
| 33.3486300 | | |
| -92.9279800 | | |
YES | |
YES | |
| |
|
0313911459 | |
Mahony, J K 1 | |
1981 | |
| 33.2924350 | | |
| -92.8647900 | | |
YES | |
YES | |
| |
|
0313910776 | |
McCorkle 1 | |
1976 | |
| 33.1480600 | | |
| -92.7203300 | | |
YES | |
YES | |
| |
|
0313910815 | |
MORGAN 1 | |
1976 | |
| 33.3210030 | | |
| -92.8982900 | | |
YES | |
YES | |
| |
|
0313912751 | |
Murphy 3 | |
1988 | |
| 33.2091400 | | |
| -92.8604000 | | |
YES | |
| |
| |
|
0313910461 | |
Murphy 6 | |
1973 | |
| 33.1011990 | | |
| -92.6722196 | | |
| |
| |
| |
YES |
0313911004 | |
Murphy A-1-8 | |
1978 | |
| 33.0848524 | | |
| -92.8769567 | | |
YES | |
YES | |
| |
|
60 |
 |
RSI-3353 |
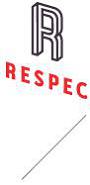
API
Number | |
Well
Name | |
Year
Drilled | |
| Latitude | | |
| Longitude | | |
Structure Data | |
Porosity Data | |
Core Data | |
Production
or Injection
Data |
0313912661 | |
Murphy Estate 2 | |
1986 | |
| 33.2053450 | | |
| -92.8651400 | | |
YES | |
| |
| |
|
0313912662 | |
Natural Resources 1 | |
1986 | |
| 33.2030870 | | |
| -92.8304700 | | |
YES | |
| |
| |
|
0302710779 | |
Newell Etal 1 | |
1980 | |
| 33.0355461 | | |
| -92.9988495 | | |
YES | |
YES | |
| |
|
0313912423 | |
Pendleton 1 | |
1984 | |
| 33.1393000 | | |
| -92.6716400 | | |
YES | |
YES | |
| |
YES |
0313972061 | |
Reeves BSW 7M 1 | |
1977 | |
| 33.1846470 | | |
| -92.8583700 | | |
YES | |
YES | |
| |
|
0313912867 | |
Robertson 1 | |
1991 | |
| 33.1078500 | | |
| -92.5561100 | | |
YES | |
YES | |
| |
YES |
0313912905 | |
Rogers 1 | |
1993 | |
| 33.0635450 | | |
| -92.7530700 | | |
YES | |
| |
| |
|
0313910921 | |
Rosen Trust 1 | |
1983 | |
| 33.3153460 | | |
| -92.8756400 | | |
YES | |
YES | |
| |
|
0313911387 | |
Russell 1 | |
1980 | |
| 33.2156140 | | |
| -92.7606900 | | |
YES | |
| |
| |
|
0313912789 | |
Scales, Frances BSW 9 | |
1989 | |
| 33.1871214 | | |
| -92.8489570 | | |
YES | |
YES | |
| |
YES |
0313913401 | |
Sessions 1 | |
1926 | |
| 33.2905500 | | |
| -92.8625260 | | |
| |
| |
| |
YES |
0313904383 | |
Shell-Pratt, J. C. | |
1948 | |
| 33.0294040 | | |
| -92.6001400 | | |
YES | |
| |
| |
|
0313912177 | |
Spencer 1 | |
1983 | |
| 33.1741300 | | |
| -92.7971500 | | |
YES | |
YES | |
| |
YES |
0313911402 | |
SWD 10M | |
1980 | |
| 33.1716357 | | |
| -92.9644587 | | |
YES | |
YES | |
| |
YES |
0313911397 | |
SWD 12 | |
1980 | |
| 33.1705550 | | |
| -92.6735000 | | |
YES | |
YES | |
| |
YES |
0313912790 | |
SWD 12M | |
1989 | |
| 33.1508013 | | |
| -92.8373076 | | |
YES | |
| |
| |
YES |
0313912781 | |
SWD 13 | |
1988 | |
| 33.1702080 | | |
| -92.6414200 | | |
YES | |
YES | |
| |
YES |
0313912921 | |
SWD 14M | |
1993 | |
| 33.1543553 | | |
| -92.8512415 | | |
| |
| |
YES | |
YES |
0313912912 | |
SWD 15 | |
1993 | |
| 33.1979180 | | |
| -92.7068415 | | |
YES | |
| |
| |
YES |
0313912919 | |
SWD 16 | |
1993 | |
| 33.1877020 | | |
| -92.7109900 | | |
YES | |
YES | |
| |
YES |
0313912940 | |
SWD 16M | |
1995 | |
| 33.2955500 | | |
| -92.9645800 | | |
YES | |
YES | |
YES | |
YES |
0313912925 | |
SWD 17 | |
1994 | |
| 33.1851655 | | |
| -92.6730410 | | |
| |
| |
| |
YES |
0313912942 | |
SWD 17M | |
1995 | |
| 33.2926369 | | |
| -92.8828778 | | |
YES | |
YES | |
YES | |
YES |
0313912943 | |
SWD 18M | |
1995 | |
| 33.2917600 | | |
| -92.9408100 | | |
| |
| |
YES | |
YES |
0313912947 | |
SWD 19M | |
1995 | |
| 33.2919511 | | |
| -92.9049207 | | |
| |
| |
YES | |
YES |
0313910559 | |
SWD 1M | |
1994 | |
| 33.1660420 | | |
| -92.9582750 | | |
| |
| |
YES | |
YES |
0313912939 | |
SWD 21S | |
1995 | |
| 33.1105533 | | |
| -92.7046875 | | |
YES | |
| |
| |
YES |
0313913592 | |
SWD 22S | |
2019 | |
| 33.1331525 | | |
| -92.6942309 | | |
YES | |
YES | |
| |
YES |
0313910578 | |
SWD 2M | |
1975 | |
| 33.1589583 | | |
| -92.9385476 | | |
YES | |
YES | |
YES | |
YES |
0313904790 | |
SWD 3 | |
1966 | |
| 33.1384300 | | |
| -92.7586200 | | |
| |
| |
| |
YES |
0313911226 | |
SWD 3A | |
1980 | |
| 33.1670700 | | |
| -92.6737200 | | |
YES | |
YES | |
YES | |
YES |
0313910803 | |
SWD 3M | |
1976 | |
| 33.1515200 | | |
| -92.9253300 | | |
YES | |
YES | |
| |
YES |
0313904791 | |
SWD 4 | |
1967 | |
| 33.1348054 | | |
| -92.7583276 | | |
| |
| |
YES | |
YES |
0313912800 | |
SWD 4A | |
1989 | |
| 33.1578570 | | |
| -92.6728418 | | |
| |
| |
| |
YES |
0313910671 | |
SWD 4M | |
1975 | |
| 33.1506974 | | |
| -92.9087054 | | |
YES | |
YES | |
| |
YES |
0313910035 | |
SWD 5 | |
1969 | |
| 33.1259100 | | |
| -92.7851000 | | |
| |
| |
| |
YES |
0313910452 | |
SWD 5 | |
1973 | |
| 33.1973080 | | |
| -92.6906360 | | |
YES | |
YES | |
| |
YES |
0313910863 | |
SWD 5M | |
2008 | |
| 33.1456000 | | |
| -92.8814800 | | |
YES | |
YES | |
| |
YES |
0313910487 | |
SWD 6 | |
1973 | |
| 33.1547052 | | |
| -92.6639400 | | |
YES | |
YES | |
| |
YES |
0313912713 | |
SWD 6 | |
1987 | |
| 33.1321730 | | |
| -92.8002839 | | |
| |
| |
| |
YES |
0313912933 | |
SWD 6A | |
1994 | |
| 33.1547740 | | |
| -92.6637200 | | |
| |
| |
| |
YES |
0313910929 | |
SWD 6M | |
1977 | |
| 33.1669120 | | |
| -92.9606200 | | |
YES | |
YES | |
| |
YES |
0313910525 | |
SWD 7 | |
1974 | |
| 33.1753119 | | |
| -92.6509982 | | |
YES | |
| |
| |
YES |
0313912749 | |
SWD 7 | |
1988 | |
| 33.1721080 | | |
| -92.7434840 | | |
| |
| |
| |
YES |
61 |
 |
RSI-3353 |
API
Number | |
Well
Name | |
Year
Drilled | |
| Latitude | | |
| Longitude | | |
Structure Data | |
Porosity Data | |
Core Data | |
Production
or Injection
Data |
0313911122 | |
SWD 7M | |
1979 | |
| 33.1461423 | | |
| -92.8672778 | | |
YES | |
YES | |
YES | |
YES |
0313910530 | |
SWD 8 | |
1974 | |
| 33.1824023 | | |
| -92.6470486 | | |
YES | |
YES | |
| |
YES |
0313983124 | |
SWD 8 | |
2008 | |
| 33.1430100 | | |
| -92.7615900 | | |
| |
| |
| |
YES |
0313911129 | |
SWD 8M | |
1979 | |
| 33.1455100 | | |
| -92.8515300 | | |
YES | |
YES | |
YES | |
YES |
0313911232 | |
SWD 9M | |
1980 | |
| 33.1713417 | | |
| -92.9600731 | | |
YES | |
YES | |
YES | |
YES |
0313910561 | |
Templeton 17S | |
1974 | |
| 33.0800500 | | |
| -92.6030400 | | |
YES | |
| |
| |
YES |
0313903415 | |
Triangle 1 | |
1961 | |
| 33.1921132 | | |
| -92.7755764 | | |
| |
| |
| |
YES |
0313910466 | |
Trimble 9 | |
1973 | |
| 33.1050570 | | |
| -92.7116400 | | |
YES | |
| |
| |
YES |
0313904360 | |
Union Sawmill 1 | |
1939 | |
| 33.0553630 | | |
| -92.5413060 | | |
YES | |
| |
| |
|
0313912817 | |
Waste Disposal Well | |
1989 | |
| 33.1849300 | | |
| -92.9390700 | | |
| |
| |
| |
YES |
0313983122 | |
Wilson 1 | |
1982 | |
| 33.1666017 | | |
| -92.7588750 | | |
| |
| |
| |
YES |
0313912929 | |
Woods 18S | |
1994 | |
| 33.1052858 | | |
| -92.6134203 | | |
YES | |
YES | |
| |
YES |
62 |
 |
RSI-3353 |
| 11.0 | Sample
Preparation, Analyses, and Security |
Standard Lithium’s
Property sampling programs and the analyses performed prior to 2022 are described in detail in the MIRE (Eccles et al. 2018) and PEA
(Dworzanowski et al. 2019). QP Brush has reviewed those reports and agrees with those reports’ conclusions that the sampling programs
they described were appropriate, appear to have been executed correctly and securely, and provided samples that were used to prepare
reasonable brine lithium composition estimates.
QPs Brush and Williams participated in the May 2022
brine sampling program. The samples were collected in a consistent and secure manner, with a clear chain of custody from the sample collection
point to the shipment to the laboratory and following the procedures summarized below.
Brine sampling undertaken
to support resource definition and geochemical analysis was completed with a key focus on ensuring the integrity of the brine sample.
The LANXESS bromine plants
and well/pipeline infrastructure were originally designed specifically for brine collection, processing and production of bromine from
Smackover brine. Accordingly, as a brine-specific production-system, brine access points were available throughout the Property and were
utilized for sampling.
Samples were collected
at all operating brine supply wells and all bromine processing facilities at locations prior to and after bromine processing.
Brine sampling programs
were undertaken using a methodology as summarized below:
| / | Prepare
and label new laboratory supplied containers including sample ID, date and time of sample
collection and the sampler’s initials. Sample containers required to support the required
analytical suite: |
| » | Unpreserved
Poly (density, pH, alkalinity, TDS, anions) – 1000 ml |
| » | Nitric
acid (HNO3) Preserved Poly (Metals) – 500 ml |
| » | Phosphoric
acid (H3PO4) Preserved Amber Glass (TOC) – 250 ml |
| / | Purge
the sample point for a period of 5-10 seconds to ensure the spigot is cleared of any stagnant
brine, oil, dirt or other contaminants. |
| / | Following
purging, fill the required sample containers to capacity, or near-capacity and immediately
seal container. |
| / | Re-check
sample containers to verify that all sample label information is correct, and the sample
container is properly sealed. |
| / | Store
samples in a cooler for transport to the analytical laboratory. |
63 |
 |
RSI-3353 |
| / | Collect
an additional 250 ml sample for additional field measurement using a Myron Ultrameter 6PIIFCE.
Calibrate meter prior to use and record: |
| » | Electrical
conductivity; |
| » | Oxidation
Reduction Potential; and, |
| / | Complete
the sampling process by recording physical attributes of the brine samples and any comments
that might be significant to the sampling site, the sample collection or the sample itself. |
Field
duplicate samples, standard sample blanks and synthetic brine standard samples were employed for quality assurance and quality control
purposes as follows:
| / | Field
duplicate samples, taken at the same time as the original sample, were collected for every
10 field samples collected and assigned random identification prior to laboratory delivery
to confirm precision of the laboratory results. |
| / | Standard
sample blanks were inserted for every 10 field samples taken as an additional laboratory
check. Sample blanks were comprised of deionized water, which contained no lithium. |
| / | Synthetic
brine solutions with 250 mg/L Li and a TDS of 250,000 mg/L were prepared by University of
British Columbia. The synthetic brine samples were included in sample sets at a rate of 1
sample for every 20 laboratory samples to measure the accuracy of the laboratory. |
Sample
security protocols including chain of custody documentation, sealed delivery containers and delivery auditing were employed as part of
the sampling program.
| 11.1.2 | Analytical
Protocol |
Analysis
of brine samples collected was undertaken by independent laboratories covering an expanded lithium brine analytical suite prepared specifically
for the Project and which included the following analytical work (following the associated ASTM, SM and EPA international and national
method code):
| / | General
chemistry: density, pH, temperature, carbonate, bicarbonate, total dissolved solids, total
organic carbon (ASTM 1963, SM 4500-H+B, SM 2550B, SM 2320B, SM 2540C and SM 5310B). |
| / | Anions
by Ion Chromatography: chloride, sulfate, bromide, fluoride (EPA 300.0). |
| / | Sample
preparation: trace metal digestion (EPA 200.2). |
| / | Trace
metals by ICP-OES: Al, Sb, As, Ba, Be, B, Cd, Ca, Cr, Co, Cu, Ga, Fe, Pb, Li, Mg, Mn, Mo,
Ni, P, K, Sc, Se, Si, silica, Ag, Na, Sr, Sn, Ti, V and Zn (EPA 200.7). |
64 |
 |
RSI-3353 |
| 12.1 | Verification
of Lithium Concentration Data |
QP Brush verified the lithium
concentration data five different ways:
| / | Reviewed
the choice of analytical laboratory |
| / | Reviewed
the overall scatter in each well’s lithium concentration data |
| / | Compared
concentration results between samples taken by the author and those by Standard Lithium |
| / | Compared
concentration results between known standards and reported concentrations |
| / | Compared
the recent Wetlabs results to historic data. |
In 2021, subsequent to
the reviews of the analytical laboratories in the MIRE (Eccles et al. 2018) and PEA (Dworzanowski et al. 2019) which found WetLab to
be acceptable as the primary analytical laboratory for the Project, Standard Lithium conducted an extensive comparison test of four laboratories
known for brine analysis. This study’s results indicate that WetLabs is the appropriate choice for the range of lithium concentrations
encountered in this TR. QP Brush has reviewed the supporting documentation of that study and agrees with its conclusions. As a result,
WetLabs-reported lithium concentration data is used throughout this TR.
The lithium data summary,
Table 9-1, shows the number of samples for each well over all sampling events and the percent standard deviation for each well, ranging
from 0.6 percent to 22.2 percent, with an average of 9.2 percent for all the wells. This captures the variation between sampling events
and between samples within a given sampling event. The observed standard deviation values are an acceptable level of uncertainty for
the lithium concentration values.
While not used in this
report’s lithium concentration analyses because of uncertainty in the testing methodologies, the available earlier lithium concentration
data was reviewed and found to be consistent with the Wetlabs lithium concentration data. Figure 12-1 is a map of the average WetLab
lithium concentration values from Table 9-1. Figure 12-2 adds the historical values from the USGS, LANXESS sampling in 1990, and other
values presented in Moldovanyi and Walker, 1992. While there is the expected scatter in the data, the historical values are in close
agreement with the WetLab values, aside from two clear errors in the historical data (the 5 mg/L and 1,700 mg/L data points). This exhibit
confirms that the WetLab values reasonably represent the current distribution of lithium in the Property’s sampled wells.
65 |
 |
RSI-3353 |
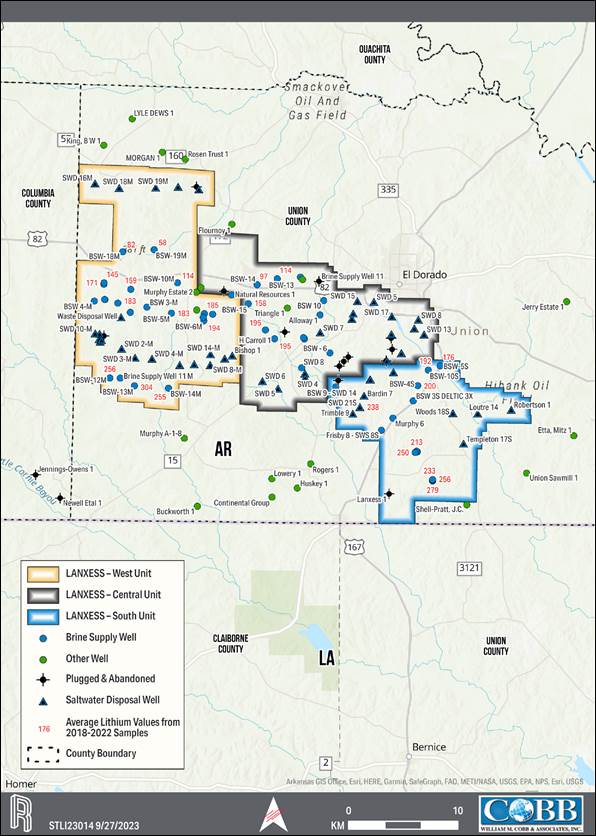
Figure 12-1. Recent
Average Well Lithium Concentrations
66 |
 |
RSI-3353 |
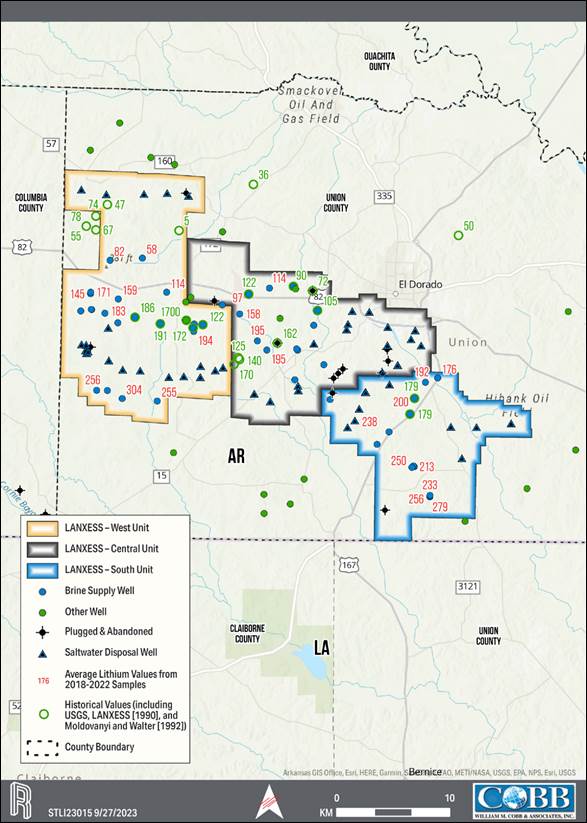
Figure 12-2. Historical
and Recent Well Lithium Concentrations
67 |
 |
RSI-3353 |
Table 12-1 lists the
comparison samples' lithium concentrations, the absolute percent variation of the WCA samples from the Standard Lithium samples, and
the statistical characterization of the comparison. Figure 12-3 compares those two sets of lithium concentration results. For each
data point an error bar representing a two standard deviation range of Absolute Percent Variation is shown. From this plot one can conclude
that the Standard Lithium samples results were closely related to the results for the WCA duplicate samples. In all but one case the
error bar encounters the X = Y line. The best fit line to the cross plot of the two data sets indicates the WCA duplicate samples average
7.2 percent higher than the Standard Lithium samples.
To evaluate the accuracy
of the laboratory two types of calibration samples were sent for analysis, interspersed with the well test samples. Three samples (two
Standard Lithium, one WCA) of deionized water with no lithium were found to contain less than 2.0 mg/L of lithium (the minimum measurement
sensitivity of the laboratory). A total of 17 samples (16 Standard Lithium, one WCA) of synthetic brine with 250 mg/L of lithium were
found to contain, on average, 280 mg/L of lithium. This average value is within 0.8 standard deviation (37 mg/L) of the calibration sample
lithium concentration. Both sets of comparisons demonstrate the accuracy and repeatability of the laboratory results.
Based on these three different analyses,
QP Brush concludes that the preparation, security, and analysis of May 2022 sampling program, as well as the prior sampling programs,
were appropriate, with no significant issues identified, resulting in lithium concentration values that are valid for the purposes of
this report.
68 |
 |
RSI-3353 |
Table 12-1.
Sample Concentration Comparison
Well | |
Standard
Lithium Sample
mg/L Li | | |
WCA
Sample
mg/L Li | | |
Absolute
%
Variation | |
BSW 14 | |
| 101 | | |
| 111 | | |
| 9.4 | % |
BSW 13 | |
| 121 | | |
| 123 | | |
| 1.6 | % |
BSW Spencer | |
| 192 | | |
| 224 | | |
| 15.4 | % |
BSW 15 | |
| 199 | | |
| 200 | | |
| 0.5 | % |
BSW 24S | |
| 199 | | |
| 267 | | |
| 29.2 | % |
BSW 20S | |
| 220 | | |
| 224 | | |
| 1.8 | % |
BSW Carrol | |
| 224 | | |
| 223 | | |
| 0.4 | % |
BSW 21S | |
| 240 | | |
| 238 | | |
| 0.8 | % |
BSW 22S | |
| 264 | | |
| 325 | | |
| 20.7 | % |
BSW 23S | |
| 285 | | |
| 267 | | |
| 6.5 | % |
| |
| Minimum | | |
| 0.4 | % |
| |
| Maximum | | |
| 29.2 | % |
| |
| Mean | | |
| 8.6 | % |
| |
| Standard
Deviation | | |
| 9.5 | % |
| |
| Best
Fit Slope | | |
| 1.072 | |
| |
| Best
Fit R2 | | |
| 0.986 | |
69 |
 |
RSI-3353 |
Figure
12-3. Duplicate Sample Comparison
12.2 | Verification
of Well Logs and Core Data |
The well log and core data used to create
the geologic model meets the standard of reliability required by this report. This data was taken by independent vendors in a manner
meeting industry standards, consistent with the identical data collection procedures used in dozens of projects evaluated by QPs Brush
and Williams over the last 30+ years. Importantly, this data was obtained for a purpose unrelated to the estimation of lithium resources
and reserves. Therefore, it was not subject to any biases related to that estimation process.
12.3 | Verification
of Production and Injection Data |
The
brine production and injection rates used to history match the reservoir simulation model are the product of LANXESS’ Property
operations and are used as the basis of their daily operations. LANXESS has made every effort over the years to provide accurate data,
recognizing that the quality of the bromine process evaluations depends directly on the quality of the data provided by LANXESS. The
brine production and injection rates used in the reservoir simulation model forecasts are the result of discussions with LANXESS and
represent their best current estimates for rates associated with future operations.
70 |
 |
RSI-3353 |
12.4 | Qualified
Person’s Opinion |
Each well’s production or injection
data has been reviewed as part of the history matching process, and the data was found suitable for this evaluation. The lithium concentration,
well log, core, production, and injection data used in the preparation of this TR meets the highest standards for the evaluation of the
brine deposit. Any limitations present in the data are the unavoidable limitations present in all field measurements. LANXESS and its
predecessor companies have exerted industry-standard efforts in gathering high-quality data on the Property. The Property’s data
gathering program has been thorough over its history, and this history of high-quality data gathering results directly in a high-quality
database for use in this evaluation of the Property’s lithium deposit.
71 |
 |
RSI-3353 |
13.0 | Mineral
Processing and Metallurgical Testing |
Standard Lithium has developed a process
flowsheet to selectively extract lithium from Smackover Formation brine and produce battery-quality lithium carbonate. Smackover brine
used for lithium extraction by the Project will originate from the LANXESS Tail Brine system delivered from the existing South Brine
Unit supply well network and South Plant bromine extraction operation. The Project will pre-treat the brine received from LANXESS to
condition the brine prior to the lithium extraction process. The mineral processing and hydrometallurgical flowsheet for the Project
consists of seven process areas, three of which areas are included in LANXESS’ existing operations:
1. | Brine
Production – Brine from the Smackover Formation is produced from multiple existing
brine supply wells, separated from associated sour gas and crude oil through three-phase
separators at the wellheads, and then delivered via pipeline to the LANXESS South Plant. |
2. | Bromine
Extraction and Tail and Bypass Brine Pre-treatment – Brine received from the field
at the LANXESS South Plant is treated to remove most of the dissolved H2S in the
brine by vacuum degassing. The degassed brine is fed into a bromine tower where it is reacted
with elemental chlorine (Cl2), converting bromides in the brine to elemental bromine
(Br2). Bromine extracted from the brine is recovered from the top of the bromine
tower and (bromide-barren) Tail Brine discharges from the bottom of the bromine tower. Before
the Tail Brine is delivered to Standard Lithium for lithium extraction, it is first pre-treated
with sodium bisulfite (NaHSO3) to reduce the free chlorine and free bromine from
the brine and then is partially neutralized with anhydrous ammonia. If the bromine tower
is not operating for any reason, to avoid shutting down brine production wells, degassed
brine bypasses the bromine tower and is discharged directly into the Tail Brine system downstream
of sodium bisulfite dosing. Bypass Brine is partially neutralized, similar to Tail Brine.
The pre-treated Tail Brine and Bypass Brine is then pumped to the Standard Lithium Plant. |
3. | Feed
Brine Pre-Treatment for Lithium Extraction – Brine received from the LANXESS South
Plant is neutralized, chemically adjusted to increase the ORP (oxidation-reduction potential),
and then is filtered to remove suspended solids that could interfere with the downstream
Direct Lithium Extraction (DLE) process. |
4. | Direct
Lithium Extraction (DLE) Process) – A proprietary Direct Lithium Extraction (DLE)
process is used for extraction of lithium from the pre-treated brine, producing a relatively
pure lithium chloride (LiCl) solution that is low in contaminants. |
5. | Purification
and Concentration of the LiCl Solution – Further purification and concentration
of the LiCl solution produced by the DLE process uses chemical softening and impurity removal
processes that are industry standard processes for water and wastewater treatment, including
BWRO (Brackish Water Reverse Osmosis), lime soda softening, ion exchange for removal of calcium
(Ca), magnesium (Mg), and boron (B), and OARO (Osmotically-Assisted Reverse Osmosis). |
6. | Battery-Quality
Lithium Carbonate Production – Purified LiCl solution is converted to battery-quality
lithium carbonate in an industry-proven process that includes reacting the LiCl with sodium
carbonate (Na2CO3), producing crude lithium carbonate, conversion to
lithium bicarbonate, ion exchange, secondary crystallization to produce pure lithium carbonate,
and finally drying, milling, and packaging of the final product. |
72 |
 |
RSI-3353 |
7. | Effluent
Brine Return to LANXESS for Reinjection – The final process is the return of the
lithium-depleted, barren brine from the DLE process and other Project effluents back to LANXESS
for reinjection into the Smackover Formation, and disposal of any excess effluent brine volume
into two Underground Injection Control (UIC) wells. |
With respect to the above identified
process areas 1, 2 and 7, the Project relies on the existing brine infrastructure of the LANXESS South Plant for the supply of lithium-rich
brine and disposal of most of the Project’s effluent brine. Testing programs associated with these process areas focused primarily
on the characterization of the quality of Feed Brine to be processed by the Project.
With respect to process areas 3, 4 and
5, Standard Lithium has been continuously running a pre-commercial Demonstration Plant at the LANXESS South Plant since May 2020.
This operation has produced significant data on the performance of the various unit processes for pre-treatment of brine from the South
Plant and operation of the DLE technology on this brine. The Demonstration Plant has produced significant quantities of purified and
concentrated LiCl solution and has converted portions into battery-quality lithium carbonate, on site and at vendor facilities.
With respect to process area 6, Standard
Lithium is relying on commercially proven lithium carbonate conversion technologies from globally recognized vendors. These vendors have
supported the Project with specific bench-scale testing at their laboratory facilities using LiCl solution produced at the Demonstration
Plant to validate vendor guarantees related to commercial-scale production of battery-quality lithium carbonate in the Project.
The intent of this Section is to
provide an overview of the specific lithium-brine mineral processing test work completed to support the characterization of the brine
resource (i.e., brine quality) as well as support the development of commercial processes for the Project and confirm the associated
process performance.
Standard Lithium plans to use a demonstrated
proprietary DLE technology (discussed further in Section 13.5.1) to extract lithium from the pre-treated, lithium-bearing, Smackover
brine, supplied as tail and Bypass Brine from the LANXESS South Plant. The DLE process selected for the Project produces a slightly concentrated
and significantly more pure brine than the received Feed Brine. The LiCl solution produced by the DLE process is purified and concentrated,
then converted to battery-quality lithium carbonate using an industry-proven lithium carbonate process. The lithium extraction technology
described in this study has been operated on a 24hr / 7 day per week basis at Standard Lithium’s Demonstration Plant since October 2022.
The brine pre-treatment and DLE technology, while still being optimized, has been sufficiently tested and validated for commercial use
for the Project.
Figure 13-1 provides a simplified schematic
illustrating the main process steps proposed for the Project using Feed Brine from the LANXESS South Plant.
73 |
 |
RSI-3353 |
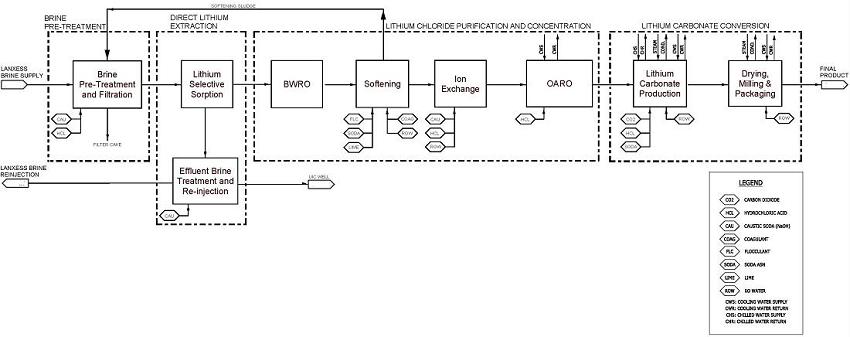
Figure
13-1. Project Process Block Flow Diagram
It is the opinion of the author preparing
this section, that the discussion includes an objective level of reasonableness and demonstrates competence and due care in the execution
of the metallurgical test work and lithium-brine recovery process steps.
All testing discussed below was performed
for or by Standard Lithium as part of the current development program either to support the Project or the broader developments contemplated
by Standard Lithium in the Smackover Formation.
13.3 | Demonstration
Plant Testing |
Considering the factors outlined in
Section 13.1.1, alternative methods to those commercially proven in lithium recovery from salar-based brines are required to continuously
extract and purify lithium from the Smackover brines. Standard Lithium has been assessing and testing technologies with a specific focus
on direct lithium extraction which to date is somewhat unproven at a commercial scale. The process evaluation conducted at the Demonstration
Plant over 3 years of operation included extensive testing of two separate DLE technologies:
| 1. | LiSTR
(Lithium Stirred Tank Reactor), a proprietary DLE technology developed, owned and patented
by Standard Lithium, which directly extracts lithium from high total dissolved solids (TDS)
brines using a high-loading-capacity, lithium-selective, solid sorbent based on lithium titanate,
in a continuous stirred tank reactor configuration. (Testing of this DLE process occurred
from May 2020 through to October 2022); and |
| 2. | LSS
(Lithium Selective Sorption, a component of the broader Li-PROTM technology),
a Koch Technology Solutions owned (KTS), proprietary, DLE technology. The LSS technology
uses a fixed bed of commercially available alumina-based resin. This technology has been
co-developed under a Joint Development Agreement between Standard Lithium and Koch Technology
Solutions. (Testing of this DLE process has commenced in October 2022 and is ongoing
as of the publishing date of this report). |
74 |
 |
RSI-3353 |
13.1.1 | Demonstration
Plant |
The Standard Lithium LiSTR Demonstration
Plant, was designed and constructed in Ontario, Canada in 2019 by Zeton Inc. The Demonstration Plant was designed to continuously process
a slipstream of the lithium-containing Tail Brine produced by the LANXESS South Plant bromine facility with a focus on developing and
confirming the operation of an integrated DLE flowsheet to allow the design of a future commercial production facility. The two DLE processes
that have been operated in the Demonstration Plant have been adjusted and optimized over time to allow integration into the full commercial
plant flowsheet. At the Demonstration Plant, the lithium-barren brine from the DLE processes, various other process effluents, and all
of the LiCl solution not used for test production of lithium carbonate are continuously transferred back to the LANXESS brine disposal
system; no lithium products were produced for sale at this test facility.
The Demonstration Plant as shown in
Figure 13-2, which consisted of 18 modules, was dismantled and transported from Canada to its current location at the LANXESS South Plant
bromine facility in Union County, Arkansas (south of the Town of El Dorado). It was erected within the existing fence line of the South
Plant on a one acre site leased from LANXESS. The site was levelled, foundations were poured, and all process, utility and power connections
were installed to ready the Demonstration Plant for operation in late 2019. The plant was installed/connected and enclosed in a tensile
fabric building in late 2019 and underwent commissioning in early 2020. Commissioning was partially delayed by the COVID-19 pandemic
and associated lockdowns. The Demonstration Plant commenced operations in May 2020.
75 |
 |
RSI-3353 |
Figure
13-2. Standard Lithium Demonstration Plant
The Demonstration Plant initially comprised
of brine pre-treatment, LiSTR DLE process tanks and equipment, and purification equipment for removal of calcium, magnesium and silica.
Process modifications to address scalability for commercialization were made in December 2020 and an osmotically assisted reverse
osmosis (OARO) unit was installed at the plant in August 2021 (membrane concentration of the purified LiCl product operation had,
until that point, been completed off-site as an occasional batch process).
Modifications were implemented in September and
October 2022 to install a fixed bed column and support equipment to prove out the second DLE process (LSS). Several subsequent modifications
have been made at the Demonstration Plant for continuing optimization of this process, including addition of a second LSS column in March 2023.
The Demonstration Plant has a dedicated
team of approximately 30 engineers, chemists, operators, and maintenance staff who run and maintain the plant on a 24 hour per day, 7
day per week basis. The plant has operated continuously since it was started, apart from shutdowns for maintenance, process improvements,
and supply outages caused by interruptions to the LANXESS brine supply. The plant includes a dedicated analytical laboratory equipped
to complete all on-site process control assays. The plant’s high level of process instrumentation and extensive program of sampling
and analysis have generated large amounts of data. The data collection underpins the assessment in this report.
76 |
 |
RSI-3353 |
The Demonstration Plant has processed
two different brines from the LANXESS South Plant: Tail Brine (brine that has been through the bromine extraction process) and Bypass
Brine (brine that has been degassed to remove hydrogen sulfide but has not been through the bromine extraction process). Representative
analyses of the Demonstration Plant brine solutions are provided in Table 13-1. There have been several periods when Bypass Brine with
>4,000 mg/L of bromide has been supplied to the DLE processes and the rest of the Demonstration Plant’s purification and concentration
processes.
Brine pre-treatment performed by LANXESS
utilizes a reducing chemical, sodium bisulfite (NaHSO3), to reduce free bromine and chlorine to low levels by converting them
to their respective bromides and chlorides. It has been observed that neither of the two DLE processes operated in the Demonstration
Plant (LiSTR and LSS) were impacted by dissolved bromide concentrations in the brine. It was found that the bromides behave similarly
to chlorides and are largely rejected with the lithium-barren brine and do not pass through into the LiCl product stream in any significant
amounts.
As of the end of Q2 2023, the Demonstration
Plant has processed approximately 55,500 m³ (approximately 14,700,000 US gallons) of brine from the LANXESS South Plant.
The purified and concentrated LiCl product
solution from the Demonstration Plant along with brine from various stages of the Demonstration Plant flowsheet have been supplied to
equipment vendors for testing in support of equipment design and process guarantees. The purified and concentrated LiCl product solution
from the Demonstration Plant has also been converted to battery-quality lithium carbonate both on site at the Demonstration Plant and
offsite by vendor testing laboratories.
The Demonstration Plant operation period
when the LiSTR DLE process was operated between May 2020 and October 2022 provided useful information to further the overall
process development. This included, but was not limited to:
| / | Development
of analytical techniques to evaluate process operational performance, |
| / | Understanding
the variability and characteristics of the Tail Brine received from LANXESS, |
| / | Evaluation
of potential materials of construction through plant operation and submerged metallurgical
coupon testing, |
| / | Demonstration
of membrane ultra-filtration (UF) system operation, |
| / | Demonstration
of multi-media filtration, |
| / | Demonstration
of Osmotically Assisted Reverse Osmosis (OARO), |
| / | Operation
of calcium, magnesium, and boron removal by ion exchange, |
| / | Preparation
of samples for three lithium carbonate crystallization campaigns conducted in the laboratories
of two vendors of lithium carbonate systems. |
Since October 2022, test work at
the Demonstration Plant is on-going using the LSS DLE technology. The LSS testing program is expected to continue to optimize the operation
and product quality.
Operations within the Demonstration
Plant can be systematically varied, and as such, the effect of changing operating parameters on performance metrics such as degree of
lithium recovery from the incoming brine, rejection of impurities, reagent usage and water balance have all been studied in a controlled
manner. As with any industrial process, there are many competing factors, and the optimal operation has been proven to be a trade-off
between the various inputs. For reference, representative LiCl analyses generated by the two flowsheets tested in the Demonstration Plant
are provided in Table 13-1, though these can be modified by varying the processes in the Demonstration Plant.
77 |
 |
RSI-3353 |
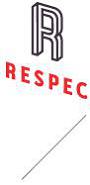
A test program is in progress at SGS
(Société Générale de Surveillance) laboratory using brine and LSS eluate supplied from the Demonstration
Plant which is exploring brine pretreatment (prior to LSS) and post treatment of the LSS Eluate. Specifically, this includes lime—soda
softening which will precipitate calcium, magnesium, strontium, and silica followed by ion exchange to reduce the above impurities to
levels near 1 mg/L.
Table 13-1. Representative Analyses
of Brine and LiCl Products.
Table 13-1.
Demonstration Plant LiCl Analysis
Element | |
Brine
Feed to Demonstration Plant from LANXESS1 (mg/L) | | |
Raw
LiCl from LiSTR DLE2,3(mg/L) | | |
Raw
LiCl from LSS DLE2,4(mg/L) | | |
Polished
LiCl from Demonstration Plant2,5(mg/L) | |
Lithium (Li) | |
| 237 | | |
| 1427 | | |
| 301 | | |
| 4917 | |
Sodium (Na) | |
| 61136 | | |
| 2217 | | |
| 817 | | |
| 28896 | |
Calcium (Ca) | |
| 31793 | | |
| 3423 | | |
| 620 | | |
| 0.5 | |
Magnesium (Mg) | |
| 2682 | | |
| 169 | | |
| 56 | | |
| 0 | |
Potassium (K) | |
| 2385 | | |
| N/A | | |
| 30 | | |
| 672 | |
Strontium (Sr) | |
| 1932 | | |
| N/A | | |
| 35 | | |
| 0 | |
Boron (B) | |
| 189 | | |
| N/A | | |
| 37 | | |
| 0 | |
Silicon (Si) | |
| 10 | | |
| 26 | | |
| 4 | | |
| 0 | |
Notes:
[1] Demonstration Plant brine supply
composition is average sample data collected in the Demonstration Plant from 4th May to 30th June 2023 to reflect the period
when Sr was regularly measured.
[2] All LiCl compositional data is based
on data collected during normal operation of the Demonstration Pant. The results from the on-site laboratory have been regularly validated
by independent testing by WetLabs, NV, over the period of May 2020 through to June 2023.
[3] The data from LiSTR is based on
compositional averages of approximately 6,000 hours of operation from March 2021 through to November 2021. During this period,
B, K and Sr were not measured, but data from Wetlabs samples indicates typical values of 100, 67, and 221 respectively. Following November 2021,
a sorbent development and optimization program was initiated to assess the performance of bespoke sorbents and target specific operating
parameters and long-term continuous operation was discontinued in support of shorter duration testing.
[4] The LSS data is based on compositional
averages of a 1,200-hour period of continuous operation in Q2 2023.
[5] The LiCl Product from the Demonstration
Plant is based on the average of bulk samples. The samples were produced in the Demonstration Plant by LSS DLE with subsequent IX processes
for removal of bivalent cation and boron followed by OARO for concentration suitable for vendor testing of downstream processes.
78 |
 |
RSI-3353 |
13.1.2 | Tail
Brine Measurement Skid |
A measurement and sampling skid was
designed and built by Standard Lithium to enable the Tail Brine discharged directly from the LANXESS bromine tower to be measured continuously,
and for samples of the Tail Brine to be more easily collected for laboratory analysis. A photograph of the Tail Brine measurement and
sampling skid is shown in Figure 13-3, below. Direct measurements taken by the field instrumentation on the skid were recorded in the
Demonstration Plant data archive. These measurements included: Tail Brine temperature, specific gravity, pH, ORP and turbidity.
Figure
13-3. Tail Brine Measurement Skid at the LANXESS Bromine Tower
13.1.3 | Brine
Pre-Treatment Testing |
As part of operating the pre-commercial
Demonstration Plant facility, a variety of brine pre-treatment processes, including those proposed for inclusion in the commercial operation,
have been demonstrated at the facility. These included:
| / | pH
and chemical adjustment and control using reagents for preventing and encouraging solids
precipitation and associated silica, iron, aluminum, and other metals removal, |
| / | Temperature
adjustments for protection of downstream equipment |
| / | Different
solid-liquid separation equipment: |
| » | Conventional
fabric cartridge filters |
| » | Pressurized
ultrafiltration membrane filters |
| » | Submerged
ultrafiltration membrane filters |
| » | Profiled
metal plate filters |
79 |
 |
RSI-3353 |
| » | Conventional
and lamella clarifiers, with and without coagulant and flocculant dosing |
| / | Alumina
sorbent for removing silica from the brine, |
| / | Media
filters for hydrocarbons removal |
| » | Walnut
shell media filters |
| » | Activated
carbon for hydrocarbons removal, |
Note that many of the pre-treatment
technologies tested have subsequently been discarded as likely unsuitable or unnecessary for commercialization.
13.2 | Brine
Pre-treatment at LANXESS |
Tail Brine will be chemically reduced
by the addition of sodium bisulfite (SBS) and Tail Brine or Bypass Brine will be neutralized with anhydrous ammonia at the LANXESS South
Plant in a set of four new mixed reaction tanks prior to the brine being pumped to Standard Lithium. SBS is added to reduce free bromine
and chlorine to bromide and chloride. Currently Standard Lithium is examining the use of chemical addition to stabilize the Tail Brine.
This may not be necessary once the new buffer tanks are installed by LANXESS, allowing improved control over the brine quality.
Control of the incoming Tail and Bypass
Brine pH is important for effective brine pre-treatment. The precipitate (sludge) formed during LiCl chemical softening will be recycled
to the brine pretreatment area utilizing the brine acidity to dissolve the softening sludge which is primarily calcium carbonate and
magnesium hydroxide. The Tail Brine from the bromine tower will typically be in the range of pH 0.5 to 0.7 and it will be partially neutralized
by LANXESS to between approximately pH 1 and 5.5.
In October 2022, Standard Lithium
performed Feed Brine neutralization tests using softening sludge produced by treating the LSS eluate with sodium carbonate. Lime was
not used and therefore the precipitate was substantially calcium carbonate (96.5%) with no magnesium hydroxide. The quantity of sludge
required to neutralize the Tail Brine from pH 0.55 to 4.0 was measured to be 1.5 g/l (as CaCO3) and is shown in the following
diagram. The tests performed demonstrate that softening sludge can effectively neutralize Feed Brine.
80 |
 |
RSI-3353 |
Figure
13-4. Sludge Dissolution for Tail Brine pH Adjustment
Figure
13-5. Sludge Dissolution for Brine pH Control
The brine pretreatment includes membrane
filtration to deliver a solids free liquid stream to LSS. A pilot system using Koch Separation System’s (KSS) Puron MP Filters
has been in continuous service at the Standard Lithium Demonstration Plant since March 2022. The membrane has a pore size near 0.01
mm and is expected to remove all particles > 1 micron. There have been very few operational problems.
81 |
 |
RSI-3353 |
13.5 | Key
Findings from Brine Pre-Treatment Test Work |
Key findings and outcomes from the Demonstration
Plant pre-treatment testing work are:
|
/ | Pre-treatment
of the incoming Tail and Bypass Brine is necessary to remove residual hydrogen sulfide, suspended
solids, and other contaminants which may result from brine extraction and bromine processing. |
|
/ | Real
brines processed on a continuous basis are significantly more complex than synthetic brines
based on the same underlying chloride matrix. Continuous, long-term (greater than two years)
field testing of equipment is crucial in ensuring sufficient design inputs to support reliable
scale-up. |
|
/ | The
Demonstration Plant has effectively pre-treated, neutralized, and filtered the Feed Brine
to be suitable for DLE testing. |
13.5.1 | DLE
Testing at the Demonstration Plant |
The Demonstration Plant has tested two
different DLE processes, LiSTR and LSS, as described below.
13.5.1.1 | LiSTR
DLE Testing |
The LiSTR DLE technology is a proprietary
process designed, patented, and owned by Standard Lithium. It uses a high-loading-capacity lithium titanate-based sorbent (meta-titanic
acid in its active form) for selective extraction of lithium from the brine stream using a slurry of the sorbent in stirred-tank reactors
and a conventional Counter Current Decantation (CCD) circuit. The LiSTR technology was initially developed in 2017 and went through two
main scale-ups (each approximately a 100× scale-up) during 2018 and 2019, resulting in operation in the Demonstration Plant in
May 2020.
LiSTR was originally commissioned and
operated using a commercially available sorbent from China. Since testing in the Demonstration Plant, Standard Lithium has maintained
a continued, dedicated sorbent development program over the past 3 years with the aim to develop sorbents with improved parameters for
lithium loading capacity, separation efficiency and physical/chemical robustness.
The pre-commercial operation of the
LiSTR process in the Demonstration Plant has proven high selectivity for lithium, high recovery of lithium from the brine, and long-term
reliability.
13.5.1.2 | Key
Findings from LiSTR DLE Test Work |
|
/ | Continuous
and accurate pH control in the loading and stripping reactors is critical to good performance
and sorbent stability. |
|
/ | Loading
efficiency (lithium extraction efficiency) is a direct function of sorbent capacity and mass
flux vs brine flow in the loading reactors – this is a variable that can be controlled.
Lithium extraction during loading can exceed 90% when a two-stage counter-current loading
configuration is used (the maximum sustained extraction efficiency was in excess of 95%). |
|
/ | Contaminant
(Ca, Mg, and Na) rejection efficiencies for most contaminants are consistently observed within
the Demonstration Plant to be over 98%. |
|
/ | Submerged
membranes can be used effectively in the loading reactors to remove barren (lithium-free)
brine, but their utility is limited at very high solids concentrations in the sorption slurries. |
82 |
 |
RSI-3353 |
|
/ | The
stripping performance of the sorbent is sensitive to temperature and pH and long-term operation
under stable conditions is required to optimize the process performance. |
| / | Industry-standard
counter current decantation (CCD) circuits can be used to wash the sorbent in either the
loaded or stripped (reactivated) state. |
| / | Bulk
properties and settling characteristics of the sorbent are key for effective solid-liquid
separation and sorbent recovery for recycle. |
| / | Bulk
quantities of suitable sorbent have been produced by independent third parties with pilot
scale equipment to demonstrate that sorbent can be produced at a commercial scale in North
America. |
| / | LiSTR
requires continuous addition of acid/base during loading and stripping and as a result, is
more sensitive to reagent pricing than LSS. |
The Lithium Selective Sorption (LSS)
DLE is a Koch Technology Solutions LLC (KTS) proprietary technology for which Standard Lithium has a Joint Development Agreement and
Smackover regional exclusivity agreement in place (for a period of time). This process uses a fixed bed adsorption with a lithium-selective
solid resin, based on aluminum hydroxide copolymer, a resin material with elution by fresh water rather than an acid strip as used in
LiSTR process. The core of the technology was originally developed by a consultant to Standard Lithium and purchased by KTS. The synergies
associated with the relationship between Standard Lithium, various Koch Industries businesses and the process inventor led to an opportunity
to operate and develop this process in parallel to LiSTR in the Demonstration Plant.
The LSS DLE process has been in operation
at the Demonstration Plant since October 2022 and extensive work has been undertaken to prove scale-up and reliable operation. The
LSS columns have been operated more than 6,000 cycles at the time of this technical report. Process refinement is on-going at the Demonstration
Plant and is aiming to optimize the process operation steps to determine the best balance for lithium recovery, impurity rejection, water
usage and lithium concentration that can be achieved.
To date, LSS has shown significant promise
in reducing reagent use, reducing excess water addition, and simplifying the DLE process with lower equipment costs. The LSS process
has the additional benefit that independent third-party process guarantees can be provided, and, as a result, has been recommended as
the core technology for Standard Lithium’s Commercial Lithium Extraction Plant Project.
The average recovery of lithium and
rejection of impurities for the current LSS column configuration and operating profile recorded between July 2023 and August 2023
is presented in Table 13-2 below. This process will continue to be developed and optimized in parallel with the project execution.
83 |
 |
RSI-3353 |
Table 13-2.
LSS Process Parameters
| |
Dilution | | |
Recovery/ Rejection (%) | |
| |
% | | |
Li | | |
Ca | | |
Na | | |
Mg | | |
B | |
Goal | |
<6 | | |
>95 | | |
>99.0 | | |
>99.0 | | |
>98.5 | | |
>90 | |
Average | |
| 4.7 | | |
| 95.6 | | |
| 99.7 | | |
| 99.9 | | |
| 99.3 | | |
| 95.0 | |
St. Dev | |
| 0.0 | | |
| 2.7 | | |
| 0.2 | | |
| 0.1 | | |
| 0.3 | | |
| 2.5 | |
Max | |
| 4.7 | | |
| 100.0 | | |
| 100.0 | | |
| 100.0 | | |
| 100.0 | | |
| 100.0 | |
Min | |
| 4.7 | | |
| 90.3 | | |
| 99.1 | | |
| 99.7 | | |
| 98.3 | | |
| 83.6 | |
13.5.1.4 | Key
Findings from LSS DLE Test Work |
| / | Lithium
extraction efficiencies of greater than 95% have been observed in the Demonstration Plant,
which is consistent with the expected performance of the LSS technology provided by KTS;
Similarly, contaminant (Ca, Mg, Na, and K) rejection efficiencies are consistently observed
at over 99%, while boron rejection is typically over 90%. |
| / | The
key benefits of the LSS process over LiSTR are reduced excess water use (contributing to
lower dilution of the effluent brine) which allows better control and maintenance of the
Smackover Formation pressure and the elimination of hydrochloric acid and sodium hydroxide
in the elution/regeneration steps. |
| / | The
fixed bed resin can be sensitive to high solids in the feed so proper brine feed quality
control is critical. |
| / | LSS
operation has shown that optimization of operating step volumes during loading, displacement,
and elution can provide high lithium recovery, concentration, and impurity rejection while
minimizing raffinate (lithium-barren brine) dilution. |
| / | The
commercially available resin tested in the Demonstration Plant has performed well. Refer
to the LSS performance data shown in Table 13-2. The KTS-Standard Lithium development team
believe that better performance can be achieved in terms of selectivity of lithium and rejection
of impurities. In support of this, continued optimization is on-going in the Demonstration
Plant including testing of alternate resins. |
| / | Both
DLE processes operated at the Demonstration Plant showed high selectivity for lithium extraction
from the Smackover Formation brine to produce a LiCl solution in which the ratio of lithium
to other components has been increased materially from <0.005:1 (i.e., 237 mg/L Lithium
relative to the combined impurities at approximately 95,000 mg/L Na/Ca/Mg) to closer to a
0.2:1 (301mg/L lithium relative to approximately 1,500 mg/L). In addition, both lithium extraction
processes are not measurably affected by the presence or absence of bromide in the incoming
brine. |
| / | The
proven performance of LSS in the Demonstration Plant, the reduced excess water use, and the
absence of reagent use validates the selection of LSS as the DLE for the Project. |
13.6 | Demonstration
Plant LiCl Solution Purification and Concentration |
Downstream of the DLE processes, the
LiCl solution is processed by various technologies to remove unwanted impurities (e.g., calcium, magnesium, boron and silica) and to
concentrate the purified solution by reverse osmosis processes, including brackish water reverse osmosis (BWRO) and osmotically assisted
reverse osmosis (OARO); the latter is sometimes referred to as counter-flow reverse osmosis. The Demonstration Plant has demonstrated
the ability to produce LiCl solutions suitable as feedstock for battery-quality lithium carbonate production.
84 |
 |
RSI-3353 |
Standard Lithium had multiple lab-scale
tests conducted of various technologies and for purification of the brines and concentration of the LiCl product from the DLE processes,
including ion exchange, nanofiltration, ultrafiltration, high pressure reverse osmosis, and osmotically assisted reverse osmosis prior
to selecting technology for installation in the Demonstration Plant.
The following sections describe the
test work completed on the LiCl solution purification and concentration processes.
13.7 | LiCl
Solution Concentration by Reverse Osmosis |
13.7.1 | Brackish
Water Reverse Osmosis (BWRO) |
Eluate from the LSS process (LiCl product
solution) will be concentrated using brackish water reverse osmosis (BWRO). The goal is to concentrate the LiCl and recover water (permeate)
for recycle to the process, primarily to use for LSS elution.
A BWRO system was installed in the Demonstration
Plant in January 2023. The BWRO system was tested to concentrate the LiCl solution from LSS separate from the main Demonstration
Plant process. All components in the LSS eluate product (LiCl solution) are concentrated during BWRO.
13.7.2 | Osmotically
Assisted Reverse Osmosis (OARO) |
Following the removal of calcium, magnesium,
and boron the purified LiCl solution is concentrated using Osmotically assisted Reverse Osmosis (OARO). OARO differs from BWRO in that
recirculation of effluent to the permeate side allows concentration to TDS levels as high as 180,000 mg/L compared to 60,000 mg/L in
the BWRO. The permeate has higher impurities and must be recycled to BWRO for improved impurity rejection.
An OARO system was installed in the
Demonstration Plant in August 2021 to enable a concentrated high purity LiCl solution to be produced for testing lithium carbonate
production at vendor laboratories and for use in testing Standard Lithium’s proprietary SiFT battery-quality lithium carbonate
process installed at the Demonstration Plant. The OARO system was operated at the Demonstration Plant, on a batch basis for producing
concentrated high purity LiCl solution. The OARO system has demonstrated the ability to concentrate the LiCl solution to greater than
10,000 mg/L Li, which is in excess of what is required for battery-quality lithium carbonate production processes contemplated for the
Project.
Table 13-3 below shows two examples
of the OARO concentrate that were produced using LSS eluate (LiCl) as the feed solution (post IX polishing). Trial 1 was completed in
July 2023 and Trial 2 was completed in August 2023.
85 |
 |
RSI-3353 |
Table
13-3. OARO Examples
| |
Trial 1 | | |
Trial 2 | |
| |
| Average
LiCl
Feed
Composition | | |
| Composite
Concentrate
after OARO | | |
| Average
LiCl
Feed
Composition | | |
| Composite
Concentrate
after OARO | |
Lithium (Li) | |
| 434 | | |
| 10,986 | | |
| 416 | | |
| 12,577 | |
Sodium (Na) | |
| 694 | | |
| 14,488 | | |
| 162 | | |
| 6,559 | |
Calcium (Ca) | |
| 2 | | |
| 3 | | |
| 11 | | |
| 181 | |
Magnesium (Mg) | |
| 0 | | |
| 0.6 | | |
| 16 | | |
| 115 | |
Potassium (K) | |
| 12 | | |
| 878 | | |
| 9 | | |
| 187 | |
Boron (B) | |
| 20 | | |
| 150 | | |
| 19 | | |
| 159 | |
Silica (Si) | |
| 2 | | |
| 42 | | |
| 7 | | |
| 45 | |
Figure
13-6. Osmotically Assisted Reverse Osmosis System at the Demonstration Plant
13.8 | Calcium
and Magnesium Removal Processes |
13.8.1 | Soda
Lime Softening Testing |
Soda lime softening is included in the
commercial LiCl solution purification process flow sheet for removing calcium and magnesium to reduce the reagent costs associated with
the calcium and magnesium ion exchange process. The soda ash (sodium carbonate) and lime (calcium hydroxide) chemicals used in the softening
process are significantly less expensive than the hydrochloric acid and sodium hydroxide required for the calcium and magnesium ion exchange
resin regeneration. In addition, the softening sludge produced from the softening process can be used for neutralizing the tail and Bypass
Brine received from LANXESS, reducing the amount of anhydrous ammonia required for this pre-treatment.
86 |
 |
RSI-3353 |
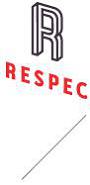
A small softening train including a
flash mixing tank, a softening reaction tank, a clarifier with rake, and systems for dosing both coagulant and flocculant was constructed
at the Demonstration Plant in March 2023 and used to treat the eluate from the LSS process.
It has been demonstrated that Ca and
Mg removal approaching 100% is achievable. However, this is not an efficient operating mode as it requires an excess of chemical reagent
addition. Additional laboratory testing is ongoing at SGS in Lakefield, Ontario to independently confirm the results and to develop design
and operating parameters to support the commercial facility. The recent results from SGS are presented below. This test work was performed
by adjusting the pH to 10.5 with hydrated lime and then adding soda ash at 100 and 110% stochiometric dosage. The simple dosing with
soda ash (even without lime) reliably reduced the calcium concentration in the eluate to below 5 mg/L. Dosing with lime and soda ash
reliably reduced the magnesium concentration in the eluate to below 5 mg/L. No coagulant or flocculant was needed to produce a relatively
clear supernatant from the softening clarifier.
Figure
13-7. Calcium Removal with Soda Ash
87 |
 |
RSI-3353 |
Note:
[1] pH increased to 10.5 with hydrated
lime prior to soda ash addition.
Figure 13-8. Magnesium Removal
with Soda Ash
88 |
 |
RSI-3353 |
13.8.2 | Calcium
and Magnesium Ion Exchange |
This is conventional technology which
has been demonstrated by Standard Lithium and its vendors. The ion exchange resin being proposed are commercially available and are routinely
used in large scale wastewater treatment for hardness removal, as seen in Figure 13-9.
Figure
13-9. Calcium and Magnesium Ion Exchange System at the Demonstration Plant
13.9 | Boron
Removal Ion Exchange |
This technology has been demonstrated
by Standard Lithium and its vendors. The ion exchange resin being proposed is commercially available and is routinely used in industry
for boron removal.
13.10 | Key
Findings from LiCl Purification and Concentration Test Work |
Key findings and outcomes from the Demonstration
Plant testing are:
| / | The
Demonstration Plant has produced polished LiCl product and has demonstrated: |
| » | LiCl
solution with Li concentration greater than 10,000 mg/L. |
| » | Rejection
of calcium, boron and magnesium to less than 1 mg/l which meets rejection targets for the
commercial process. |
89 |
 |
RSI-3353 |
| / | The
LSS eluate (raw LiCl solution) from DLE can be efficiently purified by commercially available
ion exchange (IX) resins. |
| / | Traditional
soda lime chemical softening has also been proven to work reliably down to very low levels
of both calcium and magnesium to less than 5 mg/L. For commercial operations, softening should
be used only to reduce the calcium and magnesium to 30-100 mg/L before using calcium and
magnesium IX. |
| / | Boron
has been shown to be easily removed from the concentrated LiCl solution by Standard Lithium
and third party work using OEM industry standard IX technology (< 1 mg/L). |
| / | The
final LiCl concentrate is suitable for conversion to lithium carbonate. |
13.11 | Additional
LiCl Purification and Concentration Testing |
A number of additional processes have
been tested extensively in the Demonstration Plant to evaluate the best fit technology for the Project. All of the technologies have
commercial precedent and have been shown to work at the Demonstration Plant. The key technologies that have been evaluated include:
| / | Chemical
softening using carbon dioxide instead of sodium carbonate to minimize introduction of additional
impurities. |
| / | Silica
removal by pH adjustment. |
| / | Silica
removal using a proprietary IX approach. |
| / | Silica
removal by activated alumina. |
The outcomes of testing and the learnings
from the Demonstration Plant operations, have facilitated the refinement of the process design for the Project to allow for the selection
of the appropriate process unit operations to support a robust integrated flowsheet for the commercial facility.
13.12 | Lithium
Carbonate Crystallization |
One lithium carbonate system vendor
performed two laboratory testing campaigns to demonstrate their ability to produce battery quality lithium carbonate from the Standard
Lithium LiSTR LiCl product. The first proof of concept campaign performed in February 2021 successfully produced 1 kg of battery
quality crystal lithium carbonate. The second campaign performed in October 2021 produced 3 kg of battery quality lithium carbonate
and further clarified the commercial design parameters. A third program at a second lithium carbonate vendor laboratory was completed
in June 2023 using LSS LiCl product. It produced 12kg of battery quality crystal lithium carbonate.
90 |
 |
RSI-3353 |
13.12.1 | First
Production of Lithium Carbonate |
In October 2021, the first lithium
carbonate system vendor received 250 L of LiCl product solution produced by the LiSTR DLE process. The analysis of the LiCl is shown
in Table 13-4, below.
Table 13-4
- LiCl Product Used for Lithium Carbonate Conversion – Trial 1
Cation/Anion | |
Units | | |
Concentration | |
Sodium (Na) | |
| ppm | | |
| 11800 | |
Calcium (Ca) | |
| ppm | | |
| 1344 | |
Magnesium (Mg) | |
| ppm | | |
| 245 | |
Potassium (K) | |
| ppm | | |
| 266 | |
Lithium (Li) | |
| ppm | | |
| 2628 | |
Strontium (Sr) | |
| ppm | | |
| 250 | |
Boron (B) | |
| ppm | | |
| 106 | |
Chloride (Cl) | |
| ppm | | |
| 35300 | |
Silicon (Si) | |
| ppm | | |
| 81 | |
Sulfate
(SO4) | |
| ppm | | |
| 90 | |
Barium (Ba) | |
| ppm | | |
| 14 | |
TDS | |
| ppm | | |
| 52124 | |
SG | |
| | | |
| 1.05 | |
The following describes the processes
that the vendor used for purifying the LiCl solution for production of battery-quality lithium carbonate:
| / | The
LiCl solution was initially processed by caustic and soda ash softening to remove the bulk
of the calcium, and magnesium. Softening reduced calcium to 97 ppm and magnesium to
2 ppm, which is consistent with the expected commercial values. |
| / | The
vendor then used a 4% stoichiometric excess of sodium carbonate and maintained pH at 11.5
with caustic soda. |
| / | Calcium
IX was then used to reduce calcium and magnesium to a combined level of <1ppm (CaCO3
equivalent). |
| / | Boron
Ion Exchange reduced Boron from 106 ppm to < 1ppm. |
The ion exchange test work was performed
to generate brine suitable for lithium carbonate production. The goal was not to optimize reagents, water use or column design parameters
but simply to produce solution for the crystallization work. The columns were not operated to breakthrough or exhaustion.
Following purification, the brine was
evaporatively concentrated to increase the lithium concentration and simultaneously crystallize sodium chloride. The crystallization
of sodium chloride is not included in the current standard lithium carbonate flowsheet. Instead, concentrated brine from the OARO process
will be delivered to the Lithium Carbonate Plant.
Lithium carbonate was produced in a
two-stage process. In the 1st stage, lithium chloride was reacted with 25% sodium carbonate solution to crystallize crude
lithium carbonate. The sodium carbonate used in the treatment was commercially available technical grade which contained about 100 ppm
equivalent calcium and magnesium. The calcium and magnesium almost quantitatively reported to the 1st stage crystals. The
crystals were coarse 200-300 microns in size and were mainly agglomerated. Washing could only remove a portion of the impurities.
91 |
 |
RSI-3353 |
The crude 1st stage crystals
were repulped in water and then carbonated to produce soluble lithium bicarbonate. Following filtration, the lithium bicarbonate solution
was filtered, and then subjected to Ion Exchange to reduce the brine to < 1ppm calcium equivalent.
The lithium bicarbonate was thermally
decomposed to release carbon dioxide and crystallize purified lithium carbonate. The carbon dioxide that is released would be recycled
in the commercial plant.
The 2nd stage or purified
crystals were mainly singular crystals, 200-300 µm in length with an aspect ratio (length to width) of approximately 10. The photograph
of the 2nd stage crystals shown in Figure 13-10, below, were de-watered, washed, analyzed, and confirmed to meet battery quality
specification. See Table 13-5, below, comparing typical battery quality lithium carbonate specifications with laboratory-produced lithium
carbonate made from Standard Lithium LiCl product solution. The vendor produced approximately 1 kg of battery quality lithium carbonate
crystals during their laboratory testing.
Table 13-5
–Lithium Carbonate Product – Trial 1
Element | |
Analysis
Method | |
Typical
Specification1 | | |
Units | | |
Standard
Lithium Li2CO3
Sample
Produced | |
Sodium (Na) | |
AA | |
| <500 | | |
| ppm | | |
| 13 | |
Potassium (K) | |
AA | |
| <10 | | |
| ppm | | |
| <10 | |
Calcium (Ca) | |
AA | |
| <100 | | |
| ppm | | |
| <10 | |
Magnesium (Mg) | |
AA | |
| <60 | | |
| ppm | | |
| <10 | |
Iron (Fe) | |
ICP | |
| <10 | | |
| ppm | | |
| <1 | |
Manganese (Mn) | |
ICP | |
| -- | | |
| ppm | | |
| <1 | |
Copper (Cu) | |
ICP | |
| <10 | | |
| ppm | | |
| <1 | |
Nickel (Ni) | |
ICP | |
| <10 | | |
| ppm | | |
| <1 | |
Zinc (Zn) | |
ICP | |
| <10 | | |
| ppm | | |
| <1 | |
Sulfate (SO4) | |
ICP | |
| <300 | | |
| ppm | | |
| <30 | |
Boron (B) | |
ICP | |
| <10 | | |
| ppm | | |
| <1 | |
Aluminum (Al) | |
ICP | |
| <10 | | |
| ppm | | |
| <3 | |
Lead (Pb) | |
ICP | |
| <10 | | |
| ppm | | |
| <1 | |
Chromium (Cr) | |
ICP | |
| <10 | | |
| ppm | | |
| <1 | |
Chloride (Cl) | |
Titration | |
| <100 | | |
| ppm | | |
| <50 | |
Notes:
[1] Typical specification listed is
based on industry standards for reference only.
92 |
 |
RSI-3353 |
Figure
13-10. Photo of 2nd Stage Lithium Carbonate Crystals
13.12.2 | Second
Production of Lithium Carbonate |
In October 2021, the first lithium
carbonate system vendor received 350 L of LiCl solution produced by the LiSTR process after RO concentration and Strong Acid Cation IX
to remove calcium, and magnesium. The analysis of the brine is shown in Table 13-6 below.
Table 13-6
- LiCl Product Used for Lithium Carbonate Conversion – Trial 2
Cation/Anion | |
Units | | |
Concentration | |
Sodium (Na) | |
| ppm | | |
| 18800 | |
Calcium (Ca) | |
| ppm | | |
| <1 | |
Magnesium (Mg) | |
| ppm | | |
| <1 | |
Potassium (K) | |
| ppm | | |
| 122 | |
Lithium (Li) | |
| ppm | | |
| 5500 | |
Strontium (Sr) | |
| ppm | | |
| <1 | |
Boron (B) | |
| ppm | | |
| 292 | |
Chloride (Cl) | |
| ppm | | |
| 58600 | |
Silicon (Si) | |
| ppm | | |
| 48 | |
Sulfate
(SO4) | |
| ppm | | |
| 30 | |
Barium (Ba) | |
| ppm | | |
| <1 | |
TDS | |
| ppm | | |
| 83400 | |
SG | |
| - | | |
| 1.05 | |
Boron IX reduced boron in the LiCl solution
from 292 ppm to < 1ppm. The ion exchange test work was performed to generate a LiCl solution suitable for lithium carbonate production.
Again, the goal was to produce solution for crystallization not to evaluate the purification processes.
Following purification, the LiCl solution
was evaporatively concentrated to increase the lithium concentration and simultaneously crystallize out sodium chloride. The evaporation
was performed continuously over a 14-day period using two 22-L bench scale evaporators. Lithium was concentrated to 24% by weight of
lithium chloride. The crystallization of sodium chloride is not included in the current standard lithium carbonate flowsheet.
93 |
 |
RSI-3353 |
Lithium carbonate was produced in a
two-stage process. The campaign was conducted over one week. In the 1st stage, lithium chloride was reacted with 30% sodium
carbonate solution to crystallize crude lithium carbonate at 95°C. The sodium carbonate used in the treatment was commercially available
technical grade which contained about 100 ppm equivalent calcium and magnesium. Most of the calcium and magnesium from the sodium carbonated
ended up in the 1st stage crude lithium carbonate crystals.
The 1st stage crystals were
coarse 200-300 µm and mainly agglomerated. See Figure 13-11, below. Washing could only remove a portion of the impurities.
The crude 1st stage crystals
were repulped in water and then carbonated to produce soluble lithium bicarbonate. Following filtration, the lithium carbonate brine
was filtered, and then again subjected to Ion Exchange to reduce the brine to < 1ppm calcium equivalent. The column flux rate was
15 BV/h. The lithium carbonate was thermally decomposed to release carbon dioxide, which would be recycled in the commercial plant, and
purified lithium carbonate crystallized. The 2nd stage crystals were mainly singular, 200-300 microns in length, with an aspect
ratio (length to width) of approximately 10. See Figure 13-12, below. The crystals picture in Figure 13-12, below, were de-watered, washed,
analyzed, and confirmed to meet battery quality specification. Approximately 3 kg of battery quality crystals were produced during the
laboratory testing campaign. Refer to Table 13-7 below for the lithium carbonate sample analysis produced.
Table 13-7
- Lithium Carbonate Product – Trial 2
Element | |
Analysis
Method | |
| Typical
Specification | | |
| Units | | |
Standard
Lithium
Li2CO3
Sample Produced |
Sodium (Na) | |
AA | |
| <500 | | |
| ppm | | |
<15 |
Potassium (K) | |
AA | |
| <10 | | |
| ppm | | |
<10 |
Calcium (Ca) | |
AA | |
| <100 | | |
| ppm | | |
<10 |
Magnesium (Mg) | |
AA | |
| <60 | | |
| ppm | | |
<10 |
Iron (Fe) | |
ICP | |
| <10 | | |
| ppm | | |
<1 |
Manganese (Mn) | |
ICP | |
| -- | | |
| ppm | | |
<1 |
Copper (Cu) | |
ICP | |
| <10 | | |
| ppm | | |
<1 |
Nickel (Ni) | |
ICP | |
| <10 | | |
| ppm | | |
<1 |
Zinc (Zn) | |
ICP | |
| <10 | | |
| ppm | | |
<1 |
Sulfate
(SO4) | |
ICP | |
| <300 | | |
| ppm | | |
<100 |
Boron (B) | |
ICP | |
| <10 | | |
| ppm | | |
<1 |
Aluminum (Al) | |
ICP | |
| <10 | | |
| ppm | | |
<5 |
Lead (Pb) | |
ICP | |
| <10 | | |
| ppm | | |
<1 |
Chromium (Cr) | |
ICP | |
| <10 | | |
| ppm | | |
<1 |
Chloride (Cl) | |
Titration | |
| <100 | | |
| ppm | | |
<100 |
Silicon (Si) | |
ICP | |
| -- | | |
| ppm | | |
<12 |
Notes:
[1] Typical specification
listed is based on industry standards for reference only.
94 |
 |
RSI-3353 |
Figure
13-11. Photo of 1st Stage Lithium Carbonate Crystals
Figure
13-12. Photo of 2nd Stage Lithium Carbonate Crystals
13.12.3 | Third
Production of Lithium Carbonate |
In June 2023, a second lithium
carbonate system vendor received 2800 L of LiCl solution produced by the LSS process and subsequently purified and concentrated in the
Demonstration Plant. The LiCl eluate solution was treated to remove calcium and magnesium using strong acid cationic (SAC) IX followed
by weak acid cationic (WAC) IX. The purified solution was next concentrated using OARO and then treated for boron removal using boron
IX and finally treated one more time using WAC IX. The analysis of the brine is shown in Table 13-8 below.
95 |
 |
RSI-3353 |
Table
13-8. LiCl Product Used for Lithium Carbonate Conversion – Trial 3
Cation/Anion | |
Units | | |
Concentration | |
Sodium (Na) | |
| mg/L | | |
| 52083 | |
Calcium (Ca) | |
| mg/L | | |
| 2.6 | |
Magnesium (Mg) | |
| mg/L | | |
| 1.4 | |
Potassium (K) | |
| mg/L | | |
| 1260 | |
Lithium (Li) | |
| mg/L | | |
| 7703 | |
Boron (B) | |
| mg/L | | |
| 2.2 | |
Chloride (Cl) | |
| mg/L | | |
| 119600 | |
Silicon
(SiO2) | |
| mg/L | | |
| 21.4 | |
Sulfate
(SO4) | |
| mg/L | | |
| 145 | |
Ammonia
(NH3) | |
| mg/L | | |
| 15 | |
Bromine (Br) | |
| mg/L | | |
| 304 | |
TDS | |
| mg/L | | |
| 180000 | |
SG | |
| | | |
| 1.1 | |
The test program simulated reactive
crystallization of Li2CO3 through addition of soda ash to the OARO concentrated DLE eluate feed. The soda ash was
provided by Standard Lithium to match the impurity profile expected during commercial operation. A thickening system was used to increase
the slurry density in the crude crystallizer to match the commercial design. At periodic intervals, a centrifuge was used to separate
the crude Li2CO3 crystals from the mother liquor (ML). The resulting Li2CO3 cake was then
washed with mother liquor from the refined crystallizer to reduce impurities contained in the residual moisture on the crystal surface.
The dewatered and washed crude crystals
were repulped in recycle ML from the refined crystallizer. Distillate was added to satisfy the material balance. CO2 was then
sparged through this solution to convert the suspended Li2CO3 crystals to soluble LiHCO3. The resulting
solution was filtered through a cloth filter and processed through a chelating ion exchange to remove multivalent cations.
The purified LiHCO3 solution
was then fed to the refined crystallizer, where thermal decomposition released CO2 from the solution, leading to the precipitation
of Li2CO3. A thickening system was used to increase the slurry density in the refined crystallizer to match the
commercial design. At periodic intervals, a centrifuge was used to separate the refined Li2CO3 crystals from the
mother liquor. The resulting Li2CO3 cake was then washed with distilled water to reduce impurities contained in
the residual moisture on the crystal surface.
96 |
 |
RSI-3353 |
See Table 13-9 below comparing typical
battery quality lithium carbonate specifications with laboratory-produced lithium carbonate made from Standard Lithium LiCl product solution.
The vendor produced approximately 12 kg of battery quality lithium carbonate crystals during their pilot testing.
Table 13-9.
Lithium Carbonate Product – Trial 3
Element | |
Analysis
Method | |
| Typical
Specification | | |
| Units | | |
Standard
Lithium Li2CO3
Sample Produced |
Sodium (Na) | |
ICP-OES | |
| <500 | | |
| ppm | | |
<12 |
Potassium (K) | |
ICP-OES | |
| <10 | | |
| ppm | | |
<0.3 |
Calcium (Ca) | |
ICP-OES | |
| <100 | | |
| ppm | | |
<25 |
Magnesium (Mg) | |
ICP-OES | |
| <60 | | |
| ppm | | |
<4 |
Iron (Fe) | |
ICP-OES | |
| <10 | | |
| ppm | | |
<2 |
Manganese (Mn) | |
ICP-OES | |
| -- | | |
| ppm | | |
<0.3 |
Copper (Cu) | |
ICP-OES | |
| <10 | | |
| ppm | | |
<0.1 |
Nickel (Ni) | |
ICP-OES | |
| <10 | | |
| ppm | | |
<0.3 |
Zinc (Zn) | |
ICP-OES | |
| <10 | | |
| ppm | | |
<2 |
Sulfate (SO4) | |
ICP-OES | |
| <300 | | |
| ppm | | |
<50 |
Boron (B) | |
ICP-OES | |
| <10 | | |
| ppm | | |
<0.2 |
Aluminum (Al) | |
ICP-OES | |
| <10 | | |
| ppm | | |
<2 |
Lead (Pb) | |
ICP-OES | |
| <10 | | |
| ppm | | |
<0.3 |
Chromium (Cr) | |
ICP-OES | |
| <10 | | |
| ppm | | |
<0.4 |
Chloride (Cl) | |
Pyrohydrolysis then IC | |
| <100 | | |
| ppm | | |
<25 |
Silicon (Si) | |
ICP-OES | |
| -- | | |
| ppm | | |
<10 |
13.12.4 | Key
Findings from Lithium Carbonate Crystallization Test Work |
| / | Pilot
testing of the complete lithium carbonate crystallization process flowsheet including all
unit operations has demonstrated commercial suitability |
| / | Testing
confirmed battery-quality lithium carbonate can be produced meeting the required impurity
specifications for the Project using LiCl produced from the Demonstration Plant from the
same brine which will be processed by the Project |
| / | Produced
representative refined crystals that were measured to be crystalline Li2CO3
with >99.98% purity excluding moisture as calculated by sum of impurities |
13.13 | Process
Testing QA/QC |
During the operation of the Demonstration
Plant, routine daily chemical analysis is conducted in the internal laboratory using standard solution analysis instrumental techniques;
principally, Inductively Coupled Plasma – Optical Emission Spectroscopy (ICP-OES). For more important determinations, duplicate
samples are submitted to SGS Canada Inc. (SGS) for analysis using their standard ISO 9000 compliant protocols (principally ICP-OES),
developed based on their experience working on numerous lithium projects. Additional brine and solid samples are also periodically sent
to other third-party analytical laboratories (principally Wetlabs) in order to provide suitable independent verification of data generated
by the Demonstration Plant.
Other instrumentation in the Demonstration
Plant undergoes a rigorous maintenance schedule to ensure accurate collection of data from the plant.
97 |
 |
RSI-3353 |
13.14 | Process
Technical Risks and Mitigation Measures |
Similar to all lithium brine processing
projects (including those using ‘conventional’ evaporation ponds), there are risks that need to be addressed or resolved
as the Project moves through the usual development stages:
| / | Effect
of varying feed composition on lithium selectivity. The Demonstration Plant has been operated
with the South Plant brine feed and as such little variation is expected. Extensive testing
has been completed to characterize the brine. In addition, variations in Feed Brine will
be commercially limited by commercial agreements which set out minimum brine quality requirements
for the delivery of Feed Brine to the facility by LANXESS. |
| / | Process
Scalability. The pre-treatment technology used on the Tail Brine and Bypass Brine supplied
from the LANXESS South Plant to prepare it for the LSS DLE process is industry standard technology.
The LSS DLE process has now been operated continuously for approximately 12 months at a pre-commercial
Demonstration Plant scale and has been developed to FEED (DFS) level in support of the Commercial
Lithium Extraction Plant Project. It is believed that all operations comprising the DLE process
can be reasonably scaled-up. Scale-up will occur by the addition of multiple standard size
LSS columns operating in parallel. The same fluid velocities and step bed volumes will be
maintained in the commercial design. Scale up from the Demonstration Plant to the Commercial
Lithium Extraction Plant Project will be about 60:1. The purification, concentration, and
crystallization unit operations of the flowsheet are all commercially demonstrated. Similarly,
the lithium carbonate drying, micronizing, product handling, and packaging equipment are
commercial processes, and are not deemed to be areas of risk. |
13.15 | Conclusions
and Recommendations |
Standard Lithium has completed substantial
test work at the Demonstration Plant and in external laboratories. Most aspects of the proposed flowsheet for the Project are commercially
available industrial processes and have been demonstrated at substantial pre-commercial scale, or have been verified by pilot scale work
on similar solutions. As such, the author feels that the test work completed supports the feasibility of the flowsheet proposed for the
Project to use for commercial development, subject to the successful conclusion of additional on-going test work.
Recommendations are:
| / | Continue
to operate and collect data from the existing Demonstration Plant. |
| / | Continue
to test alternative filtration technologies and optimize brine filtration by varying the
media and incoming brine temperature, pH, and ORP to optimize capital and operating costs. |
| / | Continue
to optimize the LSS DLE to improve the quality of the Raw LiCl by elimination of impurities,
including testing of alternative resins and adjustments to operating parameters to support
future commercial operations. |
| / | Undertake
continuous brine neutralization using softening sludge for commercial process optimization. |
98 |
 |
RSI-3353 |
14.0 | Mineral
Resources Estimates |
This section describes the preparation
of the Lithium Resource brine estimate for the three Units that make up the Property obtained from the simulation model results. These
estimates are based on the volume of porous rock as described in the geologic model and the estimated lithium concentrations present
in the brines stored within the formation on the Property as of the effective date of August 18, 2023.
A portion of the resource estimates
have been upgraded from the Indicated category, PEA (Worley 2019), to the Measured category based on the extensive geologic data and
lithium concentration data, combined with consideration of the 65-year history of brine recovery from the Property. This information
demonstrates the proven capability of the existing field operations to effectively displace and recover brine from this Smackover reservoir.
This upgrading of the resource estimates is described in more detail in Section 14.4.
This resource estimate has been prepared
is in accordance with the CIM Definition Standards for Mineral Resources and Mineral Reserves (CIM, 2014).
Mineral Resources are sub-divided, in
order of increasing geological confidence, into inferred, indicated and measured categories. An Inferred Mineral Resource has a lower
level of confidence than that applied to an Indicated Mineral Resource. An Indicated Mineral Resource has a higher level of confidence
than an Inferred Mineral Resource but has a lower level of confidence than a Measured Mineral Resource.
An Inferred Mineral Resource
is that part of a Mineral Resource for which quantity and grade or quality are estimated on the basis of limited geological evidence
and sampling. Geological evidence is sufficient to imply but not verify geological and grade or quality continuity.
An Indicated Mineral Resource
is that part of a Mineral Resource for which quantity, grade or quality, densities, shape and physical characteristics are estimated
with sufficient confidence to allow the application of Modifying Factors in sufficient detail to support mine planning and evaluation
of the economic viability of the deposit.
A Measured Mineral Resource
is that part of a Mineral Resource for which quantity, grade or quality, densities, shape, and physical characteristics are estimated
with confidence sufficient to allow the application of Modifying Factors to support detailed mine planning and final evaluation of the
economic viability of the deposit.
The estimation of resources and reserves
in this report have been carried out in conformance with NI 43-101 and have been estimated using the CIM Definition Standards for Mineral
Resources and Mineral Reserves, as amended and adopted (CIM, 2014), and CIM Best Practice Guidelines for Resource and Reserve Estimation
for Lithium Brine (CIM, 2012).
99 |
 |
RSI-3353 |
The Best Practice Guidelines (CIM, 2012)
have been adapted for the specific conditions present at this Property. Unlike a brine-bearing salar, the Property’s brine accumulation
exists in a well-defined porous geologic formation at depth, the Smackover. This brine accumulation is bounded vertically by impermeable
formations and laterally by changes in lithium concentration to the north and formation geologic properties to the south. The Property
area itself is determined by the West, Central, and South Unit property boundaries. Also unlike a salar, the brine recovery from the
Smackover is the result of rich brine displacement by injected lean brine. This brine-on-brine displacement mechanism is efficient, with
all of the lithium-bearing brine in a given reservoir volume contacted by the injected brine displaced. For this reason, the Guidelines’
use of Specific Yield for estimating resources, which assumes some remaining content of lithium in the subject formation, has been replaced
here with the Effective Porosity of the formation. The estimation of the fraction of the resources that will be recovered by the Project
(the recovery factor, equal to the estimated reserves divided by the estimated resource for the Project area) is done using reservoir
simulation. Simulation accounts for the key reservoir properties (lithium concentration, porosity, and permeability) and for the specific
Project development activities, including time limits applied to those activities. The recovery factor is not pre-determined at the resource
estimation step.
This approach to the estimation of both
resources and reserves using a detailed geologic model as the basis for the reservoir simulation model fully captures all factors and
mechanisms that affect the content and recovery of brine and the associated lithium from this porous underground formation.
14.1 | Geologic
Model Description |
The geologic characteristics of the
reservoir and its productivity have been proven by the 65-year development history of bromine extraction by LANXESS and its predecessors.
All this data and historical production information provides the basis upon which to estimate the resource and plan this lithium extraction
Project.
A geologic multi-zone
model of the Property was constructed using Petra that serves the basis of the brine body simulation model. The geologic mapping covered
the Property and the surrounding area [Geologic Study Area] (Figure 7-1). The following steps were carried out to construct the geologic
multi-zone model:
| 1. | The
Smackover was divided into six zones called Oolites 1 through 6, based on their distinct
geologic characteristics. These divisions are identified in the well type log, Figure 14-1. |
| 2. | The
zone picks were made on each well log. |
| 3. | Each
porosity well log was evaluated to determine each zone’s gross thickness, net pay thickness
(which represents the productive thickness of the zone considering a minimum porosity cutoff
of nine percent), average porosity for that net pay interval, and the ratio of net pay thickness
to gross thickness. |
| 4. | An
example of this process is shown in Figure 14-2. The zone picks result in the gross pay values,
the application of the nine percent porosity cutoff results in the net pay values, the ratio
of those two values provides the net to gross ratio, and the average porosity over each oolite
zone’s net pay intervals results in the average porosity of the net pay for that Oolite
zone. |
100 |
 |
RSI-3353 |
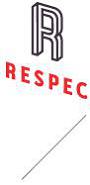
| 5. | Each
well’s geologic data (location, top of Smackover depths picks, along with the by-zone
gross thickness, net to gross ratio, and porosity data) were imported into Petra® Software. |
| 6. | A
500 ft by 500 ft (152.4 m by 152.4 m) grid was established, and the well geologic data was
contoured using two Petra gridding options: |
| a. | The
Highly Connected Features option utilizes a least-squares gridding algorithm that
is well-suited to both structure maps and the smoothly changing petrophysical data present
here. The “grid flexing” option, appropriate for this type of well-behaved data,
was used to regularize the maps’ contour lines. |
| b. | The
Directional Bias option was used, with a direction of 120 degrees. This directional
bias was applied to capture the regional direction of strike of the Smackover Formation,
corresponding to the orientation of the oolite bars as they were deposited. |
| 7. | Following
the gridding and contouring process, bounding limits were applied to the gross thickness,
porosity, and net thickness to gross thickness ratio grids. The gross thickness and the porosity
grids were constrained to between 95% of the minimum observed value and 105% of the maximum
observed value to prevent the mapping algorithm from extrapolating to unreasonable values.
Similarly, the net thickness to gross thickness ratio grids were limited between 0 and 1,
corresponding to the physical limits of that ratio. |
| 8. | The
resulting zone grids for structure, porosity, gross pay, and net pay were then exported from
Petra and loaded into the simulation model. |
101 |
 |
RSI-3353 |
Figure 9-1 depicts the locations of
wells containing structure, porosity, or core data relevant to the description of one or more of the six zones. In addition to calibrating
the porosity well log data, the core data was used to establish correlation equations between permeability and porosity data. A total
of 2187 core samples were analyzed. These relationships were then used to estimate the permeability values of each model layer based
on their respective porosity values. Figure 7-2 presents the structure map for the top of the Smackover Formation, and Figure 14-1 presents
the total gross pay for the six zones resulting from the analysis described above.
Figure
14-1. LANXESS Property Smackover Type Well
Figure
14-2. Porosity Log Net Pay Example
102 |
 |
RSI-3353 |
Figure
14-3. Total Gross Pay Map Zones 1-6
14.2 | Simulation
Model Description |
A simulation model, based on the layered
geologic description, was used to estimate the resources present in each of the three Units. Simulation was required to estimate the
resources as of August 18, 2023, because the ongoing bromine recovery process, while not altering the overall lithium content of
the Property, has moved the lithium location as a result of the production and injection of brine.
The Merlin finite-difference reservoir
simulation model, an industry-standard simulation model created by Gemini Solutions, Inc., was used to model brine content, brine
movement, bromine recovery, and lithium recovery. The Merlin model has the capability of tracking two types of water: water without tracer
and water with tracer, in varying relative combinations. That capability was adapted to track the injected lean brine (with either bromine
or lithium removed) and original rich brine (for either bromine or for lithium). The physical process being modeled, the displacement
of rich brine by lean brine, is identical for both bromine and lithium brines.
The model grid is shown in Figure 14-4.
The by-zone geologic model maps, gridded on a 152.4 m spacing, were loaded into the model and re-gridded to conform to the model’s
grid architecture. The model covers an area of approximately 48.3 km by 33.8 km. The grid dimensions are 120 cells in the east-west direction
by 84 cells in the north-south direction, resulting in each 402.3 m by 402.3 m cell covering approximately 40 acres (16.2 hectares).
There are 14 model layers, resulting in 141,120 model cells. Eight model layers were added to the six geologic zones by subdividing each
of the four highly permeable geologic zones (oolites 1, 3, 5, and 6) into three layers. Based on the core permeability and porosity data,
either a low, medium, or high permeability as a function of porosity equation was applied to that oolite zones’ porosity data.
This technique better captures the permeability heterogeneity present in the Smackover Formation and its impact on brine movement.
103 |
 |
RSI-3353 |
Model parameters including average horizontal
permeability, gross rock volume, average net-to-gross ratio, net rock volume, average porosity, and brine volume, were quantified on
a Unit-by-Unit basis. These values are presented in Table 14-1.
The model was calibrated by achieving
a historical match between field and model injection and production well rates and production well bromine concentrations over the life
of the bromine recovery project. This history-matched and calibrated model was then converted to track the movement and production of
lithium-containing brine, including the reinjection of the brine stripped of lithium once the Project is implemented.
The model was initialized with the estimated
initial lithium concentration map, Figure 9-3. The model then tracked the movement of lithium-bearing brine in the reservoir during the
history of the Property. While no lithium was removed during this period, the produced brine, with its lithium concentration varying
by location, was combined at each Unit’s processing facility. As a result, each Units’ injected lithium concentration was
based on the volume-weighted average produced lithium concentration for that Unit. Therefore, during this period (up to the start of
the Project), the total lithium content of each Unit did not change significantly, but the distribution of lithium within each Unit did
change. These changes were tracked by the varying lithium concentrations in the model cells.
Following Project startup, the future
recovery of lithium from the South Unit was modeled by specifying the injection and production rates, with the injected brine lithium
concentration reflecting the removal of lithium from the process stream by the Project. This report’s estimated lithium recovery
values are based on the model’s produced volumes and associated lithium concentrations, which were then subjected to the appropriate
recovery factors, as described in Section 16.
The simulation model’s ability
to match the observed field performance (injection rates, production rates, bromine concentrations, and lithium concentrations) provides
confidence in its forecasts for lithium production rates and the resulting Resource estimates. The model-simulated average produced lithium
concentrations from the three Units, corresponding to each Unit’s plant inlet lithium concentrations, were found to closely match
the measured plant inlet lithium concentrations, as obtained by Standard lithium, as shown in Figure 14-5. This accuracy in matching
the field rate and concentration data extends to the match of individual wells. Figure 14-5 depicts the matches achieved for the six
South Unit wells that will be produced as part of the Project. In QP Brush’s opinion this accurate history match confirms the suitability
of the simulation model for use in estimating the lithium resources.
104 |
 |
RSI-3353 |
Figure
14-4. Simulation Model Grid Layout
105 |
 |
RSI-3353 |
Figure
14-5. Simulation Model Match of Unit Produced Lithium Concentration Data
106 |
 |
RSI-3353 |
107 |
 |
RSI-3353 |
Figure
14-6. Simulation Model Match of South Unit Well Produced Lithium Concentration Data
108 |
 |
RSI-3353 |
14.3 | Lithium
Resource Estimate |
To estimate the in-place lithium Resource
effective August 18, 2023, the simulation model was used instead of the layered geologic model, because the bromine production activities
over the Property history moved the lithium around within each Unit. The lithium content was calculated by multiplying the brine volume
for each of the simulation model’s cells by the lithium concentration on that date for that cell. The resulting values were then
summed over each Unit. Any cell in more than one Unit was allocated between the Units, as were cells straddling the outer boundaries
of the Units. The estimated properties for each Unit are listed in Table 14-1. The resulting estimated average lithium concentration
and in-place estimated Lithium Mineral Resource value for each of the three Units as of August 18, 2023, are presented in Table
14-2.
Table 14-1.
Estimated Unit Properties Resulting from Finite Difference Modeling
Estimate | |
Units | | |
West Unit | | |
Central
Unit | | |
Central
Unit
Expansion | | |
South Unit | | |
Total/Average | |
Average Horizontal Permeability | |
| Md | | |
| 85 | | |
| 91 | | |
| 91 | | |
| 88 | | |
| 88 | |
Gross Rock Volume | |
| 106
m3 | | |
| 32,800 | | |
| 24,000 | | |
| 3,900 | | |
| 20,800 | | |
| 81,500 | |
Average Net to Gross Ratio | |
| % | | |
| 34.1 | | |
| 30.8 | | |
| 36.6 | | |
| 24.3 | | |
| 30.8 | |
Net Rock Volume | |
| 106
m3 | | |
| 11,200 | | |
| 7,400 | | |
| 1,400 | | |
| 5,100 | | |
| 25,100 | |
Average Porosity | |
| % | | |
| 14.1 | | |
| 14.2 | | |
| 14.3 | | |
| 14.4 | | |
| 14.2 | |
The resulting estimated average lithium
concentration and in-place estimated Measured and Indicated Estimated Lithium Resource value for each of the three Units (including the
Central Unit Expansion) as of August 18, 2023, are presented in Table 14-2. The Estimated Lithium Resources are presented in tonnes
of elemental lithium. The 529,000 tonnes of total Measured plus Indicated elemental lithium resources corresponds to approximately 2,820,000
tonnes of LCE, using a conversion factor of 5.323.
109 |
 |
RSI-3353 |
Table 14-2.
Statement of Resources In-Place by Unit effective date, August 18, 2023
| |
Units | |
South | | |
West | | |
Central | | |
Central
Expansion | | |
Total | |
Gross
Volume [1] | |
km³ | |
| 20.8 | | |
| 32.8 | | |
| 24 | | |
| 3.9 | | |
| 81.5 | |
Net
Volume [1] | |
km³ | |
| 5.1 | | |
| 11.2 | | |
| 7.4 | | |
| 1.4 | | |
| 25.1 | |
Average
Porosity [2] | |
% | |
| 14.4 | | |
| 14.1 | | |
| 14.2 | | |
| 14.3 | | |
| 14.2 | |
Brine
Volume [8] | |
km3 | |
| 0.73 | | |
| 1.58 | | |
| 1.05 | | |
| 0.2 | | |
| 3.56 | |
Average Lithium Concentration | |
mg/L | |
| 204 | | |
| 122 | | |
| 164 | | |
| 78 | | |
| 148 | |
Measured Resource | |
thousand tonnes | |
| 148 | | |
| 192 | | |
| 173 | | |
| - | | |
| 513 | |
Indicated Resource | |
thousand tonnes | |
| - | | |
| - | | |
| - | | |
| 16 | | |
| 16 | |
Measured
LCE Resource [9] | |
thousand tonnes | |
| 788 | | |
| 1,022 | | |
| 921 | | |
| - | | |
| 2,731 | |
Indicated
LCE Resource [9] | |
thousand tonnes | |
| - | | |
| - | | |
| - | | |
| 85 | | |
| 85 | |
Notes:
[1] Volumes are in-place.
[2] Cutoff of 9% porosity.
[3] The effective
date of the resource estimate is August 18, 2023
[4] Mineral Resources
are inclusive of Mineral Reserves.
[5] The Qualified
Persons for the Mineral Resource Estimates is Randal M. Brush, PE and Robert E. Willliams, Jr., PG, CPG.
[6] The Mineral Resource
estimate follows 2014 CIM Definition Standards and the 2019 CIM MRMR Best Practice Guidelines.
[7] These Mineral
Resources are not Mineral Reserves as they do not have demonstrated economic viability.
[8] Calculated brine
volumes only include Measured and Indicated Mineral Resource volumes that when blended from the well field result in feed above the cut-off
grade of 100 mg/L.
[9] Lithium Carbonate
Equivalent (“LCE”) is calculated using mass of LCE = 5.323 multiplied by mass of lithium metal.
[10] Results are presented
in-situ. The number of tonnes was rounded to the nearest thousand. Any discrepancies in the totals are due to rounding effects.
[11] The Qualified
Person is not aware of any known environmental, permitting, legal, title-related, taxation, socio-political or market issues, or any
other relevant issue that could materially affect the potential development of Mineral Resources other than those discussed in the Mineral
Resource Estimates.
110 |
 |
RSI-3353 |
14.4 | Qualified
Person Discussion |
The simulation model was run to track
changes in lithium concentrations over the entire Property history and was found to closely match the current produced lithium concentrations,
indicating the model is well calibrated. Therefore, this simulation model is appropriate to use in modeling both the historic movement
of lithium in the field and in estimating the future production of lithium from the Project’s brine source wells.
The Indicated Resources associated with
the three Units evaluated in the PEA (Worley, 2019) have been reclassified in this report as Measured Resources. This reclassification
is based on the following observations:
| / | The
multi-zone geologic description incorporates the available well log and core data and describes
the variation in reservoir properties over each of the three Units. This data covers the
entire vertical and horizontal extent of the reservoir within the Units that has been developed,
and there is not a significant undeveloped target within the three Units. |
| / | The
Smackover has demonstrated sufficient permeability and thickness throughout the three Units
to permit 55,600 to 87,400 m3 per day (350,000 to 550,000 barrels per day) of
production and matching injection of brine (total Property throughput) over the last 30 years. |
| / | The
reservoir simulation model based on that geologic description has been confirmed as reasonable
by the match to Property production data achieved by the model, which has been history matched
to 60+ years of bromine brine production and injection activities. |
| / | The
simulation model has also been confirmed as reasonable by the match of model-estimated lithium
concentrations to recently collected plant inlet lithium concentration data. |
| / | The
lithium concentration data and the lean brine breakthrough data allow for the accurate mapping
of the spatially varying original lithium concentration values, a significant increase in
accuracy over the application of an average lithium concentration field wide. This map enables
the modeling of the 60+ years of injection and production performance to estimate the current
distribution of lithium within the three Units. |
| / | The
recognition of the high levels of geologic continuity between injection and production wells
in those formations, as demonstrated by the 60+ years of bromine-rich brine displacement
by lean processed brine. This lean brine breakthrough behavior is matched by the simulation
model, which incorporates 100 percent continuity of the net pay in its geologic layers. |
| / | In
summary, all three Units have been fully developed over the last 60+ years for bromine production,
providing geologic and engineering data to fully describe their lithium content. The addition
of lithium recovery to the field takes full advantage of the information gathered by the
existing bromine recovery project. |
The lithium resources associated with
the recently approved approximate 6,560-acre (2,654.7-hectare) expansion to the Central Unit (Arkansas Oil & Gas Commission
Order Number 095-2022-12, January 5, 2023) have been classified as Indicated Resources, based on this area’s location in close
proximity to existing wells in the West Unit and Central Unit. As with the PEA (Worley 2019), there are no Inferred Resources.
111 |
 |
RSI-3353 |
A minimum lithium concentration cutoff
of 100 mg/L was applied as part of the Indicated and Measured Resource estimation procedure. Because the ongoing bromine recovery process
results in all of each Unit’s lithium-bearing formation contributing to the produced brines from the brine source wells, the cutoff
did not impact the resource estimation. The brine from these wells is mixed at each Unit’s central plant. The option to selectively
produce certain parts of the geologic formation does not exist because the wells produce from and inject into all the permeable parts
of the formation, regardless of lithium concentration. As a result, all in-place brine subject to injection and production will be subject
to the lithium recovery process. Therefore, the entirety of each Unit is part of that Unit’s lithium resource, regardless of its
current lithium concentration.
Geological evidence is derived from
detailed and reliable exploration, sampling and testing and is sufficient to confirm geological and grade or quality continuity between
points of observation. In this case, the geologic and physical characteristics of the lithium accumulation have been fully analyzed,
and the resulting description is suitable for detailed Project planning. Any revisions to the geologic and physical descriptions prior
to Project implementation would result from additional lithium sampling at the same locations as previously sampled, which could produce
minor changes in the estimated lithium concentration map. As of the date of this report no additional wells are planned to be drilled
in the West and Central Units.
In addition to the technical
and economic advantages of implementing the Project at an ongoing brine recovery facility, the uncertainties associated with permitting,
environmental, legal, title, and other social and political issues are expected to be greatly reduced or eliminated because the Project
is supported by the Property’s existing long-term bromine recovery operations.
112 |
 |
RSI-3353 |
| 15.0 | Mineral
Reserve Estimates |
This Report presents the estimate of
Probable and Proven Mineral Reserves, consistent with the CIM Definitions (CIM, 2014), which state:
/ A
Mineral Reserve is the economically mineable part of a Measured and/or Indicated Mineral Resource. It includes diluting materials
and allowances for losses, which may occur when the material is mined or extracted and is defined by studies at Pre-Feasibility or Feasibility
level as appropriate that include application of Modifying Factors. Such studies demonstrate that, at the time of reporting, extraction
could reasonably be justified.
/ A
Probable Mineral Reserve is the economically mineable part of an Indicated, and in some circumstances, a Measured Mineral Resource.
The confidence in the Modifying Factors applying to a Probable Mineral Reserve is lower than that applying to a Proven Mineral Reserve.
/ A
Proven Mineral Reserve is the economically mineable part of a Measured Mineral Resource. A Proven Mineral Reserve implies a high
degree of confidence in the Modifying Factors.
/ Modifying
Factors are considerations used to convert Mineral Resources to Mineral Reserves. These include, but are not restricted to, mining,
processing, metallurgical, infrastructure, economic, marketing, legal, environmental, social and governmental factors.
The Project consists of the addition
of lithium recovery facilities to the ongoing bromine production at the South Unit, thereby producing a portion of the South Unit’s
Measured Mineral Resources described in Section 14. As an addition to the existing bromine recovery process, the Project is not
subject to several of the uncertainties and economic costs associated with ‘greenfield’ projects; the production and injection
facilities are already in place, are in operation, and benefit from the ongoing bromine production.
| 15.2 | Lithium
Reserve Estimate |
The lithium Reserve estimates reported
here were obtained using the simulation model described in Section 14. The lithium Mineral Reserves are that part of the Measured
Mineral Resource for the South Unit effective August 18, 2023, that are estimated to be recovered by the Project over the 25-year
forecast operating period, with project start-up of mid 2026. The basis for the forecast operating conditions is provided in Section 16.
Two cases of Feed Brine rates were evaluated
to estimate the Project Reserves. The Proven Reserves case is based on LANXESS’s minimum annual average South Unit Feed Brine rate
expected over the 25-year Project production period of 4.96 x 106 m3 per year. This minimum annual average production
rate is based on the South Unit Development Plan as set out in the Site Access, License and Reservation Agreement (SARL) between Company
and LANXESS. (Standard Lithium 2023). The Proven plus Probable Reserves case rate forecast is based on the average South Unit brine production
expected over the 25-year Project production period of 5.21 x 106 m3 per year. Both cases assume the same process
efficiency and lithium recovery factors over that period, with the Probable Reserves equal to the difference between the two cases. The
estimated Proven and Probable reserves are presented in Table 15-1.
113 |
 |
RSI-3353 |
The Project’s Modifying Factors
include the following, and are summarized in Table 15-2:
/ South
Unit Feed Brine Rate: The total volume of Feed Brine processed by the South Unit bromine plant which is available for processing
by the Project.
/ System
Availability: The availability of the lithium extraction facility.
/ Lithium
Recovery Efficiency: The fraction of the lithium contained in the brine received by the Project that is recovered by the process;
unrecovered lithium is injected back into the reservoir.
/ Lithium
Carbonate Attrition: The fraction of lithium lost in the production and handling of the lithium carbonate product, attributable to
sampling, spillage, and other non-process related losses.
Additional validation for the Probable
and Proven Reserve estimates presented in Table 15.1 results from the potential Project upside aspects, including:
/ Project
Optimizations: The Project operating conditions assumed in this analysis do not include potential optimizations, such as modifying
the injection locations for the processed lean brine to reduce lean brine breakthrough at production wells, or the implementation of
more-efficient or less-expensive lithium recovery technologies.
/ Project
Expansion: The reserve estimates are based on rates associated with current operations, and do not include any as-yet unplanned expansions
to either processing facilities or Project area.
/ Increased
Throughput: It may be possible to operate the South Unit at a higher brine production rate through improved brine field production
system availability.
While a 100 mg/L minimum
producing lithium concentration cutoff was evaluated for the estimation of South Unit lithium Brine Reserves, it did not affect the results,
The Feed Brine concentration exceeded the 100 mg/L cutoff value throughout the 25-year evaluation period. This cutoff was not applied
to individual wells because the wells will be produced for bromine recovery, regardless of lithium content. Unless otherwise noted, Brine
Reserves are referenced at the inlet to the lithium processing plant.
114 |
 |
RSI-3353 |
Table 15-1.
Phase 1A Proven and Probable Reserves
| |
Units | |
Proven | | |
Probable | | |
Proven
+ Probable | |
Brine
Reserves [4,8] | |
million m³ | |
| 124 | | |
| 84 | | |
| 209 | |
Average
Lithium Concentration [4,8] | |
mg/L | |
| 227 | | |
| 201 | | |
| 217 | |
Lithium
Metal [4,8] | |
thousand tonnes | |
| 28.2 | | |
| 17 | | |
| 45.2 | |
LCE
Reserves [4,9,10,12] | |
thousand tonnes | |
| 129 | | |
| 79 | | |
| 208 | |
Notes:
[1] The effective date of the reserve
estimate is August 18, 2023.
[2] Any discrepancies in the totals
are due to rounding effects.
[3] The Qualified Person for the Mineral
Reserve estimate is Randal M. Brush, PE.
[4] Reserves are exclusive to the South
Brine Unit.
[5] The average lithium concentration
is weighted per well simulated extraction rates.
[6] The Proven case assumes a 25-year
operating life at 4.96 million m3/year of brine production at a cut-off of 100 mg/L.
[7] Proven plus Probable Reserves assume
a 40-year operating life at 5.21 million m3/year of brine production at a cut-off of 100 mg/L.
[8] The Reserves reference point for
the brine pumped, average lithium concentration, and lithium metal is the brine inlet to the Standard Lithium processing plant.
[9] The Reserves reference point for
the LCE is the product output of the processing plant.
[10] Lithium Carbonate production values
consider plant processing efficiency factors.
[11] The Mineral Reserve estimate follows
2014 CIM Definition Standards and the 2019 CIM MRMR Best Practice Guidelines.
[12] Lithium Carbonate Equivalent (“LCE”)
is calculated using mass of LCE = 5.323 multiplied by mass of lithium metal.
[13] The Qualified Person is not aware
of any known environmental, permitting, legal, title-related, taxation, socio-political or marketing issues, or any other relevant issue,
that could materially affect the potential development of Mineral Resources other than those discussed in the Mineral Resource Estimates.
Table 15-2.
Phase 1A Modifying Factors
Modifying
Factor | |
Units | | |
Proven
Reserves
Case | | |
Probable
Reserves
Case | |
South Unit Feed Brine Rate | |
| million
m3/yr | | |
| 4.96 | | |
| 5.21 | |
Years 2 through 25 System Availability | |
| Percent | | |
| 94.0 | % | |
| 94.0 | % |
Lithium Recovery Efficiency | |
| Percent | | |
| 93.1 | % | |
| 93.1 | % |
Lithium Carbonate Attrition | |
| Percent | | |
| 0.5 | % | |
| 0.5 | % |
Notes:
[1] Year 1 production is expected to
be 75% of the facility capacity to account for the ramp-up period
115 |
 |
RSI-3353 |
| 15.3 | Discussion
of Results |
The lithium reserves estimate presented
in this TR are supported in several ways:
/ The
successful brine injection and production activities associated with bromine recovery in south Arkansas and in the Property over the
past 60 plus years provides compelling evidence regarding the brine content, the productivity, and the continuity of the Smackover Formation
over large distances, essential elements to support of the lithium brine recovery Project described in this TR.
/ The
bromine extraction process in the South Unit is planned to occur with or without the implementation of the lithium recovery process.
This greatly reduces uncertainties associated with the Project life and creates potential project upside regarding the extension of the
project if the bromine production is enhanced in the future.
/ The
geological characteristics of the Property have already been fully delineated by the existing wells. Therefore, the estimated reservoir
volumes associated with the Measured and Indicated Resources, and with the Proven and Probable Reserves have been fully delineated.
/ The
geological model was incorporated into the reservoir simulation model, which was matched to the full life of the bromine production history
which aligned with the lithium sampling results.
/ The
simulation model, through its history match of field production, has confirmed the geological characteristics of the Property, demonstrating
the reservoir to be productive, continuous, and to contain the estimated volume of brine.
/ This
single calibrated and matched simulation model, used as the basis both for the Measured and Indicated Resources and for the Proven and
Probable Reserves ensures consistency between the reported mineral resource and reserves estimates.
For these reasons, the mineral reserve
estimates reported here are considered to be reasonable, and in conformance with the requirements of NI 43-101.
116 |
 |
RSI-3353 |
Recovery of the lithium will use the
existing LANXESS South Unit brine production facilities (brine supply wells, down-hole pumps, surface flowlines, bromine processing facilities,
and connecting pipelines and disposal wells, as described in the PEA (Dworzanowski et al. 2019) to supply the Feed Brine from the LANXESS
South Plant to the Project. Once the lithium is extracted from the brine, the processed brine will be re-injected into brine disposal
wells, along with any brine not processed by the Project. This production and injection process from a deep brine reservoir is identical
to that used in the adjacent Albemarle bromine project and incorporates the production and injection technology which has been proven
by the petroleum industry in thousands of fields worldwide.
Examples of a typical brine source well
(BSW) and salt water disposal (SWD) wells are given in Figures 16-1 and 16-2, and the configuration of the South Unit wells and the existing
pipeline network is presented in Figure 16-3.
Figure 16-1. Typical Brine Source
Well Diagram
117 |
 |
RSI-3353 |
Figure 16-2. Typical Disposal
Well Diagram
118 |
 |
RSI-3353 |
Figure 16-3. South Unit Well
and Flow Line Configuration
The assumed Project injection and production
rates are based on the existing well capacity and historic field operations, as LANXESS set out in the South Unit Development Plan, which
sets out a high level, the contemplated production from the South Unit by LANXESS over the life of the Project. The extraction method
is not expected to impose any significant changes on the existing bromine processing activities. Based on the current predicted life
of the existing brine supply and disposal wells, no new wells are anticipated to be required during the initial 25-year operating life
of the facility.
Proven Reserves case total brine rate
and lithium concentration are plotted in Figure 16-4. The decrease in lithium concentration over the life of the Project results from
the increasing production volume of injected lean brine that has been processed to remove the lithium, as expected in a brine displacement
process.
119 |
 |
RSI-3353 |
Figure 16-4. South Unit Production
- Concentration Estimates
The Project contemplates production
of battery-quality lithium carbonate averaging 5,400 tonnes per annum (tpa) over a 25-year operating life, producing 135,000 tonnes LCE
from the LANXESS South Brine Unit.
The Project has the potential to operate
over a 40-year life based on the Proven and Probable Reserves of 208,000 tonnes LCE. The TR makes very conservative assumptions that
production of brine will occur from the existing wellfield, and that no additional wells are drilled in the future to supplement or add
to the current brine flow, or to add additional brine from higher lithium content zones available in the production unit(s). See Figure
16-5 for the annual production plan.
120 |
 |
RSI-3353 |
Figure 16-5. Project Production
Plan
The LANXESS the South Unit Brine Resource
and Proven Brine Reserves support the production of Lithium Carbonate well in excess of the initial 25-year economic life of the Project.
The long-established history of brine production coupled with the proven experience of LANXESS in brine field operations, coupled with
the fact that economic benefit will be obtained from both bromine and lithium extraction from the Project production, further supports
planned future brine production from the South Unit.
121 |
 |
RSI-3353 |
Table 16-1.
Planned South Unit Production by Year for First 25 Years of Production
| |
| |
Proven
Reserves | |
Proven
and Probable Reserves | |
| Year
No. | |
| Year | |
| Average
Lithium
Concentration | |
| Lithium
Processed by
the Plant | |
| Equivalent
Lithium at
Plant Outlet,
100% Purity | |
| Average
Lithium
Concentration | |
| Lithium
Processed by
the Plant | |
| Equivalent
Lithium at
Plant Outlet,
100% Purity | |
| | |
| | |
| (mg/L) | |
| (tonnes/year) | |
| (tonnes/year) | |
| (mg/L) | |
| (tonnes/year) | |
| (tonnes/year) | |
| 1 | |
| 2026 | |
| 239 | |
| 888 | |
| 780 | |
| 239 | |
| 932 | |
| 864 | |
| 2 | |
| 2027 | |
| 237 | |
| 1,072 | |
| 941 | |
| 237 | |
| 1,162 | |
| 1,077 | |
| 3 | |
| 2028 | |
| 236 | |
| 1,070 | |
| 939 | |
| 236 | |
| 1,160 | |
| 1,074 | |
| 4 | |
| 2029 | |
| 235 | |
| 1,062 | |
| 933 | |
| 235 | |
| 1,151 | |
| 1,066 | |
| 5 | |
| 2030 | |
| 234 | |
| 1,058 | |
| 929 | |
| 234 | |
| 1,147 | |
| 1,062 | |
| 6 | |
| 2031 | |
| 233 | |
| 1,054 | |
| 926 | |
| 233 | |
| 1,142 | |
| 1,058 | |
| 7 | |
| 2032 | |
| 233 | |
| 1,053 | |
| 925 | |
| 232 | |
| 1,142 | |
| 1,058 | |
| 8 | |
| 2033 | |
| 232 | |
| 1,048 | |
| 920 | |
| 232 | |
| 1,135 | |
| 1,052 | |
| 9 | |
| 2034 | |
| 231 | |
| 1,045 | |
| 917 | |
| 231 | |
| 1,132 | |
| 1,048 | |
| 10 | |
| 2035 | |
| 231 | |
| 1,042 | |
| 915 | |
| 230 | |
| 1,129 | |
| 1,045 | |
| 11 | |
| 2036 | |
| 230 | |
| 1,042 | |
| 915 | |
| 230 | |
| 1,128 | |
| 1,045 | |
| 12 | |
| 2037 | |
| 229 | |
| 1,036 | |
| 909 | |
| 229 | |
| 1,121 | |
| 1,039 | |
| 13 | |
| 2038 | |
| 229 | |
| 1,032 | |
| 906 | |
| 228 | |
| 1,117 | |
| 1,035 | |
| 14 | |
| 2039 | |
| 228 | |
| 1,028 | |
| 903 | |
| 227 | |
| 1,112 | |
| 1,030 | |
| 15 | |
| 2040 | |
| 227 | |
| 1,027 | |
| 902 | |
| 226 | |
| 1,109 | |
| 1,028 | |
| 16 | |
| 2041 | |
| 226 | |
| 1,019 | |
| 895 | |
| 225 | |
| 1,100 | |
| 1,019 | |
| 17 | |
| 2042 | |
| 224 | |
| 1,014 | |
| 890 | |
| 223 | |
| 1,093 | |
| 1,013 | |
| 18 | |
| 2043 | |
| 223 | |
| 1,008 | |
| 885 | |
| 222 | |
| 1,086 | |
| 1,006 | |
| 19 | |
| 2044 | |
| 222 | |
| 1,005 | |
| 882 | |
| 220 | |
| 1,081 | |
| 1,002 | |
| 20 | |
| 2045 | |
| 220 | |
| 995 | |
| 874 | |
| 219 | |
| 1,070 | |
| 992 | |
| 21 | |
| 2046 | |
| 219 | |
| 989 | |
| 868 | |
| 217 | |
| 1,063 | |
| 984 | |
| 22 | |
| 2047 | |
| 218 | |
| 982 | |
| 863 | |
| 215 | |
| 1,055 | |
| 977 | |
| 23 | |
| 2048 | |
| 216 | |
| 979 | |
| 859 | |
| 214 | |
| 1,050 | |
| 973 | |
| 24 | |
| 2049 | |
| 215 | |
| 970 | |
| 851 | |
| 212 | |
| 1,040 | |
| 963 | |
| 25 | |
| 2050 | |
| 213 | |
| 963 | |
| 846 | |
| 211 | |
| 1,032 | |
| 956 | |
122 |
 |
RSI-3353 |
The Project Facility will be constructed
adjacent to the existing LANXESS South Plant which currently receives, processes, and reinjects Smackover brine from the South Unit via
a series of brine supply and reinjection wells as described in Section 16. The Project will receive brine downstream of the bromine
processing facility, recover the lithium and return the lithium-depleted brine to LANXESS for reinjection into the Smackover Formation.
The Feed Brine received by the Project
is pH adjusted, filtered and conditioned in a series of pre-treatment processes in preparation for the Direct Lithium Extraction (DLE)
process. The DLE technology chosen for the Project is Lithium Selective Sorption (LSS), a Koch Technology Solutions LLC (KTS) proprietary
technology, which extracts lithium ions from the brine to produce a raw lithium chloride solution that is low in contaminants. The lithium
chloride is then purified through chemical softening and ion exchange, and concentrated using reverse osmosis to produce a polished lithium
chloride solution.
The polished lithium chloride then enters
a conventional, two-stage, lithium carbonate crystallization process to produce battery quality lithium carbonate. The lithium carbonate
is dried, milled, and packaged to produce the finished product.
The lithium recovery method within the
Project Facility consists of the following major process blocks:
/ Brine
Pre-Treatment;
/ Direct
Lithium Extraction;
/ Concentration
and Purification; and
/ Lithium
Carbonate Conversion.
The process block flow diagram included
in Figure 17-1 provides an overview of the lithium recovery process proposed for Standard Lithium’s Commercial Lithium Extraction
Plant.
123 |
 |
RSI-3353 |
Figure 17-1. Project Process
Block Flow Diagram
| 17.2 | Brine
Supply and Reinjection (LANXESS) |
Under the terms of the commercial agreements,
LANXESS is responsible for the supply and reinjection of brine which meets the process conditions set out in the commercial agreements.
Figure 17-2 provides an overview of the brine supply and return process between the Project Facility and LANXESS South Plant.
Figure 17-2. Standard Lithium
and LANXESS Process Block Flow Diagram
Smackover brine produced by LANXESS
from the wells in the South Unit is treated and then gathered and delivered via pipeline to the South Plant for processing. Separation
equipment at each well head is used to remove the bulk of any produced hydrocarbons and the sour gas (H2S) from the brine
stream prior to delivery to the South Plant. The sour gas collected is transported to the LANXESS Central Plant via pipeline and then
delivered to the Delek Refinery for processing. Any produced hydrocarbons are locally collected and transported to the Delek Refinery
for processing.
124 |
 |
RSI-3353 |
Once the brine is received at the South
Plant, it first passes through a LANXESS vacuum degasser to remove residual sulfides entrained in the brine to less than 30 ppm (wt/wt)
of H2S, prior to the bromine extraction process. LANXESS may or may not extract bromine from the brine.
Brine which bypasses the bromine extraction
facilities, referred to as Bypass Brine, requires pH adjustment using anhydrous ammonia (NH3) prior to delivery to the Project
Facility or reinjection into the formation. Bromine-depleted brine, referred to as Tail Brine, requires a further treatment by LANXESS
using sodium bisulfite (SBS) to reduce any residual bromine and chlorine in the Tail Brine stream to bromides and chlorides.
The Project will be able to treat Feed
Brine (Tail Brine or Bypass Brine) from LANXESS at a range of pH between 1 to 5.5. By receiving the brine at a lower pH, softening sludge
produced by the Project Facility’s downstream lithium chloride purification process can be used for coarse pH adjustment, which
results in improved lithium recovery for the Project and an operating cost savings to LANXESS through reduced anhydrous ammonia consumption
and to the Project through reduced reagent consumption.
Following the lithium extraction process
and any treatments required to meet reinjection specifications, the majority of the lithium-depleted brine and ancillary waste streams
are consolidated and returned to LANXESS for reinjection into the Smackover Formation using the existing LANXESS reinjection well network.
Any excess brine volumes are reinjected underground using the Project’s Class 1 Non-Hazardous Underground Injection Control
(UIC) wells as described in Section 18.
The Project is designed to receive Feed
Brine from the LANXESS South Plant at an operating rate of 680 m3/hr [3,000 US gpm] with a 10% design factor. This is to ensure
the project maximizes the volume of Feed Brine processed accounting for fluctuation in brine delivery rates from South Plant. The Feed
Brine is typically hot, acidic, and highly saline. Besides lithium, the brine’s primary constituents include sodium, potassium,
magnesium, and calcium chlorides with minor quantities of boric acid.
The objective of Brine Pre-treatment
is to neutralize, cool, and filter the Feed Brine in preparation for the Direct Lithium Extraction (DLE) process.
Feed Brine received from LANXESS is
initially processed through two pH control tanks. Under normal operations, the first tank uses chemical softening sludge, primarily calcium
carbonate and magnesium hydroxide produced in the downstream raw lithium chloride softening system, for coarse pH adjustment, specifically
to raise the Feed Brine pH to approximately 4.0 - 4.5. The second tank uses caustic soda (sodium hydroxide solution) to further raise
the brine pH to 5.5, the target pH for the DLE process. In the event there is insufficient softening sludge available, LANXESS will adjust
the pH of the Feed Brine prior to delivery to the Project.
125 |
 |
RSI-3353 |
The Feed Brine temperature ranges between
60-90°C. To optimize the downstream process, two heat exchangers operating in parallel are used to moderate the brine temperature
to 65°C primarily to protect the downstream membrane filtration system. The lithium-depleted brine produced downstream from the DLE
process is used as coolant after passing through an evaporative cooling tower. The cooling tower is used to cool the lithium-depleted
brine from 65°C to less than 40°C. The cooling tower also removes 35 m3/hr of water from the brine by evaporation,
which reduces the total volume of brine required to be reinjected into the Smackover Formation.
The pH and temperature adjusted Feed
Brine is pumped through ultrafiltration (UF) membrane filters, for the removal of any fine suspended solids (over 0.04 µm). The
UF membrane filters consist of five operating and one standby module. The membrane modules are removed from service one at a time to
release the collected solids by air scouring and backwashing. Lithium-depleted brine is used for regular backwash of the membrane filters.
The solids-laden backwash is transferred to the effluent brine tank. Clean-in-Place (CIP) of the UF membranes is periodically required.
CIP uses a combination of cleaning agents including acids and detergents to remove any buildup of solids on the membrane.
| 17.4 | Direct
Lithium Extraction |
| 17.4.1 | Lithium
Selective Sorption |
The key unit process for the production
of lithium chloride solution is the Direct Lithium Extraction process. Standard Lithium has selected the Lithium Selective Sorption (LSS)
process as the DLE process for the Project. The selection is based on improved economics, the expected performance guarantees to be provided
by KTS, and the DLE test work undertaken as described in Section 13.3.3.
The LSS equipment is a Koch Technology
Solutions proprietary technology for which Standard Lithium have a Joint Development Agreement and Smackover Formation exclusivity agreement
in place (for a period of time). The process will be a fixed bed, selective adsorption process that favors lithium chloride. Lithium-rich
brine will be pumped through the fixed bed of sorbent, loading the sorbent with both lithium and chloride ions, and discharging a raffinate
that is barren of lithium. The loading will be stopped at the point that lithium breakthrough occurs. After displacing remaining raffinate
from the sorbent bed, the sorbent will be eluted with water, releasing the lithium and chloride, and producing an eluate that compared
to Feed Brine is somewhat higher in lithium concentration and much lower in other undesirable ions such as sodium, potassium, calcium,
magnesium and boron. The remaining eluate will then be displaced from the column to the feed tank and the cycle will be repeated.
After the LSS DLE process, the eluate
or raw lithium chloride solution will recover approximately 95% lithium and will have rejected in excess of 98% of the major contaminants
for sodium, calcium, magnesium, and potassium.
| 17.4.2 | Lithium-Depleted
Brine Processing |
Lithium-depleted brine rejected from
LSS passes through a brine cooling tower and heat exchangers described above in Brine Pre-treatment. Lithium-depleted brine is also reused
as membrane filter backwash. All lithium-depleted brine and other process waste streams are ultimately consolidated, pH adjusted and
then sent for reinjection either to the LANXESS brine reinjection network or to one of the Project’s two dedicated UIC wells.
126 |
 |
RSI-3353 |
| 17.5 | Purification
and Concentration |
| 17.5.1 | Brackish
Water Reverse Osmosis |
The raw lithium chloride from LSS is
concentrated via conventional Brackish Water Reverse Osmosis (BWRO) to remove nearly 90 percent of the water. In this process lithium
in the chloride solution is concentrated to 2,500 to 3,000 mg/L along with 99% of the solution impurities. The BWRO concentrate
is the product that continues to the next step as lithium chloride. The BWRO permeate is reused throughout the process but mainly as
eluant for the DLE process.
CIP of the BWRO membranes is periodically
required. CIP uses a combination of cleaning agents including acids, detergents, anti-scalant, and bases to remove any buildup of solids
on the membrane.
The objective of chemical softening
is to reduce calcium and magnesium from the lithium chloride rich solution.
The lithium chloride from BWRO is chemically
treated with soda ash (Na2CO3) and lime (Ca(OH)2) to precipitate calcium carbonate and magnesium hydroxide.
The lithium chloride is then separated from the precipitates through a clarifier.
The clarifier underflow is filtered
and reslurried with Feed Brine to produce the softening sludge required in Brine Pre-treatment for pH adjustment.
The clarifier overflow following polishing
by a multi-media filter continues to the next step as softened lithium chloride.
The purity requirements for battery-quality
lithium carbonate require near complete removal of calcium, magnesium, and boron. To meet the lithium carbonate purity requirements,
two ion exchange systems are used. The first removes calcium and magnesium and the second removes boron from the softened lithium chloride.
| 17.5.3.1 | Calcium
and Magnesium Removal |
The softened lithium chloride is treated
to remove calcium and magnesium using a chelating resin through a continuous ion exchange system. The columns will alternate between
loading and regeneration.
The softened lithium chloride passes
through the ion exchange columns during loading, where calcium and magnesium are loaded onto the resin and stripped from the lithium
chloride. The calcium and magnesium are then stripped from the resin during regeneration using a combination of water, acid, and base
which is then directed to the effluent brine system.
127 |
 |
RSI-3353 |
| 17.5.3.2 | Ion
Exchange Boron Removal |
The boron ion exchange system receives
lithium chloride after calcium and magnesium removal and uses boron-selective chelating resin.
The lithium chloride passes through
the ion exchange columns during loading, boron is loaded onto the resin and stripped from the lithium chloride. The boron is then stripped
from the resin during regeneration using a combination of water, acid, and base and then directed to the effluent brine system.
| 17.5.4 | Osmotically-Assisted
Reverse Osmosis (OARO) |
The lithium chloride, after calcium,
magnesium and boron removal, is concentrated via an Osmotically Assisted Reverse Osmosis (OARO) treatment system until lithium concentrations
reach approximately 8,000 – 10,000 mg/L. The OARO permeate is reused as RO water and the OARO concentrate or polished lithium chloride
is advanced for lithium carbonate conversion. After RO the lithium chloride brine contains lithium chloride, sodium chloride and minor
levels of other impurities,
Impurities, including silica, aluminum,
manganese, and iron, must be controlled ahead of the OARO to avoid fouling or damaging the membranes, and are expected to be reduced
to acceptable levels during chemical softening and ion exchange. CIP of the OARO membranes is periodically required. CIP uses a combination
of cleaning agents including acids, detergents, anti-scalant, and bases to remove any buildup of solids on the membrane.
| 17.6 | Lithium
Carbonate Conversion |
| 17.6.1 | Lithium
Carbonate Crystallization |
The lithium carbonate crystallization
system receives polished lithium chloride solution from OARO and produces lithium carbonate using a two-stage conventional crystallization
process with a bicarbonate process and further ion exchange treatment.
Low solubility lithium carbonate is
produced by reacting lithium chloride with a sodium carbonate solution. Crude lithium carbonate that forms from the reaction is recovered
with the following process.
First, the lithium carbonate is crystallized
in a draft tube baffled (DTB) first stage lithium carbonate crystallizer. The lithium carbonate slurry is combined with the baffle overflow
liquor before being pumped to a peeler type first stage lithium carbonate centrifuge. The crystals are de-watered and washed using centrate
from the second stage lithium carbonate centrifuges. The cake discharged from the centrifuge is then repulped with recycled centrate
from the second stage lithium carbonate centrifuges and RO water.
128 |
 |
RSI-3353 |
The first stage lithium carbonate crystals
produced from the first stage centrifuge are impure, containing unacceptable levels of calcium and magnesium contributed by the reaction
with soda ash, and sodium and chloride from the lithium chloride feed.
The centrate from the first stage lithium
carbonate is purged from the carbonation process to prevent a build-up of contaminants in the process. It is returned to the Feed Brine
ahead of the LSS process as this carbonate purge stream has high lithium content.
The lithium carbonate slurry fed into
the bicarbonate reactor is converted to soluble lithium bicarbonate by reaction with carbon dioxide under pressure. The lithium bicarbonate
solution is then filtered and purified to remove calcium and magnesium in a fixed-bed ion exchange system.
The second stage lithium carbonate crystallizer
is a DTB type crystallizer which is heated by sparged steam and operates at 95°C. At this temperature and atmospheric pressure, the
lithium bicarbonate is converted to lithium carbonate with carbon dioxide evolving from the solution while the lithium carbonate crystallizes.
The overhead vapor from the crystallizer is condensed with cooling water and the non-condensable carbon dioxide is recompressed and recycled
to the lithium bicarbonate reactor. Lithium concentration in the mother liquor from the second stage crystallizer is about 3,000 mg/L.
Lithium carbonate crystals at 15 wt.% slurry density are combined with the baffle overflow before being pumped to peeler-type second
stage lithium carbonate centrifuges with hot treated water used to wash the lithium carbonate crystals in the centrifuge. The second
stage centrate is used to repulp the first stage crude lithium carbonate and to wash the first stage centrifuge cake.
Crystals in the second stage centrifuge
cake are battery-quality lithium carbonate. The washed, pure lithium carbonate second stage centrifuge cake is then dried in an indirect-steam-heated
dryer.
| 17.6.2 | Drying,
Milling, and Packaging |
Following crystallization, the lithium
carbonate will be dried in an indirect-steam heated dryer, cooled, micronized (crushed), and pneumatically conveyed for packaging. After
sampling and laboratory analysis, the battery quality lithium carbonate is then loaded into 500 kg or 1,000 kg bulk bags, palletized,
and ready for shipment.
| 17.7 | Energy.
Water, and Process Materials |
| 17.7.1 | Energy
Requirements |
The electrical power required for the
Project is estimated at 7.6 MWh during normal operation and will be supplied by the regional electric service provider Entergy. Entergy
is currently completing a Facility Study to determine the specific upgrades required to the Entergy infrastructure for supplying this
new connected load.
The natural gas required for the Project
is estimated at 260 GJ per day to support boiler steam production and ancillary heating needs. The natural gas supply infrastructure
will be provided by Energy Transfer and the natural gas will be purchased from a local supplier/marketer.
129 |
 |
RSI-3353 |
Raw water for process uses will be sourced
from one of two new wells to be drilled and completed on the Project Site. Each well will have the capacity to supply up to 160 m3/hr
from the Sparta Aquifer. The plant raw water demand can be satisfied by either well. Water used for most lithium extraction processes
and for boiler feedwater is first purified using reverse osmosis. Additional treatment is required to produce the high purity water used
in the lithium carbonate washing circuit. Untreated well water and recycled storm water, when available, is used for fire protection,
irrigation and general plant washdown.
Chlorinated well water for non-potable
domestic uses will be sourced from either one of the new on-site wells and chlorinated, or chlorinated water will be purchased from LANXESS
and delivered by pipeline from South Plant. Potable water for drinking water purposes will be locally purchased or produced on site from
treated well water.
The various lithium recovery and purification
processes require hydrochloric acid (HCl) and caustic soda (NaOH) for pH adjustment and ion exchange resin regeneration, soda ash (Na2CO3)
for softening and to precipitate lithium carbonate, and lime (Ca(OH)2) for magnesium removal in softening. Estimated annual
consumption of reagents are presented in table 17-1 below.
Table 17-1.
Reagent Consumption
Description |
|
Average
Consumption per Year |
32%
Hydrochloric Acid (HCl) |
|
6,200
tonnes |
50%
Caustic Soda (NaOH) |
|
11,400
tonnes |
Soda
Ash (Na2CO3) |
|
15,500
tonnes |
Lime
((Ca(OH)2) |
|
700
tonnes |
Other reagents and additives to the
process include:
/ anti-scalant;
/ carbon
dioxide;
/ citric
acid;
/ coagulant;
/ flocculant;
and
/ surfactant.
These chemicals are used in the lithium
carbonate circuit, CIP systems, boiler feedwater treatment, cooling tower chemicals, and other ancillary processes.
130 |
 |
RSI-3353 |
| 18.0 | Project
Infrastructure |
| 18.1 | Infrastructure
Description |
The proposed Project Facility is strategically
located on undeveloped lands adjacent to the existing LANXESS South Plant to allow interconnection with key elements of existing LANXESS
South Plant infrastructure, specifically the brine handling system as generally shown on Figure 18-1. Supporting services including power,
natural gas, and water is readily available at the Project Site.
Figure 18-1. Proposed Project
Facility Location
The infrastructure associated with the
Project includes:
/ Brine
Supply and Return Pipelines;
/ Processing
Plant;
/ Non-process
Buildings; and
/ Supporting
Infrastructure.
Under the terms of the commercial agreements,
LANXESS is responsible for construction of certain improvements (LANXESS Constructed Improvements) to the existing LANXESS Tail Brine
system to facilitate the delivery of Feed Brine to the Project. This is further discussed in Section 18.6.
131 |
 |
RSI-3353 |
Figure 18-2 provides a general overview
of the Project infrastructure.
Figure 18-2. Project Site Overview
A geotechnical field program and engineering
study was completed in March 2023 to assess the suitability of the proposed Project Site for the proposed development. The field
program included soil boring, test pitting and soil sampling to characterize ground conditions and confirm groundwater levels, with the
objective of identifying any material ground risks, and to input into the design of the Project.
The field program confirmed the expected
soil stratigraphy at the Project Site, determined to consist of highly variable layers of clay, silt, and sandy soils. Typically, the
upper soils are more cohesive in content and become sandier with depth. The lower sand soils appear laminated and cross-bedded, with
variable lenses of clay transitioning into in clayey sand soils. Groundwater was typically observed between a depth of 7m to 16m below
the existing ground surface.
The study provided preliminary geotechnical
recommendations for the earthworks, foundations, and pavements and to address seismic conditions. These recommendations are considered
in the design of the Project Facility. Overall, the study concluded that the site is suitable for the proposed development and conventional
foundation and construction techniques used in the area can be applied without the need for ground improvements.
| 18.2 | Brine
Supply and Return |
Brine will be delivered to and from
the Project Facility via pipeline. Two operating and one standby centrifugal pumps with variable frequency drives located at the South
Plant will be constructed to transfer Feed Brine to the Project Facility via a 1 km long, 300 mm (12 inch) fiberglass pipeline.
A parallel 300 mm fiberglass pipeline will transfer Effluent Brine from the Project Facility back to the South Plant.
132 |
 |
RSI-3353 |
The pipelines will be surface run within
the fence line of the South Plant and buried outside. A horizontal direction drill (HDD) will be used to route the supply and return
pipelines to pass under the existing LANXESS pipelines, utilities and main South Plant access road. Figure 18-3 shows the pipeline routing.
Figure 18-3. Brine Supply and
Return Pipelines
Metering and sampling equipment will
be installed by the Project on the brine supply and return pipelines to continuously monitor the volume and quality of brine received
and discharged by the Project.
The processing plant encompasses brine
pre-treatment, lithium selective sorption, effluent brine, softening, ion exchange, lithium chloride concentration, and lithium carbonate
production and drying, milling, and packaging. Figure 18-4 provides a layout of the Project Facility.
133 |
 |
RSI-3353 |
Figure 18-4. Project Facility
Layout
| 18.3.1 | Brine
Pre-Treatment |
Feed Brine received from the brine supply
pipeline must be chemically treated and conditioned prior to the direct lithium extraction process. Major equipment required to support
Pre-Treatment includes:
/ Softening
recycle tank with agitator;
/ Neutralization
tank with agitator;
/ Two
Feed Brine storage tanks;
/ A
storage swing tank that can be used either to store Feed Brine or Effluent Brine;
/ Two
heat exchangers;
134 |
 |
RSI-3353 |
/ UF
membrane filter package; and
/ Membrane
backflush filter press.
The two Feed Brine storage tanks provide
the ability to store up to eight (8) hours of brine production from LANXESS at the design capacity of 680 m3/hr. This
allows the Project to continue to receive brine from LANXESS in the event of a downstream process interruption, or to continue running
the downstream process in the event of an upstream interruption. The brine storage swing tank provides additional operational flexibility
for additional Feed Brine or Effluent Brine storage as may be required.
| 18.3.2 | Lithium
Selective Sorption (LSS) |
The LSS package is a proprietary technology
for direct lithium extraction. It includes multiple trains of columns filled with resin to load and elute lithium from the brine. Provisions
for the inspection and efficient replacement of resin will be included.
The softening circuit removes calcium
and magnesium from the lithium chloride and recycles the softening sludge to pre-treatment for Feed Brine neutralization. The major equipment
required for softening includes:
/ Flash
tank with agitator;
/ Reactor
tanks with agitators;
/ Clarifier;
/ Media
Polishing Filter;
/ Softened
Brine storage;
/ Filter
press;
/ Softened
Sludge repulp and recycle.
There will be two continuous ion exchange
systems used to reduce impurities to acceptable levels for lithium carbonate production. The first system uses a chelating resin to target
calcium and magnesium removal. The second system targets boron. A series of columns will be mounted on a rotating carousel. Each carousel
is anticipated to include 30 columns.
| 18.3.5 | Lithium
Chloride Concentration |
There are two RO packages (BWRO and
OARO) used to concentrate the lithium chloride to acceptable levels for lithium carbonate production. Both packages use cartridge filters,
high pressure pumps, and RO membranes to increase concentration through desalination.
| 18.3.6 | Lithium
Carbonate Production |
The lithium carbonate plant receives
polished and concentrated lithium chloride to produce battery-quality lithium carbonate. The major equipment includes:
/ Lithium
chloride storage tank;
135 |
 |
RSI-3353 |
/ First
stage crystallizer;
/ First
stage centrifuge;
/ Lithium
bicarbonate reactor;
/ Secondary
calcium ion exchange system;
/ Second
stage crystallizer; and
/ Second
stage centrifuge.
The lithium chloride storage tank provides
the ability to store up to 24 hours of lithium chloride to feed the lithium carbonate plant at the design capacity of approximately 30
m3/hr. This allows the project to continue producing lithium chloride in the event of a downstream process interruption, or
to continue producing lithium carbonate in the event of an upstream process interruption.
| 18.3.7 | Drying,
Milling, and Packaging |
Drying, milling, and packaging of the
lithium carbonate product will take place in a secure building. The lithium carbonate is stored in three shift bins. The product is then
conveyed to the bagging system which loads the product into 500 kg or 1,000 kg bulk bags ready for delivery by truck. The building includes
space to store the equivalent of three days of production of finished bagged lithium carbonate.
Lithium-depleted brine received from
LSS is collected, along with other effluent brine streams as is collectively conditioned to ensure quality requirement for discharge
are met prior to return to the South Plant or reinjection into UIC wells. Major equipment required to support effluent brine handling
includes:
/ Neutralization
tank;
/ Brine
cooling tower; and
/ Effluent
Brine storage tank.
The Effluent Brine storage tank provides
the ability to store 4 hours of effluent brine at the design capacity of 680 m3/hr. This allows the Project to continue to
process brine in the event of a downstream process interruption at LANXESS. If additional storage is required, the swing tank from Brine
Pre-Treatment can be used for Effluent Brine.
| 18.3.9 | Process
Control & Instrumentation Systems |
The Project facility will have a Process
Control System (PCS) within a prefabricated and equipped Central Control Room (CCR). It will be a single-story building located within
the processing plant. The system will be equipped with an onsite radio and communication system to provide access to the internet and
telephones. In addition, the control room building will have main operator consoles, conference area, restrooms, and small kitchen area.
Controls will be implemented using a
Distributed Control System (DCS) with remote I/O (RIO) panels placed throughout the facility. Placement of the panels will be defined
by I/O count in the area and location of vendor control panels to minimize communication runs. Vendor PLC control panels will be integrated
into the DCS controller. DCS area controllers will remain inside the area Power Distribution Centers (PDC) buildings.
136 |
 |
RSI-3353 |
The main operator interface will be
via operator consoles in the new CCR. The operator consoles will show the graphic displays depicting the process units. Vendor control
panels will be integrated into the DCS controller. The control system will employ redundant processors to provide a high level of reliability
and uptime.
Control room design will have a separate
and secure data/server room which will house the control system servers, HMI servers, data historian, cyber-security, firewall, and other
network equipment.
| 18.4 | Non-Process
Buildings |
Non-process buildings include an administration
building, hourly workers building, warehouse, maintenance shop, onsite laboratory, and guardhouse.
The administration and hourly workers
buildings will be constructed to accommodate the approximately 90 people anticipated to be required to support operations. The administration
building will include offices, a conference room, break room, and restroom facilities. The hourly workers building will include male
and female locker rooms, restrooms, and a break room designed for 40 people. The number of staff and visitor parking stalls to be provided
is 100 and will include EV changing facilities. The administration building will be accessible to guests and visitors from outside the
process facilities.
A combined maintenance shop and warehouse
facility will also be constructed in the non-process building area. It will be a well-ventilated (non-climate controlled) steel clad
building with concrete flooring. The maintenance shop will include a tool crib, welding area, shop area and three climate-controlled
offices. The warehouse will include a receiving dock for deliveries with direct access from outside of the process plant, one climate-controlled
office, and parts storage including conditioned storage areas.
An on-site laboratory is provided to
support the production of battery quality lithium carbonate as well as real-time assessment of process production conditions to ensure
reliable continuous operation of the facility. The laboratory will be a modular facility that will be constructed next to the warehouse
and shops.
A guard house will be provided at the
plant entrance to control point entry and exit to the process facilities. The guard house will be a permanent stick built or pre-engineered
modular facility. It will include workstations, a briefing room, restroom(s), and IT room.
To address the risk of extreme weather,
specifically tornadoes, severe weather shelters will be incorporated into facility structures, such as the control room, or addressed
using stand-alone pre-engineered structures designed to FEMA standards to protect on-site personnel.
137 |
 |
RSI-3353 |
The Project is based on the transportation
of all products, byproducts, reagents, materials, and equipment by truck to and from the Project Facility.
The primary reagents required for the
operation of the Project Facility received by truck will be stored locally on site in permanent storage systems with sufficient inventory
for reliable operation of the Project Facility.
Hydrochloric acid will be stored in
a common tank and distributed to local day tanks to support the various unity operations. Caustic soda will be stored in a single tank
and diluted with RO water for use. Soda ash will be delivered in bulk and stored dry in a storage bin. Citric Acid for membrane CIP will
be bulk delivered and stored in a tank. Lime will be received in bulk bags.
The supply of natural gas to the facility
will be provided by Energy Transfer. There is an existing 150 mm [6 inch] pipeline nearby with sufficient capacity to serve the Project.
The pipeline tie-in will be located to the north of the South Plant. Energy Transfer will construct a metering station at the tie-in
location. From the meter station, a 100 mm [4 inch] natural gas pipeline approximately 1 km long, running parallel to the brine supply
and return lines, will be installed by the Project to deliver gas to the Project facility. Similar to the brine pipelines, HDD will be
used to allow the supply and return pipelines to pass under the existing LANXESS pipelines, utilities, and main South Plant access road
as well as to pass under the existing the right-of-way for the Ouachita Railroad on the north side of the South Plant.
A dedicated and independent power supply
will be provided for the Project Facility by Entergy, the current provider of electrical power the LANXESS South Plant, from Entergy’s
115kV El Dorado Upland Substation which is located immediately to the east of the Project Facility. The existing 13.8 kV distribution
bus in the Entergy substation will be extended, and two new feeder bays and breakers will be installed by Entergy. Entergy will provide
a metering pole at the boundary of the substation which will the electrical tie-in point for the Project. 13.8kV overhead lines will
be installed by the Project between the Project Lease Area and Meter Pole tie-in location. The 13.8kV overhead lines will tie into the
power distribution center (PDC) feeding the process facilities as well as supply power to pole mounted utility transformers feeding the
non-process buildings. From the 13.8kV PDC, underground distribution will feed three local motor control center (MCC) buildings located
strategically around the process plant. The MCC buildings will house the required switchgear, motor control centers and lighting panels.
MCC’s will be smart type and the communication to the control system will be via ethernet over fiber optic cable.
138 |
 |
RSI-3353 |
Two new water wells will be installed and operated by the Project,
one at the northeast corner and one on the southwest corner of the Project Facility. Each well, capable of supplying up to 160 m3/hr
of water, will be used to support process water requirements, fire protection, or chlorinated on site for other domestic uses. A process
water tank will provide buffer storage for the facility prior to distribution.
A 50 mm [2 inch] potable water line
from the South Plant will provide an alternative source of chlorinated water for the Project Facility. The chlorinated water line from
the South Plant will follow the same general routing as the brine and natural gas pipelines from South Plant and provide water at a rate
of up to 11 m3/hour [50 US gpm]. Chlorinated water will be used for potable water needs including safety showers, eye wash
stations, faucets, toilets, and showers.
A Reserve Osmosis (RO) package will
be installed to supply RO water for boiler feed, seal water, CIP systems, reagent dilution, and for other process uses. An additional
water chiller will provide chilled process water to support the production of lithium carbonate.
| 18.5.3.4 | Steam &
Condensate |
A natural gas fired boiler will be installed
to supply low pressure steam for processing and other ancillary heating requirements. A condensate return system will be included to
recycle condensate to the boiler.
A centralized compressed air system
is provided to support both process air and instrument air requirements.
A small vendor supplied packaged wastewater
treatment plant will be installed for treatment of domestic sewage prior to surface discharge.
A fire protection system will be provided
including fire detection in buildings and a fire water distribution piping and hydrant network. As there is no municipal fire water system
in the Project Facility, fire water will be stored locally on site to support the plant fire water system. Local fire water pumps will
be provided and installed in accordance with National Fire Protection Association (NFPA) requirements.
| 18.5.5 | Stormwater
Management |
The collection and disposal of stormwater
on site will be managed in accordance with a comprehensive stormwater management plan which addresses both construction and operation
of the Project Facility. Surface water will generally be directed via ditches and culverts, utilizing natural grade on the site, towards
a sedimentation pond (which removes suspended solids) to be constructed along the east side of the site. Where process containment areas
are constructed, stormwater collected within the containment areas will first be tested prior to discharge and once deemed safe for discharge,
directed to the site sedimentation pond. The sedimentation pond will discharge to the east of the site, into the existing drainage which
currently receives surface runoff for the undisturbed site.
139 |
 |
RSI-3353 |
To support management of reservoir pressures
in the Smackover Formation and minimize surface waste streams, the Project has committed to the safe disposing of any excess effluent
brine and other process wastewater streams into the Hosston Formation using two redundant Class I Non-Hazardous UIC wells. Each
well will be permitted to dispose of up to 70 m3/hr of brine or wastewater on an individual basis or up to a maximum of 100
m3/hr on a combined basis.
A perimeter fence will enclose the Project
Facility with a minimum setback from the property boundary, providing a visual barrier into the facility. CCTV monitoring systems will
be installed throughout the facility and monitored by site security personnel on a 24-hour, 7-days-per-week basis.
Truck and vehicle access to process
areas of the facility will generally be restricted to essential activities and controlled by security personnel at the main gate house.
The secondary construction access gate, provided for construction and future maintenance activities, will be located on the east side
of the facility and will be either locally or remotely monitored.
Visitor access will be provided through
the administration building. Deliveries will be received directly at the Warehouse from outside the process plant to limit non-essential
personnel and vehicles inside the process plant.
Secondary security restrictions and
access control within the process facility will be provided to protect personnel and visitors and restrict unnecessary access to critical
process areas.
The plant telecommunications system
consists of a private high speed fiber optic internet service, a cloud-based PBX phone system, a plant wireless system, VHF/UHF radios,
a business LAN/WAN, and a process control LAN.
| 18.5.8.1 | Main
Internet Service |
A private high speed fiber optic internet
service is provided and continually monitored by the local internet provider to ensure high availability of internet service to support
cloud-based business and process applications. Critical business and process applications are hosted from local servers within the plant.
| 18.5.8.2 | Cloud
Based PBX phone system |
The PBX phone system is proposed to
be hosted in the cloud by a local telephone company.
| 18.5.8.3 | Plant
Wireless System |
A plant wireless system is provided
for a cohesive wireless communication platform across the physical and functional areas of the plant operations, enabling the wireless
network to support diverse applications such as connected worker and industrial internet of things (IIoT).
140 |
 |
RSI-3353 |
| 18.5.8.4 | VHF/UHF
Radio System |
Handheld VHF/UHF radios are provided
to plant operations and maintenance personnel as the main source of communications for managing day-to-day activities. The control room
will be provided with a VHF/UHF base station with an antenna to provide good radio coverage over the entire plant.
The business network consists of the
hardware and software infrastructure that connects the plant’s business computers, servers, and other devices, providing employees
with a connection to shared resources and access to internal and external applications.
The LAN infrastructure supports the
connection to the plant’s local applications such as the card access system, the phone system, and the CCTV cameras. The cloud
infrastructure supports the connection to cloud hosted applications, such as the Corporate ERP, lab information system, and maintenance
management systems.
The main internet service terminates
in the business server room located in the administration building. The server room incorporates redundant servers to host local business
applications. On a power supply, hard drive or CPU failure, the redundant servers allow the business systems to run uninterrupted on
the backup server. On a plant power outage, the server room UPSs provide power to the redundant servers and other critical networking
equipment for a period of time, to allow for the operation and controlled shutdown of the systems. The business applications run in virtualized
containers on the server to allow for easier administration and upgrades of the software. Daily backups of the business applications
are automatically stored offsite in cloud storage. A disaster recovery procedure ensures quick recovery of the business systems in the
event of a catastrophic failure.
The business network will be distributed
throughout the plant via remote network cabinets installed in other buildings and in the field. Each network cabinet will house managed
network switches used to connect business end devices such as desktop computers, printers, CCTV cameras, desktop phones, wireless ethernet
access points, card access readers, and truck scale operator panels. The managed network switches use virtual Lans (VLANs) to separate
the business network traffic to allow the traffic to be optimized based on the application.
The enterprise network security is designed
and implemented using best practice standard ISO/IEC 27001 Information Security, Cybersecurity and Privacy Protection.
| 18.5.8.6 | process
Control lan |
The process control LAN consists of
the hardware and software system used to control and monitor the process equipment running within the plant. The process control LAN
provides the communication link between control equipment such as DCS controllers, remote IO junction boxes, motor starters, VFDs, process
analyzers, operator consoles, data historians, and alarm management systems.
For security of process control equipment,
the process LAN is physically isolated from the business LAN. The process control LAN is designed and implemented using best practice
standards ISA/IEC62443 Security for Industrial Automation and ISA95 Enterprise Control System Integration.
141 |
 |
RSI-3353 |
| 18.6 | LANXESS
Constructed Improvements |
The purpose of the LANXESS constructed
improvements is to support the supply and disposal of Feed Brine to and from the Standard Lithium facility. The scope and schedule for
LANXESS Constructed Improvements is addressed in the SARL Agreement and will be further defined in the definitive Brine Agreement between
LANXESS and the Project Company.
It is currently proposed that LANXESS
will construct four (4) new buffering and mixing tanks downstream of their bromine tower Tail Brine surge tank to facilitate improved
chemical conditioning of the Feed Brine to ensure the brine meets the required quality conditions prior to delivery to the Project. These
agitated tanks will have the ability to receive both bromine-depleted brine, which has been processed through the LANXESS bromine tower,
and bromine-rich brine, which bypasses the bromine extraction facility. The Project is designed to extract lithium from both bromine-depleted
or bromine-rich Feed Brine. The Project will construct the pipelines and pumps from the outlet flange of the new LANXESS constructed
tanks required to deliver the Feed Brine to the Project Facility.
Following lithium extraction, the Project
will pump the lithium-depleted brine back to the bromine processing area where it will be discharged into a new LANXESS-constructed effluent
brine tank to facilitate gravity discharge into the existing LANXESS Tail Brine and disposal system for reinjection back into the Smackover
Formation. The Project will be responsible for delivering the lithium-depleted brine to the inlet flange of the new LANXESS constructed
effluent brine tank.
Figure 18-5. Project Brine Pipeline
Network
142 |
 |
RSI-3353 |
| 19.0 | Market
Studies and Contracts |
The lithium market is in a period of
transformation because of the supply and demand response from a global demand in 2010 of less than 100k metric tons (Mt) of lithium carbonate
equivalents (LCEs) to a demand in 2020 of more than 300k Mt LCE. Battery-related use accounts for approximately 60 percent of the market,
driven in part by the growing demand for electric transportation, predominantly electric vehicles (EVs).
By 2030, demand may exceed 3,000k Mt
with more than 90 percent of use related to lithium-ion batteries in electric transportation and energy storage. Considering the time
it takes for greenfield lithium projects to be developed and come into production, the demand will likely outstrip supply for the remainder
of the decade.
The consulting company McKinsey &
Company forecasts lithium-ion battery cell demand to grow from 700 gigawatt hours (GWH) in 2022 to 4,700 GWH in 2030, as shown in Figure
19-1. Each terawatt hour (1,000 GWH) requires a minimum of 800k Mt of LCE.
Figure
19-1. Global Lithium-Ion Battery Cell Demand, GWh, Base (after McKinsey & Company
2023).
143 |
 |
RSI-3353 |
The world’s largest lithium producer,
Albemarle, forecasts a similar demand pattern for LCE growth shown in Figure 19-2. The lithium use aligns well with the forecast in Figure
19-1.
Figure 19-2. Forecasted Lithium
Demand (Albemarle, 2023)
Asia is expected to remain the largest
market for lithium chemicals for the remainder of the decade. China currently has 70 percent of lithium-ion battery cell production capacity
and will remain the largest single market for EVs into the next decade. Korea and Japan are also significant battery producers.
North America is expected to become
the second-largest market for lithium chemicals by the end of the decade. U.S. legislation has taken several steps to support growth
of the domestic electric vehicle (EV) market and a North American battery supply chain.
The American Jobs Plan proposed $174
billion of investments to support development of the U.S. EV market by doing the following:
/ Providing
tax credits for EVs worth up to $7,500 for a new EV and $3,750 for a used EV
/ Expanding
access to charging stations with a goal of installing 500,000 new EV chargers by 2030
/ Setting
an ambitious goal of 50 percent of U.S. automobile sales being EVs by 2030
The European Union is supporting the
growth of lithium-ion batteries through their “Green Deal” with a stated objective of making Europe the first carbon neutral
continent by 2050.
144 |
 |
RSI-3353 |
Lithium-ion batteries are anticipated
to play a central role in the global energy transition. Ensuring adequate supply of lithium chemicals to support the growth of batter
demand is becoming a global concern. The Project is well positioned to support the growth in demand for lithium chemicals in North America
and other world markets.
| 19.2 | Lithium
Supply and Demand |
The supply of lithium chemicals is expected
to remain constrained for this decade and perhaps longer with demand outpacing supply. Lithium for use in batteries remains a specialty
chemical rather than a commodity because of the raw material specifications required for EV batteries.
Advisory firm Global Lithium LLC’s
supply and demand forecast is shown in Figure 19-3. It is more conservative than demand shown in Figure 19-2, predicting a 2030 demand
of approximately 3,000k Mt LCE versus Albemarle’s forecast of 3,700k Mt. Although the supply line appears in relative balance with
demand in some years, consumers may have difficulty sourcing qualified product in adequate volumes maintaining upward price pressure.
Figure 19-3. Lithium Supply and
Demand Forecast (McKinsey & Company, 2023)
The two fastest growing lithium chemicals
sectors are expected to be battery quality lithium hydroxide (lithium hydroxide monohydrate) and lithium carbonate. Types of resources
that provide a source of lithium include hard rock (spodumene), brines and clay deposits. Lithium chemical supply from recycling is not
anticipated to be a significant source at this time.
145 |
 |
RSI-3353 |
Lithium hydroxide is primarily used
in longer range EV batteries requiring high nickel content while lithium carbonate is favored in lower capacity, less expensive EV batteries,
electric buses, and energy storage systems. Figure 19-3 shows a relatively even balance of lithium carbonate and lithium hydroxide demand
by 2030.
Lithium carbonate produced from brine
sources is almost universally lower cost than the output from hard rock assets, giving brine-based sources a competitive advantage if
market conditions move to an oversupply situation.
Currently, Western Australia is the
largest global source of lithium supplying more than 40 percent of the total in 2022, mostly in the form of spodumene concentrate
converted in China to lithium chemicals. Over the next several years, Australia is expected to convert significant volumes of their spodumene
into lithium chemicals, causing China to seek feedstock elsewhere.
Chile is the second largest lithium
producer, supplying approximately 30 percent of LCEs globally in 2022. China is the largest producer of lithium chemicals globally, sourced
from imported feedstock.
| 19.3 | Lithium
Carbonate Price |
Since 2021, the price of lithium has
shown volatility from lows of $10,000 USD/tonne to a peak of $70,000 USD/tonne. The global average price from 2016 to early 2023 by month
is shown in Figure 19-4. Several hard rock mines in Western Australia came online in 2018 and 2019, leading to a temporary oversupply
situation and causing the price to fall below $5,000 USD/tonne. In late 2020, EV growth in China and Europe shifted the market back to
a shortage situation.
146 |
 |
RSI-3353 |
Figure 19-4. Global Weighted
Average Lithium Carbonate Price From 2016 to Q1 2023 (source, https://tradingeconomics.com/commodity/lithium)
Global Lithium LLC estimates that average
large-contract pricing will remain between $50,000 and $60,000 USD/tonne through 2030 based on the assumption that demand will exceed
battery quality supply until at least the early 2030s. The price forecast in Figure 19-5 shows multiple price scenarios, including an
average of the price forecasts of three major investment banks, the projection of China spot price by Benchmark Mineral Intelligence,
with pricing considerations in an oversupply situation and the price if the high-cost facility production was curtailed.
For purposes of estimating new project
future cash flows, Global Lithium LLC recommended a conservative approach using the forecast high end of the cost curve. Although Global
Lithium LLC forecasts global pricing well above the grey line in Figure 19-5, using a conservative price is recommended in case of unforeseen
market circumstances. From 2031 to 2036, Global Lithium recommended using a price of $30,000 USD/tonne for economic evaluations.
147 |
 |
RSI-3353 |
Notes:
[1] Contract Average is the ex-China
average price per Global Lithium LLC estimates
[2] Cost Curve reflects the China hard
rock converter cost
[3] IB Average is the ex-China price
average from three major investment banks
[4] China spot price
Figure 19-5. Battery Quality
Lithium Price Carbonate Scenarios 2023-2030
| 19.4 | LANXESS
Memorandum of Understanding and Offtake Option |
Under the terms of an Amended and Restated
MOU, dated February 23, 2022, between Standard Lithium and LANXESS Corporation, LANXESS was given the right to purchase and take
from the Project up to 100% of the product.
In the event LANXESS desires to exercise
this right, the parties are obligated to reasonably and in good faith negotiate the terms and conditions a definitive offtake agreement
and use commercially reasonable efforts to cause the execution and delivery of such agreement by a date set forth in the MOU.
In the event LANXESS participates as
an equity investor in the Project and is entitled to customary dividend, distribution or similar rights, the price under such offtake
agreement for the market price less a handling fee. In the event that LANXESS does not participate as an equity investor in the Project
or shall not enjoy customary dividend, distribution or similar rights, the price under such offtake agreement is established at the market
price minus a discount up to 20%.
148 |
 |
RSI-3353 |
| 20.0 | Environmental
Studies, Permitting, and Social or Community Impact |
| 20.1 | Environmental
Regulatory Setting |
The Project Facility is situated in
southern Union County, Arkansas, adjacent to developed chemical manufacturing facilities operated by LANXESS and The Chemours Company.
The site is in a rural unincorporated area of Union County and not subject to local planning or zoning restrictions or any local permitting
authority.
The environmental regulatory programs
applicable to the Project Facility are administered by the U.S. Army Corps of Engineers (USACE), the Arkansas Department of Energy &
Environment, and the Arkansas Department of Health (ADH). Those agencies have been delegated authority from the U.S. Environmental Protection
Agency (EPA) for permits and approvals required for operation of the Project.
The Project Facility relies on the existing
brine supply and disposal infrastructure associated with the LANXESS South Plant. After extraction of lithium from the brine, the majority
of the lithium depleted brine will be returned to LANXESS for reinjection into the Smackover using the existing network of brine disposal
pipelines and injection wells. Any excess volumes of lithium depleted brine will be managed and disposed of by Standard Lithium through
two new injection wells to be permitted and constructed specifically for the Project.
No amendment to the existing LANXESS
brine supply and disposal permits issued by the ADEE-AOGC are anticipated as a result of the Project. An amendment to the existing LANXESS
ADEE-DEQ No Discharge Permit associated with the existing brine disposal surface infrastructure is required. Amendment of permits issued
to LANXESS remains the responsibility of LANXESS as the permit holder. Excess brine, byproducts, wastes, and emissions not transferred
to LANXESS will be addressed through permits issued directly for the Project as described below.
| 20.2 | Permits
and Authorities |
The Project has been evaluated to determine
the specific permits necessary to construct and operate the facility and supporting infrastructure. Based on the evaluations completed
to date, the Project is not subject to review under the National Environmental Policy Act (NEPA). Construction and operational emissions
to air, surface waters, and subsurface waters are regulated by the federal and state agencies to protect the environment while allowing
responsible development of the lithium resources.
Standard Lithium has initiated early
consultation with permitting agencies for the construction and operation of the Project. A Baseline Environmental Site Assessment has
been conducted as well as investigations of jurisdictional waters of the U. S., wildlife studies, and cultural resources of the Project,
as discussed in Sections 20.6, 20.7 and 20.8, respectively.
149 |
 |
RSI-3353 |
Federal agency permitting required for
the Project is limited to authorization from the USACE Vicksburg District for placement of dredged or fill material into waters of the
U.S., including wetlands. Section 404 permits refer to that division of the Clean Water Act (CWA) to protect wetlands and jurisdictional
waters of the U.S.
The area of development associated with
the Project Facility has been assessed to identify jurisdictional waters of the U.S. The area designated for development will impact
jurisdictional waters and a Nationwide Permit (NWP-39) will be required for construction of the Project Facility.
The EPA has delegated responsibility
for most of the regulatory programs under its jurisdiction to the Arkansas Department of Energy & Environment, Division of Environmental
Quality (ADEE-DEQ) including programs under the CWA; Clean Air Act (CAA); Resource Conservation and Recovery Act (RCRA); Comprehensive
Environmental Response, Compensation, and Liability Act (CERCLA); Underground Injection Control (UIC); and the Superfund Amendments and
Reauthorization Act (SARA). Additionally, the Arkansas Department of Energy & Environment, Oil and Gas Commission (ADEE-AOGC)
is the permitting authority for construction of drilling fluid temporary holding basins associated with drilling of the UIC injection
well permits.
The ADEE-DEQ has primacy in issuing
relevant environmental permits for the construction and operation of the proposed lithium extraction facility. Ancillary activities to
support the manufacturing operations, specifically development of a non-transient non-community public water supply is authorized by
a permit issued by the ADH. The list of identified permits necessary and the respective issuing agency is provided in Table 20-1.
150 |
 |
RSI-3353 |
| 20.3 | Construction
and/or Operation Permits |
New permits required to accommodate
the Project Facility are provided in Table 20-1. A brief discussion of each approval required for construction and/or operation is provided
below.
Table 20-1.
Permits for Project
Agency |
|
Permitted
Activity |
|
Expected
Permit
Issuance Time |
USACE |
|
Placement of fill in waters
of the U.S. |
|
6 months |
ADEE-DEQ |
|
Air Permit for Commercial
Facility |
|
9 months |
ADH |
|
Fresh Water Supply for
Potable Water |
|
9 months |
ADEE-DEQ |
|
Construction Storm Water
NPDES Permit for Facility Construction Site |
|
1 month |
ADEE-DEQ |
|
Surface Discharge of Non-Brine
Process Wastewater, Non-contact Cooling Water, Treated Sanitary Wastewater |
|
12 months |
ADEE-DEQ |
|
Construction of Treatment
System Associated with a NPDES Permit |
|
12 months |
ADEE-DEQ |
|
Stormwater Discharges
from a Categorical Industry |
|
1 month |
ADEE-DEQ |
|
Construct/Operate Surface
Facility for New Class I Nonhazardous Injection Wells |
|
9 months |
ADEE-DEQ |
|
Construct/Operate New
Class I Nonhazardous Injection Wells |
|
12 months |
ADEE-AOGC |
|
Construct Drilling Pit
for Class 1 Nonhazardous Injection Wells |
|
1 month |
ADEE-DEQ |
|
Transfer Barren Brine
to LANXESS No-Discharge Permitted Facility |
|
9 months |
| 20.3.1 | CWA
SECTION 404 – Nationwide Permit 39 |
Section 404 of the Clean Water
Act established a statutory mechanism for control of dredged or fill material into waters of the U. S., including wetlands. The USACE
has final administrative authority to determine the status of land surface as jurisdictional waters. Currently, certain land characteristics
are scientifically used as indicators of waters through a process known as a Jurisdictional Determination (JD). Private entities commonly
prepare and submit JD reports to the USACE to expedite their decision-making process and in some cases, the USACE will conduct a site
survey to confirm the private JD or absent a private submittal, to provide the basis for the agency’s permitting decision. Construction
of the Project Facility includes placement of fill in an area and diversion of a small creek that a field investigations deemed to be
waters of the U. S. Thus, Standard Lithium will be required to obtain a Section 404 permit for the proposed activity.
USACE authorizes impacts to WOTUS through
nationwide or individual Section 404 permits. Nationwide permits are structured for specific activities and minimal impacts and
do not require lengthy agency review. The Project Facility will be subject to NWP 39 – Commercial and Institutional Developments.
Nationwide permits mandate compensatory
mitigation for impacts to waters of the U.S. Mitigation is commonly satisfied through purchase of wetlands credits from a USACE-recognized
mitigation bank. Once the Section 404 permitting process is initiated, the USACE will determine the degree of compensatory mitigation
(if any) and institute a review of threatened/endangered species and cultural resources that may be impacted by the Project Facility.
151 |
 |
RSI-3353 |
| 20.3.2 | Minor
Source Air Permit |
The ADEE-DEQ, Office of Air Quality,
issues new permits for proposed facilities after reviewing and evaluating permit applications for administrative and technical completeness
and ensuring that each application meets regulatory adequacy, as required by Title V of the CAA. It is a legally enforceable document
designed to improve compliance by clarifying what facilities (sources) must do to control air pollution. ADEE-DEQ has primacy for the
issuance of permits and regulation of air emissions sources in Arkansas.
A single permit will be issued by ADEE-DEQ
for construction and operation of the facility. The permit must be in place prior to initiating construction, including preparation of
foundations for any air emission source.
Emissions estimates for the Project
Facility have been developed using engineering calculations and preliminary equipment specifications. Based on the emissions estimates,
the operation will be required to obtain a Minor Source permit, and an application for the new facility must be reviewed and approved
by the ADEE-DEQ. The permit application will include a review of the applicability of federal rules for specific sources. The ADEE-DEQ
has authority to issue a permit with federally enforceable conditions and limitations. The permit conditions and limitations will be
developed by ADEE-DEQ to prevent deterioration of ambient air quality and to comply with State and National Ambient Air Quality Standards
or with other applicable regulations.
| 20.3.3 | Public
Water Supply |
The ADH issues approvals for Public
Water Systems serving non-municipal potable water. The Project will require fresh water sources to support the lithium extraction process
and provide potable for personnel use. There is no municipal water system in the vicinity of the project. Currently, the adjacent LANXESS
South Plant has fresh water extracted from an underground source (Sparta Aquifer) approximately 275 m (900 feet) to 500 m (1,640 feet)
but does not have sufficient excess capacity to support the Project.
Standard Lithium expects to drill and
construct two Sparta Aquifer fresh water supply wells. Fresh water produced by the wells will be disinfected, stored, and distributed
following ADH rules. Following submission of engineering design and construction plans and specifications that meet ADH standards, the
ADH will issue a Noncommunity Public Water System permit for the non-transient, non-municipal water system supplying potable water to
the Project Facility.
| 20.3.4 | NPDES
Construction Stormwater Discharge |
The ADEE-DEQ, Office of Water Quality
has been delegated authority by the EPA for administration of the NPDES permit program in accordance with the federal CWA.
The ADEE-DEQ, Office of Water Quality
has issued a general permit for discharges of stormwater runoff from construction (earthmoving) activities. General permits are developed
for multiple facilities that have similar activities and limitations. The objective of permit ARR150000 is to eliminate or reduce the
transport of sediments and construction-related contaminants from earthmoving and construction activities that disturb 1 acre or more
area. As the Project Facility development will exceed 5 acres, a Stormwater Pollution Prevention Plan (SWPPP) specific to the construction
site must be prepared and submitted to ADEE-DEQ along with a Notice of Intent for coverage under the general NPDES permit. The SWPPP
includes management practices and physical controls to minimize sediment/contaminant transport off the construction area as a result
of precipitation events. Once authorized, the permit is in effect until the disturbed area is stabilized after construction is completed.
The current permit ARR150000 was effective November 1, 2021, and expires October 31, 2026.
152 |
 |
RSI-3353 |
| 20.3.5 | NPDES
Non-Brine Process Water Discharge |
The ADEE-DEQ, Office of Water Quality
regulates discharges of non-brine process-related effluents from industrial operations and sanitary or domestic wastewater through the
NPDES permit program. Process effluent includes any water that, during manufacturing or processing, comes into direct contact with or
results from the production or use of any raw material, intermediate byproduct, finished product, byproduct, or waste product. An individual
NPDES permit will be required for non-brine effluents from the Project Facility that are discharged to surface waters. Tail-brine is
prohibited from discharge to surface waters and must be disposed subsurface in UIC Class I or V injection wells.
An individual NPDES permit application
includes information on the processes generating the effluent, treatment (if any) of the effluent before its discharge, an actual or
predicted pollutant characterization of the effluent, and a schematic diagram depicting the mass flow of water through the facility before
its discharge. Administrative information on the Project Facility will be included and the application must be signed by a Responsible
Official. Individual NPDES permits are issued with 5-year expirations and must be renewed 180 days before the expiration date.
| 20.3.6 | State
Construction Permit for Wastewater Treatment |
The ADEE-DEQ, Office of Water Quality
requires a Construction Permit for industrial treatment and collection facilities that discharge treated effluent to a surface water
as permitted by an individual NPDES permit. A Construction Permit will be necessary for the Project Facility. The Construction Permit
is a state-only permit and is required to ensure that treatment systems proposed comply with the applicable provisions of the “Recommended
Standards for Wastewater Facilities” by the Great Lakes – Upper Mississippi River Board of State and Provincial Public Health
and Environmental Managers, commonly known as “The 10 States Standards.” The Construction Permit is an add on to the individual
NPDES permit application submitted by an Arkansas Professional Engineer and is in effect until the treatment system is completed and
operational. Construction in accordance with the issued permit must be certified by an Arkansas Professional Engineer at the completion
of construction.
| 20.3.7 | NPDES
Stormwater Discharges from Categorical Industry |
Stormwater runoff discharges from certain
industrial categories are regulated by the ADEE-DEQ Office of Water Quality in the NPDES program using a multi-sector general permit.
The Project Facility will require the general stormwater permit for operation and is included in Sector J3: Mineral Mining and Dressing,
Chemical and Fertilizer Mineral Mining. Standard Lithium will submit a Notice of Intent to ADEE-DEQ to request coverage under the industrial
general stormwater permit.
153 |
 |
RSI-3353 |
The industrial general permit ARR000000
for stormwater runoff discharges from industrial sites has requirements similar to the general permit for construction stormwater discharges
(ARR150000) that emphasize pollution prevention and best management practices. A SWPPP must also be prepared specific to the operational
site. Discharges of storm runoff from the area of industrial activity must be sampled, analyzed, and reported to ADEE-DEQ annually. ADEE-DEQ
has established benchmark values for pH and Total Suspended Solids (TSS) in stormwater discharges from industrial Sector J3. The benchmark
for pH is a range from 6.0 S.U. to 9.0 S.U. and for TSS is 100 mg/l, The benchmark concentrations are established to alert facilities
and the ADEE-DEQ of potential exposure to industrial materials or processes, and to provide the facility opportunity to implement new
or amend existing management practices to reduce the parameter of concern.
| 20.3.8 | State
No-Discharge Permit |
The ADEE-DEQ regulates waste disposal
systems that do not discharge to surface waters through a “No-Discharge Water Permit”. The State No-Discharge Permit (ADEQ
NDSP) is required for the storage tanks and ancillary equipment associated with disposal of effluent brine in the two proposed Class I
injection disposal wells. The intent of the ADEQ NDSP is to allow ADEE-DEQ the opportunity to review and approve the waste handling process
and equipment with regard to good engineering practices to prevent unauthorized discharges to surface waters. The ADEQ NDSP application
must be prepared and submitted by an Arkansas Professional Engineer.
| 20.3.9 | Underground
Injection Control Permit |
The Project will use two distinct paths
for management of lithium-depleted (barren) brine from the lithium extraction process. The majority of the brine will be returned to
the LANXESS South Plant for injection in the existing Class V wells and the remainder (excess over volume) will be injected into
two new Class I Non-hazardous wells owned and operated by Standard Lithium. For the brine returned to LANXESS, refer to Section 20.4.
The ADEE-AOGC issues Class V Permits
for brine injection wells. Disposal of barren brine processed through the Project Facility using the existing LANXESS brine disposal
well network does not require modification of the existing ADEE-AOGC permits held by LANXESS as the injectate is still considered
“spent brine” and the lithium-depleted brine remains consistent with fluids permitted for injection into the Class V
wells. Class V well authorizations do not expire until a well is permanently plugged and abandoned.
Class I wells are used to inject
non-hazardous waste into deep, confined rock formations. The Class I well target depths for the two new Hosston Formation wells
in this project range from 1,151 m (3,775 feet) to 1,646 m (5,400 feet) below ground level elevation. Class I wells are strictly
regulated under the Resource Conservation and Recovery Act (RCRA), and the Safe Drinking Water Act (SDWA). The Project is preparing and
will submit an application for the two required UIC Class I wells. Class I permits are issued with 10-year terms and applications
for renewal must be submitted before the expiration date.
| 20.3.10 | Resource
Conservation and Recovery Act Subtitle C Treatment, Storage, and Disposal Permit |
A RCRA Hazardous Waste Permit is required
of any facility that performs treatment, storage (greater than 90 days), or disposal of waste meeting the criteria to be classified as
hazardous. The Project Facility will not conduct any of the activities requiring a RCRA permit authorization. Process wastes generated
by the facility are not expected to meet the hazardous classification. Small quantities of universal wastes (e.g., batteries, pesticides,
mercury-containing equipment, lamps, electronics, and aerosol cans) may be generated by the operation and maintenance of the site. Title
40 Code of Federal Regulations, Part 273 provides an alternative set of management standards for universal wastes in lieu of regulation
as hazardous waste.
154 |
 |
RSI-3353 |
New permits required to accommodate
the Project Facility are listed in Table 20-1. An existing State No-Discharge Permit issued to LANXESS for surface equipment associated
with disposal of barren brine must be modified to include the Project Facility. Information regarding the permit is noted in Table 20-2.
Table 20-2.
Permits for LANXESS South Plant to be Modified
Permit,
Application,
or Reference Number | |
Activity | |
Construction
or Operation | |
| Agency | | |
Permit/Plan |
ADEQ PERMIT 5048-WR-2 | |
Transfer Barren Brine to LXS for Smackover
Injection | |
Operation | |
| ADEE-DEQ
| | |
Modify LXS State No-Discharge Permit
5048-WR-2 |
Permit 5048-WR-2 is a State No-Discharge
Permit issued by ADEE-DEQ to LANXESS for operation of the brine disposal system (tanks, equipment, pipelines) associated with the UIC
Class V injection well network. The narrative description and flow schematic diagram of the permit must be revised to include brine
diverted to and returned from the Project Facility. The permit modification request will be initiated by LANXESS and supported by the
Project.
| 20.5 | Environmental
Liabilities |
The construction of the Project Facility
has the potential to cause conditions which may create minor environmental liabilities through the discovery of improperly abandoned
oil/gas wells, permanent closure/abandonment of existing LANXESS ground water monitoring wells within the construction area, and potential
off-site transport of sediments because of improper or inadequate erosion control measures.
The Project Facility is included in
a portion of the historical El Dorado South oil/gas field, which was discovered in 1922. The El Dorado South field is mostly depleted
with a few “stripper” wells operated by independent producers remaining. An August 1957 historical field map of El Dorado
South used by the ADEE-AOGC to indicate the location of producing and abandoned wells shows three possible abandoned well locations within
the Project Facility boundary. ADEE-AOGC plugging and abandonment records for the period from 1922 to 1957 were researched but unsuccessful
in identifying any documents regarding drilling, operation, or abandonment of the three wells. A field investigation of the mapped well
locations did not indicate the presence of historical oil production or of any wellbores, and it is presumed the wells, if actually constructed
within the boundary of the construction areas, were plugged and abandoned properly. If evidence of wellbores is discovered during construction,
the ADEE-AOGC will be notified and further investigation conducted as to the plugging status of the well. The potential liability for
improperly abandoned wells remains with the original permit holder. The ADEE-AOGC has a fund for plugging improperly abandoned wells
for which ownership cannot be established. Any well discovered on the subject property would be eligible for public funding of the closure
action, if required.
155 |
 |
RSI-3353 |
Monitoring wells owned and operated
by LANXESS South are located within the proposed construction area of the project. If required, the wells will be plugged and abandoned
in accordance with accepted groundwater protection measures; where possible existing wells will be maintained to allow for ongoing groundwater
monitoring by LANXESS.
Earth disturbance during the construction
of the facility will require preparation of a SWPPP in accordance with ADEE-DEQ NPDES Permit ARR150000 requirements discussed in Section 20.3.3.
The SWPPP and other permit conditions are established to prevent transport of sediments off site during construction.
Any additional environmental liabilities
discovered during the course of construction or operation, and which are determined through investigation to be a result of pre-existing
conditions, will remain the responsibility of LANXESS as lessor of the Project properties, the permit holder in the case of abandoned
wells.
| 20.6 | Environmental
Baseline Studies |
A Baseline Environmental Site Assessment
(ESA) was conducted from November 2022 to March 2023 on property proposed to be leased from LANXESS for the construction of
the Project Facility. The assessment was conducted to determine if historical activities and processes on the property or adjacent properties
have impacted surface and subsurface soil and water quality, and to document the pre-construction conditions of the site prior to alterations
associated with the Project Facility. Field investigation activities included collecting representative samples of subsurface groundwater
and soil, surface stormwater and soil, and vegetation for chemical analysis. The investigation was based upon the best judgment of the
environmental professional in consideration of the proximity of chemical manufacturing operations and historical oil/gas production in
the area. The data collection was completed in accordance with standard operating procedure for quality assurance/quality control (QA/QC)
consistent with EPA guidance.
| 20.6.1 | Subsurface
– Groundwater |
The adjacent LANXESS chemical manufacturing
operation has an established network of groundwater monitoring including wells on the Project Facility site. LANXESS groundwater monitoring
wells are completed in the uppermost saturated zone less than 200 feet below ground surface. On November 28, 2022, two new permanent
groundwater monitoring wells were installed by Standard Lithium on the Project Facility site. Well MGW-1 is located on the northern boundary
of the subject property, east of the LANXESS South Plant entrance parking lot. Ground water monitoring well MWG-2 is located centrally
on the site. Both groundwater wells were completed in the uppermost saturated zone equivalent in depth to the nearby LANXESS monitoring
wells
From January 26 to February 2,
2023, 12 existing wells and the two newly installed wells were sampled using low-flow purging and sampling procedures. Water collected
from the individual wells was sealed in appropriate sample containers and transported to the analytical laboratory. Samples were analyzed
for sulfate, ammonia-nitrogen, nitrate-nitrogen, nitrite-nitrogen, hexavalent chromium, mercury, lead, zinc, barium, dioxins, non-pesticide
organic compounds, RCRA characteristic hazardous waste parameters, adsorbable organic fluorine, halogens, major cations and other substances
of potential interest. Three metals (mercury, barium, and manganese) and one halogen (chloride) were observed above health risk-based
concentrations or primary drinking water maximum contaminant levels in some of the LANXESS monitoring wells.
156 |
 |
RSI-3353 |
In addition to the sampling performed
January-February 2023, LANXESS provided historical groundwater information for the existing wells on the Property including analytical
results of previous monitoring. As a result of historical operations at the LANXESS South facility, there is known subsurface contamination
of chemical manufacturing-related constituents (e.g., chlorides, bromoform, methylene chloride, 1-2-Dichloroethane [EDC]). Groundwater
collected during the baseline study further confirmed that there are contaminants in shallow groundwater at the proposed Project Facility.
This pre-existing contamination is associated with documented historical releases from the LANXESS South Plant and is routinely monitored
by LANXESS as the responsible party. Construction and operation of the Project Facility will not expose or impact the contaminated shallow
groundwater thus no preventive or remedial action is required by Standard Lithium.
Soil core sampling was conducted during
the installation of MWG-1 and MWG-2, consisting of two borings at three different depths for a total of six core samples. Core sampling
was conducted at surface level (0 to 4 ft) and at or directly above the saturated zone. Soil core samples submitted for laboratory analysis
for MWG-1 included those taken at depths of 0 to 2 ft, 2 to 4 ft, and 55 ft. Samples of borings at 0 to 2 ft, 2 to 4 ft, and 40 to 42
ft were selected at MWG-2. Samples were analyzed for Total Recoverable Metals, VOCs, SVOCs, and halogens,.
Arsenic was detected at concentrations
greater than health risk-based screening levels in all six soil cores. Selenium was detected from near-surface cores (0 to 4 ft subsurface)
at both well locations was greater than health risk-based screening levels. Mercury and methylene chloride were detected from the soil
core immediately above the saturated zone (42 to 44 ft subsurface) in MWG-2 exceeded the health risk-based screening levels for those
analytes.
Arsenic is a naturally occurring heavy
metal with documented background concentrations in the state of Arkansas. The core samples exceeded the EPA screening concentrations
for arsenic; however, the arsenic concentration was well below the ambient background concentration of 9.7 mg/kg (Shacklette, 1984).
The detection of arsenic can be assumed to be naturally occurring and not the result of industrial activities in the vicinity of the
Property. Metals mercury and selenium detected at various depths may be present as a result of adjacent operations or as naturally occurring
elements in the soil. However, the organic chemical methylene chloride observed above EPA screening levels in MWG-2 is presumed present
because of historical industrial operations as discussed in 20.6.1.
Metals observed in shallow (0-4 feet)
soil cores may be disturbed during construction and operation of the Project Facility. Exposure to and transport of soils at the Project
Facility will be mitigated by management practices and if necessary, engineering controls and are unlikely to impair the ability to construct
and operate the Project; no extraordinary measures are anticipated.
157 |
 |
RSI-3353 |
| 20.6.3 | Surface
– Stormwater |
Twelve individual locations for monitoring
stormwater run-on/runoff of the subject property were identified based on topographical features of the site. Locations included five
areas where stormwater runs on the property from the adjacent LANXESS South facility and seven monitoring locations where stormwater
leaves the subject property.
Stormwater samples were collected during
three events (January 24, 2023, February 14, 2023, and March 17, 2023) and analyzed for sulfate, ammonia-nitrogen, nitrate-nitrogen,
nitrite-nitrogen, hexavalent chromium, mercury, lead, zinc, barium, dioxins, non-pesticide organic compounds, RCRA characteristic hazardous
waste parameters, adsorbable organic fluorine, halogens, and major cations. Stormwater analyses did not exceed any health risk-based
screening concentrations at any location sampled.
Sediment sampling was conducted at each
of the stormwater monitoring locations between a depth of 0 to 6 inches subsurface in the drainage pathway. Samples were analyzed for
the Total Recoverable Metals, VOCs, SVOCs, and halogens. Surface sediment exceeded the screening concentration for arsenic at all sampling
locations. In addition, mercury was exceeded at multiple locations. Arsenic and mercury exceeded the EPA screening concentrations at
the site; however, background concentrations of the two heavy metals are known to be elevated in the region, with concentrations of 9.7
mg/kg and 0.067 mg/kg, respectively (Shacklette, 1984). All of the sample concentrations fell below the background concentrations, suggesting
that the detections of heavy metals in the soil are naturally occurring and are not caused by the industrial activity at the subject
or adjacent property.
Sediment samples collected at two run-on
locations and one runoff location exhibited concentrations of polycyclic aromatic hydrocarbon (PAH) compounds greater than health risk-based
screening levels. Detection of PAHs in sediments could be the result of historical oil production, forest management practices, or the
adjacent chemical manufacturing operations and at the concentrations observed do not present an elevated worker exposure risk for the
Project.
Detections of chemicals of potential
concern in sediments and shallow soils do not present an elevated worker exposure risk or likely active remediation potential based on
current regulations. Compound concentrations were screened against conservative risk-based concentrations and do not pose an appreciable
threat to personnel.
| 20.6.5 | Surface
– Vegetation |
Vegetation samples were taken to establish
baseline conditions and determine if air emissions from adjacent industrial operations may be affecting subject property vegetation.
On November 29, 2022, vegetation samples were collected in three separate locations at the Property. One pine tree at each monitoring
location was selected for collection of fresh pine needles from canopy height. Trees selected are estimated to have been approximately
40 ft tall and 6 to 8 inches in diameter. Pine needles from the canopy level branches were collected and analyzed for RCRA metals, and
halogens. Screening levels for vegetation are not available; therefore, analytical results were compared to soil screening levels. No
vegetation sample exceeded a health risk-based screening level for any parameter.
158 |
 |
RSI-3353 |
A threatened and endangered species
review was conducted for the Project Facility. The basis of the review was information obtained from the U.S. Fish and Wildlife Service
(USFWS) Information for Planning and Consulting (IPaC). Information provided through the IPaC review included a letter providing a list
of threatened and endangered species that may occur in the proposed project area and consistency letters for several of the species.
The consistency letters are developed after completion of determination keys in which several questions are answered to facilitate a
determination of potential effects the project may have on listed species. The IPaC reports are valid for 90 days as new information
obtained by the USFWS may result in changes to the list.
The Project Facility is located in an
area within the distribution range of one endangered and one proposed endangered bat, the northern long-eared bat (Myotis septentrionalis)
and the tricolored bat (Perrimyotis subflavus); four threatened/endangered birds—the eastern black rail (Laterallus jamaicensis
spp. Jamaicensis), the piping plover (Charadrius melodus), the red knot (Calidris cantus rufa), the red-cockaded woodpecker
(Picoides borealis); one proposed threatened reptile—the alligator snapping turtle (Macrochelys temminckii); one
candidate insect—the monarch butterfly (Danaus plexippus); and one endangered flowing plant—pondberry (Lindera
melissifolia).
The northern long-eared bat is primarily
distributed in northern and western Arkansas where caves are prevalent for winter hibernation. Their summer ranges extend out but are
still primarily confined to the northern and western parts of the state. During summer months northern long-eared bats roost in trees
containing suitable cover such as snags or loose/shaggy bark. The tricolored bat is similar in respect to primarily hibernating in caves;
however, these bats are known to be less selective in their roosting locations and tend to roost among leaves of deciduous hardwood trees.
The eastern black rail prefers a marsh habitat with dense cover. The piping plover is a shore bird that prefers areas devoid of vegetation,
typically sandy beach-type areas. The red knot is typically associated with ocean areas and depends heavily on horseshoe crab eggs to
sustain their long migration. The red-cockaded woodpecker is strongly tied to old-growth pine forests that burn frequently, leaving the
understory mostly clear of younger trees. The alligator snapping turtle prefers to inhabit the deeper beds of large rivers, canals, and
lakes. The monarch butterfly utilizes a variety of habitats but depends on milkweed for breeding. Pondberry is associated with wetland
habitats such as bottomland and hardwoods.
The IPaC multispecies determination
key resulted in a determination of no effect for the eastern black rail, piping plover, pondberry, and red knot. Based on the multispecies
key, the project may affect the red-cockaded woodpecker and would require further consultation with the USFWS to determine the effects.
The northern long-eared bat determination key resulted in a determination of no effect based on the finding that the project action would
not intersect an area where the northern long-eared bat is likely to occur. The determination keys do not cover species proposed for
listing as threatened or endangered (alligator snapping turtle, monarch butterfly, and tricolored bat).
The Project Facility lacks large waterbodies
or wetlands and would not likely support the alligator snapping turtle. Habitat for the monarch butterfly may exist in the vicinity of
the Property, however, milkweed plants were not observed in the project area during site visits. Guidance on distribution for the tricolored
bat and implementation of USFWS consultation is currently limited in Arkansas, but based on conversations with USFWS, the distribution
and consultation requirements are expected to mimic that for the northern long-eared bat.
159 |
 |
RSI-3353 |
The red-cockaded woodpecker preferred
habitat is very limited (old-growth pine forests). Union County is included in the known species range with some documented colonies
in the county. A desktop review of the Property shows that the area has historically been silvicultural land use, with pine being the
dominant tree species. Although pine has been a dominant species on site, it would not likely be classified as old-growth pine forests.
The project area also contains dense understory particularly in the areas including the oldest pine stands on the site. Additionally,
the USFWS ECOS website does not depict any known species locations within the project area. While impacts are not anticipated, consultation
with USFWS is suggested to confirm that the Project would not adversely affect the red-cockaded woodpecker.
The USFWS IPaC report also generated
a list of migratory birds of conservation concern. These are species identified by the USFWS that, without conservation efforts, are
likely to become candidates for listing under the Endangered Species Act. The only migratory bird listed on the IPaC repot is the chimney
swift (Chaetura pelagica). Chimney swifts breed in urban and suburban habitats and are most commonly found in areas with vertical
structures that provide nest site (e.g., chimneys). They can also nest in hollow trees, tree cavities, and caves. They primarily forage
over open areas, but are can be found foraging over forests, ponds, and residential areas. While potentially present, no hollow trees
were observed during the site visits nor is there a high likelihood for hollow trees to be present based on the current makeup of the
vegetative community. The proposed project will likely not have an adverse effect on the chimney swift.
Development of the Project Facility
will result in temporary and permanent disturbance to the existing habitat. However, no adverse impacts to the threatened and endangered
species or migratory birds listed are expected as a result of the Project. This assessment is contingent upon further consultation with
the USFWS regarding the red-cockaded woodpecker.
The Project Facility is located north
of US Hwy 167 in Union County, adjacent to the LANXESS South Plant and within Section 32 of T18S R15W and Section 5 of T19S
R15W. A desktop cultural review of the Project area was performed by Commonwealth Heritage Group on March 27, 2023. During the cultural
review, one archaeological site was found to be within a 0.8 km [0.5 mile] radius and two additional sites were within a 8 km [5 mile]
radius of the Project Site. The St. Marks Church and Cemetery, located 0.6 km [0.4 miles] southeast of the site, is part of the Union
County Historic Site Survey. The Smyrna Church and cemetery, located 3.1 km [1.9 miles] east of the Project Site, is also part of the
Union County Historic Site Survey. The Joel Smith Plantation, located 3.5 km [2.2 miles] northeast of the site, is listed on the Arkansas
Historic Preservation Program (AHPP) and is a National Register of Historic Places listed property. A further review of the AHPP shows
that no historical tracts are within the Project Site. A review of the General Land Office (GLO) plat map dating back to 1845 shows one
feature near the Property—the Pine Hill Road that runs north-south between the center of the sections reviewed (T18S R15W and T19N
R15W). A review of historical quadrangle maps shows that three or four structures (i.e., houses) were located within the subject property
prior to 1927. The structures were no longer present on a quadrangle map from 1951 and they do not exist today.
160 |
 |
RSI-3353 |
No previously recorded archaeological
sites or historic properties are located within the subject property of the proposed Project . Based on the desktop review the construction
of the Project should not result in any threat or loss to historic and cultural resources. This will be confirmed through USACE during
the Section 404 permitting process through agency consultation with the Arkansas Historic Preservation Program and Native American
Tribal groups with interest in the Project area.
Potential environmental impacts during
the construction, operation, and closure stages of the Project have been identified but not quantified in consideration of the global
effects of the Project. Those items are summarized as follows:
| / | Change
in local air quality from construction and operation of the facility |
| / | Removal
of existing forested areas on the site for construction and operation of the facility |
| / | Altered
stormwater runoff hydrology from land development activities and installation of impervious
surfaces for the operational facility |
| / | Increased
noise levels from the equipment, machinery and vehicles, and process operations |
| / | Increased
personal and transport vehicle traffic on county roads and state highways |
| / | Increased
light pollution from fixed lighting at the operational site |
| / | Increased
withdrawal of fresh water from the Sparta Aquifer via water supply wells drilled for the
operational facility |
| / | Increased
greenhouse gas (GHG) emissions from hydrocarbon combustion and extraction/processing equipment |
| / | Change
in water characteristics in Bayou DeLoutre and Walker Branch from operational stormwater
runoff |
| / | Reduction
of the usable life span of the Hosston Formation injection zone for waste disposal caused
by the addition of new injection wells/wastes |
| / | Reduction
of non-renewable natural gas reserves because of its consumption by the facility |
| / | Reduction
in GHG emissions as a result of replacement of petroleum fueled vehicles with electric vehicles
fueled by lithium batteries manufactured from Lithium Carbonate produced by the Project. |
| / | Increased
demand for electricity requiring potential increases in GHG emissions from power generation
facilities |
The potential direct environmental impacts
from construction, operation, and closure of the Project will be mitigated through compliance with rules and permits issued by ADEE-DEQ,
ADH, ADEE-AOGC, and other regulatory agencies. The potential indirect environmental impacts will be mitigated or offset by actions of
those entities directly responsible, such as public utility providers and government services.
161 |
 |
RSI-3353 |
Standard Lithium is committed to conducting
its future Project activities with best management practices and endeavors to maintain a collaborative relationship with the local communities
that the Project may impact. Engagement consists of regular community meetings as required; newsletters; and attendance at community
and business functions, and industry conferences.
The ADEE-DEQ permit process includes
public notices and the opportunity for community input on the regulatory approvals necessary for the Project. This includes oversight
for implementation of responsible environmental management; compliance reporting in accordance with approvals/permit conditions; consultation
regarding changes or updates to approvals; and compliance audits and inspections.
There is an opportunity for a positive
social impact on the surrounding communities. The community will benefit from the construction phase because the project will require
skilled labor and many contractors to complete. The community will also benefit with the additional opportunities for a labor market
skilled in similar operations once the facility has been constructed. Local businesses that supply goods and services to the Project
may also be uplifted by the influx of capital associated with construction and operation of the facility.
The construction phase of the Project
is approximately two years and will require an average of 200 workers and will include an overall payroll economic impact estimated at
approximately $22M. The workforce staffing for the continuous operation of the facility would begin approximately 6 months before the
completion of the construction phase. Standard Lithium estimates the continuous operation will require approximately 90 direct full time
employees ranging from high school/GED to MS level education with an average salary of $70,000/yr (Arkansas mean annual wage = $48,570)
(Bureau, 2022). The overall base salary economic impact is estimated to be between $6.3M and $7.0M per year. Currently over 80% of the
Demonstration Plant full-time team in Arkansas are local workers that live less than 120 kilometers (less than 75 miles) from the facility.
Standard Lithium has partnered with
South Arkansas College in El Dorado, Arkansas, for the new Catalyst Program, which is a collaborative effort between employer partners
and sponsors to provide free, pre-employment training for individuals interested in the chemical production and services sector (SouthArk,2023).
This 16-week program provides a great opportunity for local workers, including high school seniors and GED-level, to learn new skills
and advance their careers and ensures there is a short-term workforce development pathway that leads to high-wage careers. Standard Lithium
is fully committed to being a strong and supportive partner to the local community in southern Arkansas.
| 20.11 | Waste
Management/Disposal |
The Project Facility will generate a
small quantity of non-hazardous solid waste from the brine filtration and conditioning steps of the process. The solid waste is mainly
filter-aid (diatomaceous earth), insoluble impurities from soda ash and lime, precipitated hydroxides and inorganics from the Feed Brine
as well as undissolved calcium carbonate and magnesium hydroxide from the recycled softening sludge.
162 |
 |
RSI-3353 |
The waste streams amount to 1,000 to
1,800 tonnes per year and will be collected on site and transported to permitted disposal facilities. All waste container management
will be performed on paved or concrete surfaces within the Project Facility. The non-hazardous solid wastes will be moved via transport
truck to a land disposal facility licensed and permitted to accept the industrial wastes. The nearest ADEE-DEQ permitted waste disposal
facility is the Union County Landfill, approximately 15 miles north of the Project Facility.
| 20.12 | Environmental
Management and Closure Plan |
Environmental Management Plans to guide
compliance with the various regulatory programs and requirements will be developed following receipt of applicable construction and/or
operating permits from the state agencies. These plans will address the various aspects of the design, construction, commissioning, and
operation phases of the Project, identify the key environmental issues from the various Project phases, and provide plans and actions
that will be undertaken to manage the phases effectively.
A Closure Plan specific to the two new
Class I UIC wells will be submitted to and approved by the ADEE-DEQ through the permit application process. All other operations
of the Project are not subject to any state or federal formal Closure Plan requirement. The estimated cost of the closure fund related
to the Class I UIC wells is estimated at approximately $650,000. It is currently contemplated that a surety bond will be secured
(a condition of the permit) to provide the necessary assurances that the mine closure funding will be available at or prior to the conclusion
of operations of the wells.
Standard Lithium is committed to decommissioning
and restoring the Project Site when operations cease in the future. Process feedstock, liquids in vessels, reagents, finished products,
and ancillary materials will be removed to a proper use, recycling, or disposal facility. Solid residuals and nonhazardous solid wastes
will be transported off site to an appropriate permitted recycling or disposal facility. Small quantities of regulated hazardous wastes/universal
wastes accumulated during the operation and site termination activities will be transported to an authorized facility. Surface facilities
and equipment will be re-purposed or recycled where possible and where not possible, disassembled, scrapped and disposed of off-site
in accordance with applicable commercial obligations and relevant regulatory requirements.
163 |
 |
RSI-3353 |
| 21.0 | Capital
and Operating Costs |
Capital and Operating Costs for the
Project were prepared in accordance with the principles set out by the AACE International (Association for Advancement of Cost Engineering
International). The estimated costs are based on the engineering design completed for this study, supported by a combination of competitive
quotes and engineering estimates compiled using industry standard estimating practices and the experience of the Project team with similar
projects.
All dollars in the cost estimates are
in 2023 United States of America (USA or US) dollars unless otherwise noted. Major components are presented in tabular form. Numbers
stated are rounded such that differences may appear between individual and total values, or between tables.
The total capital cost (CAPEX), including
contingency, to construct the Project is estimated at $365 million. Direct project costs represent $259 million and indirect Project
Costs represent $56 million of the total cost. A contingency of $50 million is included, which equates to approximately 15% of direct
and indirect costs.
The capital cost estimate is considered
to have an accuracy range of -15% to +20%. All costs are expressed in 2023 US Dollars. No allowances are included for cost escalation.
The total estimated capital cost for
the Project by area is summarized in Table 21-1.
Table 21-1.
Project Capital Cost Estimate Summary
Area | |
$ M | |
Brine Delivery (Tie-ins) | |
| 9.0 | |
Brine Pretreatment | |
| 43.3 | |
Direct Lithium Extraction | |
| 38.1 | |
Concentration and Purification | |
| 53.3 | |
Carbonation | |
| 53.4 | |
Drying, Milling, and Packaging | |
| 18.9 | |
Effluent Brine Disposal | |
| 24.3 | |
Reagent Systems | |
| 8.8 | |
Utilities | |
| 51.1 | |
Other
(First Fills, Membranes, Licensing) | |
| 14.7 | |
Subtotal | |
| 315.0 | |
Contingency | |
| 49.9 | |
Total
CAPEX | |
| 364.9 | |
Notes:
[1] Any discrepancies in
the totals are due to rounding effects.
164 |
 |
RSI-3353 |
Figure 21-1. Project Capital
Estimate Component Breakdown
| 21.1.1 | Estimate
Methodology |
The capital cost estimate was assembled
based on costs established for each of the Project areas, following the area and cost breakdown structure developed for the Project.
The estimate is considered to be reflective of the design completed to date, the proposed EPC contracting strategy and considers the
anticipated construction schedule.
Estimated costs were established using
industry standard estimating practices and methodologies. The estimate is generally derived from:
| / | Material
and equipment vendor quotes |
| / | Supply
and installation quotes from contractors |
| / | Unit
pricing received from contractors, vendors and consultants |
| / | Equipment
factored cost estimates |
| / | Historical
pricing, rates or allowances based on experience with similar recent projects |
Quotations were obtained based on loose
shipped field erected materials, pre-assembled modules or turnkey design, supply and installation work packages.
Multiple quotations were obtained for
the majority of equipment and construction packages which were then tabulated, equalized, assessed, any gaps addressed and escalation
applied to adjust price to align with the estimate date. The most appropriate bid, not necessarily the lowest price bid, was selected
as the basis for the estimate. Unit pricing estimates were developed with supporting material take-offs based on design drawings.
For reference, equipment-factored estimates
are produced by taking the cost of individual process equipment, and multiplying the equipment cost by an installation factor to arrive
at a total installed costs. The installation factor, or total installed cost factor, includes subcontracted costs and direct labor costs
and materials and indirect costs associated with the installation of the equipment. Where used, project specific installation factors
are based on industry norms for US Gulf Coast installation. Where factored estimates were employed, the methodology followed Peters &
Timmerhaus 2003 (P&T 2003) methodology.
165 |
 |
RSI-3353 |
The capital cost estimate includes all
materials, equipment, and labor to construct the commercial scale lithium extraction plant required to produce an average 5400 tonnes
per annum of battery-quality lithium carbonate over the 25-year life of the Project.
Capital costs include direct, indirect
and associated owners costs associated with the Project which generally includes:
| / | Site
preparation, including temporary access roads. |
| / | Lithium
extraction plant, including technology licenses. |
| / | Brine
supply and return pipelines (to and from the South Plant). |
| / | Two
(2) new Underground Injection Wells. |
| / | Utility
tie-ins and upgrades such as electric, gas, and water. |
| / | Offices,
shops, laboratory and other site buildings and infrastructure. |
| / | Construction
labor and supervision, equipment including mobilization, contractors overhead and profit
and other construction expenses. |
| / | Design
engineering, permitting and environmental services required during construction. |
| / | Commissioning
and startup costs including first fills. |
| / | Owner’s
costs, insurance, spare parts, sureties and contingencies. |
Direct costs include, but are not limited
to, the supply and installation of equipment, piping, electrical, instrumentation and controls, buildings, site improvements, service
facilities, and non-process equipment as generally described below.
| · | Site
improvements including site development, clearing and grading, roads, stormwater management
systems, walkways, fences, parking areas and landscaping. |
| · | Equipment
including the supply and installation of all process and mechanical equipment identified
on design drawings / equipment lists, such as tanks, pumps, motors, cooling towers, and including
equipment foundations, containments, structural supports, insulation, painting, and associated
spare parts. |
| · | Piping
including process piping with suitable structural supports, pipe hangers, fittings, valves,
and insulation where required. |
| · | Electrical
systems including power distribution centers, transformers, capacitor banks, switchgear,
conduit, wire, fittings, feeders, grounding, instrument and control wiring, lighting, and
panels, and associated electrical materials. |
166 |
 |
RSI-3353 |
| · | Instrumentation
and controls including field instrumentation, control valves and their installation and calibration,
and process control, security and communication systems including associated networks, wiring,
hardware and software. |
| · | Buildings
including process and auxiliary buildings, substructures, superstructures, platforms, supports,
stairways, ladders, access ways, cranes, monorails, and hoists and associated building services
which include plumbing, heating, ventilation, air conditioning, lighting, painting, and building
fire protection. |
| · | Facility
wide utility and distribution systems for steam, water, fuel gas, and waste disposal. |
| · | Fire
protection systems including fire water storage and distribution, fire detection and suppression
systems and fire extinguishers and hose stations. |
| · | Non-process
equipment including building furniture and equipment, safety and medical equipment, shop
equipment, material-handling equipment, laboratory equipment, storage systems and other equipment
required for the safe operation of the facility. |
Indirect costs include, but are not
limited to, temporary facilities, contractor management, engineering, supervision expenses, overhead and profit as generally described
below:
| · | Temporary
facilities, including construction offices, temporary roads and access, contractor parking,
temporary power, utilities, communications, and construction fencing. |
| · | Construction
tools and equipment. |
| · | Construction
supervisors, accounting, timekeeping, purchasing, expediting, and warehouse personnel, security
guards and safety personnel, and all associated travel and living expenses, medical and fringe
benefits. |
| · | Construction-related
permits, field tests, special licenses, taxes, insurance, and interest. |
| · | Engineering,
including detailed discipline engineering design and consulting, cost engineering, engineering
field supervision and reviews, environmental monitoring and testing, field and shop inspections
and associated reporting. |
| · | Procurement
including purchasing, expediting, receiving, testing and inspection and vendor field support
during startup and commissioning. |
The capital cost estimate is based on
construction and commissioning of the facility in accordance with the Project contracting strategy and Project schedule as outlined in
Figure 21-1. The Company expects to make a Final Investment Decision in the first half of 2024 which would result in first production
of lithium carbonate in 2026.
167 |
 |
RSI-3353 |
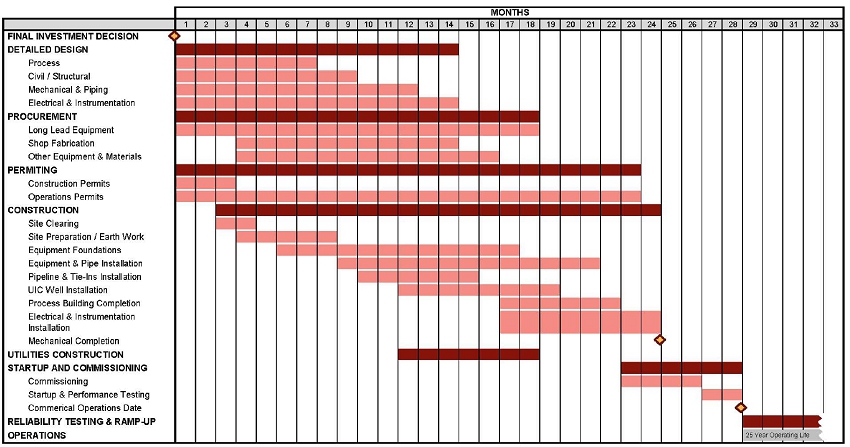
Figure 21-2. Project Schedule
| 21.1.4 | Contracting
Approach |
The construction of the Project is proposed
to be contracted on a Lump-Sum-Turn-Key (LSTK) basis to a single EPCC (Engineering, Procurement and Construction and Commissioning) contractor
who will be responsible for all remaining engineering, procurement, construction and commissioning activities required, except as may
be otherwise provided directly by the Project Company. This approach provides the Project Company, and its financing partners, with execution
certainty, primarily through the provision of certain performance and schedule guarantees included in the EPCC agreement. The cost of
the proposed contracting approach is considered in the preparation of the cost estimate.
An allowance of 12% is applied to the
equipment purchase cost to cover freight, insurances, duties, and sales taxes associated with shipping to the Project Site which is included
based on benchmarking and industry norms.
An allowance of 2.5% is applied to major
equipment purchased cost, excluding buildings and tanks, for construction, commissioning, and startup spares.
A contingency of $50 million is included,
which equates to approximately 15% of the direct and indirect capital costs.
Contingency is included
as a separate line item to address items, conditions or events which their state, occurrence, or effect is uncertain and that experience
shows will likely result in additional costs. Contingency does not cover changes in scope, cost fluctuations or currency fluctuations,
nor does contingency account for project event risks such as labor unrest, blockades, adverse market conditions, force majeure, but instead
is included to allow for unknowns that arise during construction.
168 |
 |
RSI-3353 |
The following items are not included
within the capital cost estimate:
| / | Historical
or sunk costs including Pre-Feasibility and Feasibility study costs |
| / | Interest
and financing costs |
| / | Improvements
to LANXESS owned facilities and equipment |
| / | Improvements
to the Entergy electrical substation which is assumed to be addressed through electrical
tariff |
| / | Sustaining
capital and capital spares |
It should be noted that the Project
is based on receiving brine at current brine wellfield production rates and as such the existing brine field infrastructure can support
the Project without new wells or additional capital improvements to existing wellfield infrastructure.
| 21.1.8 | Estimate
Confidence |
The cost estimate was developed following
the principles set out by AACE International (Association for Advancement of Cost Engineering International) and has a stated accuracy
range of -15% to +20%. This accuracy range is supported by over 95% of equipment items pricing based on vendor quotes, which range from
an accuracy level of firm to +/- 15%. The estimate accuracy range is supported by engineering design maturity that meets the requirements
for this classification of estimate.
| 21.2 | Operating
Cost Estimate |
The operating cost (OPEX) of the Project
is estimated to be $6,810 per tonne of lithium carbonate produced. The unit cost of operation is based on production of an average of
5,400 tonnes of lithium carbonate for sale per year over the 25-year life of the Project.
Operating costs are categorized as variable
or fixed costs. Variable operating costs are those which are production rate dependent. Fixed operating costs do not vary with production
and generally remain constant on an annualized basis. Variable costs include reagents, power, fuels, consumable operating supplies and
production-based fees and royalties and were derived based on the steady state mass balance and considering vendor recommendations. Fixed
costs include maintenance materials, rent and leases, insurance, labor and administrative costs.
The sustaining capital allowance included,
specifically for those capital improvements required to maintain the Project over its economic life, are expected to be approximately
$79M over the life of the project or approximately $580 per tonne of lithium carbonate produced. The all-in operating cost including
OPEX and sustaining capital is estimated at $7,390 per tonne.
The total estimated all-in operating
cost for the Project is summarized in Table 21-2.
169 |
 |
RSI-3353 |
Table 21-2.
Project Operating Cost Summary
Category | |
Type | |
Average
Annual Cost
($/t)[1] | |
Electric Power and Infrastructure | |
Variable | |
| 950 | |
Reagents and Consumables | |
Variable | |
| 2,880 | |
Maintenance
Materials and External Services[2] | |
Variable | |
| 610 | |
Workforce[3] | |
Variable | |
| 1,930 | |
Insurance | |
Fixed | |
| 340 | |
Miscellaneous
Costs[4] | |
Fixed | |
| 100 | |
Total
OPEX | |
| |
| 6,810 | |
Sustaining
Capital Cost | |
| |
| 580 | |
All-in
Operating Cost [5][6] | |
| |
| 7,390 | |
Notes:
[1] Operating costs are calculated
based on an average annual production of 5,400 tonnes of lithium carbonate.
[2] Includes contract maintenance,
solid waste disposal, and external lab services.
[3] Approximately 89 full
time equivalent positions.
[4] Includes general and administrative
expenses.
[5] Does not include future
royalties or brine lease-fees-in-lieu-of-royalties which are still to be determined and subject to regulatory approval (lease-fees-in-lieu-of-royalties
have been determined for bromine and certain other minerals in the State of Arkansas but have not yet been determined for lithium extraction).
[6] Does not include brine
fees which may be due to LANXESS as a result of finalization of the commercial arrangements between LANXESS and Company.
| 21.2.1 | Electric
Power and Infrastructure |
Electrical power and infrastructure
related costs are estimated to average $5.1M/year or $950 per tonne of lithium carbonate produced on an average over the life of the
Project. The major utility demand for the Project is electricity. The Project will utilize new dedicated infrastructure for the supply
of electricity, natural gas and water.
The cost of power required to operate
the Project Facility is estimated at $4.4M per year, based on an average annual consumption of 67 million kWh and a unit rate of $0.0655
per kWh. Electrical substation upgrades by Entergy in support of the Project are estimated at $3.0M. It is anticipated that the capital
cost recovery will be distributed over the first five years through the electrical tariff by Entergy. Capital recovery charges are reflected
in the annualized average power cost for the Project.
Natural gas will be delivered to the
Project by Energy Transfer. Natural gas infrastructure improvements, including a new gas meter station, are assumed to be recovered through
a component of the delivery charge. Natural gas delivery charges are estimated at $390,000 per year for the first five years to account
for capital recovery and $270,000 per year thereafter. The project is expected to consume an average of 260 GJ per day. Annualized average
natural gas costs are estimated at $380,000 per year based on unit cost of natural gas of $4.00 per GJ ($4.25 per MMBtu).
An allowance is included for the small
quantity of chlorinated water supplied by LANXESS for domestic uses which will be charged to the project on a cost plus basis.
170 |
 |
RSI-3353 |
| 21.2.2 | Reagents
and Consumables |
Reagent and consumables costs are estimated
to average $15.6M or $2,880 per tonne of lithium carbonate produced on an average over the life of the Project. A variety of reagents
and consumables are necessary to support multiple steps throughout the lithium recovery process. Reagent costs are the single largest
component of variable costs. Reagent consumption rates are estimate based on average steady state production of the Project Facility.
Reagent costs are based on vendor pricing received from regional chemical suppliers generally located in the gulf coast region. Unit
costs are based on expected long-term pricing forecasts supported by historical average pricing.
Table 21-3.
Reagent Cost Estimate
Category | |
Units | | |
Units/year | | |
$/Unit | | |
$ M/year | |
Caustic Soda (NaOH) | |
$/t | | |
| 6,250 | | |
| 542 | | |
| 3.4 | |
Soda Ash (Na2CO3) | |
$/t | | |
| 11,500 | | |
| 485 | | |
| 5.6 | |
Hydrochloric Acid (HCl) | |
$/t | | |
| 15,600 | | |
| 221 | | |
| 3.4 | |
Hydrated
Lime (Ca(OH)2) | |
$/t | | |
| 740 | | |
| 766 | | |
| 0.6 | |
Citric Acid | |
$/t | | |
| 140 | | |
| 1296 | | |
| 0.2 | |
Other | |
$ | | |
| - | | |
| - | | |
| 1.7 | |
Total | |
| | |
| | | |
| | | |
| 14.9 | |
Notes:
[1] Any discrepancies in the
totals are due to rounding effects.
[2] Other Reagents includes
allowances for small quantities of surfactants, flocculants, coagulants and other reagents associated with the operation of the Project
Facility.
Consumables required for the Plant are
shown in Table 21-4.
Table 21-4.
Consumable Costs
Category | |
$/year | |
Filter clothes | |
| 250,000 | |
Packaging materials | |
| 175,000 | |
Membranes, filters | |
| 130,000 | |
Fuel, diesel | |
| 50,000 | |
Safety | |
| 25,000 | |
Other | |
| 100,000 | |
Total | |
| 730,000 | |
| 21.2.3 | Maintenance
Materials and External Services |
Maintenance materials and external services
costs are estimated to average $3.3M or $610 per tonne of lithium carbonate produced on an average over the life of the Project.
Maintenance materials include allowances
for parts, equipment and other materials required to maintain the facility but excludes sustaining capital costs. Maintenance materials
are estimated at $0.5M per year.
171 |
 |
RSI-3353 |
External services include laboratory
support, third party chemical analysis, IT services, professional consultants, training services, contract maintenance, vendor support,
boiler and cooling tower service, UIC well maintenance and waste management. External services are estimated at $2.8M per year.
Workforce costs are estimated to average
$10.4M or $1,930 per tonne of lithium carbonate produced on an average over the life of the Project. Personnel is the seconded largest
operating cost for Standard Lithium. Workforce positions are estimated based on the requirement for operation of the Project Facility
on a 24 hours per day, seven days per week basis.
Table 21-5.
Workforce Positions
Area | |
Position | |
Workforce
per Shift | |
Shifts | | |
Total | |
Operations | |
Operations Manager | |
| 1 | |
1 | | |
| 1 | |
| |
Shift Foreman Pre-treatment | |
| 1 | |
4 | | |
| 4 | |
| |
Shift Foreman Lithium Carbonate | |
| 1 | |
4 | | |
| 4 | |
| |
Control Room Operator | |
| 2 | |
4 | | |
| 8 | |
| |
Production Operator | |
| 4 | |
4 | | |
| 16 | |
| |
Product Handling Operators | |
| 3 | |
2 | | |
| 6 | |
| |
|
|
|
|
|
Operations Subtotal | | |
| 39 | |
Maintenance | |
Maintenance Manager | |
| 1 | |
1 | | |
| 1 | |
| |
Supervisor | |
| 2 | |
1 | | |
| 2 | |
| |
Planner | |
| 2 | |
1 | | |
| 2 | |
| |
Mech/Welder/Pipe Fitter | |
| 4 | |
1 | | |
| 4 | |
| |
Electrical/Instrument | |
| 2 | |
1 | | |
| 2 | |
| |
Shift Maintenance (Mech, Elect.) | |
| 3 | |
4 | | |
| 12 | |
| |
Electrical/Controls Engineers | |
| 1 | |
1 | | |
| 1 | |
| |
Maintenance/Reliability Engineer | |
| 1 | |
1 | | |
| 1 | |
| |
|
|
|
|
|
Maintenance Subtotal | | |
| 25 | |
Technical Services | |
Technical Manager | |
| 1 | |
1 | | |
| 1 | |
| |
Plant Engineers | |
| 2 | |
1 | | |
| 2 | |
| |
QA/QC Supervisor | |
| 1 | |
1 | | |
| 1 | |
| |
Dayshift Technicians | |
| 2 | |
1 | | |
| 2 | |
| |
Lab Supervisor | |
| 1 | |
1 | | |
| 1 | |
| |
Chemists | |
| 1 | |
4 | | |
| 4 | |
| |
|
|
|
|
|
|
Technical Subtotal | | |
| 11 | |
General and Administration | |
Plant Manager | |
| 1 | |
1 | | |
| 1 | |
| |
Controller | |
| 1 | |
1 | | |
| 1 | |
| |
Purchasing Supervisor | |
| 1 | |
1 | | |
| 1 | |
| |
Human Resources Supervisor | |
| 1 | |
1 | | |
| 1 | |
| |
Health Safety Enviro. Manager | |
| 1 | |
1 | | |
| 1 | |
| |
Purchasing Clerks | |
| 1 | |
1 | | |
| 1 | |
| |
Accounting / Payroll | |
| 1 | |
1 | | |
| 1 | |
| |
Administration Clerks | |
| 1 | |
1 | | |
| 1 | |
| |
Gatehouse (Shift) | |
| 1 | |
4 | | |
| 4 | |
| |
Warehouse Clerks | |
| 1 | |
2 | | |
| 2 | |
| |
|
|
|
|
General and Administration Subtotal | | |
| 14 | |
|
|
|
|
|
|
Workforce Total | | |
| 89 | |
172 |
 |
RSI-3353 |
The average base salary for professional
and hourly workers is approximately $83,000 per year. Workforce costs also include burdens estimated at an average of 45% of base salary
and a 15% allowance for overtime.
Table 21-6.
Workforce Costs
Category | |
Annual
Cost ($M/year) | |
Operations | |
| 4.3 | |
Maintenance | |
| 3.1 | |
Technical Services | |
| 1.4 | |
General and Administration | |
| 1.6 | |
Total | |
| 10.4 | |
Insurance costs are estimated to average
$1.8M or $340 per tonne of lithium carbonate produced on an average annualized basis and are assumed to cover risks including property
damage, general liability, and business interruption.
| 21.2.6 | Miscellaneous
costs |
Miscellaneous operating costs are estimated
to average $0.5M or $100 per tonne of lithium carbonate produced on an average annualized basis. Miscellaneous costs include general
and administrative expenses including mobile equipment leases, office and IT costs, telephone and fax, computer equipment, software,
licenses, subscriptions, office supplies, and travel.
Sustaining capital costs are estimated
at $79M over the life of the Project which on an annualized average basis equates to approximately US$580 per tonne of lithium carbonate
produced.
Sustaining capital costs include repair
or replacement of equipment or materials during the 25-year life of the Project. The frequency of repair or replacement of infrastructure
considered ranges or replacement intervals between 1 and 10 years. The cost and frequency of sustaining capital expenditures are based
on recommendations from vendors and equipment manufacturers, quotations, previous project experience, and industry standards.
Major equipment replacements and activities
considered as sustaining capital expenditures and which are reflected in the sustaining capital cost estimate include, but are not limited
to, the following:
| / | LSS
DLE Resin replacement; |
| / | Ultrafiltration
membrane replacement; |
| / | BWRO/OARO
membrane replacement; |
| / | Carbonate
preheater plate replacement; |
| / | Filter
press plate replacement; |
173 |
 |
RSI-3353 |
| / | Agitator
seal replacement; |
| / | Rubber
lining replacement; |
| / | Lithium
carbonate centrifuge refurbishment; |
| / | Bicarbonate
reactor cooler refurbishment; |
| / | Tank
coating refurbishment; |
| / | Structure
steel coating refurbishment; |
| / | Low
pH service pump replacements; and |
| / | UIC
well refurbishments including bullhead acidizing and radioactive tracer survey. |
The following items are not included
within the operating cost estimate:
| / | Future
royalties or brine lease-fees-in-lieu-of-royalties which are still to be determined and subject
to regulatory approval. Lease-fees-in-lieu-of-royalties have been determined for bromine
and certain other minerals in the State of Arkansas but have not yet been determined for
lithium extraction. |
| / | Brine
fees which may be due to LANXESS as a result of finalization of the commercial arrangements
between LANXESS and Company. |
| / | Taxes,
other than sales taxes which may be due on the purchase of materials and equipment. |
It is the QP’s opinion that the
estimated capital and operating costs accurately reflect the level of project understanding and are appropriate for a Feasibility Study.
174 |
 |
RSI-3353 |
The objective of the economic analysis
is to determine if the Project is financially viable. The economic analysis was prepared using a Discounted Cash Flow (DCF) economic
model, showing both pre-tax and post-tax results, to evaluate the Project. CAPEX and OPEX expenditures presented in Section 21 have
been used in this analysis. The model includes taxes but excludes any government and commercial royalties/payments. The results include
net present value (NPV) for an 8% discount rate, internal rate of return (IRR), and sensitivity analysis of key inputs.
| 22.1 | Inputs
and Assumptions |
The key inputs and assumptions are listed
in Table 22-1. These assumptions represent the base case for the commercial operation.
Table 22-1.
Project Economic Model Key Input Parameters
Key Parameters | |
Units | |
Assumption |
South Unit Brine Production
(LANXESS) | |
m3/yr | |
5.21 |
Plant
Availability (Plant + Utilities) [1, 2] | |
% | |
94% |
Effective
Extraction Efficiency (Plant) [2] | |
% | |
93.1 |
Attrition
(Lithium Carbonate Losses) [2] | |
% | |
0.5 |
Initial
Annual Production of Li2CO3 | |
tpa[3] | |
5,730[3,4,5] |
Average
Annual Production of Li2CO3 | |
tpa | |
5,400[4] |
Plant Operating Life | |
years | |
25[6] |
CAPEX – Confidence | |
| |
P85 |
Total Capital Expenditures | |
$ millions | |
365[7,8] |
Average Annual Operating Cost | |
$/t | |
6,810 |
Average Annual All-in Operating Cost | |
$/t | |
7,390[9,10] |
Selling Price | |
$/t | |
30,000[11] |
Financing | |
| |
Unlevered IRR |
Discount Rate | |
% | |
8 |
Federal Tax Rate | |
% | |
21 |
Arkansas State Tax | |
% | |
5.1 |
Inflation Reduction Act Manufacturing
Tax Credit | |
- | |
10 (45X) |
Notes:
[1] Plant Availability excludes LANXESS
South Plant availability which is already considered in South Unit Feed Brine Rate.
[2] Refer to Section 15 for modifying
factors considered.
[3] Tonnes (1,000 kg) per annum.
[4] Commercial production is based on the production plan. Refer to Section 16.
[5] Initial annual production figure
represents Year 2 production, following a ramp-up period in Year 1.
[6] Plant design and financial modelling based on 25-year economic life. Proven and Probable Reserves support a 40-year operating life.
[7] Capital Expenditures include 15% contingency.
[8] No inflation or escalation has been carried for the economic modelling.
[9] Includes operating expenditures and sustaining capital.
[10] Brine lease-fees-in-lieu-of-royalties (to be approved by AOGC) have not been defined and are not currently included in the economic
modelling.
[11] Selling price of battery-quality lithium carbonate based on a flatline price of $30,000/t over total project lifetime. Refer to
Section 19.
[12] Any discrepancies
in the totals are due to rounding effects.
175 |
 |
RSI-3353 |
Capital investment for the average annual
production of 5,400 tonnes per year of battery-quality lithium carbonate, including equipment, materials, indirect costs, and contingency
at 15% of direct and indirect costs, is estimated to be US$365 Million. This total excludes interest expenses that might be capitalized
during the same period.
The average annual operating cost for
the Project is estimated at US $37 Million. As the cash flow model accounts for decreasing Lithium Carbonate production over the lifetime
of the project, the annual operating costs correspondingly decreases each production year. The annual operating cost includes process
reagents, utilities, process consumables, natural gas, maintenance materials, external services, labor, and miscellaneous general and
administration (G&A) costs. Approximately 86% of the OPEX costs are derived from three (3) of OPEX cost categories as shown
below.
The remaining components of the operating
costs have a significantly lower impact on the overall economics. Insurance is added on top of the above-mentioned operating costs at
0.5% of CAPEX per year. A total of $2.98M of electrical infrastructure cost is distributed evenly over the first 5 years of production
to account for capital costs related to the required Entergy Substation upgrades which are recovered by Entergy during the initial operating
period.
Major repairs or replacements of critical
processing plant items are included in sustaining capital. Sustaining capital is capitalized and depreciated over their useful lives.
A provision of $78.8M for sustaining capital over the life of the Project was included in the economic model.
Cash flow will reach 100% after a production
ramp-up period of twelve months. During the ramp-up period, it is assumed the facility will produce and monetize 75% of expected steady-state
production of saleable lithium carbonate. Similarly, it is assumed that operating costs associated with process reagents and variable
utilities will be at 85% of steady-state consumption (all other operating costs are assumed at 100% of steady-state consumption).
The economic model assumes a construction
period of 27 months.
The Project is modelled with a 25-year
economic life from the start of production. No allowances are included in the model for extension of the project life beyond 25 years.
As described in Section 15, the Project’s Proven and Probable Reserves support a 40-year operating life.
176 |
 |
RSI-3353 |
As described in Section 19, the
selling pricing assumption for battery-quality Lithium Carbonate is US $30,000/tonne in 2023. Since the economics are calculated without
any escalation, the price remains constant in the model over the 25 years of operation.
| 22.1.8 | Discounted
Cash Flow (DCF) |
A discount rate of 8% yearly has been
assumed for the calculation of the NPV.
| 22.1.9 | Pre-Construction
Expenses |
Pre-construction expenses are treated
as sunk costs and are not included in the DCF analysis.
The following
royalties and taxes have been applied to the economic analysis of the Project.
The cash flow model does not consider
any royalty payments (also referred to as Lease-fees-in-lieu-of-royalties) which may be due to mineral owners in relation to the profitable
extraction of lithium from brine as to date the AOGC has not approved a lease payment related to lithium extraction from brine.
No allowances are included for brine
fees which may be due to LANXESS as a result of finalization of definitive commercial arrangements between LANXESS and the Project Company.
A yearly depreciation of 5% (facility
evenly depreciated over 20 years of operating life) is used for this analysis.
The US Federal Corporate Income Tax
(CIT) rate of 21% and the State of Arkansas Corporate Income Tax rate of 5.1% are used for this analysis.
| 22.2.4 | 45X
MPTC Tax Credit |
The cash flow model considers the Advanced
Manufacturing Production Tax Credit (45X MPTC) for the business case. The Advanced Manufacturing Production Credit provides a tax credit
for each “eligible component” which is produced in the U.S. The credit is 10% of costs incurred with respect to the production
of critical minerals (of which lithium is one). For modeling purposes, a 10% credit is applied annually (with a 1-year lag) on the total
operating cost, sustaining capital, and depreciation.
| 22.3 | CAPEX
Spending Schedule |
The economic model assumes that capital
investments disbursements will be spread over 27 months.
177 |
 |
RSI-3353 |
Production revenues have been estimated
based on the price scenario for a Lithium Carbonate product, as identified in Section 19 and the production plan set out in Section 16.
Table 22-2 summarizes the DCF for the
assumed for the Project for the purposes of this Technical Report.
Table 22-2.
Project Discounted Cashflow Model

| 22.6 | Economic
Evaluation Results |
The project economics resulting from
the assumed price scenario at full production, which was used in the economic model, are presented in Table 22-3. The NPV values were
also calculated for a discount rate of 8%.
Table 22-3.
Project Economic Evaluation
Internal Rate of Return (IRR) |
|
|
|
| |
Net Present Value (NPV) |
Pre-Tax | |
| 29.53 | % | |
NPV – Pre-Tax | |
$ | 772,204,000 |
Post-Tax | |
| 24.04 | % | |
NPV – Post-Tax | |
$ | 549,561,000 |
Notes:
[1] All model outputs are expressed on a 100% project ownership basis with no adjustments for project financing assumptions.
[2] Assumes a U.S. Federal tax rate of 21% and State of Arkansas Tax rate of 5.1%, as well as variable property taxes.
[3] Any discrepancies in the totals are due to rounding effects.
178 |
 |
RSI-3353 |
A sensitivity analysis methodology,
using one-factor-at-a-time (OAT), involves changing one input variable, keeping others at their baseline (nominal) values, and then returning
the variable to its nominal value. This is repeated for each of the other inputs in the same way.
OAT sensitivity analysis of the project
key variables CAPEX, OPEX, Selling Price changing +/- 20%, and Production +/- 5% was conducted to illustrate the impact of changes on
the corresponding values of NPV and IRR. The results of the sensitivity analysis, at an 8% discount rate, are presented in Tables 22-4
to Table 22-7, and Figures 22-1 to 22-4.
Table 22-4 shows the sensitivity of
NPV and IRR to a 20% CAPEX increase and decrease from the base case. It must be noted that some of the OPEX items are percentages of
the CAPEX.
Table 22-4.
Sensitivity Analysis to CAPEX Variation
Overview | |
| -20% | | |
| Base
Case ($M) | | |
| +20%
($M) | |
Capital Cost (CAPEX) | |
| 292.0 | | |
| 364.9 | | |
| 437.9 | |
NPV Pre-Tax | |
| 837.6 | | |
| 772.2 | | |
| 706.8 | |
NPV Post-Tax | |
| 608.3 | | |
| 549.6 | | |
| 490.8 | |
IRR Pre-Tax | |
| 35.9 | % | |
| 29.5 | % | |
| 25.0 | % |
IRR Post-Tax | |
| 29.2 | % | |
| 24.0 | % | |
| 20.4 | % |
Table 22-5 shows the sensitivity of
NPV and IRR to a 20% OPEX increase and decrease from the base case.
Table 22-5.
Sensitivity Analysis to OPEX Variation
Overview | |
| -20% | | |
| Base
Case ($M) | | |
| +20%
($M) | |
Operating Cost (OPEX) | |
| 30.7 | | |
| 38.4 | | |
| 46.1 | |
NPV Pre-Tax | |
| 837.6 | | |
| 772.2 | | |
| 706.8 | |
NPV Post-Tax | |
| 608.3 | | |
| 549.6 | | |
| 490.8 | |
IRR Pre-Tax | |
| 31.1 | % | |
| 29.5 | % | |
| 27.9 | % |
IRR Post-Tax | |
| 25.1 | % | |
| 24.0 | % | |
| 22.9 | % |
Table 22-6 shows the sensitivity of
NPV and IRR to a 20% Product Price increase and decrease from the base case.
Table 22-6.
Sensitivity Analysis to Product Price Variation
Overview | |
| -20% | | |
| Base
Case ($M) | | |
| +20%
($M) | |
LCE Price | |
| 24,000 | | |
| 30,000 | | |
| 36,000 | |
NPV Pre-Tax | |
| 485.1 | | |
| 772.2 | | |
| 1,059.3 | |
NPV Post-Tax | |
| 337.3 | | |
| 549.6 | | |
| 761.7 | |
IRR Pre-Tax | |
| 22.4 | % | |
| 29.5 | % | |
| 36.2 | % |
IRR Post-Tax | |
| 18.4 | % | |
| 24.0 | % | |
| 29.3 | % |
Table 22-7 shows the sensitivity of
NPV and IRR to a 5% Production Volume increase and decrease from the base case.
179 |
 |
RSI-3353 |
Table 22-7.
Sensitivity Analysis to Production Volume Variation
Overview | |
| -20% | | |
| Base
Case ($M) | | |
| +20%
($M) | |
Production first year (Mt) | |
| 5,473 | | |
| 5,761 | | |
| 6,049 | |
NPV Pre-Tax | |
| 708.9 | | |
| 772.2 | | |
| 835.5 | |
NPV Post-Tax | |
| 502.0 | | |
| 54.9.6 | | |
| 597.1 | |
IRR Pre-Tax | |
| 28.0 | % | |
| 29.5 | % | |
| 31.1 | % |
IRR Post-Tax | |
| 22.8 | % | |
| 24.0 | % | |
| 25.2 | % |
Sensitivity of Pre-Tax IRR to the changes
in the CAPEX, OPEX, Selling Price, and Production Output is illustrated in the tornado chart in Figure 22-1.
Figure 22-1. Pre-Tax IRR Sensitivity
Sensitivity of Post-Tax IRR to the changes
in the CAPEX, OPEX, Selling Price, and Production Output is illustrated in the tornado chart in Figure 22-2.
Figure 22-2. Post-Tax IRR Sensitivity
180 |
 |
RSI-3353 |
Sensitivity of Pre-Tax NPV at an 8%
discount rate to the changes in the CAPEX, OPEX, Selling Price, and Production Output is illustrated in the tornado chart in Figure 22-3.
Figure 22-3. Pre-Tax NPV Sensitivity
Sensitivity of Post-Tax NPV at an 8%
discount rate to the changes in the CAPEX, OPEX, Selling Price, and Production Output is illustrated in the tornado chart in Figure 22-4.
Figure 22-4. Post-Tax NPV Sensitivity
The OAT sensitivity analysis indicates
that the project is as follows:
| / | IRR
and NPV are most sensitive to the product Selling Price variation. |
| / | IRR
and NPV are least sensitive to OPEX variation. |
| / | IRR
and NPV are moderately sensitive to CAPEX and Production. |
181 |
 |
RSI-3353 |
| 22.8 | Conclusions
and Sensitivity Analysis |
The Project’s
economics resulting from the assumed price scenario used in the economic model is presented in Table 22-1. A sensitivity analysis was
conducted to illustrate the impact of +/-20% changes in CAPEX, OPEX, and Selling Price, and +/-5% changes in Production Output on the
project’s NPV and IRR (Table 22-3 and 22-5).
The Sensitivity analysis of the project
economics indicates that the project is economically viable under the base case conditions as well as under the condition of the isolated
cases of a 20% increased CAPEX, a 20% reduced product Selling Price, a 5% reduced Production Output, and a 20% increased OPEX.
182 |
 |
RSI-3353 |
This section discusses mineral-brine
properties that occur outside of the Property. In some cases, the Authors have not been able to verify information pertaining to mineralization
on the adjacent properties, and therefore, the Authors and Standard Lithium advocate that the information is not necessarily indicative
of the mineralization on the Property that is subject to this report.
There are two major bromine producers
in Arkansas: LANXESS and Albemarle Corporation (see Figure 23-1). LANXESS has its Arkansas headquarters in El Dorado, Arkansas. Albemarle’s
Arkansas headquarters are at the center of its property in Magnolia, Arkansas. Albemarle’s property is situated approximately 3
km from the western boundary of the LANXESS Property. In addition, Saltwerx has developed a property package approximately 15km from
the western boundary of the LANXESS Property. To date, there is no lithium production from adjacent properties but lithium leases have
been established by Saltwerx and Tetra Technologies. The Standard Lithium Project stands to be the first commercial lithium production
from the Smackover Formation.
LANXESS operates three brine-based bromine
extraction plants near El Dorado, AR (U.S.). The well-field that supports the LANXESS El Dorado Plants is sub-divided into three contiguous
‘units’ based on the three unitized areas of bromine operation: South, Central, and West unit areas.
During 2021, LANXESS processed approximately
13.3 million cubic meters [83.7MM U.S. Barrels] of brine to support their South Arkansas Bromine Operations. In addition to bromine,
LANXESS entered the battery chemistry business with electrolyte production for lithium-ion batteries in Leverkusen, Germany (LANXESS,
2021) and is actively supporting operation of Standard Lithium’s Demonstration Scale Lithium Pilot Plant which is located at the
LANXESS South Plant.
| 23.2 | Albemarle
Corporation |
Albemarle Corporation is one of the
largest producers of bromine and lithium related resources and products world-wide with bromine operations in Arkansas (U.S.) and Jordan
and lithium operations in Chile, Australia, Germany and Clayton Valley, Nevada (U.S.). Albemarle exclusively operates using conventional
lithium extraction technologies at their commercial facilities but have previously invested in DLE research. To QP’s knowledge,
no lithium has been commercially produced to date by Albemarle at either of their facilities in South Arkansas.
Albemarle Corporation operates two (2) brine-based
bromine extraction plants near Magnolia, AR. Albemarle's Magnolia North and South plants are fed by a network of brine production wells
in Columbia County. During 2021, Albemarle Corporation processed approximately 20 million cubic meters (125.4MM U.S. Barrels) of brine
to produce approximately 74,000 tons of bromine at its Magnolia facilities (Albemarle Corporation, 2021). In 2021, Albemarle announced
the company will double capacity for brine extraction by 2025 at a cost of $30 miillion to $50 million (Albemarle Corporation, 2021c).
The well field that supports Albemarle’s Magnolia operations directly abuts sections of the properties associated with Standard
Lithium’s South West Arkansas project on the field’s northern and eastern boundaries.
183 |
 |
RSI-3353 |
| 23.3 | Saltwerx
(Subsidiary to Galvanic, LLC) |
Saltwerx, LLC (Subsidiary to Galvanic
Energy) has ownership of 120,000 gross acres of resource claims in the Smackover Formation. Saltwerx has completed well testing, reservoir
modeling, and inferred mineral resource estimations on their lithium-brine prospect in southern Arkansas. They estimate that this acreage
could contain 4 million tons of lithium carbonate equivalent (Saltwerx, 2021). Saltwerx’s property is located approximately 15km
west of the Property and directly south of the TETRA Property.
Tetra Technologies and Standard Lithium
entered into a 2017 option agreement that grants Standard Lithium an option to acquire the rights to produce and extract lithium form
a portion of Tetra’s total brine leasehold. The option period is valid for a period of 10 years subject to Standard Lithium’s
annual payments. Standard Lithium has not yet exercised its option to acquire the rights to produce and extract lithium.
In September 2022, TETRA completed
a maiden inferred bromine and lithium brine resource estimation report for its leased acreage in the Smackover Formation. The brine resource
underlying the approximately 5,000 gross acres where TETRA holds lithium mineral rights that is not subject to the lithium option agreement
with Standard Lithium is estimated to contain an inferred resource of 212,000 tonnes of lithium carbonate equivalent (Tetra, 2022). In
June 2023, TETRA filed an application to establish a unitized brine unit on this property and indicated an increase in the acreage
to approximately 6,000 acres (Tetra, 2023). No further information was published on an increase to the inferred resource estimate.
| 23.5 | South
West Arkansas Project |
Standard Lithium acquired brine production
rights to lithium for the South West Arkansas (SWA) project directly from TETRA through an option agreement. The SWA project has conducted
a five-well exploration program, well testing, reservoir modeling, and inferred mineral resource estimations at a Preliminary Feasibility
Study (PFS) level study for this greenfield project with an Indicated and Inferred Mineral Resource of 1.4 Mt and 0.4 Mt lithium carbonate
equivalent, respectively. The PFS study demonstrates robust economics, assuming production of at least 30,000 tonnes per year of battery-quality
lithium hydroxide beginning in 2027 over a 20-plus year operating life. Standard Lithium anticipates completing a FEED and DFS for the
SWA project in 2024 and beginning construction in 2025. Commercial production is expected in 2027, subject to continuing project definition,
due diligence, project financing and receipt of future feasibility studies.
184 |
 |
RSI-3353 |
Figure 23-1. Location of Active
and Potential Brine Producers in Southern Arkansas
185 |
 |
RSI-3353 |
| 24.0 | Other
Relevant Data and Information |
There is no other data and information
relevant to this report.
186 |
 |
RSI-3353 |
| 25.0 | Interpretations
and Conclusions |
The Project has been independently evaluated,
leading to the following conclusions and interpretations regarding the suitability of the proposed site and the viability of the Project.
It is determined that a clear path is established to reach a positive Final Investment Decision subject to concluding remaining commercial
agreements and obtaining the required financing.
| / | The
Proven and Probable Reserves confirm the viability of the Project over its 25 year economic
life at an average annual production rate of 5400 tonne per annum of lithium carbonate. |
| / | The
Proven and Probable Reserves support an operating life of up to 40 years. |
| / | The
development and testing completed at the Demonstration Plant provides a robust basis for
the commercial design which is based on Direct Lithium Extraction technology. |
| / | Work
to date completed at the Demonstration Plant illustrates that lithium can be economically
extracted from the lithium rich brine produced from the Smackover Formation. |
| / | The
Project Site secured is considered well suited for development and is situated near all necessary
utilities. |
| / | Environmental
studies have concluded the Project Site is suitable for development with limited adverse
environmental and social impacts, generally limited to the boundaries of the Project Site. |
| / | There
is a clear pathway for the Project to obtain the state permits required for development. |
| / | The
economic analysis yielded positive results in a timeline for development and first production
that is considered realistic based on timely funding and is typical of projects of similar
magnitude within industry. |
| / | Overall,
the result of this Feasibility Study demonstrates that lithium can be economically extracted
from the lithium rich brine within the Smackover Formation. |
The opinions of the
Qualified Persons are further stated in the following sections.
| 25.1 | Geology,
Resources and Reserve Estimate |
Significant confidence
within the geologic modeling was developed by utilizing decades of available bromine production data and ongoing lithium sampling from
within the Property. Based on the geologic modeling the following Resource and Reserve conclusions have been reached:
| / | The
Property has the Resources and Reserves required to support the Project. |
| / | The
total in-situ Measured and Indicated Brine Resources for the combined LANXESS South, Central
and West Brine Units are estimated at 2.8 Mt LCE or 529,000 tonnes of elemental lithium at
an average concentration of 148 mg/L. |
| / | The
total Proven and Probable Brine Reserves for Phase 1A are estimated at 208,000 tonnes of
LCE or 45,200 tonnes of elemental lithium at an average lithium concentration of 217 mg/L. |
187 |
 |
RSI-3353 |
| / | Resource
Estimate is upgraded from the 2019 PEA from Indicated to Measured for the LANXESS Project.
This upgrade is supported by numerical modelling and verified by correlating over 60 years
of operating data, supported by a robust well sampling program, and 3.5 years of Demonstration
Plant testing with extensive monitoring of brine characteristics and LANXESS operating performance. |
| / | The
Project is based on a 25-year economic life. The Proven and Probable Reserves of 208 Kt lithium
carbonate equivalent (“LCE”) at an average concentration of 217 mg/L can support
up to 40 years of operations. |
| / | The
Project is planned to produce 135,000 tonnes LCE from the LANXESS South Brine Unit over the
25-year life of the Project which represents production of approximately 5% of the in-situ
Measured and Indicated Resources. |
| / | All
LANXESS supply and disposal wells proposed to support the Project are currently in operation,
with the latest wells commissioned in 2019. |
| / | The
large underlying resource, existing operating brine field, experienced operator, coupled
with sampling, testing and Demonstration Plant operations results in a Project which is substantially
de-risked from a resource perspective when compared to other greenfield lithium projects. |
| / | The
size of the broader Resource could support additional lithium extraction developments subject
to additional feasibility studies. |
| 25.2 | Process
Information and Design |
Standard Lithium has
successfully brought a new DLE technology to an established bromine producing region. Through multiple design iterations and testing,
the studied processing approach is optimized for the Project’s Resource. The following conclusions can be reached regarding process
information and design:
| / | The
Project is based on processing a well understood feed stock, specifically brine which has
been successfully produced from the Smackover Formation for more than 60 years, from existing
infrastructure that supports the Project’s design capacity. |
| / | All
unit operations have been demonstrated either by Standard Lithium or in vendor facilities
using real brine from the Smackover. Numerous production options have been evaluated. The
current design concept appears to be near optimal and poses minimal commercial risk. |
| / | The
ongoing operation of the Demonstration Plant located at the South Plant and Project Site
has provided invaluable information for the design of the commercial facility. |
| / | Long
term Demonstration Plant testing has led to a thorough understanding of the brines and has
provided key data which have been incorporated into the design of the commercial facility. |
| / | Two
DLE technologies have been tested and evaluated. The current KTS LSS technology is considered
to be the best technology for the Project, based upon lithium recovery, impurity rejection,
operating cost and effluent dilution (i.e. lowest water use). |
188 |
 |
RSI-3353 |
The Project location
in Union County offers a pool of skilled labor and services. The plant has modest water, power, and thermal energy requirements. All
necessary utilities are within close proximity to the Project Site including power and natural gas with brine and water. High-capacity
transportation routes are readily accessible within the region and locally in the area of the Project. The site requires little grading
and has ample area for equipment layout and construction lay down areas. Space has been allocated in the plot plan to accommodate future
expansion.
| 25.4 | Environmental
Studies |
The Project Site has
been investigated for potential risk to development from pre-existing conditions and the presence of waters of the United States. Based
on the investigations conducted the conclusions are:
| / | The
site has been subject to historical timber harvesting/production and possibly oil and gas
exploration/production operations. The possible oil well locations were investigated during
the environmental study and no evidence of their existence was observed. The site is currently
undeveloped and has minimal infrastructure associated with the adjoining LANXESS operations.
There is no known risk from historical operations. |
| / | Jurisdictional
waters of the United States have been identified at the margin of the Project Site. Those
areas will be minimally impacted by site development and will be eligible for a Nationwide
Permit from the U. S. Army Corps of Engineers. The Project Site development is not expected
to cause significant adverse effects to waters of the United States. |
| / | The
presence of commercial chemical products was documented in surface and subsurface media at
the Project Site. Those materials do not present a risk to construction or operation of the
Project Facility based on concentration levels and/or potential exposure pathways. |
| / | In
consideration of site characteristics and proximity to existing utility and transportation
infrastructure, resource supply and disposal facilities, the Project Site is suitable for
construction and operation of the lithium extraction facility. |
| / | Documented
pre-existing conditions from historical operations are unlikely to have a material impact
on the development and operation of the Project. |
| 25.5 | Environmental
Regulatory Permitting |
The Project has been
examined to establish specific environmental regulatory permits necessary for construction and operation of the Project Facility and
its supporting infrastructure. Based on the examination the conclusions are:
| / | Standard
Lithium has been proactive in assessing potential environmental and regulatory risks to improve
the Project development certainty, including a comprehensive review of permit applicability,
a preliminary review of site cultural resources, and performance of a multimedia baseline
investigation of the Project Site. |
| / | The
Project is designed in consideration of applicable environmental regulatory standards and
does not present a risk of construction or operational permit denial or significant delay
in issuance. |
189 |
 |
RSI-3353 |
| / | The
Project is not subject to review, delay or denial under the NEPA thus there is no risk associated
with NEPA applicability based on the current development program. |
| / | Construction
and operation of the Project Facility are regulated through Federal and State agencies through
established permit procedures. Project Facility emissions to air, surface waters and subsurface
waters will require permit authorizations including restrictions to protect the environment
while responsibly developing the lithium resources. There is no risk associated with permit(s) issuance
on the basis the prescriptive requirements for receipt of the permits are met. |
| / | Minimization
of emissions and wastes from construction and operation and avoidance of adverse environmental
impact were significant factors in the engineering design of the Project, resulting in permit
tiers that are not at risk of denial or delay by the regulatory agencies. |
| / | The
Project Site plan factored the presence of waters of the United States in the development
and as proposed avoids significant impacts to those waters. There is no risk associated with
receiving Nationwide Permits requested from the U. S. Army Corps of Engineers. |
| / | The
Arkansas Department of Energy and Environment is proficient in regulating the extraction
of resources from brine reservoirs. The adjacent LANXESS bromine production facility has
been in operation for decades as have multiple bromine production facilities in Union and
Columbia Counties. The LANXESS facility is currently permitted for discharges similar to
those proposed for the Project Facility including air emissions, wastewater surface discharges
and underground injection of waste brine via Class I injection wells. |
| / | The
brine Resource for the Project is currently permitted and the supply well field is operational.
Underground injection wells for management of waste brine following extraction of lithium
are likewise permitted and operating. |
| / | Regulatory
permit application documents are being prepared by Standard Lithium with priority for submission
placed on those permits with longer agency review periods to maintain the project construction
timeline. |
| / | The
Project is viable and as proposed will perform within the boundaries of established environmental
standards, noting that the regulatory programs that authorize construction and operation
of the Project facility are based on protection of the environment and hence the sustainability
of the site and the local community. |
| 25.6 | Social
and Community Impact |
The Project is situated
in a region significantly supported by natural resource production and refining for over one hundred years. Bromine production and associated
chemical manufacturing operations have been a principal contributor to the local community for decades. In that context, the following
opinions are presented regarding local, regional, and national impacts from the Project:
| / | South
Arkansas is a regional hub for natural resource/brine production and processing industries.
The Project is comparable to established mineral extraction operations and natural resource
production/refining. The local community is generally supportive of those industries and
recognizes the value of their existence and their positive impact on the regional economy. |
| / | The
region will benefit from the infusion of capital via employment of skilled labor and contractors
and acquisition of materials during the construction of the Project facility. The economic
benefit will extend to the operation phase through staffing payrolls and ongoing supporting
purchases. |
190 |
 |
RSI-3353 |
| / | Lithium
is a critical mineral with national self-sufficiency implications for military/defense needs
and for the transition away from fossil fueled transportation. The Project supports the goal
of domestic lithium production. |
| / | Continuing
engagement with the local/regional community is recommended as the Project proceeds through
the investment decision and construction phases. |
| / | The
Demonstration Plant and public disclosures regarding the Project have been met with positive
regional support. The Project is generally well supported by the regional citizens and there
is no legitimate basis for organized opposition to the Project. |
| 25.7 | Capital
and Operating Costs |
Project capital and
operating cost estimates were developed utilizing industry standard approaches and benchmarked against related projects, as summarized
below:
| / | The
total capital estimate is $365 million and includes a contingency of $50M based on approximately
15% of direct and indirect costs. |
| / | The
capital cost estimate is based on approximately 95% of equipment and packages being quoted.
Embedded budgetary vendor quotations have a stated accuracy of +15%. |
| / | Reagent
and utility consumptions have been developed from the integrated mass balance and vendor
recommendations. Power costs are based upon vendor motor selections. |
| / | Labor
and management costs, maintenance materials, sustaining capital and contract labor costs
were developed with input from the Project’s operations team. |
| / | The
operating cost for the life of the Project is estimated to be $6,810/t of lithium carbonate.
Labor, reagents, consumables, and energy account for over 70% of the operating costs. All-in
operating cost, including sustaining capital expenditures is $7,390/t. |
| / | The
operating costs exclude any potential brine fees and future royalties (or brine lease-fees-in-lieu-of-royalties)
yet to be established. |
| / | The
timeline for development and first production appears realistic based on timely funding and
is typical of projects of similar magnitude within industry. |
| / | In
the QPs opinion the estimated capital cost at $365 million reasonably reflects the level
of project understanding. The operating cost estimate is well supported and is considered
to reasonably represent the expected Project OPEX. Both the CAPEX and OPEX are considered
appropriate for the Definitive Feasibility Study level. |
Project economics
were derived from inputs based on the annual production schedule, capital expense estimate, and operating expense estimate as set forth
in the DFS. The positive results from the economic analysis are summarized within the following conclusions:
| / | An
after-tax NPV of $550M and IRR of 24% assuming discount rate of 8% and a long-term price
of $30,000/t for battery-quality lithium carbonate and capital expenditure of $365 Million. |
191 |
 |
RSI-3353 |
| / | First
production of battery-quality lithium carbonate is to occur in 2026 with an average annual
production of 5,400 tpa over the operating life and a peak annual production of 5,700 tpa. |
| / | The
Sensitivity analysis of the Project economics indicates that the Project is economically
viable under the base case conditions as well as under the condition of the isolated case.
The isolated cases included modeling a 20% increased CAPEX, a 20% reduced product Selling
Price, a 5% reduced Production Output, and a 20% increased OPEX. |
| / | Running
sensitivity analysis on DCF parameters resulted in the following rank of sensitivity listed
from the most to least sensitive, respectfully: +/-20% change in lithium carbonate price,
+/- 20% change in capital costs, +/-5% change in production rate, and +/- change in operating
costs. |
Table
25-1. Project Economic Analysis Conclusions
Project Parameters | |
Units | |
Values | |
Initial
Annual Production of Li2CO3 | |
tpa
[1] | |
| 5,730 | [2] |
Average
Annual Production of Li2CO3 | |
tpa | |
| 5400 | |
Plant Operating Life | |
years | |
| 25 | [3] |
Total Capital Expenditures | |
$ millions | |
| 365 | [4,5] |
Average Annual Operating Cost | |
$/t | |
| 6810 | |
Average Annual All-in Operating Cost | |
$/t | |
| 7,390 | [6,7] |
Selling Price | |
$/t | |
| 30,000 | [8] |
Discount Rate | |
% | |
| 8 | |
Net Present Value (NPV) Pre-Tax | |
$ millions | |
| 772 | |
Net Present Value (NPV) After-Tax | |
$ millions | |
| 550 | [9] |
Internal Rate of Return (IRR) Pre-Tax | |
% | |
| 29.5 | |
Internal Rate of Return (IRR) After-Tax | |
% | |
| 24.0 | |
Notes:
All model outputs
are expressed on a 100% project ownership basis with no adjustments for project financing assumptions.
[1] Tonnes (1,000
kg) per annum.
[2] Initial annual
production figure represents Year 2 production, following a ramp-up period in Year 1.
[3] Plant design and
financial modelling based on 25-year economic life. Proven and Probable Reserves support a 40-year operating life.
[4] Capital Expenditures
include 15% contingency.
[5] No inflation or
escalation has been carried for the economic modelling.
[6] Includes operating
expenditures, assumed brine supply fees, and sustaining capital.
[7] Brine lease-fees-in-lieu-of-royalties
(to be approved by AOGC) have not been defined and are not currently included in the economic modelling.
[8] Selling price
of battery-quality lithium carbonate based on a flatline price of $30,000/t over total project lifetime.
[9] Assumes a U.S.
Federal tax rate of 21% and State of Arkansas Tax rate of 5.1%, as well as variable property taxes.
[10] Any discrepancies
in the totals are due to rounding effects.
As with any development
project, there exists potential risks and uncertainties. There are no known significant encumbrances on the Property. Standard Lithium
will attempt to reduce risk/uncertainty through effective project management, utilization of technical experts, continued Demonstration
Plant testing, community engagement, and development of contingency plans. The Project development and contracting approach to-date
has incorporated risk mitigation clauses that support Project development certainty (i.e., term sheets, mechanical and performance guarantees,
and delivery schedules). The risks to developing the Project on the Property include, but are not limited to, the following:
192 |
 |
RSI-3353 |
| / | Variations
in production rate resulting from unanticipated well production issues. |
| / | Variations
in produced lithium concentrations resulting from unanticipated reservoir heterogeneity. |
| / | Operational
variances within the LANXESS South Plant that adversely impact the quality of the Feed Brine
beyond those conditions that have already been experienced during Demonstration Plant operations. |
| / | Scalability
from the Demonstration Plant to the commercial scale production. |
| / | Obtaining
all the necessary permits and authorizations on acceptable terms, in a timely manner. |
| / | Variations
in pricing of capital. |
| / | Variations
in lithium carbonate product price. |
| / | Lithium
brine royalty assessment by the AOGC is not completed in a timely manner and/or the royalty
rates have a significant impact on project economics. |
| / | Finalization
of the definitive commercial agreements. |
| / | Changes
in laws and their implementation impacting activities on the Property. |
193 |
 |
RSI-3353 |
The Qualified Persons
involved in the Report make the following recommendations:
| / | Obtain
and review any new log and core data collected in the West, Central, and South Brine Units
which may become available in the future. Continue to monitor and analyze brine data from
production wells in the South, Central and West Brine Units, in particular in relation to
lithium concentration. |
| / | Continue
to monitor the LANXESS South Unit brine production performance. If field performance deviates
materially from forecasts, make necessary adjustments to geologic and simulation models and
revise forecasts. |
| / | Continue
test work at the Demonstration Plant with the objectives of: |
| » | obtaining
further understanding of long-term process performance, in particular for the selected DLE
technology and associated unit operations; |
| » | supporting
detailed engineering, including alternative equipment evaluations, process optimizations
and other cost saving opportunities; and, |
| » | increasing
operating knowledge of the lithium extraction process and associated brine field operations
in support of operator development and the future commercial operation of the Project (and
subsequent developments). |
| / | Continue
to advance key permits and authorizations required for construction and operation of the
Project, to ensure permits and authorizations remain off the critical path to commercial
operation. |
| / | Address
the responsibility for pre-existing environmental conditions in commercial agreements. |
| / | Continue
the process of establishing project-specific lithium royalties (lease-fees-in-lieu-of-royalties)
with the AOGC, in accordance with Arkansas Statute, to facilitate the commercial extraction
of lithium. |
| / | Evaluate
and pursue additional federal and state incentive programs including sales tax credits, state
and federal income tax reductions, government grants, and other Critical Mineral incentive
programs which may be available to improve overall Project economics. |
| / | Given
the sensitivity of the Project economics to the product price, consider offtake pricing mechanisms
to mitigate the commercial risk associated with short-term lithium price fluctuations. |
| / | Finalize
definitive commercial agreements with LANXESS and other parties which are required to support
a positive Final Investment Decision. |
194 |
 |
RSI-3353 |
Arkansas Oil &
Gas Commission, 2018. South Brine Unit & South Brine Expansion Unit, Order 057-2018-10, November 19, 2p.
Arkansas Oil &
Gas Commission, 2021. Production by Field – 2021. Accessed May 4, 2023, https://www.aogc.state.ar.us/annual/HistBrine.aspx?HYr=2021.
Arkansas Oil &
Gas Commission, 2022a. South Arkansas Oil Production, 1970-2020. Accessed December 9, 2022, https://www.aogc.state.ar.us/annual/HistProduction.aspx?HYr=2020.
Arkansas Oil &
Gas Commission. 2022b. LANXESS Brine Production-Injection Data, 2017-2022. Accessed May 4, 2023, https://www.aogc.state.ar.us/data/querybuild.aspx
and https://www.aogc.state.ar.us/welldata/production.aspx.
Arkansas Oil &
Gas Commission, 2023. Central Brine Unit Expansion Order Number 095-2022-12, January 5, 2023
Budd, D. A., and
R.G. Loucks, 1981, Smackover and Lower Buckner Formations South Texas: Depositional Systems on a Jurassic Carbonate Ramp: The University
of Texas at Austin, Bureau of Economic Geology, Report of Investigations No. 112, 38 p.
Benson, T.R., M.A.,
Coble, J.J. Rutyba, and G.A Mahood 2017. Lithium enrichment in intracontinental rhyolite magmas leads to lithium deposits in caldera
basins; Nature Communications, v. 8, no. 270, p. 1–9.
Blondes, M.S.,
Gans, K.D., Rowan, E.L., Thordsen, J.J., Reidy, M.E., Engle, M.A., Kharaka, Y.K. and Thomas B. (2016). U.S. Geological Survey National
Produced Waters Geochemical Database v2.2 (PROVISIONAL) Documentation; USGS Energy Resources Program: Produced Waters, 16 Feb 2016, <
Available on 14 July 2018 https://archive.org/stream/USGSProducedWatersV2.2c/USGS%20Produced%20Waters%20Database%20 v2.2%20Documentation_djvu.txt
>.
Blondes, M.S.,
K.D. Gans, E.L. Rowan, J.J. Thordsen, M. E. Reidy, M.A. Engle, Y.K. Kharaka, and B. Thomas B, 2019. U.S. Geological Survey National
Produced Waters Geochemical Database v2.2 (PROVISIONAL) Documentation; USGS Energy Resources Program: Produced Waters, 16 Feb 2016, <
Available on 14 July 2018 at: https://archive.org/stream/USGSProducedWatersV2.2c/USGS%20Produced%20Waters%20Database%20v2.2%20Documentation_djvu.txt
>.
Bradley, D., H.
Jochens, S. Hynek, and K Labay 2006. A Preliminary Deposit Model for Lithium Brines; USGS Open-File Report 2013–1006, 9 p.
Bradley,
D.C., L.L. Stillings, B.W. Jaskula, L. Munk, and A.D. McCauley, 2017. Lithium, Schulz, K.J., DeYoung, J.H., Jr., Seal, R.R., II,
and Bradley, D.C. (eds.), Critical mineral resources of the United States-Economic
and environmental geology and prospects for future supply, U.S. Geological Survey Professional Paper 1802, p. K1-K21.
195 |
 |
RSI-3353 |
Budd, D. A. and
R. G. Loucks, 1981. Smackover and lower Buckner formations, south Texas. Depositional systems on a carbonate ramp. Bureau of Economic
Geology, The University of Texas at Austin, Report of Investigations, 112 p.
Bureau of Labor,
2022. U.S. Bureau of Labor Statistics, https://www.bls.gov/oes/current/oes_ar.htm
CIM, 2012.
CIM Best Practice Guidelines for Resource and Reserve Estimation for Lithium Brines available online at https://mrmr.cim.org/media/1041/best-practice-guidelines-for-reporting-of-lithium-brine-resources-and-reserves.pdf
CIM, 2014.
“CIM Definition Standards for Mineral Resources & Mineral Reserves” available online at https://mrmr.cim.org/media/1128/cim-definition-standards_2014.pdf
CIM, 2019.
CIM Estimation of Mineral Resources and Mineral Reserves Best Practice Guidelines, prepared by the Canadian Institute of Mining, Metallurgy,
and Petroleum, CIM Mineral Resources & Mineral Reserve Committee, Westmount, QC, Canada. Available online at https://mrmr.cim.org/media/1146/cim-mrmr-bp-guidelines_2019_may2022.pdf
Collins, A. G.,
1976. Lithium abundance in oilfield waters; Lithium Resources and Requirements by the Year 2000, U.S. Geol. Survey Prof. Paper 1005,
p. 116–123.
Daitch, P.J., 2018.
Lithium extraction from oilfield brine; MSc/MBA Thesis, University of Texas at Austin, May 2018, 141 p.
Dworzanowski, M.,
and D.R. Eccles, 2019. Preliminary Economic Assessment of LANXESS Smackover Project NI 43-101 Technical Report, Document No.: 207036-00088-00-PM-REP-0002,
prepared for Standard Lithium, Saskatoon, Saskatchewan, Canada, August 1, 230p.
Eccles, D.R., W.
Black, K. Hill, R. Molnar, K. Rakhit. 2018. Geological Introduction and Maiden Inferred Resource Estimate for Standard Lithium Ltd.’s
LANXESS Smackover Lithium-Brine Property in Arkansas, United States, prepared for Standard Lithium, Ltd., Calgary, Alberta, Canada,
November 19.
Eccles, D.R., J.
Touw, W. Novak, R.M. McGowen, 2022, Maiden Inferred Bromine- and Lithium-Brine Resource Estimations for Tetra Technologies, Inc.’s
Tetra Property in Arkansas, United States, September 15.
Enverus, 2023.
Drilling Info, https://app.drillinginfo.com/production/#/default.
Evans, R.K. 2014
Lithium; In: A.G. Gunn (Ed.), Critical Metals Handbook, John Wiley & Sones td., Chichester, UK.
Fontes, J-C. and
J. M. Matray, 1993. Geochemistry and origin of formation brines from the Paris Basin, France; Chemical Geology, v. 109, p. 149–175.
Garrett, D.E.,
2004 Handbook of Lithium and Natural Calcium Chloride: Their Deposits, Processing, Uses and Properties. Elsevier. 476 p.
196 |
 |
RSI-3353 |
Imlay, R.W. 1940.
Lower Cretaceous and Jurassic formations of southern Arkansas and their oil and gas possibilities; Arkansas Geological Survey, Information
Circular 12, 64 p.
Kunasz, I.
2006, Lithium Resources; In: J.E. Kogel, N.C. Trivedi, J.M. Barker and S.T. Kurkowski (Eds)., Industrial Minerals and Rocks,
7th Edition Society of Mining, Metallurgy and Exploration Inc., Little Colorado, U.S., p. 599-613.
Magnolia Reporter,
2023. Albemarle Corporation building lithium pilot plants in Columbia County, Mike McNeill, publisher and editor August 3, 2023
updated September 13, 2023 https://www.magnoliareporter.com/news_and_business/local_business/article_237518fa-3237-11ee-9fac-d3df52622fc9.html
McKinsey &
Company, 2023. Battery 2030: Resilient, sustainable, and circular. January 16 https://www.mckinsey.com/industries/automotive-and-assembly/our-insights/battery-2030-resilient-sustainable-and-circular
Moldovanyi, E.P.
and L.M. Walter, 1992. Regional trends in water chemistry, Smackover Formation, southwest Arkansas: Geochemical and physical controls;
The American Association of Petroleum Geologists, Bulletin, v. 76, no. 6., p. 864-894.
Munk, L., Jochens,
H., Jennings, M., Bradley, D. Hynek, S. and Godfrey, L. (2011): Geochemistry of lithium-rich brines in Clayton Valley, Nevada, USA;
Presentation and paper from the 11th Biennial Meeting of the Society for Geology Applied to Mineral Deposits, 26-29 September 2011,
Antofagasta, Chile.
Schneider, H.C.,
1924. Smackover Oil Field, Ouachita and Union Counties, Ark.; The Society of Petroleum Engineers, Transactions 70 (01), p. 1079-1099
Standard Lithium,
2022, Standard Lithium and Lanxess Finalize Plan for First Commercial Lithium Project in Arkansas; https://www.standardlithium.com/investors/news-events/press-releases/detail/113/standard-lithium-and-lanxess-finalize-plan-for-first
Shengsong, Y.,
1986. The hydrochemical features of salt lakes in Qaidam Basin; Chinese Journal of Oceanology and Limnology, v. 4, no. 3, p. 383-403.
Schouakar-Stash,
O., S.V. Alexeev, S.K. Frape, L.P. Alexeeva, and R.J. Drimmie, 2007: Geochemistry and stable isotopic signatures, including chlorine
and bromine isotopes, of the deep groundwaters of the Siberian Platform, Russia; Applied Geochemistry, v. 22, p. 589-605.
SouthArk,2023.
South Arkansas College Catalyst Program, https://www.southark.edu/in-the-news/1301-catalyst-program-enrolling-now
Standard Lithium
Ltd. 2023. Management’s Discussion and Analysis for the Three and Nine Months Ended March 31, 2023, https://d1io3yog0oux5.cloudfront.net/_4b683aa985ac14cd157062faf4aa6159/standardlithium/db/385/2073/file/SLL-+MDA+March+31+2023+FINAL.pdf
197 |
 |
RSI-3353 |
Standard Lithium
2023 Confidential: Site Access, License and Reservation Agreement (SARL) between Standard Lithium Ltd and LANXESS.
Stueber, A. M.,
Pushkar, P. and Hetherington, E.A. 1984. A Strontium Isotopic Study of Smackover Brines and Associated Solids, Southern Arkansas;
Geochimica et Cosmochimica Acta, v. 48, p. 1637-1649.
Tahil, W., 2007.
The trouble with lithium; Meridian International Research, January 2007.
Tetra Technologies, Inc.
2023, United States Securities and exchange Commission Form 8-k Item 1.01 Entry into a Material Definitive Agreement. June 19
https://www.sec.gov/ix?doc=/Archives/edgar/data/844965/000095017023029677/tti-20230619.htm
Walter, L.M., E.P.
Molclovanyi and L.S. Land, 1990. Boron isotopic composition of subsurface brines (Smackover Formation, southwest Arkansas): Implications
for chemical evolution and migration; Geological Society of America 1990 Annual Meeting Abstracts with Programs, p. A62.
Weather.gov, 2023,
NOWdata – NOAA online Weather Data, https://www.weather.gov/wrh/climate?wfo=shv
Wilson, T.P. and
D.T. Long 1993 Geochemistry and isotope chemistry of Michigan Basin brines: Devonian formations, Applied Geochemistry, Volume 8, Issue
1, January, p 81-100.
Worley, 2019. Preliminary Economic Assessment
of LANXESS Smackover Project NI 43-101 Technical Report, Document No.: 207036-00088-00-PM-REP-0002, prepared for Standard Lithium, Saskatoon,
Saskatchewan, Canada, August 1, 230p.
Zheng, M., Yuan,
H., Liu, J., Li, Y., Ma, Z. and Sun, Q., 2007. Sedimentary characteristics and paleoenvironmental records of Zabuye Salt Lake, Tibetan
Plateay, since 128 ka BP; Acta Geological Sinica, v. 81, no. 5, p. 681-879.
198 |
 |
RSI-3353 |
Exhibit 99.3
October 18, 2023
CONSENT OF QUALIFIED
PERSON
I, Charles Daniel Campbell, consent
to the public filing of the technical report titled NI 43-101 Technical Report for the Definitive Feasibility Study for Commercial
Lithium Extraction Plant at LANXESS South Plant, with an effective date of August 18, 2023, (the Technical Report) by Standard
Lithium Ltd. of Vancouver, British Columbia, Canada.
I also consent to the
use of extracts from and the inclusion of a summary of the Technical Report in the September 6, 2023, Press Release.
I confirm that I have
read the press release dated 6th of September 2023 issued by Standard Lithium Ltd, (the Disclosure) in which the findings
of the Technical Report are disclosed. The Disclosure fairly and accurately represents the information in the Sections of the Technical
Report for which I am responsible.
Dated this, October 18, 2023. |
|
|
|
ORIGINALLY SIGNED AND SEALED |
|
|
|
Charles Daniel Campbell, P.E. |
|
Alliance Technical Group |
|
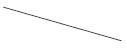
219 Brown Lane
Bryant, AR 72022
501.771.9969
Exhibit 99.4
October 18, 2023
CONSENT
OF QUALIFIED PERSON
I, Frank Gay, consent
to the public filing of the technical report titled NI 43-101 Technical Report for the Definitive Feasibility Study for Commercial
Lithium Extraction Plant at LANXESS South Plant, with an effective date of August 18, 2023, (the Technical Report) by Standard
Lithium Ltd. of Vancouver, British Columbia, Canada.
I also
consent to the use of extracts from and the inclusion of a summary of the Technical Report in the September 6, 2023, Press Release.
I confirm
that I have read the press release dated 6th of September 2023 issued by Standard Lithium Ltd, (the Disclosure) in which
the findings of the Technical Report are disclosed. The Disclosure fairly and accurately represents the information in the Sections of
the Technical Report for which I am responsible.
Dated this, October 18, 2023.
ORIGINALLY
SIGNED AND SEALED
Frank Gay, P.E.
Hunt, Guillot & Associates, LLC
8401 New Trails Drive, Suite A
The Woodlands, TX 77381
866.255.6825
Exhibit 99.5
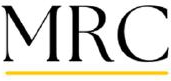
October 18, 2023
CONSENT
OF QUALIFIED PERSON
I, Mike Rockandel, consent
to the public filing of the technical report titled NI 43-101 Technical Report for the Definitive Feasibility Study for Commercial
Lithium Extraction Plant at LANXESS South Plant, with an effective date of August 18, 2023, (the Technical Report) by Standard
Lithium Ltd. of Vancouver, British Columbia, Canada.
I also consent
to the use of extracts from and the inclusion of a summary of the Technical Report in the September 6, 2023, Press Release.
I confirm
that I have read the press release dated 6th of September 2023 issued by Standard Lithium Ltd, (the Disclosure) in which
the findings of the Technical Report are disclosed. The Disclosure fairly and accurately represents the information in the Sections of
the Technical Report for which I am responsible.
Dated this, October 18, 2023.
ORIGINALLY
SIGNED AND SEALED
Mike Rockandel,
RM-SME
#4122579
Mike Rockandel
Consulting LLC
11414 N. Mountain Breeze
Tucson, Arizona
801.580.8491

Exhibit 99.6
October 18, 2023
CONSENT
OF QUALIFIED PERSON
I, Randal M. Brush, consent
to the public filing of the technical report titled NI 43-101 Technical Report for the Definitive Feasibility Study for Commercial
Lithium Extraction Plant at LANXESS South Plant, with an effective date of August 18, 2023, (the Technical Report) by Standard
Lithium Ltd. of Vancouver, British Columbia, Canada.
I also consent
to the use of extracts from and the inclusion of a summary of the Technical Report in the September 6, 2023, Press Release.
I confirm
that I have read the press release dated 6th of September 2023 issued by Standard Lithium Ltd, (the Disclosure) in which
the findings of the Technical Report are disclosed. The Disclosure fairly and accurately represents the information in the Sections of
the Technical Report for which I am responsible.
Dated this, October 18, 2023.
ORIGINALLY
SIGNED AND SEALED
Randal M. Brush, P.E.
William M. Cobb &
Associates, Inc.
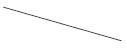
12770 Coit Road, Suite 907
Dallas, TX 75251
972.385.0354
Exhibit 99.7
October 18, 2023
CONSENT OF QUALIFIED PERSON
I, Robert E. Williams, Jr., consent
to the public filing of the technical report titled NI 43-101 Technical Report for the Definitive Feasibility Study for Commercial
Lithium Extraction Plant at LANXESS South Plant, with an effective date of August 18, 2023, (the Technical Report) by Standard
Lithium Ltd. of Vancouver, British Columbia, Canada.
I also consent to the use of extracts
from and the inclusion of a summary of the Technical Report in the September 6, 2023, Press Release.
I confirm that I have read the press
release dated 6th of September 2023 issued by Standard Lithium Ltd, (the Disclosure) in which the findings of the Technical
Report are disclosed. The Disclosure fairly and accurately represents the information in the Sections of the Technical Report for which
I am responsible.
Dated this, October 18,
2023.
ORIGINALLY
SIGNED AND SEALED
Robert E. Williams, Jr., PG, CPG
William M. Cobb &
Associates, Inc.
12770 Coit Road, Suite 907
Dallas, TX 75251
972.385.0354
Exhibit 99.8
October 18, 2023
CONSENT OF QUALIFIED
PERSON
I,
Susan B. Patton, consent to the public filing of the technical report titled Definitive Feasibility Study for Commercial Lithium Extraction
Plant at LANXESS South Plant, with an effective date of August 18, 2023, (the Technical Report) by Standard Lithium Ltd. of
Vancouver, British Columbia, Canada.
I also consent to the
use of extracts from and the inclusion of a summary of the Technical Report in the September 6, 2023, Press Release.
I confirm that I have
read the press release dated 6th of September 2023 issued by Standard Lithium Ltd, (the Disclosure) in which the findings
of the Technical Report are disclosed. The Disclosure fairly and accurately represents the information in the Sections of the Technical
Report for which I am responsible.
Dated this, October 18, 2023.
ORIGINALLY
SIGNED AND SEALED
Susan B. Patton, P.E.
RESPEC Company
LLC
660 Rood Avenue, Suite A
Grand Junction, CO 81501
720.637.8970
Standard Lithium (AMEX:SLI)
과거 데이터 주식 차트
부터 4월(4) 2024 으로 5월(5) 2024
Standard Lithium (AMEX:SLI)
과거 데이터 주식 차트
부터 5월(5) 2023 으로 5월(5) 2024